Chromium carbide is a ceramic compound that exists in several different chemical compositions: Cr3 C2, Cr7 C3 and Cr23 C6. Under standard conditions, it exists as gray matter. Chromium is a very hard and corrosion resistant metal. It is also flame retardant, which means that it remains strong even at high temperatures.
These properties of chromium make it useful as an additive in metal alloys. When carbide crystals are integrated into the surface of the material, it improves wear resistance and corrosion resistance and also retains these properties at elevated temperatures. The most complex and most commonly used compound for this purpose is Cr3 C2.
Related minerals include tongbaite and isovite (Cr, Fe) 23 C6, both extremely rare. Another rich carbide mineral is yarlongite Cr4 Fe4 NiC4.
Chromium properties
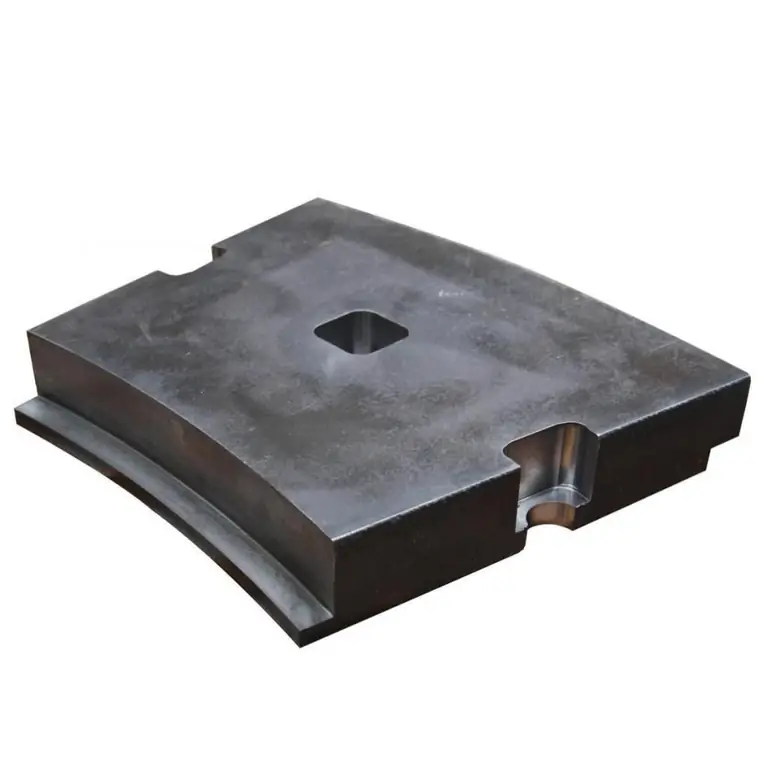
There arethree different crystal structures for carbide corresponding to three different chemical compositions:
- Cr23 C6 has a cubic structure and a Vickers hardness of 976 kg/mm2.
- Cr7 C3 has a hexagonal crystal structure and a microhardness of 1336 kg/mm2.
- Cr3 C2 is the most durable of the three compositions and has a rhombic structure with a microhardness of 2280 kg/mm2.
For this reason, Cr3 C2 is the main formula of chromium carbide used in surface treatment.
Synthesis
Carbide bonding can be achieved by mechanical alloying. In this type of process, chromium metal and carbon in the form of graphite are fed into a ball mill and ground into a fine powder. After crushing the components, they are combined into granules and subjected to hot isostatic pressing. This operation uses an inert gas, primarily argon in a sealed oven.
This pressurized substance exerts pressure on the sample from all sides while the oven heats up. The heat and pressure cause the graphite and metal to react with each other and form chromium carbide. A decrease in the percentage of carbon in the initial mixture leads to an increase in the yield of the Cr7 C3 and Cr23 C6 forms.
Another method for synthesizing chromium carbide uses oxide, pure aluminum and graphite in a self-propagating exothermic reaction that proceeds as follows:
3Cr2O3 + 6Al + 4C → 2Cr3C2 + 3Al 2O3
In this method, the reagentscrushed and mixed in a ball mill. The uniform powder is then compressed into a tablet and placed under an inert argon atmosphere. The sample is then heated. A hot wire, spark, laser, or oven can provide heat. An exothermic reaction is initiated and the resulting steam spreads the effect throughout the rest of the sample.
Production of chromium carbides
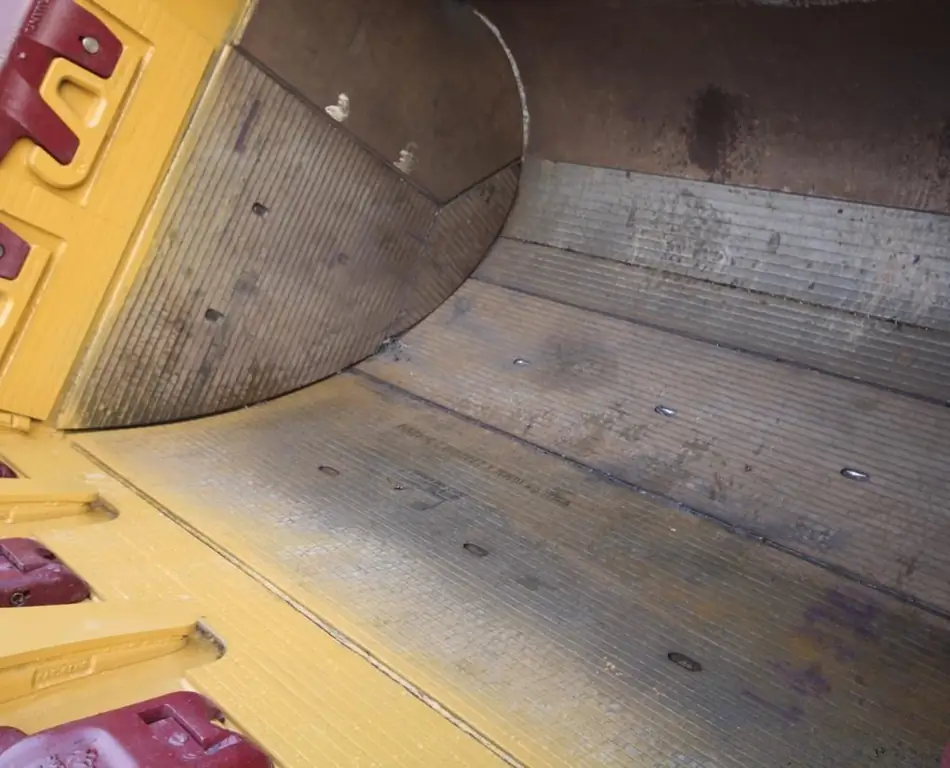
Many companies create the substance by combining aluminothermal reduction and vacuum processing at temperatures of 1500°C and above. A mixture of chromium metal, oxide and carbon is prepared and then loaded into a vacuum furnace. The pressure in the oven is reduced and the temperature is raised to 1500°C. The carbon then reacts with the oxide to form metal and gaseous monoxide, which is vented to vacuum pumps. The chromium then combines with the remaining carbon to form carbide.
The exact balance between these components determines the content of the resulting substance. This is carefully controlled to ensure that the product quality is suitable for demanding markets such as aerospace.
Production of metallic chrome
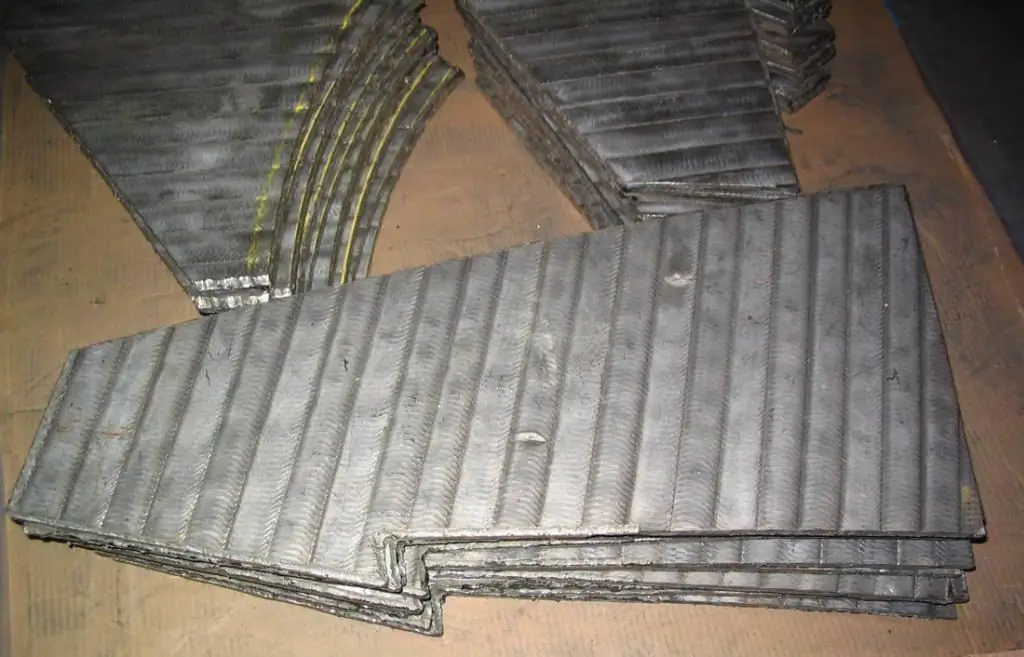
- Researchers discover a new class of carbides that derive stability from a disordered structure.
- The results of the study lay the foundation for future surveys of new carbides useful in practical applications.
- Creating 2D nitrides just got easier.
Metal thatused in many companies, produced by aluminothermic reduction, where a mixture of chromium oxide and aluminum powder is formed. They are then loaded into a roasting vessel where the mixture is ignited. Aluminum reduces chromium oxide to metal and alumina slag at a temperature of 2000-2500°C. This substance forms a molten pool at the bottom of the firing chamber, where it can be collected when the temperature has dropped sufficiently. Otherwise, contact will be difficult and very dangerous. Then the initial substance is turned into powder and used as a raw material for the production of chromium carbide.
Further grinding
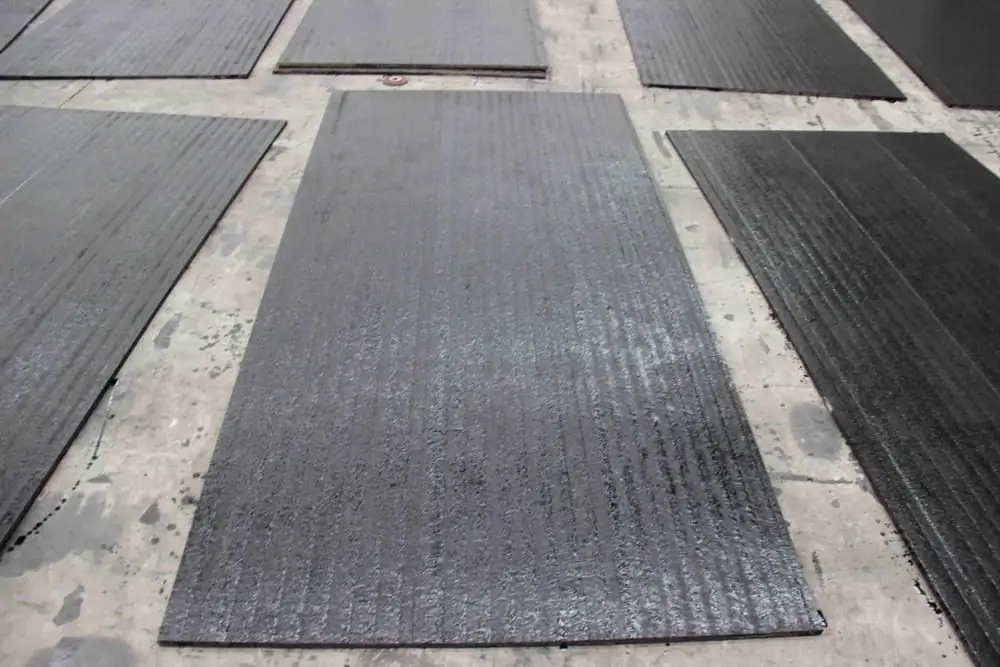
Crushing of chromium carbide and its initial substance is carried out in mills. When grinding fine metal powders, there is always a risk of explosion. That is why mills are specially designed to deal with such potential hazards. Cryogenic refrigeration (most commonly liquid nitrogen) is also applied to the facility to facilitate grinding.
Wear resistant coatings
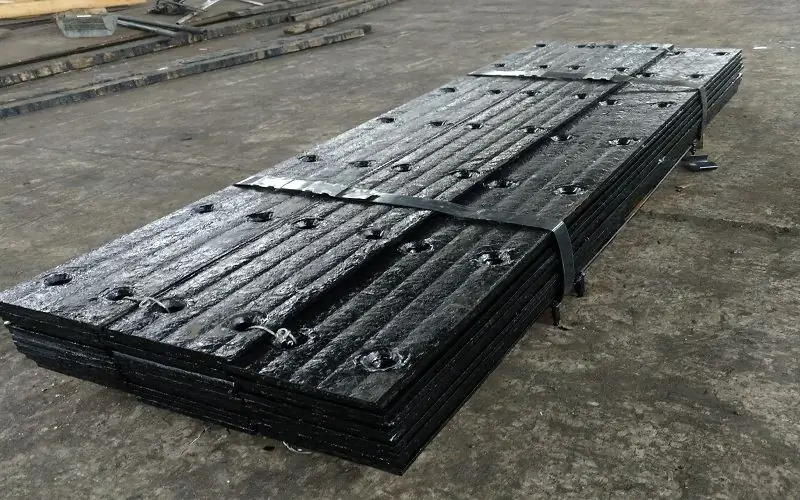
Carbides are hard and so a common use for chromium is to provide strong wear resistant coatings on parts that need to be protected. In combination with a protective metal matrix, both anti-corrosion and wear-resistant agents can be developed that are easy to apply and cost-effective. These coatings are made by welding or thermal spraying. In combination with other resistant substances, chromium carbide can be used forforming cutting tools.
Welding electrodes
These chromium carbide rods are increasingly being used in place of the old ferrochromium or carbon containing components. They give superior and more consistent results. In these welding electrodes, chromium II carbide is created during the bonding process to provide a wear layer. However, the formation of carbides is determined by the exact conditions in the finished joint. And therefore, there may be changes between them that are not visible for electrodes containing chromium carbide. This is reflected in the wear resistance of the deposited weld.
When testing a wheel made of dry sand rubber, it was found that the wear rate of the compound applied to ferrochrome or carbon electrodes was 250% higher. Compared to chromium carbide.
The trend in the welding industry from stick electrodes to flux cored wires benefits the substance. Chromium carbide is used almost exclusively in the pulverized element instead of high carbon ferrochromium because it does not suffer from the dilution effect caused by excess iron in it.
This means that a coating containing a larger amount of hard particles can be obtained, which has a high wear resistance. Therefore, as there is a shift from rod electrodes to flux cored wire due to the advantages of automation and the higher productivity associated with the latter substance welding technology, the market for carbide is increasing.
Typical uses for itare: hardfacing of conveyor screws, fuel mixer blades, pump impellers and general chromium applications where wear resistance is required.
Thermal spray
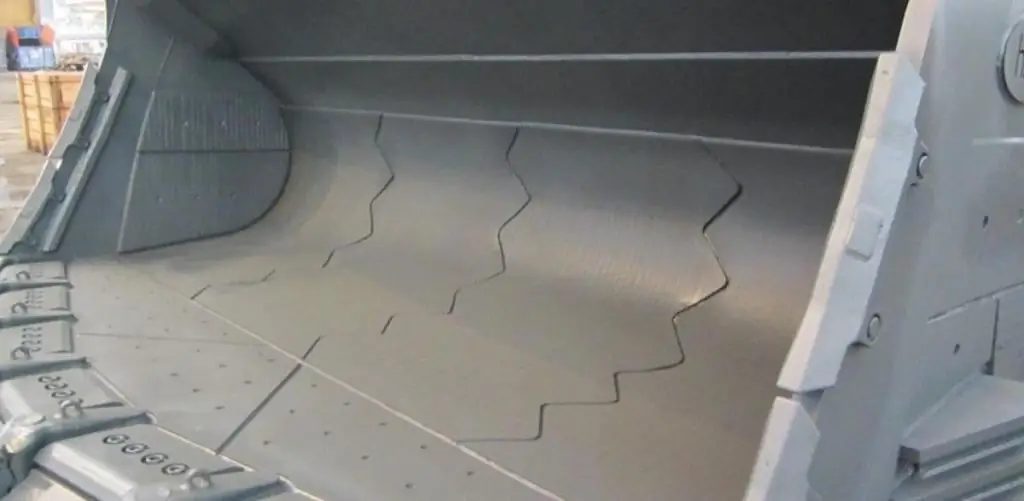
When heat sprayed, chromium carbide is combined with a metal matrix such as nickel-chromium. Typically, the ratio of these substances is 3:1, respectively. A metal matrix is present to bond the carbide to the coated substrate and to provide a high degree of corrosion resistance.
The combination of this property and wear resistance means that thermally sprayed CrC-NiCr coatings are suitable as a high temperature wear barrier. It is for this reason that they are increasingly being used in the aerospace market. Typical applications here are coatings for bar mandrels, hot stamping dies, hydraulic valves, machine parts, aluminum component wear protection and general applications with good resistance to corrosion and abrasion at temperatures up to 700-800°C.
Alternative to chrome plating
New application for thermally sprayed coatings as a replacement for hard product saturation. Hard chromium plating produces a wear resistant shell with good surface quality at low cost. Chrome plating is obtained by dipping the item to be saturated into a container of a chemical solution containing chromium. An electrical current is then passed through the tank, causing the material to deposit on the parts andformation of a coherent coating. However, growing environmental concerns are associated with the disposal of wastewater from the used electroplating solution, and these issues have caused the cost of the process to increase.
Chromium carbide coatings have wear resistance that is two and a half to five times better than hard chromium plating and have no wastewater disposal problems. Therefore, they are increasingly being used with hard chromium plating, especially when wear resistance is important or a thick coating is required for a large part. This is an interesting and fast-growing area that will become more important as the cost of environmental compliance increases.
Cutting tools
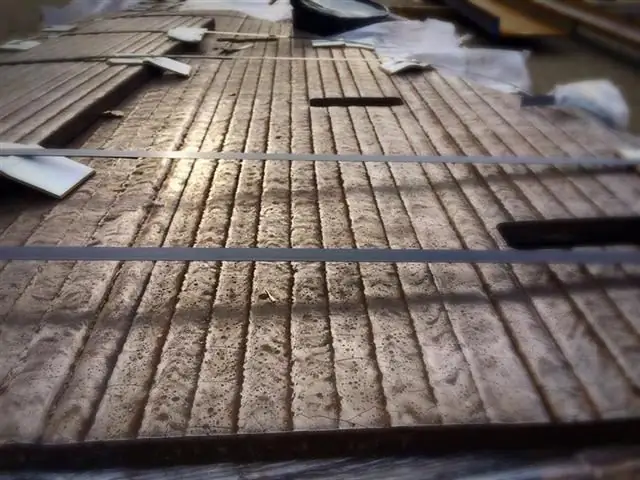
The predominant material here is tungsten carbide powder, which is sintered with cob alt to produce extremely hard objects. To improve the toughness of these cutting tools, titanium, niobium and chromium carbides are added to the material. The role of the latter is to prevent grain growth during sintering. Otherwise, excessively large crystals will form during the process, which may degrade the toughness of the cutting tool.