The metallurgical industry plays an important role in everyone's life, because every day you have to deal with various metal products. And they are made of various alloys, which are obtained through smelting. In the production of these materials, at least two metals are used, and special additives are used to improve the properties. This article will review several iron-nickel alloys, their properties and applications.
About the properties of iron
Pure iron is silver-gray in color and is malleable and malleable. Native ingots found in nature have a pronounced metallic luster and significant hardness. At the height and electrical conductivity of the material, it easily transfers current with the help of free electrons. The metal has an average refractoriness, softens at a temperature of +1539 degrees Celsius and loses its ferromagnetic properties. It is a chemically active element. At normal temperatures, it easily reacts, and when heated, these properties are enhanced. In air, it becomes covered with an oxide film, which prevents the continuation of the reaction. When exposed to a humid environmentrust appears, which no longer prevents corrosion. But, despite this, iron and its alloys are widely used.
A bit of history
Invar is an alloy of iron and nickel, which includes 36% alloying additive. It was first discovered in France in 1896 by the physicist Charles Guillaume. At this time, he was working on the search for an inexpensive metal for standards of measures of mass and length, which were made from a very expensive platinum-iridium alloy. Thanks to this discovery, the scientist received the Nobel Prize in Physics in 1920.
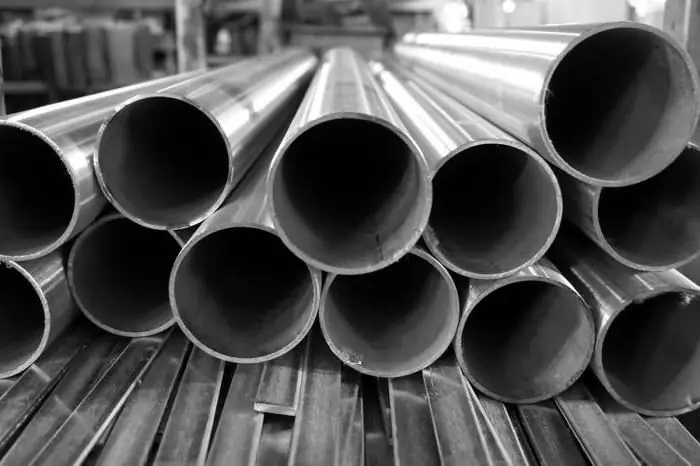
The word "invar" in Latin means unchanging. This means that the coefficient of thermal expansion of an iron-nickel alloy remains constant over a wide temperature range - from -80 to 100 degrees Celsius. This alloy has several other names: nilvar, vakodyl, nilo-alloy, radiometal. Invar is a trademark of Imphy Alloys Inc., which is owned by Arcelor Mittal steel group.
Iron-nickel alloy
To improve the properties of iron, using various additives, alloys are obtained. Scientists believed that it would not be difficult to obtain an iron-nickel alloy, taking into account the thermodynamic properties of metals. But in practice, they ran into problems. During the interaction of metals, during the production of an alloy of iron with nickel, as a result of a side oxidation process, iron from the divalent state passes into the trivalent state.
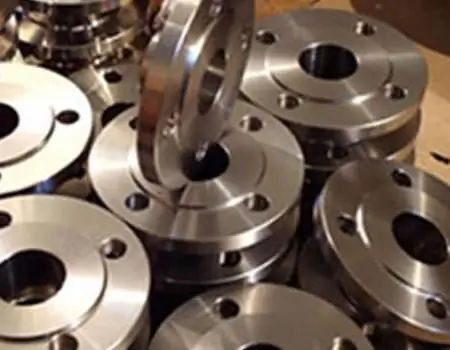
As a result, the yield of the alloy decreases and certain physical properties deteriorate. To solve this problem, amines and organic acids are added to the electrolyte, which form compounds with low solubility with ferric iron. In this regard, the elasticity of the precipitate becomes better, and for its uniform distribution, the electrolytes are mixed. The resulting alloy of iron and nickel is called invar.
Use of Invar alloy
Insignificant thermal expansion coefficient allows it to be used for production:
- instrument parts;
- tape and wire for geodetic works;
- Laser supporting structures;
- parts of watch movements, chronometer pendulums;
- rolled products: hot-rolled bar and sheet, cold-rolled strip, seamless pipes, forged bars.
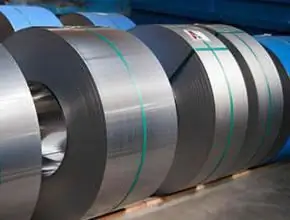
To increase the strength, cold plastic deformation of the iron-nickel alloy is performed, and then low-temperature heat treatment is performed. For greater resistance to corrosion under normal atmospheric conditions, its surface is polished and a protective layer is applied if the product is intended for use in aggressive environments. The anti-corrosion properties of Invar will also increase when about 12% chromium is added to its composition, while it retains constant elasticity when heated to 100 degrees.
Magnetic alloys
These alloys are widely used in electrical engineering. They are used to make permanent magnets, transformer cores,electrical measuring instruments, electromagnets. People have long known that iron is magnetic, and as a result, it has many uses.
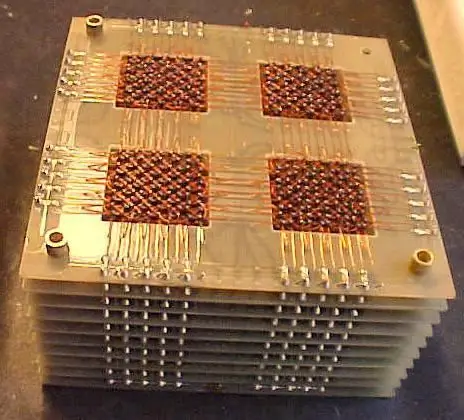
Much later it was discovered that the same property is inherent in nickel and some other metals. Products made from a magnetic alloy of iron and nickel also have the ability to maintain their own magnetic field when the external one is no longer present. Moreover, this personal field is again able to influence other magnetic bodies.
Nickel, cob alt and their alloys
Cob alt and nickel are elements of the iron subgroup. All three elements have similar properties, but there are also significant differences. Both metals are denser than iron and much harder and stronger than iron. They are less active in chemical terms, differ in corrosion resistance. In addition, metals are valued for their greater resistance to gas corrosion.
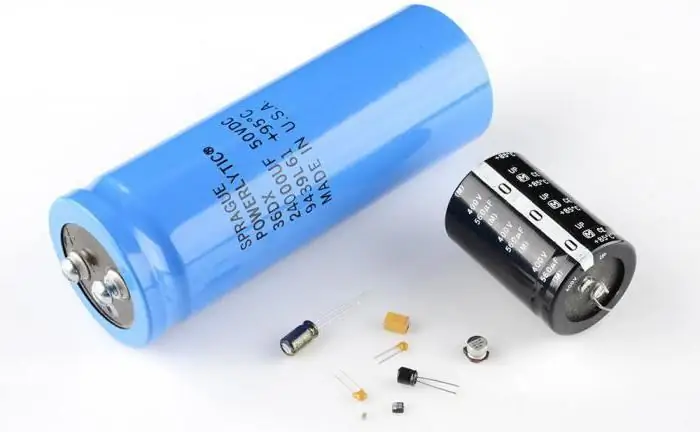
The disadvantages of cob alt and nickel are their high toxicity and significant cost relative to iron. They find their application for the anticorrosive outer coating of products made of carbon steels and iron by electrochemical reactions. And also they are used for the manufacture of components and parts that require enhanced strength and hardness. The special significance of iron, nickel and cob alt alloys, which are called koinvar, invar, supermalloy, permalloy and malloy, should be noted. Their main advantage lies in the highmagnetic properties. These alloys are used to produce magnetic circuits for various electromagnetic devices.
Alloy Kovar
The mixture consists of metals with excellent mechanical properties. They are easy to process, they are easily subjected to rolling, broaching, forging and stamping. And the alloy of cob alt, nickel and iron is otherwise called kovar. A well-chosen combination of chemical elements provides the material with excellent characteristics. This alloy has good thermal conductivity, a high coefficient of electrical resistivity, and linear expansion indices close to zero over a wide temperature range. The only disadvantage is the low corrosion resistance in wet environments, so protective coatings of silver are often used. Kovar is widely used in industry for the production of:
- pipes, tapes and wires;
- capacitors;
- cases of equipment in instrumentation;
- details in radio electronics;
- cases in the electrovacuum industry.
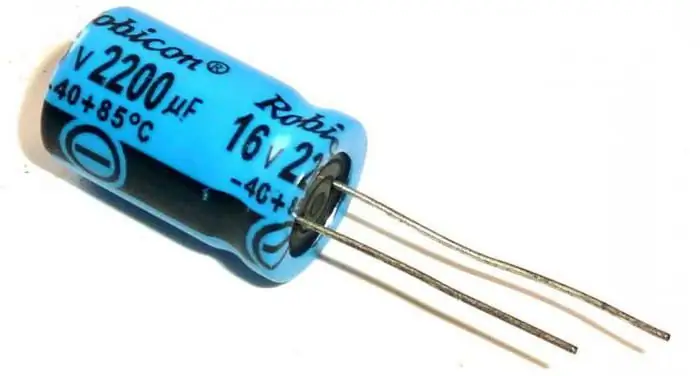
The alloy contains expensive cob alt and nickel, which increases the cost of the material, but good performance and long service life cover the initial investment.
Alni alloys
Alni is the group name for iron-nickel-aluminum magnetic alloys. With an increase in the concentration of aluminum and nickel within certain limits, the residual induction decreases, and the coercive force increases. The most commonly used alloys in which aluminum from 11 to18%, and nickel - 20-34%. The main properties of such alloys are electrical conductivity, thermal conductivity and ductility. All of them are characterized by good welding.
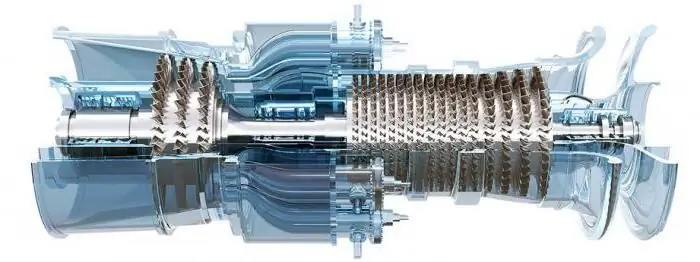
To use alloys in the manufacture of magnets, they are alloyed with cob alt and copper. In this case, the material acquires hardness and brittleness and has a coarse-grained structure. Alni alloys are used as a structural material for parts of gas turbine and jet engines operating at high temperatures of more than 1000 degrees Celsius for a long time, keeping the metal without damage.
Conclusion
All metals heavily used in modern industry are alloys. For example, almost all the iron that is produced in the world is used to produce iron and steel. This can be explained by the fact that alloys are characterized by better properties than the metals from which they are obtained. It should be noted that the alloys produced by the industry have common properties for them: strength, hardness, elasticity and plasticity. And iron-nickel ones also have magnetic properties, which are enhanced during production with the help of additional alloying.