What is distillation? This is the process of converting a liquid into vapor, which then condenses back into liquid form. The simplest example is the distillation of water, where steam from a kettle is deposited as droplets on a cold surface.
Application and history
Distillation is used to separate liquids from non-volatile solids, as in the distillation of spirits from fermented materials, or to separate two or more liquids with different boiling points, as in the manufacture of gasoline, kerosene, and lubricants from petroleum. Other industrial applications include the processing of chemicals such as formaldehyde and phenol, seawater desalination.
The distillation process was probably used by ancient experimenters. Aristotle (384-322 BC) mentioned that pure water can be obtained by evaporating sea water. Pliny the Elder (23-79 AD) described a primitive method of condensation in which oil obtained by heating rosin is collected on wool placed on top ofalembic.
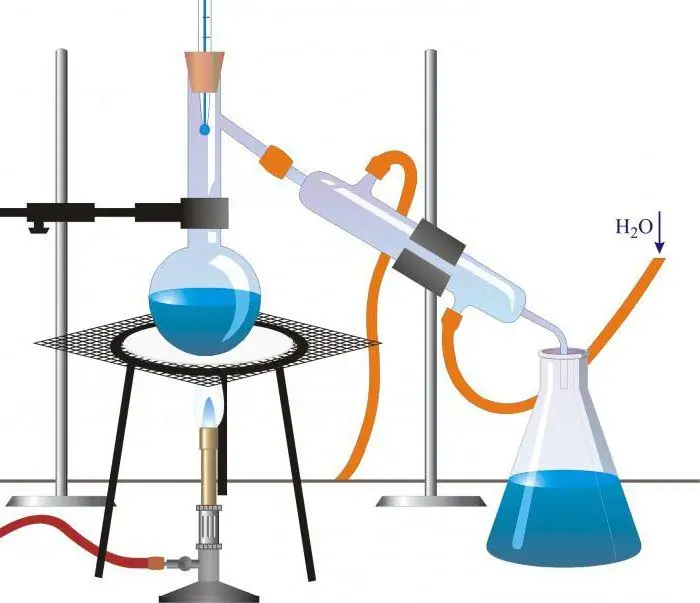
Simple distillation
Most of the distillation methods used in industry and laboratory research are variations on simple distillation. This basic technology uses a cube or retort in which the liquid is heated, a condenser to cool the vapor, and a vessel to collect the distillate. When a mixture of substances is heated, the most volatile of them, or the one with the lowest boiling point, is distilled first, and then the others are distilled, or not distilled at all. Such a simple apparatus is excellent for purifying liquids containing non-volatile components, and is quite effective for separating substances with different boiling points. For laboratory use, parts of the apparatus are usually made of glass and connected with stoppers, rubber hoses, or glass tubes. On an industrial scale, equipment is made of metal or ceramic.
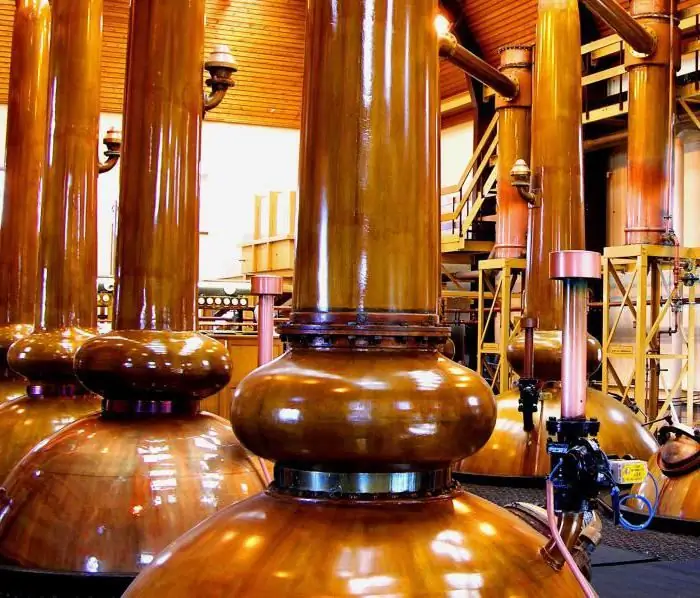
Fractional distillation
A method called fractional, or differential, distillation was developed for oil refining because simple distillation to separate liquids whose boiling points differ little is inefficient. In this case, the vapors repeatedly condense and evaporate in an insulated vertical container. A special role here is played by dry steamers, fractional columns and condensers, which allow returning some of the condensate back to the still. The goal is to achieve close contact between the rising different phases of the mixture so thatonly the most volatile fractions in the form of a vapor reached the receiver, and the rest returned in the form of a liquid towards the cube. Purification of volatile components as a result of contact between such countercurrents is called rectification, or enrichment.
Multiple distillation
This method is also called multi-stage flash evaporation. This is another kind of simple distillation. It is used, for example, to distill water in large commercial desalination plants. Converting liquid to vapor does not require heating. It simply flows from a container with high atmospheric pressure to a container with lower pressure. This leads to rapid evaporation, accompanied by the condensation of vapor into liquid.
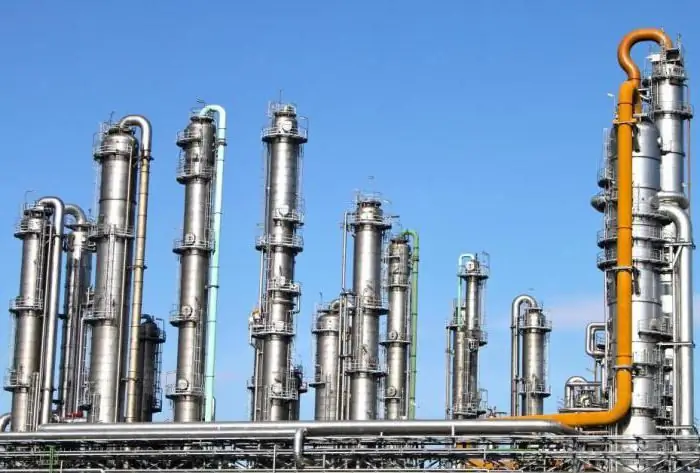
Vacuum distillation
One variation of the reduced pressure process uses a vacuum pump to create a vacuum. This method, called "vacuum distillation", is sometimes used with substances that normally boil at high temperatures or decompose when boiled under normal conditions.
Vacuum pumps create pressure in the column, which is much lower than atmospheric pressure. In addition to them, vacuum regulators are used. Careful control of the parameters is very important because the separation efficiency depends on the difference in relative volatility at a given temperature and pressure. Changing this setting may adversely affect the progress of the process.
Vacuum distillation is well known in refineries. Conventional distillation methods separatelight hydrocarbons and impurities from heavy hydrocarbons. The residual product is subjected to vacuum distillation. This makes it possible to separate high-boiling hydrocarbons such as oils and waxes at low temperatures. The method is also used in the separation of heat sensitive organic chemicals and in the recovery of organic solvents.
What is steam distillation?
Steam distillation is an alternative distillation method at temperatures below the normal boiling point. It is used when the distilled substance is immiscible and does not chemically react with water. Examples of such materials are fatty acids and soybean oil. During distillation, steam is introduced into the liquid, which heats it and causes evaporation.
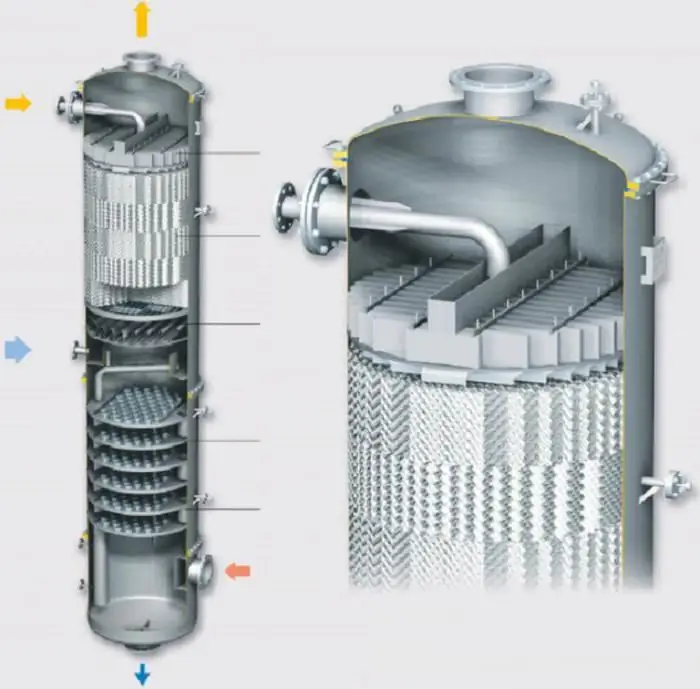
Distillation in a packed column
Although packed columns are most often used for absorption, they are also used for the distillation of vapour-liquid mixtures. This design provides a large contact surface area, which increases the efficiency of the system. Another name for such a structure is a distillation column.
The principle of operation is as follows. The raw mixture of components with different volatility is fed into the center of the column. The liquid flows down through the nozzle, and the vapor moves up. The mixture at the bottom of the tank enters the preheater and exits with steam. The gas rushes up through the packing, picking up the most volatile components of the liquid, exits the column and enters the condenser. After liquefaction, the product entersinto the phlegm collector, where it is separated into a distillate and a fraction used for irrigation.
Varying concentration leads to the fact that less volatile components pass from the vapor phase to the liquid. The nozzle increases the duration and area of contact, which increases the separation efficiency. At the outlet, the vapor contains the maximum amount of volatile components, while their concentration in the liquid is minimal.
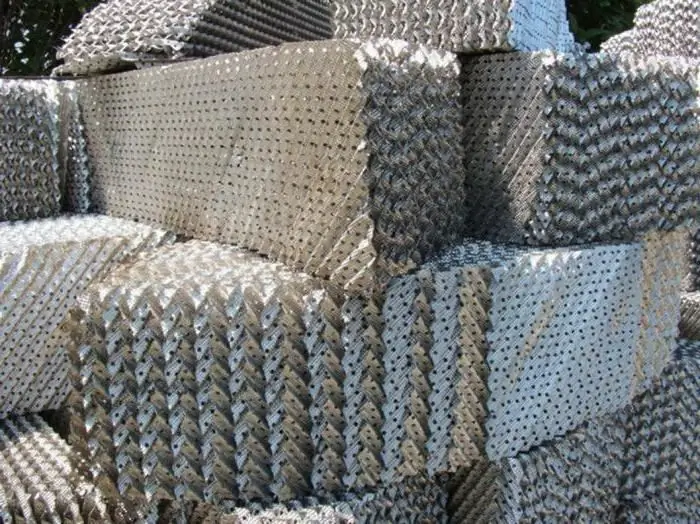
Nozzles are filled in bulk and packages. The shape of the filler can be either random or geometrically structured. It is made from an inert material such as clay, porcelain, plastic, ceramic, metal, or graphite. The filler typically has dimensions from 3 to 75 mm and has a large surface area in contact with the vapour-liquid mixture. Bulk filling has the advantage of high throughput, high pressure resistance and low cost.
Metal fillers have high strength and good wettability. Ceramics have even higher wettability, but they are not as strong. The plastic ones are strong enough, but do not wet well at low flow rates. Since ceramic fillers are resistant to corrosion, they are used at elevated temperatures that plastic cannot withstand.
Package nozzles are a structured mesh, the dimensions of which correspond to the diameter of the column. Provides long channels for liquid and vapor flows. They are more expensive, but allow you to reduce pressure drops. Packet nozzles are preferred at low flow rates and under low pressure conditions. They are usually made from wood, sheet metal or woven mesh.
Used in solvent recovery and petrochemical industries.
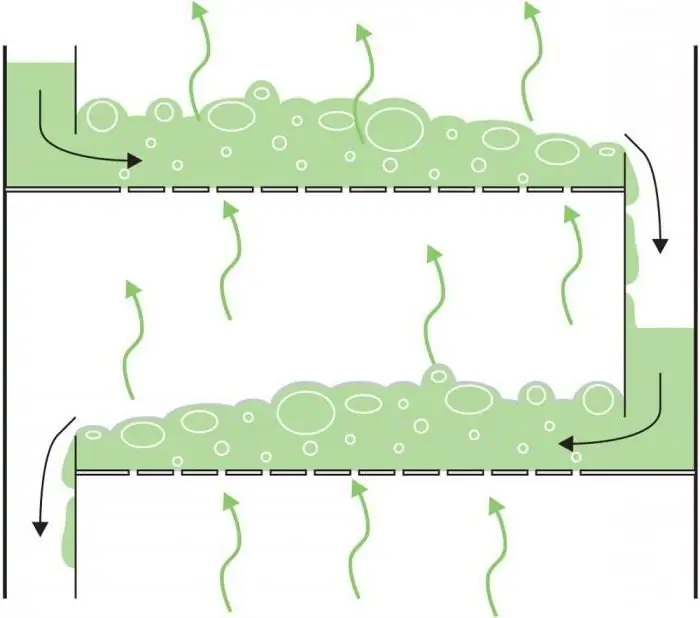
Distillation in distillation column
The most widely used column type. The number of plates depends on the desired purity and the complexity of the separation. It affects the height of the distillation column.
The principle of its operation is as follows. The mixture is fed in the middle of the height of the column. The difference in concentration causes the less volatile components to pass from the vapor stream to the liquid stream. The gas leaving the condenser contains the most volatile substances, while the less volatile substances exit through the heater into the liquid stream.
The geometry of the plates in the column affects the degree and type of contact between different phase states of the mixture. Structurally, they are sieve, valve, cap, lattice, cascade, etc. Sieve trays, which have holes for steam, are used to provide high performance at low cost. Cheaper valve trays, in which the openings are provided with opening and closing valves, are prone to clogging due to the accumulation of material on them. Caps are equipped with caps that allow vapor to pass through the liquid through tiny holes. This is the most advanced and expensive technology, effective at low flow rates. Fluid flows from one tray to another down the drain vertical pipes.
Table columns are often used to recover solvents from process waste. They are also used to recover methanol in a drying operation. Water comes out as a liquid product, and volatile organic waste goes into the vapor phase. This is what distillation in a distillation column is.
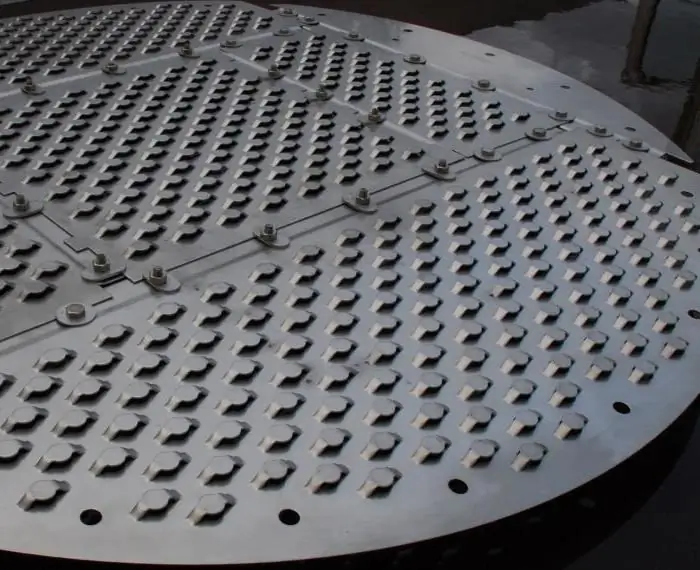
Cryogenic distillation
Cryogenic distillation is the application of general distillation methods to gases cooled to a liquid state. The system operates at temperatures below -150 °C. For this, heat exchangers and coils are used. The whole structure is called a cryogenic block. Liquefied gases enter the unit and are distilled at very low temperatures. Cryogenic distillation columns can be packed and packaged. Batch design is preferred as bulk material is less effective at low temperatures.
One of the main applications of cryogenic distillation is the separation of air into its constituent gases.
Extractive distillation
Extractive distillation uses additional compounds that act as a solvent to change the relative volatility of one of the components of the mixture. In the extractive column, a solvent is added to the substances to be separated. The component of the feed stream to be recovered combines with the solvent and exits in the liquid phase. The other component evaporates and goes into the distillate. Second run toanother column allows the substance to be separated from the solvent, which then returns to the previous stage to repeat the cycle.
Extractive distillation is used to separate compounds with close boiling points and azeotropic mixtures. Extractive distillation is not as widespread in industry as conventional distillation due to the complexity of the design. An example is the process of obtaining cellulose. The organic solvent separates the cellulose from the lignin, and a second distillation produces a pure substance.