Iron is an element that is familiar to every person on our planet. And there is nothing surprising in this. Indeed, in terms of its content in the earth's crust (up to 5%), this component is the most common. However, only a fortieth of these reserves can be found in deposits suitable for development. The main ore minerals of iron are siderite, brown iron ore, hematite and magnetite.
Origin of the name
Why does iron have this name? If we consider the table of chemical elements, then in it this component is marked as "ferrum". It is abbreviated as Fe.
According to many etymologists, the word "iron" came to us from the Proto-Slavic language, in which it sounded like zelezo. And this name came from the lexicon of the ancient Greeks. They called the metal so famous today "iron".
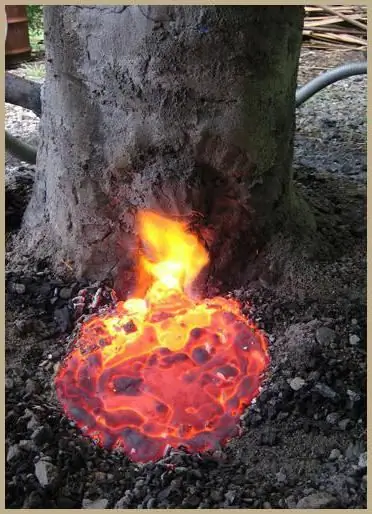
There is another version. According to her, the name "iron" came to us from Latin, wheremeant "starry". The explanation for this lies in the fact that the first samples of this element discovered by people were of meteorite origin.
Iron use
In the history of mankind, there was a period when people valued iron more than gold. This fact is recorded in Homer's Odyssey, which says that the winners of the games arranged by Achilles were given, in addition to gold, a piece of iron. This metal was essential for almost all artisans, farmers and warriors. And it was the huge need for it that became the best engine for the production of this material, as well as further technical progress in its manufacture.
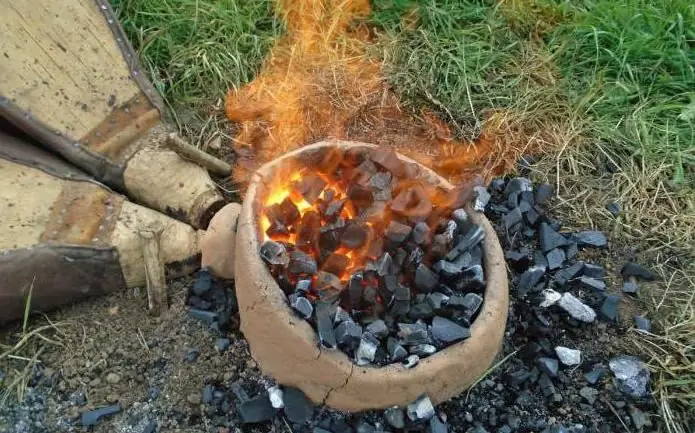
9-7 cc. BC. considered the Iron Age in human history. During this period, many tribes and peoples of Asia and Europe began to develop metallurgy. However, iron is still in high demand today. After all, it is still the main material used for the manufacture of tools.
Cheese product
What is the technology for producing bloom iron, which mankind began to extract at the dawn of the development of metallurgy? The very first method invented by mankind was called cheese-making. Moreover, it was used for 3000 years, not changing from the time of the end of the Bronze Age until the period until the 13th century. The blast furnace was not invented in Europe. This method was called raw. Horns for him were built of stone or clay. Sometimes pieces of slag acted as material for their walls. The last version of the forge from the inside wascoated with refractory clay, to which sand or crushed horn was added to improve quality.
What makes flash iron? The prepared pits were filled with “raw” meadow or swamp ore. The melting space of such furnaces was filled with charcoal, which was then thoroughly heated. At the bottom of the pit was a hole for air supply. At first, it was blown with hand bellows, which were later replaced by mechanical ones.
In the very first forges, natural draft was organized. It was carried out through special holes - nozzles, which were located on the walls of the lower part of the furnace. Often, ancient metallurgists provided air supply through the use of a design that made it possible to obtain the effect of a pipe. They created a high and at the same time narrow interior space. Very often such furnaces were built at the foot of the hills. These places had the greatest natural wind pressure, which was used to increase traction.
As a result of the ongoing process, ore was converted into metal. At the same time, the empty rock gradually flowed down. Iron grains formed at the bottom of the furnace. They stuck together with each other, turning into the so-called "creep". This is a loose spongy mass impregnated with slags. In the oven, the cracker was white-hot. It was in this state that they took it out and quickly forged it. Pieces of slag just fell off. Next, the resulting material was welded into a monolithic piece. The result was flashy iron. The final product was shaped like a flatbread.
What wascomposition of bloom iron? It was an alloy of Fe with carbon, which was very small in the final product (if we consider the percentage, then no more than hundredths).
However, the blooming iron that people received in the raw-blood furnace was not very hard and durable. That is why products made of such material quickly failed. Spears, axes and knives were bent and did not stay sharp for long.
Steel
In the production of iron in forges, along with its soft lumps, there were also those that had a higher hardness. These were pieces of ore that were in close contact with charcoal during the smelting process. A man noticed this pattern and began to deliberately increase the area in contact with coal. This made it possible to carburize the iron. The resulting metal began to meet the needs of craftsmen and those who used products made from it.
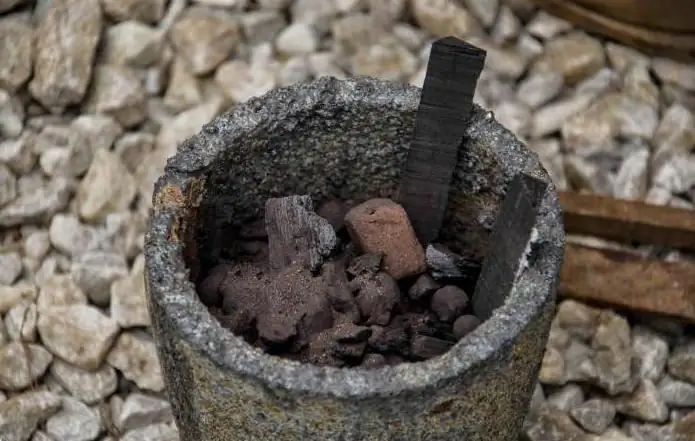
This material was steel. It is still used to this day in the manufacture of a huge number of structures and products. Steel, smelted by ancient metallurgists, is flash iron, which contains up to 2% carbon.
There was also such a thing as mild steel. It was flash iron, which contained less than 0.25% carbon. If we consider the history of metallurgy, then it was mild steel that was produced at the initial stage of cheese production. What is another name for flash iron? There is also a third variety. When it contains more than 2% carbon, thenit's cast iron.
Invention of the blast furnace
The blooming method of obtaining iron using raw-blooded forges was highly dependent on the weather. After all, for such a technology it was important that the wind must blow into the manufactured tube. It was the desire to get away from the vagaries of the weather that led a person to create furs. These were the devices needed to fan the fire in the raw-furnace.
After the appearance of bellows, forges for metal production were no longer built on hillsides. People began to use a new type of stoves, called "wolf pits". They were structures, one part of which was in the ground, and the second (houses) towered above it in the form of a structure made of stones held together by clay. At the base of such a furnace there was a hole into which a tube of bellows was inserted to fan the fire. The coal laid in the house was burned, after which it was possible to get the cracker. She was pulled out through the hole, which was formed after the removal of several stones from the lower part of the structure. Next, the wall was restored and the furnace was filled with ore and coal to start over.

Bright iron production has been constantly improved. Over time, houses began to be built larger. This necessitated an increase in the productivity of the mechs. As a result, coal began to burn faster, saturating the iron with carbon.
Cast iron
What is the high-carbon flash iron called? As it wasmentioned above, this is cast iron that is so common today. Its distinguishing feature is the ability to melt at relatively low temperatures.
Brick iron - cast iron in solid form - it was impossible to forge. That is why the ancient metallurgists did not pay any attention to him at first. From a single blow with a hammer, this material simply shattered into pieces. In this regard, cast iron, as well as slag, was initially considered a waste product. In England, this metal was even called "pig iron". And only over time, people realized that this product, while it is in liquid form, can be poured into molds to obtain various products, for example, cannonballs. Thanks to this discovery in the 14-15 centuries. in industry began to build blast furnaces for the production of pig iron. The height of such structures reached 3 meters or more. With their help, foundry iron was smelted for the production of not only cannonballs, but also the cannons themselves.
Development of blast-furnace production
A real revolution in the metallurgical business occurred in the 80s of the 18th century. It was then that one of Demidov's clerks decided that for greater efficiency in the operation of blast furnaces, air should be supplied to them not through one, but through two nozzles, which should be located on both sides of the hearth. Gradually, the number of such nozzles grew. This made it possible to make the blowing process more uniform, increase the diameter of the hearth and increase the productivity of the furnaces.
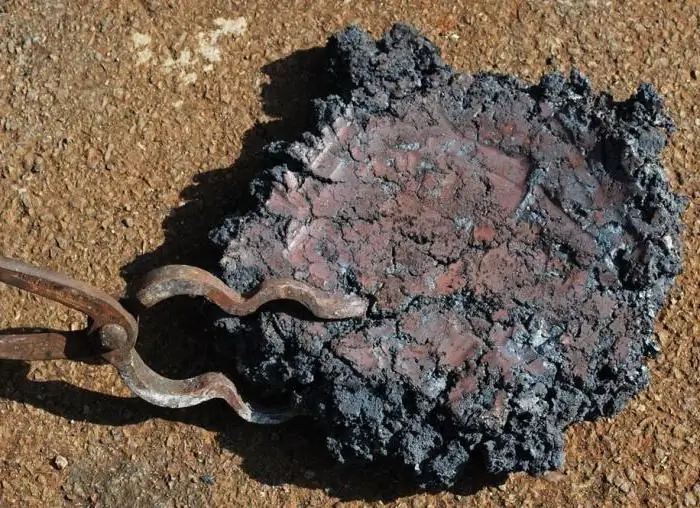
The development of blast-furnace production was also facilitated by the replacement of charcoal,for which forests were cut down, for coke. In 1829, in Scotland, at the Clayde plant, hot air was blown into the blast furnace for the first time. Such an innovation significantly increased the productivity of the furnace and reduced fuel consumption. Nowadays, the blast furnace process has been improved by replacing some of the coke with natural gas, which has an even lower cost.
Bulat
What is the name of the flash iron, which has unique properties that were used in the manufacture of weapons? We know this material as damask steel. This metal, like Damascus steel, is an alloy of iron and carbon. However, unlike its other species, it is a flashy iron with good qualities. It is resilient and hard, and also capable of producing exceptional sharpness in the blade.
Metallurgists of many countries have been trying to unravel the secret of the production of damask steel for more than one century. A large number of recipes and methods were proposed that included the addition of ivory, precious stones, gold and silver to iron. However, the secret of damask steel was revealed only in the first half of the 20th century by the remarkable Russian metallurgist P. P. Anosov. They took blooming iron, which was laid in a furnace with charcoal, where an open fire burned. The metal melted, saturated with carbon. At that time, it was covered with crystalline dolomite slag, sometimes with the addition of the purest iron scale. Under such a layer, the metal was very intensively released from silicon, phosphorus, sulfur and oxygen. However, that was not all. The resulting steel had to be cooled as much as possibleslower and calmer. This made it possible to form, first of all, large crystals having a branched structure (dendrites). Such cooling took place directly in the hearth, which was filled with hot coal. At the next stage, skillful forging was carried out, during which the resulting structure should not collapse.
The unique properties of damask steel subsequently found an explanation in the works of another Russian metallurgist D. K. Chernov. He explained that dendrites are refractory but relatively soft steel. The space between their "branches" in the process of solidification of iron is filled with more saturated carbon. That is, soft steel is surrounded by harder steel. This explains the properties of damask steel, contained in its viscosity and at the same time high strength. Such a steel hybrid during melting retains its tree structure, turning it only from a straight line to a zigzag. The peculiarity of the resulting pattern to a large extent depends on the direction of the blows, the strength, as well as the skill of the blacksmith.
Damascus steel
In ancient times, this metal was the same damask steel. However, a little later, Damascus steel began to be called a material obtained by forge welding from a large number of wires or strips. These elements were made of steel. Moreover, each of them was characterized by a different carbon content.
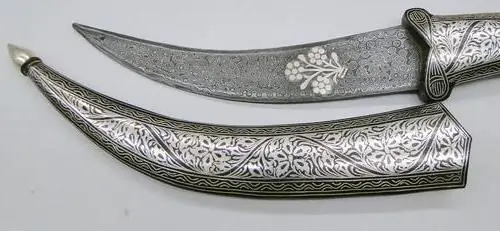
The art of making such a metal reached its greatest development in the Middle Ages. For example, in the structure of the well-known Japanese blade, the researchers foundabout 4 million steel threads of microscopic thickness. This composition made the process of making weapons very laborious.
Production in modern conditions
Ancient metallurgists left a sample of their skill not only in weapons. The most striking example of pure bloomery iron is the famous column located near the capital of India. Archaeologists determined the age of this monument of metallurgical art. It turned out that the column was built another 1.5 thousand years ago. But the most surprising thing lies in the fact that today it is impossible to detect even small traces of corrosion on its surface. The material of the column was subjected to careful examination. It turned out that this is pure flash iron, which contains only 0.28% of impurities. Such a discovery astounded even modern metallurgists.
Over time flashy iron gradually lost its popularity. The metal smelted in an open-hearth or blast furnace began to enjoy the greatest demand. However, when applying these methods, a product of insufficient purity is obtained. That is why the oldest method of producing this material has recently received its second life, which allows producing metal with the highest quality characteristics.
What is flash iron called today? It is familiar to us as a direct reduction metal. Of course, bloomery iron today is not produced in the same way as in ancient times. For its production, the most modern technologies are used. They make it possible to produce metal that has practically noforeign impurities. Rotary tube furnaces are used in production. Such structural elements are used for firing various bulk materials using high temperatures in the chemical, cement and many other industries.
What is flash iron now called? It is considered pure and is used in obtaining a method that is essentially not much different from that which existed in ancient times. Still, metallurgists use iron ore, which is heated in the process of obtaining the final product. However, today raw materials are initially subjected to additional processing. It is enriched, creating a kind of concentrate.
Modern industry uses two methods. Both of them allow you to get flash iron from concentrate.
The first of these methods is based on bringing raw materials to the required temperature using solid fuel. Such a process is very similar to that carried out by the ancient metallurgists. Instead of solid fuel, gas can be used, which is a combination of hydrogen and carbon monoxide.
What precedes getting this material? What is the name of flash iron today? After heating the iron ore concentrate, pellets remain in the furnace. It is from them that pure metal is subsequently produced.
The second method used to restore iron is very similar in technology to the first. The only difference is that metallurgists use pure hydrogen as fuel for heating the concentrate. With this method, iron is obtained much faster. Exactlytherefore, it is distinguished by a higher quality, because in the process of interaction of hydrogen with enriched ore, only two substances are obtained. The first of these is pure iron, and the second is water. It could be assumed that this method is very popular in modern metallurgy. However, today it is used infrequently, and, as a rule, only for the production of iron powder. This is explained by the fact that it is quite difficult to obtain pure hydrogen, both in terms of solving technical issues and because of economic difficulties. Storage of the received fuel is also a difficult task.
Relatively recently, scientists have developed another, third method for the production of reduced iron. It involves obtaining metal from ore concentrate, without going through the stage of its transformation into pellets. Studies have shown that with this method, pure iron can be produced much faster. However, this method has not yet been implemented in industry, as it requires significant technological changes and a change in the equipment of metallurgy enterprises.
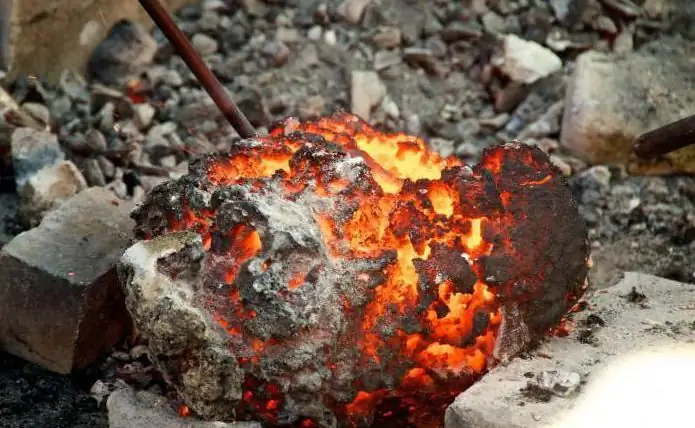
What is the name of flash iron today? This material is familiar to us as a direct reduction metal, sometimes it is also called spongy. This is a cost-effective, high-quality, environmentally friendly material that does not have impurities of phosphorus and sulfur. Due to its characteristics, bloomery iron is used in the engineering industries (aviation, shipbuilding and instrumentation).
Fechral
As you can see, today when usingthe most modern technologies use such material as blooming iron. Fechral is also a sought-after alloy. In addition to iron, it contains components such as chromium and aluminum. Nickel is also present in its structure, but not more than 0.6%.
Fechral has good electrical resistance, high hardness, works great with high alumina ceramics, has no tendency to pitting and is heat resistant in an atmosphere containing sulfur and its compounds, hydrogen and carbon. But the presence of iron in the alloy makes it quite brittle, making it difficult to process the material in the manufacture of various products.
Fechral is used in the manufacture of heating elements for laboratory and industrial furnaces, the maximum operating temperature of which is 1400 degrees. Sometimes parts from this alloy are used for other purposes. They are placed in household heating appliances, as well as in electrical devices of thermal action. Fechral has been widely used in the production of electronic cigarettes. Also, an alloy of iron, aluminum and chromium is in demand in the field of manufacturing resistive elements. These can be, for example, starting-braking resistors of electric locomotives.
Fechral is used to produce wire, as well as thread and ribbon. Sometimes circles and rods are obtained from it. All of these products are used in the manufacture of various forms of heaters for electric ovens.