In the production process, in order to take into account the efficiency of the enterprise in the manufacture of goods or the provision of services, it is necessary to control the costs incurred. The main and most common indicator is the concept of production cost.
By calculating the cost, you can determine how many costs were spent on the production process, and in accordance with this, determine the amount of markup required to sell products or determine the price of services rendered.
Cost concept
Cost - the sum of all material costs for the production of various goods and services according to a given specialization of the activity carried out.
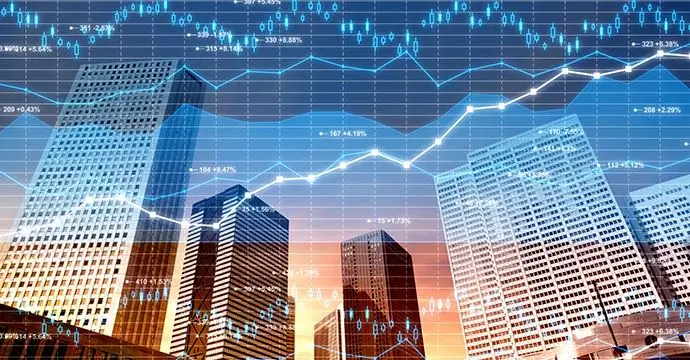
The concept of the cost of production includes the main costs, suchlike:
- buying materials for manufacturing products and fuel;
- use of vehicles and special equipment (main production assets);
- wages and payment of social package to employees of the enterprise;
- tax and other contributions to the state budget.
In addition, the final amount may include other costs necessary for the manufacture and sale of products and services.
The role of cost in financial statements
Cost is an important element for the preparation of financial statements, since the concepts of costs and production costs are directly related. Based on the calculated costs (costs) for the production of products, you can calculate the cost by adding additional costs (depreciation, tax, insurance deductions, wages, rent, etc.)
Through these indicators, the final price for the sale of manufactured goods or services is set. The higher the cost of production, the higher the cost of production, which includes the cost of sales, and added value, and wages to workers.
Cost and costs
The concepts of costs and production costs are also interrelated quantities. The cost price determines the list of costs in relation to a given period of time, which is necessary for the manufacture of goods.
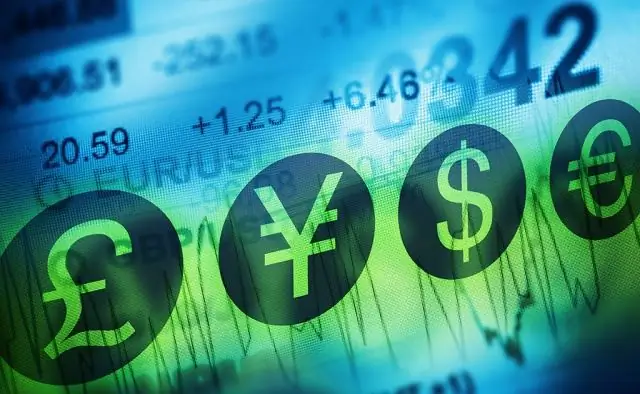
Costs for the current stage are included inthe cost of products manufactured during the present production process. In turn, expenses for subsequent periods are not included in the cost of goods currently produced. They will refer to the cost of production of the next stage of time.
Expenditures for subsequent periods are expenses for which funds have not yet been allocated, but have already been reserved. Thus, in the concept of production cost and costs play a leading role.
Cost functions
The concept and essence of the cost of production are explained by the following functions performed:
- calculation of allocated material resources for the manufacture and delivery of products;
- formation of the price at which the sale will be made;
- determining the level of profitability of the enterprise;
- justification of investments for the modernization of the enterprise, the introduction of innovative technologies and the improvement of production processes;
- justification for making decisions on the introduction of various changes.
Thus, the cost plays an important role in the regulation of the production process, in the improvement of existing methods of work and the sale of manufactured goods to buyers and resellers.
Cost types
The concept of the cost of products, works and services can have several types according to various factors by which the classification is made. These factors include:
- number of products manufactured or services provided;
- designation according to whichcost will be calculated;
- coverage of production processes;
- type of enterprise producing products and specification of the work they perform.
Depending on the required purpose, the cost can be calculated using various methods.
Quantity cost of production
The concept of the cost of production can apply both to a unit of goods and to its full batch. Depending on this, there is a classification by the number of products: the cost of one product and the cost of all production products.
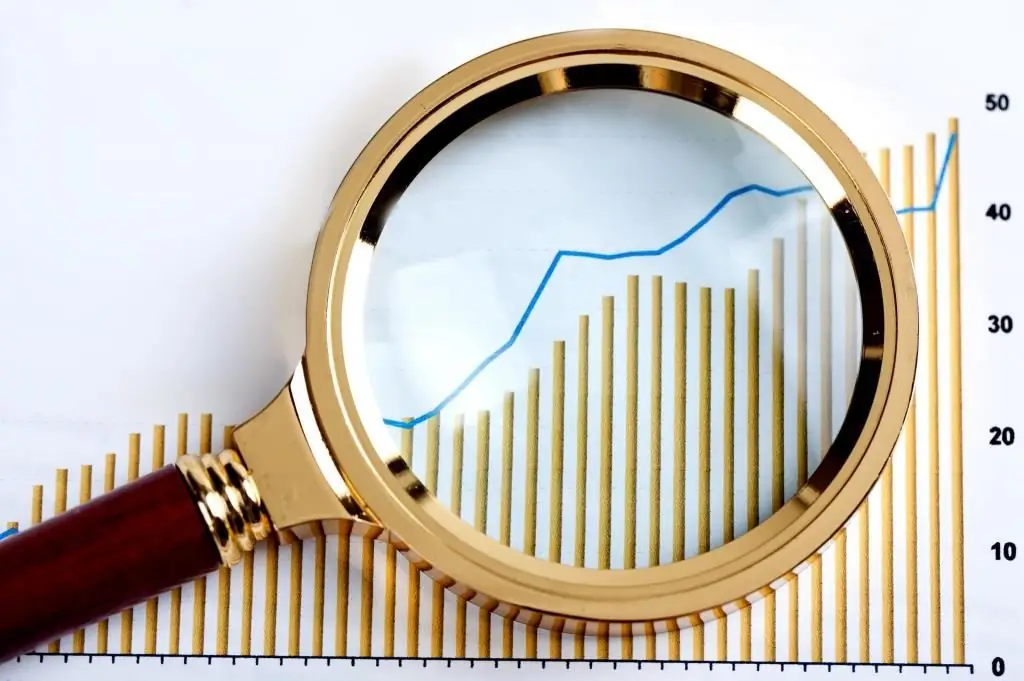
The cost of an enterprise's products is the main characteristic for determining the cost of manufacturing one unit of goods and calculating the efficiency of producing certain products at the level of one enterprise or section.
The cost of production for the entire enterprise can be calculated in the estimate for production. The cost of one unit of a product is calculated using costing methods, which are the most accurate due to the exact accounting of available factors of production.
Cost for the intended purpose
The concept of the cost of products and services, depending on the purpose, is divided into two types: planned and actual.
The planned cost is determined by the norms and prices set for manufactured products, and the actual cost is determined by the values calculated in the reports, including the costs of various non-production needs (for example, damage or loss of goods according toestablished standards).
The value of the planned cost is the leading one for determining the direction of modernization and improvement of the enterprise, increasing the level of production equipment and reducing the consumption of raw materials for the manufacture of goods. To do this, they organize special events where they solve similar organizational and technical issues.
Cost by production coverage
The concept and types of production costs also include a classification according to the breadth of coverage of production and sales. At this level, a distinction is made between full, production and precinct costs.
Sectoral cost includes the cost of servicing the workshop to perform a given type of work. This is the sum of the following elements: the cost of basic and auxiliary materials, electricity, wages and social package of employees, depreciation of instruments and equipment located on the territory of the workshop.
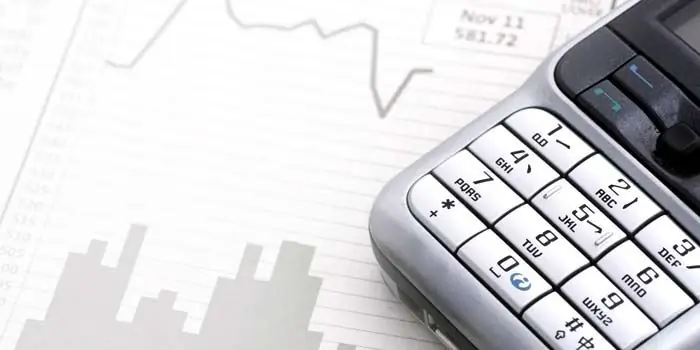
Production cost reflects the amount that the entire enterprise spent on the production of the product in question. This value includes: the cost of raw materials, fuel and electricity, wages and social package of employees, depreciation of all instruments and equipment available at the enterprise.
Full cost, in addition to the above costs, includes the cost of selling finished products: delivery, transportation, payment for the maintenance of organizations selling products, etc.
Cost by enterprise type
Forenterprises producing different types of goods and services, the concept of the cost of production may include different components of production. For organizations where special working conditions apply, the cost of products is calculated in a special way. For example, for mining operations, the cost of geological exploration is taken into account.
Similarly, the desired value is calculated for other types of work, summing up all the costs incurred for the production process. To calculate the cost per unit of production, the cost price for the entire year is divided by the volume of manufactured goods in physical terms. In this case, an approximate cost value is obtained. Calculation is carried out for the exact value.
Economic cost elements
According to economic indicators, the concept of the cost of production of an enterprise includes two parts of expenses, which can be divided into costs by economic elements and calculation items.
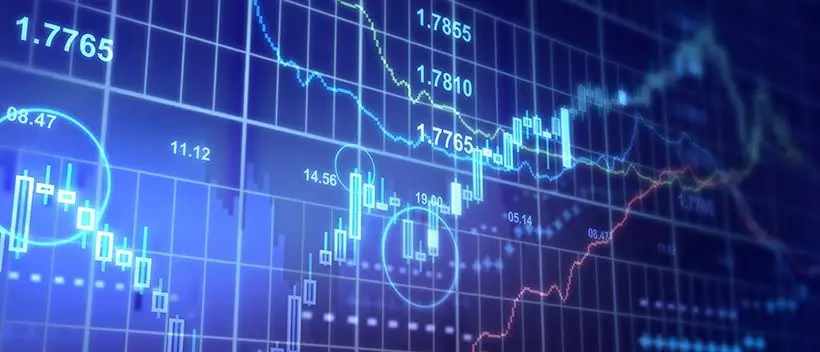
Economic elements include:
- financial costs of producing goods;
- expenses for wages and benefits package for employees;
- depreciation;
- and other possible costs incurred during the production process.
Financial costs include:
- the price of purchasing materials for the manufacture of products;
- price of purchasing materials for non-production needs;
- the price of parts for the manufacture of products and semi-finished products;
- pricefor work performed by third parties of a production nature;
- price for natural resources;
- price of fuel, which is necessary for the smooth operation of machinery and equipment, as well as space heating and other purposes;
- price of purchase energy required for production and non-production needs of the enterprise.
From the amount of financial costs received, the cost of waste received in the process of manufacturing products and sold to third-party enterprises is deducted. Waste in this case is the remains of materials, fuel, semi-finished products and other used resources that were formed during the production period and lost the properties and qualities necessary for production purposes. They are being sold at a price below the original purchase or at full price, depending on the properties.
Financial costs as part of the cost price
The above costs are part of the cost of production. Each of them includes a certain group of expenses.
Payroll costs include the cost of wages for employees involved in the production and sale of products, as well as bonuses, incentives and other payments. Benefit package costs include contributions to he alth care, social insurance and pension funds.
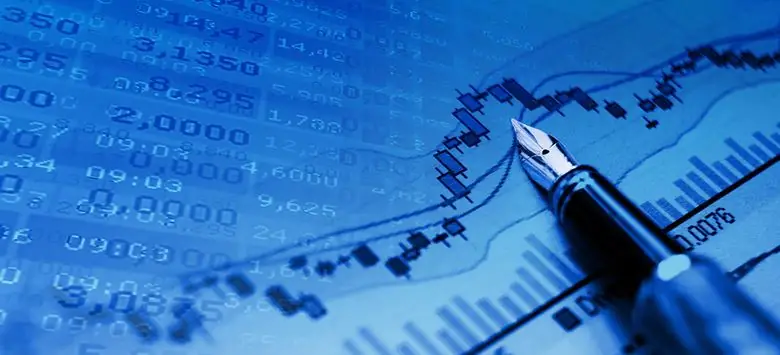
Depreciation deductions are the costs of restoring and repairing machines, instruments and equipment involved in the production process.
Also inthe full amount may include other expenses: tax deductions, payments on existing debts, expenses for employee training, rent payment, contributions to the property insurance fund, equipment repair costs, etc.
Furthermore, the actual cost includes the possible costs of warranty service during the specified period, losses from defects and forced downtime, payments to employees in case of industrial injuries, as well as shortages of funds and resources in the absence of the accused.
Cost calculation
Product costing is one of the basic concepts of the cost of production produced in accounting at the enterprise. The calculation is made in compliance with the current prices for fuel, semi-finished products and raw materials necessary for the manufacture of goods.
Calculation is made according to the relevant items corresponding to the required cost group. These include:
- attitude towards the manufacturing process;
- attribution to own price;
- ratio to turnover.
As a result of the calculation, the total amount of expenses necessary for the production of a particular product is obtained, acting at the price level of the specified time. This amount corresponds to the cost price required to perform further calculations.
Calculation is the most accurate way to determine the cost, as it does not use average values. In the calculation process, you can take into account anyan available factor of production with a required cost.
Cost value
In conclusion, we can say that the concept of the cost of production is the leading one for determining the costs of producing goods or services. Using this value, you can determine how efficiently the operation of the enterprise is carried out, where there are large losses and costs, and how the production process can be improved.
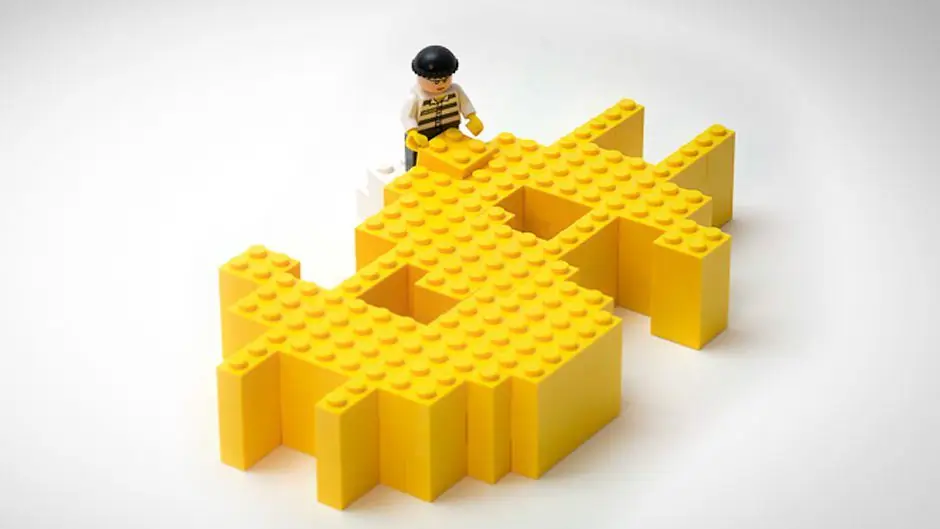
The cost price takes into account not only production costs, but also non-production costs, so it carries more information than the value of production costs. In addition, in relation to the cost, the added value of the final product during the sale is calculated.
Thus, in order to compile the correct financial statements of an enterprise for the manufacture of goods or the provision of services, it is necessary to calculate the cost of the production process.