In order to successfully operate in today's market, enterprises must implement a whole range of measures aimed at increasing competitiveness. The factors for increasing this indicator are: pricing policy, assortment, location of the point of sale, quality of goods and services, scientific and technological development and modern production equipment, highly qualified personnel, territorial distribution of points of sale within the country and abroad. To effectively implement the pricing policy, the company must regularly review its costs and reduce them.
Cost reduction factors
To achieve a reduction in the cost of producing a product, a number of conditions must be met:
- increase productivity;
- reduce labor intensity;
- reduce material consumption;
- short marriage;
- introduce savings mode at the enterprise.
Together, cost-cutting procedures will help a business increase profits while maintaining the same orincreased production.
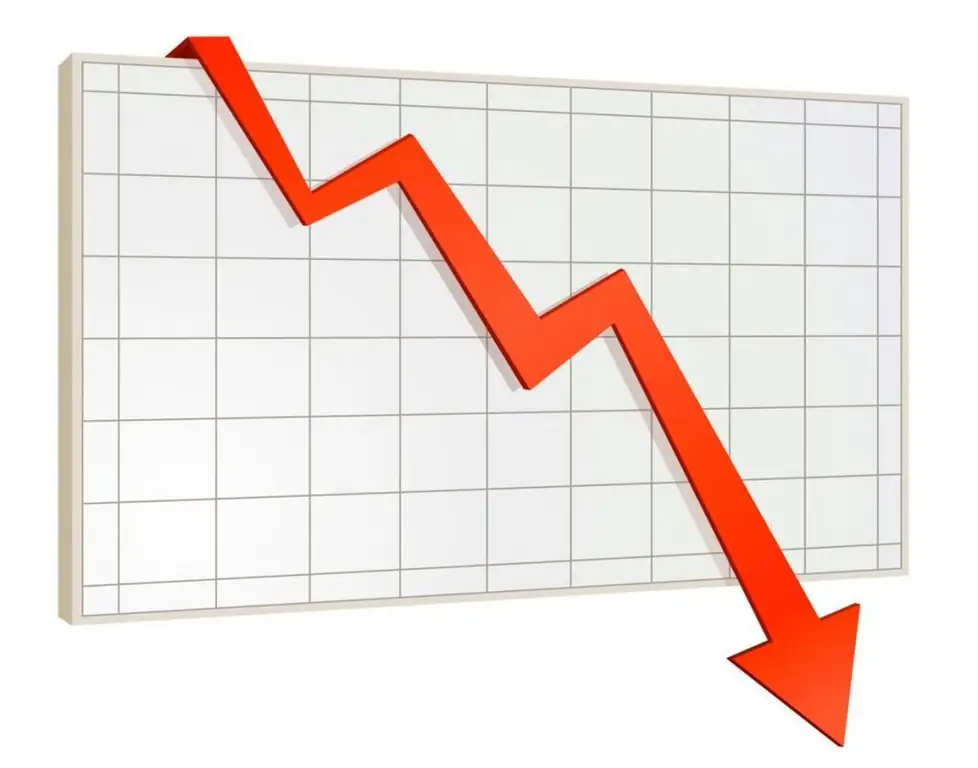
Let's take a closer look at material consumption, since it is the item of material costs that in most cases occupies the main share in the cost structure. If the indicator increases in dynamics, it means that raw materials and materials are used inefficiently, and the company needs to review and adjust the costs of raw materials and components.
Material intensity
This is a measure of how much material is used to produce a unit of output. In other words, what share is occupied by material costs in the composition of production costs. For example: industries with a large share of the cost of raw materials and materials include metal smelting, sugar production, mechanical engineering and others.
The structure of material consumption includes basic materials, auxiliary, as well as fuel, energy and depreciation of fixed production assets.
Material intensity is the inverse of material output.
Calculation formula
Material consumption - this is the figure that is in direct relationship with the amount of material costs. That is, the higher the sum of costs for raw materials and materials in the process of manufacturing a product, the greater will be the material intensity, the formula for calculating which is presented below:
Me=MZ / C, where
Me - material consumption, MZ - the amount of costs for the purchase of raw materials, C - total cost of the finished product.
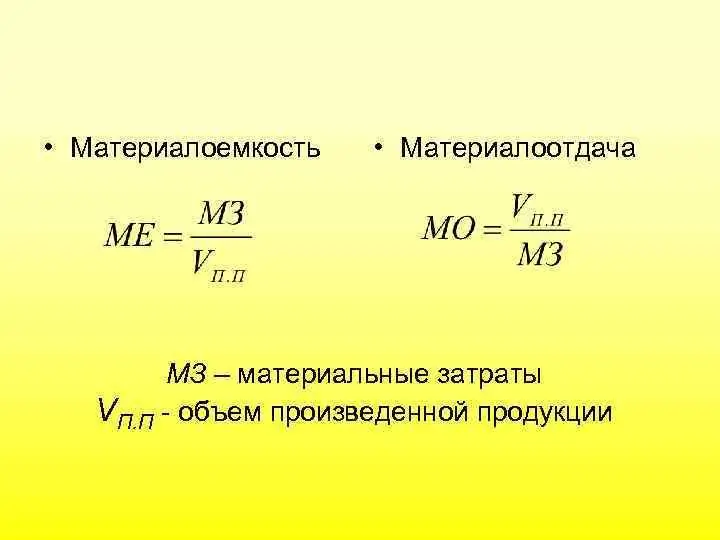
Types of material consumption
There are several types of material consumption. These are specific, structural and absolute. The specific material consumption indicates the share of materials in one piece of goods in physical terms. Structural helps to find out what share in monetary terms a particular type of raw material occupies in the production of a unit of product. The absolute value will allow the manager to find out the rate of resource costs for the production of one piece of products, as well as its share in net weight and the level of inventory costs. It is calculated by the ratio of the net weight of the product to the rate of consumption of raw materials per unit of production. The specific material consumption is the sum of the products of the types of raw materials and their specific gravity in the composition of the product.
Ways to improve
First, it is determined whether the spending plan matches the actual figures. Secondly, they decide how much the organization needs such resources. Thirdly, evaluate the efficiency of the use of materials. Fourth, with the help of factor analysis, it is found out which resources are needed more and where it is necessary to reduce the consumption of resources. Fifth, they calculate the cost of materials and its impact on production volumes.
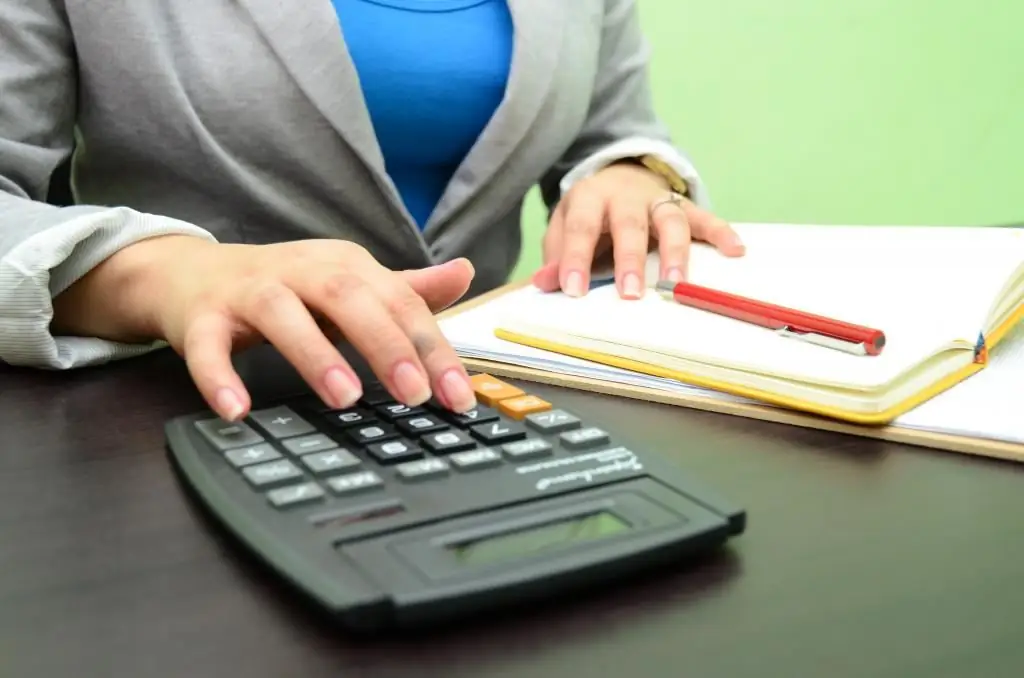
Based on the data obtained, conclusions are drawn and appropriate management decisions are made to improve or reduce costs.