Styrene-butadiene rubber is considered one of the most used options for polymeric materials. It is suitable for making tires and other rubber products with high quality.
The named polymeric material is produced from inexpensive raw materials, and its manufacturing technology is considered to be quite affordable, having a clear algorithm of actions. The resulting styrene-butadiene rubber has excellent performance and chemical characteristics. It is produced in significant volumes and is presented by the manufacturer in a wide range.
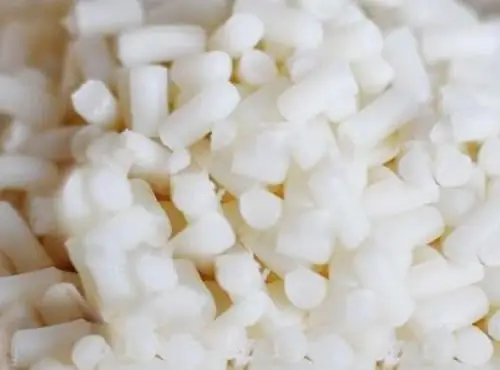
Raw materials for production
Let's take a closer look at the production of styrene-butadiene rubbers. Butadiene-1, 3 or alpha-methylstyrene is chosen as the feedstock for this polymeric material. Get styrene-butadiene rubber by solution technology or emulsion copolymerization. In the second method, styrene-butadiene solution rubbers are formed.
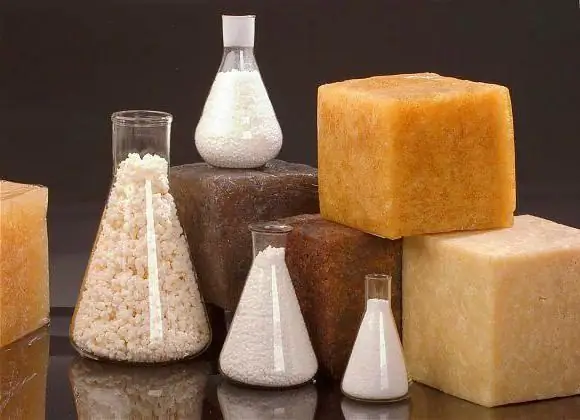
Emulsion polymerization
How is styrene butadiene rubber produced? The reaction involves the copolymerization of styrene andbutadiene in emulsion. The end product resulting from this interaction is called styrene-butadiene rubber (SBR).
Currently, the domestic rubber industry is producing a variety of polymer products based on this chemical.
How is styrene butadiene rubber classified? Manufacturers offer the following options:
- rubbers that do not contain oil (SKS-ZOARK);
- materials with an average percentage of oil (SKM-ZOLRKM-15);
- with increased amount of oil (SKS-ZODRKM-27);
- with excellent dielectric characteristics (SKS-ZOARPD).
Specific naming
The first digits in the above names tell about the quantitative content of styrene in the initial charge selected for the polymerization process:
- "A" involves the implementation of the process of low-temperature polymerization (not more than +5 degrees).
- The "M" indicates that it contains oil, not just styrene.
- Styrene-butadiene rubber with the letter "P" tells about the polymerization reaction without the presence of a regulator.
- "K" indicates the use of rosin emulsifier in the manufacture of rubber.
- The letter "P" symbolizes the material obtained in the presence in the initial mixture of s alts of fatty, synthetic acids, which are products of partial oxidation of saturated paraffins.
What characterizes styrene butadiene rubber? Its preparation is based on the polymerization process,which is familiar even to high school students studying in comprehensive schools and colleges.
So, for the production of sole rubber in the industry, resin-filled styrene-butadiene rubber is used, the formula of which is no different from the usual diene hydrocarbon. Rubbers produced on the basis of styrene-butadiene resin have increased resistance to mechanical abrasion and good leather-like characteristics.
Carry out the process of emulsion polymerization on a special industrial plant. What characterizes this styrene butadiene rubber? Receiving it is carried out according to a clear and proven technology. The average duration of a chemical reaction is 12-15 hours. After completion of polymerization, a latex is formed, which contains approximately 30-35 percent of the polymer substance. Neon D. is added to latex as an antioxidant
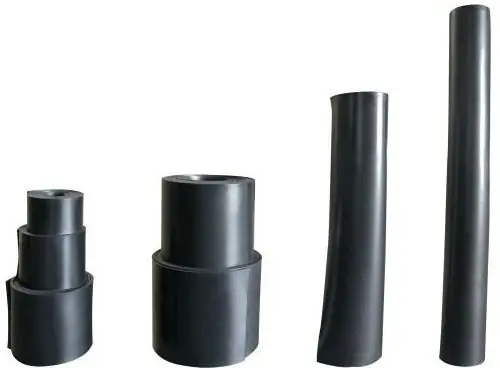
From latex, rubber is produced by coagulation of electrolytes that contain sulfuric acid. Given that rosin oil and soap based on synthetic fatty acids act as emulsifiers, in addition to coagulation, the formation of fatty acids is also observed, which have a positive effect on the technological characteristics of the finished product.
Thanks to the addition of sulfuric acid, the soap is converted into free organic acids, the coagulation of the latex is completed and styrene-butadiene rubber is formed. The use of the finished material is multifaceted, depending on the type of production. Basically rubber iscommon raw material in the chemical industry.
Structure of rubber
What is the structure of styrene butadiene rubber? The physical properties of a given substance are determined by the features of its structure. Upon receipt of the polymer by ozonation, a polymer of an irregular structure is formed. In rubber, monomeric units are randomly distributed, the molecule has a branched form.
Almost 80 percent of all units are trans, and only 20 percent are cis.
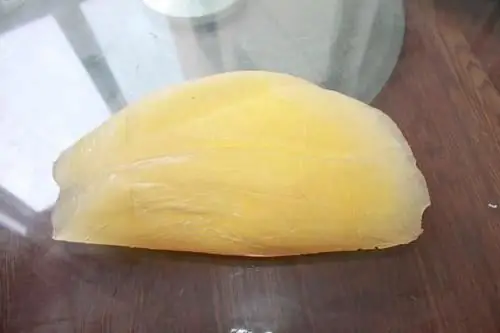
Features
Let's analyze styrene butadiene rubber. The properties of this substance are associated with its high molecular weight. On average, it is 150,000-400,000. And the technology for manufacturing oil-filled rubbers involves the choice of materials with a high relative molecular weight. This option allows you to eliminate the negative impact of oil on the quality of rubber, to maintain excellent technological characteristics of rubber for a long period.
It is possible to obtain styrene-butadiene rubber from ethylene by conducting a technological chain using activators, emulsifiers, regulators, as well as other substances, partially in the process of interaction passing into the composition of the resulting rubber.
Distinguishing Features
Let's characterize styrene-butadiene rubber. The formula of this substance indicates that it is resistant to mechanical deformation, aggressive solvents. To increase frost resistance and elasticityrubber reduce the amount of styrene in the initial mixture. The resulting polymer dissolves in gasoline and aromatic solvents.
What else makes styrene butadiene rubber stand out? Properties and relation to concentrated acids, ketones, alcohol are stable, besides, the polymer has excellent gas and water permeability. During the heating of rubber, serious structural changes are observed, which negatively affects the physical and mechanical properties of the resulting rubber.
Thermal oxidation at temperatures from 125 ° C causes a decrease in stiffness and destruction. Subsequent oxidation implies a serious structuring of the polymer, affects the increase in its rigidity.
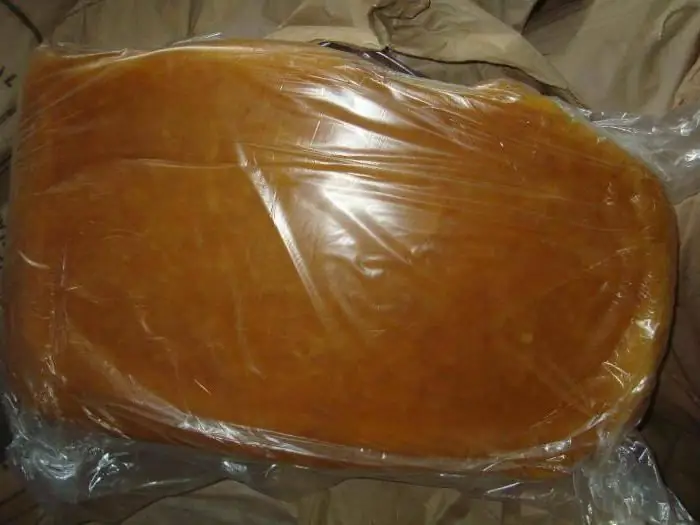
Application Features
Styrene-butadiene rubber is used to create a rubber compound. Properties, application of this representative of the class of diene hydrocarbons fully corresponds to the features of its structural formula.
The presence of side phenyl groups affects the increased resistance to the negative effects of radiation exposure in comparison with other varieties of these polymers.
Rubber compounds, which are made on the basis of styrene-butadiene rubber, have low stickiness, increased shrinkage during calendering and extrusion. This negatively affects the implementation of technological processes, as well as during the gluing (assembly) of rubber blanks.
Low-temperature rubbers have improved technological properties, they are called"hot" rubbers.
Varieties of rubbers
Soft styrene-butadiene low-temperature rubbers have low viscosity, so they are not plasticized.
Rigid rubbers are produced in small quantities, subjecting them to thermo-oxidative plasticization in air at a temperature of about 1400 °C using degradation process activators.
Unfilled vulcanizers have low tensile strength. With a decrease in the amount of bound styrene in the polymer compound, resistance and abrasion resistance decrease, frost resistance increases, and elasticity increases.
Black-filled (with carbon black) styrene-butadiene rubber vulcanizers have excellent parameters in terms of heat resistance and wear resistance, but to some extent they are inferior in elasticity and deformation resistance to conventional rubbers. Used vulcanizers have additional resistance to concentrated and dilute acids, alcohols, alkalis, esters. They swell in rubber solvents.
All obtained polymers are used in the production of tires, the manufacture of a variety of non-molded and molded products. For example, styrene-butadiene rubber is used to make conveyor belts for logging production, and rubber shoes are produced. Due to the increased radiation resistance, all these rubbers are used in the manufacture of rubbers that have optimal resistance to gamma radiation.
For the production of products with excellent frost-resistant characteristics, raw materials are used, inwhich contains a minimum content of styrene.
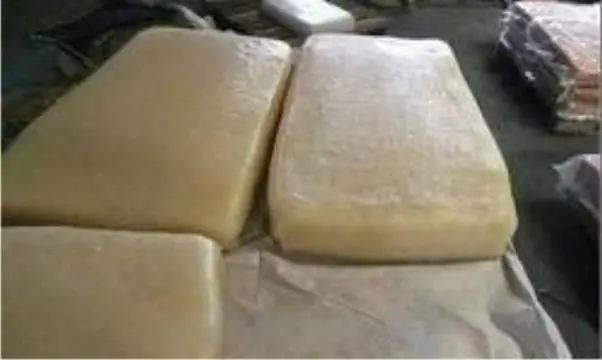
Characterization of solution polymerization styrene butadiene rubbers
In the domestic industry, the production of styrene-butadiene rubbers of solution polymerization with different styrene content has been launched:
- DSSK-10.
- DSSK-25.
- DSSK-18.
- DSSK-50.
- DSSK-25D (has enhanced dielectric characteristics).
There is also rubber on sale, which includes aromatic styrene microblocks, intended for casting processing.
In addition, there are oil-filled solution polymerization rubbers that contain up to 27% oil. Thanks to solution polymerization, in the presence of organolithium catalysts, the main parameters of the molecular structure are adjusted:
- chain branches;
- molecular weight;
- macrostructures.
Distinctive characteristics of such rubbers are the significant presence of the polymer itself (up to 98%), the minimum amount of impurities. Polymers have a linear structure compared to styrene-butadiene emulsion rubbers.
The resulting polymer materials have higher ductility, wear resistance, frost resistance, and increased resistance to cracking. We also note the high dynamic endurance of these materials. With less shrinkage, they have a higher Mooney viscosity, since macromolecules have a linear structure, are able to fill with a large numbersoot (carbon black) and oil without negatively changing the mechanical and physical properties of vulcanizers.
There are some technological advantages in the production of solution rubbers in comparison with emulsion options, but there are much more requirements for the purity of the monomers used. Solution polymerization rubbers are used in the tire industry to create durable conveyor belts, shoe soles, rubber sleeves, and numerous rubber parts. Styrene and buadiene-1, 3 are considered as initial components for the production of polymeric materials of this type. Rubbers are obtained by solution or emulsion copolymerization.
In modern production, not only the technology of manufacturing unfilled rubbers is used, but also the production of polymers, which contain resins, carbon black, and oil, has been established. Among all manufactured polymeric materials, styrene-butadiene rubber accounts for more than half of all production capacities.
The reason for this scale is the high homogeneity of the physical and chemical characteristics of the manufactured product, the availability of the starting monomers (styrene and butadiene), as well as the well-established production line.
A large mass of styrene-butadiene rubber in modern production is obtained by emulsion copolymerization of styrene and butadiene.
Classification of rubbers by structure
Taking into account the conditions of polymerization and the composition of the components used, the production of styrene-butadiene rubbers, which differ inproperties and composition. A statistical, irregular distribution of the structural units of styrene and butadiene in the macromolecule is allowed.
With decreasing temperature, a decrease in the quantitative content of low molecular weight fractions in the created rubber is observed. In addition, there is a decrease in structural branching, an increase in the regular structure of the polymer, which has a positive effect on the technical and operational characteristics of the finished product.
In the development of the domestic production of synthetic materials, an important point was the establishment of the production of styrene-butadiene materials by radical polymerization. Currently, such materials of high quality and at an affordable price are produced at factories in Krasnoyarsk, Omsk, Tolyatti, Sterlitamak, Voronezh.
Technology Features
If desired, you can get a polymer with certain parameters. For example, with a given average molecular weight, which is controlled during polymerization by introducing regulators capable of chain transfer. As the quantitative content of regulators increases, a decrease in the molecular weight of the polymer is observed.
What can be considered as emulsifiers suitable for the production of stable emulsions of monomers, as well as for the creation of final polymerization products, latexes? Potassium or sodium s alts of fatty synthetic carboxylic acids, hydrogenated rosin, as well as s alts of alkylsulfonates are considered as the main chemical components.
When choosing rosin, it must firstsubjected to special treatment. In the process of disproportionation with a catalyst (palladium), it acquires the properties necessary for the technological chain of rubber production.
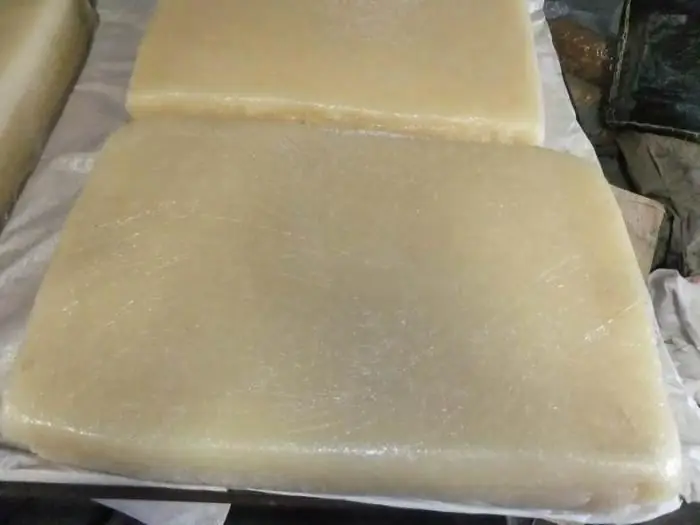
Production specifics
To carry out copolymerization, a battery of polymerizers is used. When preparing the mixture, purified and pre-dried styrene, butadiene, solvent (it may be cyclohexane) are mixed in a ratio of 5/1. Next, the components of the original charge is fed into the diaphragm mixer for high-quality mixing. Then the mixture is sent for chemical fine purification from various small impurities.
The apparatus is fed with organolithium compounds, titrated at 25 °C for 20 minutes. The degree of purification is determined by the color of the charge. If there are no impurities, the mixture has a slightly brown color. Before polymerization, the mixture is mixed with a catalyst, polar additives.
The process is carried out in a battery, which consists of three standard devices, by successive supply of the charge. The temperature inside the polymerizers is maintained in the range from 50 to 80 °C. The average duration of the entire chemical process is 6 hours.
Conclusion
In any sphere of life and activity of a timely person, there are materials based on styrene-butadiene rubber. First of all, we note the creation of rubber soles for shoes, automobile rubber tires, various watering hoses.
Statistical copolymers of styrene andbutadiene is widely used in the creation of electrical insulating materials, a variety of products for the automotive industry, including the creation of high-quality tires. Innovative technologies used by modern manufacturers of styrene-butadiene rubbers allow them to create products with specified physical and chemical parameters and desired performance characteristics.
Among the features of this production, we note the use of high quality catalysts. Depending on the structure of the synthesized rubbers, the duration of the process of their creation, as well as the final cost of rubber products manufactured on the basis of rubber, differ significantly.