Issues of energy saving are becoming more acute as the power potential of modern consumers increases. Both in the domestic sphere and in industry, the technical means, units and communication networks used require increasing amounts of energy resources. This forces us to look for new, alternative sources of heat, electricity and other forms of energy generation. Despite the active development of natural energy carriers, this segment still does not allow us to count on the complete replacement of traditional generating stations. At the same time, there is considerable interest in secondary energy resources (SER), which are largely free, but require less investment in the creation of a service infrastructure. However, the features of the secondary energy product do not end there.
Definition of VER
There are two fundamentally different ways of generating energy - natural and industrial(artificial). In the first case, the energy of natural phenomena and processes is used - for example, the flow of water, solar radiation, wind, etc. The complexity of the use of such resources is due to technical problems of an organizational nature - in particular, the instability of energy accumulation. Industrial energy generation in this sense is more controllable, but it requires raw materials to ensure reactions, during which heat, electricity, gas, etc. are generated. The combination of primary and secondary energy resources just takes place within the operating cycle of generator stations. The fact is that the main resources are not fully used, and their remains are subsequently disposed of or recycled. Stations of secondary power generation operate on the same basis.
When considering the principles of using VER, it will not be superfluous to refer to the concept of energy potential. This is the amount of energy that can theoretically be generated during the processing of waste, by-products of production and intermediate raw materials not consumed in the primary cycle. In this case, the expression of the potential in the form of energy can be different. Stocks of various wastes are represented as physical or chemically bound heat, excess pressure, kinetic energy or fluid pressure.
So, the definition of secondary resources for the operation of power plants is as follows: this is the energy potential that can be generated as a result of the technological process of processing underused waste or products of the main production. At the same time, both the waste itself and the methods of their further processing may be different.
VER characteristics
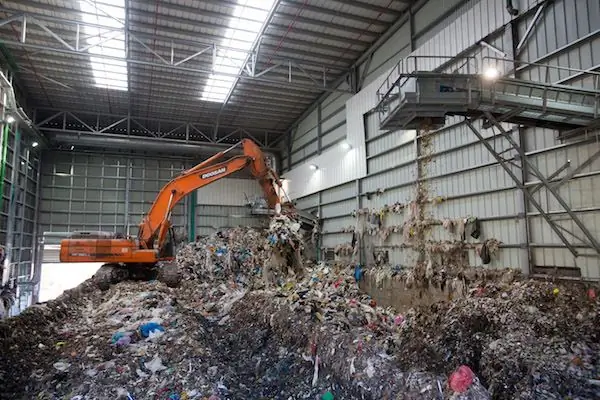
It is worth noting that for a long time this concept of energy generation was not considered by large consumers due to the lack of accurate methods for calculating efficiency and energy potentials. Today, the recycling of resources is based on a comprehensive analysis of a wide range of indicators, which makes it possible to extract the maximum benefit from the same industrial waste. The most common design characteristics of this type of resources include the following:
- Output energy coefficient - the ratio of the generation potential to the thermal volume that entered the generator with primary resources.
- Coefficient of energy consumption - the ratio of the amount of heat consumed from secondary production to the energy received in the generator set. This indicator reflects the efficiency of using a specific energy scheme of the enterprise. Moreover, there are different ways to assess the optimal consumption volumes - with an emphasis on economically viable values, actual and planned consumption indicators.
- Fuel savings opportunities are the amount of primary resources that are not consumed by the use of industrial waste. Moreover, savings can also be calculated according to the reverse scheme, when primary and secondary resources replace each other, depending on the current conditions for generating heat or electricity.
- Utilization coefficient - the ratio of the volume of generated heat to the energy potential of the resource supplied to the processing boiler.
- Energy generation factor - the amount of energy that is directly generated by using recycled materials in a recycling unit. It should be noted that the generation coefficient differs from the output energy by the amount of heat loss in the working installation.
- The service factor is a value that determines the difference between the planned energy output and the actual output generated through the ratio.
Choosing the optimal VER model
In each case, when developing a project for energy supply through secondary resources, an economic task is brought to the fore, the essence of which is to use the most efficient raw materials. To do this, preliminary certification of all available sources of secondary resources is carried out, indicating their reserves, pollution, temperature and mode of receipt. It also defines the requirements for ensuring technological processes for the utilization of VER. Depending on the operating conditions of the enterprise and the method of processing raw materials, these can be heating, ventilation, gas and water supply systems.
At the final stage of creating a project, the following procedures are also performed:
- The most cost-effective disposal method is selected for one selected or several sources of secondary raw materials.
- The economic effect of each resource processing activity is determined.
- The operating scheme of the recycling plant is being developed in accordance with the needs of the enterprise. Also, the main technological process can be supplemented by auxiliary operations like cogeneration plants - for example, if several types of fuel are required to be converted.
Sources of secondary resources
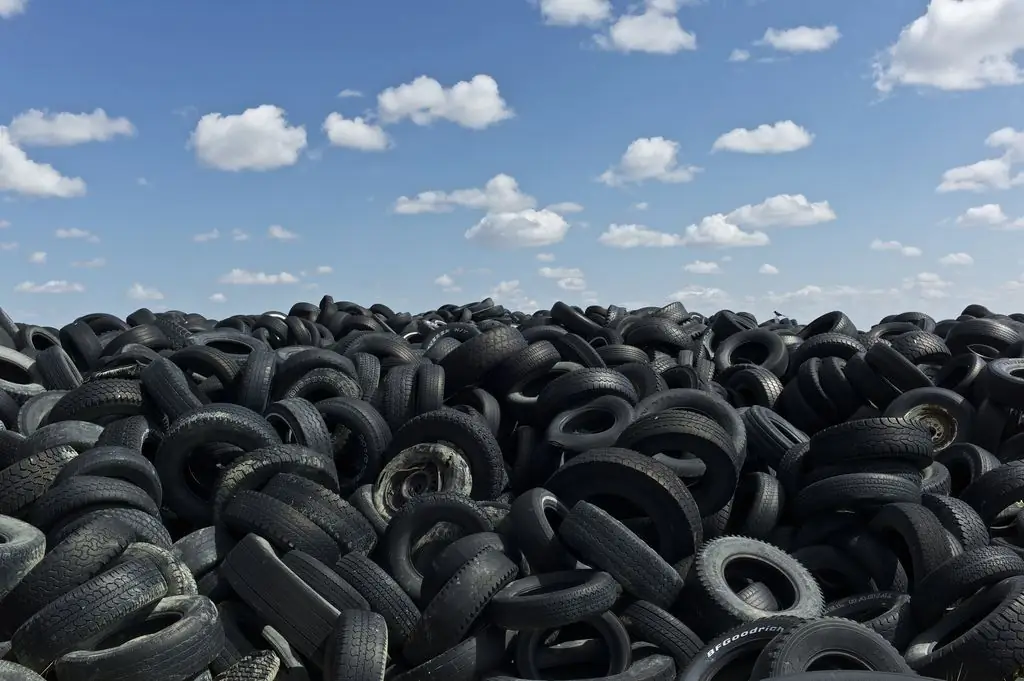
In a general sense, SER sources are understood as a set of technological processes and processed raw materials in the framework of the operation of primary energy generators. Also, different production areas can act as sources of material for the subsequent generation and conversion of heat or electricity. What is secondary energy resources? Specific types of materials are determined by the scope of primary production of raw materials. For example, metallurgical enterprises provide scrap, non-ferrous and ferrous metal waste, rubber compounds and unused alloying additives.
If we are talking about heat supply consumers, then furniture and paper factories, as well as construction woodworking enterprises that provide fuel combustible materials, will come to the fore. The following examples of secondary energy resources of this type can be given:
- Peat briquettes.
- Wood chips and bark.
- Ash from high temperature drying boilers.
- Lignin.
- Waste paper.
- Solid wood waste.
- Unclaimed cardboard and paper products.
According to the measureAs the technological processes of production become more complex, the structure of waste with emissions is also changing. Along with traditional raw materials, high-quality and complex multi-component wastes are increasingly used in secondary processing cycles. These include the following materials:
- Polymer thermoplastic elements.
- Synthetic alloy agglomerates.
- Industrial rubber products and regenerates.
- Halite waste.
- Blast furnace slag.
- Phosphogypsum.
At the same time, the level of environmental threats is also increasing. If one of the most important advantages of natural energy sources is the ecological cleanliness of generation processes, then the high efficiency of VER is to a large extent ensured by polluted and chemically aggressive substances that are not amenable to primary processing. These include oil products, sediments and sludge, worn tires, mercury-containing waste, etc.
Classification by directions of use
One of the key classifications of secondary resources, which determines the scope of energy valuable raw materials. As a rule, the following areas of use of VER are distinguished:
- Fuel combustion in units using raw materials ready for heat treatment. A simple heat generation scheme is implemented without intermediate stages of processing and conversion.
- Thermal use. Generation in thermal recovery units. Unlike the previous way of using resources, the cogeneration principle of energy generation can be implemented, but also without operations.transformations. For example, on different lines of a generator station, the use of secondary energy resources makes it possible to obtain heat, hot water or steam.
- Thermal and combined use. Along with heat generation, there is also conversion into electricity. For example, turbine units generate electricity in cogeneration or condensing forms of energy.
- Electricity. Electricity is generated with the help of a utilizing gas turbine unit.
Classification by media type
Under the carrier is understood the form of the energy resource, as well as its agrotechnical condition, under which the utilization plant will be selected. On this basis, the following recycled resources are distinguished:
- Liquid, solid and gaseous wastes.
- Pairs - worked and passing.
- Exhaust gases.
- Intermediate and finished products.
- Technical cooling water.
- Gases with increased pressure.

Classification by main types of RES
The most common are combustible and thermal secondary resources for processing at utilizing energy substations. For example, combustible VERs are typically industrial waste used as finished fuel for other industrial purposes. In this case, the following classification of secondary energy resources is applicable:
- Metallurgical blast-furnace gases.
- Wood waste in the form of chips, sawdust and shavings.
- Liquid or solid waste used in the oil refining and chemical industries.
Thermal VER provide physical heat without conversion. In this capacity, waste process gases, by-products of production, slag and ash, direct heat from operating units and apparatuses, steam and hot water can be used. It is important to emphasize that thermal resources can be used both directly as a source of heat and as raw materials, the processing of which will contribute to the production of electricity.
Resources are used less often, the potential energy of which is generated from sources of excess pressure. These are emitted types of secondary energy resources, which can be steam and gas mixtures that leave working installations into the atmosphere. Such resources are divided according to the level of energy concentration and temperature indicators. Now you can consider each of the mentioned types of VER separately.
Combustible secondary resources
In the share of world use of VER, combustible fuel occupies about 70-80%. The main type of such waste is wood and products of its processing. The target equipment for resource utilization is usually boiler-furnace units that provide technological combustion processes with heat removal. In Russia, there are also specialized plants for processing combustible types of secondary resources - for example, lignin is processed at hydrolysis plants, but due to the complexity of maintenanceproducts, such technological approaches are rare.
Relate to secondary combustible waste and car tires, which are recycled with energy release in three ways:
- With the connection of a cascade of crushers for pre-crushing.
- Using closed volume continuous compression systems in special extruders.
- With cryogenic grinding technology using liquid nitrogen.
Combined methods of burning combustible products are also popular. After sorting the raw materials according to certain characteristics (fraction, degree of contamination, chemical and structural composition), the recycling of resources of the same type is carried out. So, together with wood waste, coal and crumb rubber can be burned, if it suits the given technological characteristics. At some recycling stations, combustible waste is also prepared for further production. In particular, building materials such as hoses, mastics, fillers for various mixtures and paints and varnishes are made from activated carbon, radio engineering elements and composite materials after energy processing.
Thermal secondary energy resources
The energy potential of this type of VER also allows them to be widely used in a variety of industries and industries. The most valuable thermal resources in terms of productivity are waste gases released as a result of chemical reactions, pyrolysis and combustion of basicfuel products. Condensate heat is also used, although due to the technological complexity of energy extraction processes, this source is used only at multifunctional large enterprises with cogeneration plants. Theoretically, heat can be generated from ventilation emissions and other engineering networks with hot air and water flows, but its share in the total volume of secondary energy processing is only 2-3%.
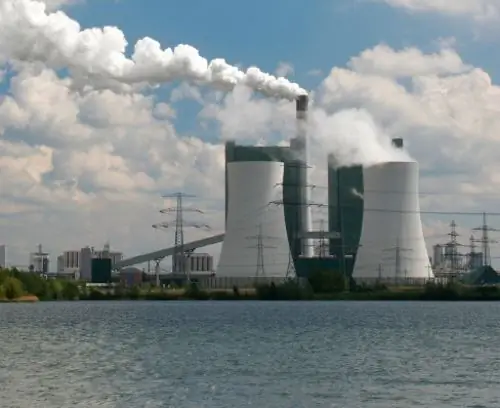
There are also restrictions on the use of heat sources of secondary energy resources, which are imposed on the supply air heating systems. In particular, the technological use of the following air media is not allowed:
- Flows removed from rooms containing flammable or explosive substances. Even if the intake site is indirectly connected to combustible gases or vapors through ventilation ducts, this air cannot be used in heat recovery units.
- Streams that can become carriers of harmful substances. This usually happens when the circulating air picks up condensing or settling particles from the processing of hazardous raw materials from the heat exchangers.
- Streams that may contain disease-causing viruses, bacteria and fungi. Biological contamination of the air environment is also determined by the specifics of a particular production or the operating conditions of an engineering system.
A characteristic feature of the use of secondary resources for the purpose of heat generation is the seasonal modeoperation of recycling facilities. This is due to the fact that a significant part of the processing boiler houses are activated during periods of heating with direct intake of thermal energy. This is especially true for utilities, but in the conditions of industrial production, thermal support for technological operations is carried out at the pace of the local schedule.
Secondary resources under overpressure
Mainly it is the production waste received as a result of technological processes of primary processing. These can be gases, liquids, and even solids. Their main feature is being under excess pressure when leaving the working installation or engineering system. It is the requirements for pressure regulation that make it difficult to use this type of secondary resources, as well as their derivatives. At a minimum, the recycle cycle should include a depressurization operation prior to release. For this, special regulators with gearboxes are used, which automatically normalize the state of the bodies to optimal performance.
VER maintenance equipment
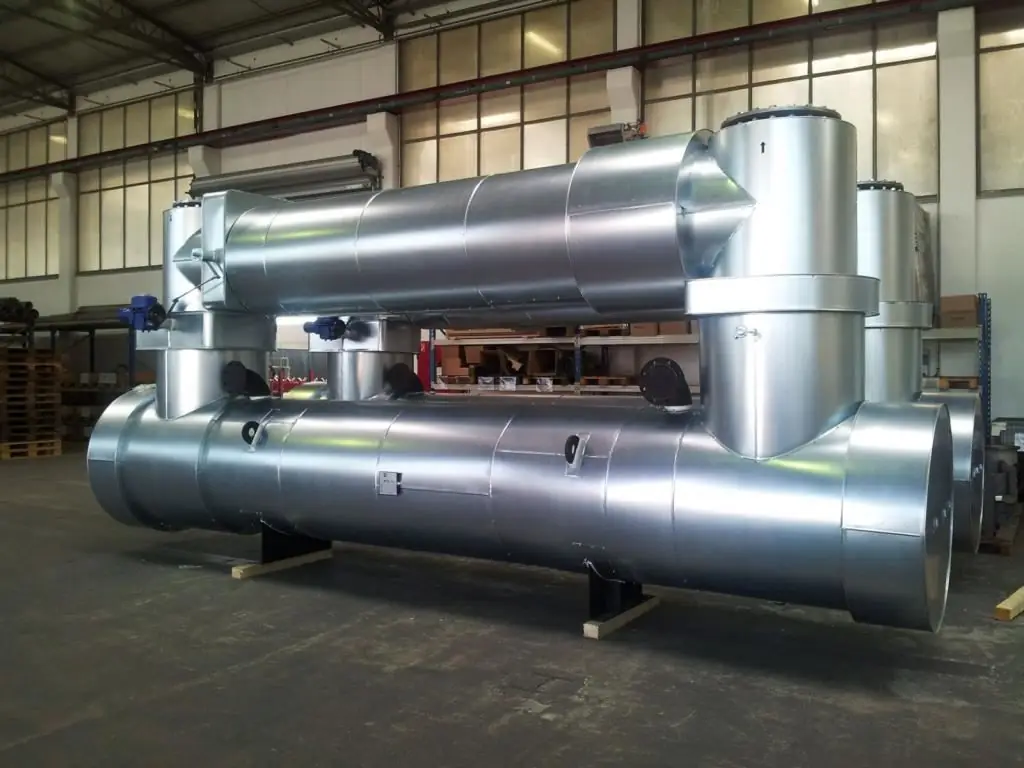
Utilization plants are used to extract energy from secondary resources, which can provide various processing and production processes. There are both specialized and universal units. Since secondary resources include media such as steam with gas and water, universal boilers and boiler plants can be considered as cogenerationequipment. The target product of such systems, as a rule, is electricity generated in large volumes.
If we talk about special narrowly targeted installations, then they include the following:
- Water recovery boilers.
- Economizers.
- Heat pumps.
- Heat exchangers.
- Absorption refrigeration systems.
- Water heaters.
- Evaporative cooling units.
- Turbine generators, etc.
Of course, for the full operation of such units, a wide range of auxiliary devices is required, due to which the system is connected to fuel sources. So, for servicing secondary energy resources in a single complex with a gas pipeline, a heat recovery unit with a separate compressor station may be required. Depending on the characteristics of the resource itself, cooling, filtration, heating, pressure regulation, etc. systems can also be used.
Use of RES for heating
At many enterprises, the possibility of space heating and heating of equipment using the energy generated by local waste is laid directly into the technological processes of production. For example, thermal boilers and furnaces emit secondary energy resources in the form of gas during operation. The waste disposal system works with the help of water heaters, which first set the temperature of the gas mixtures to about 250 °C, and then distribute the energy over the heat exchange circuits. After that, the remaining process vapors are removed throughchimney. Heated water can be used in different ways. It is usually used in the production process itself as a technical fluid or as a resource for hot water supply.
The efficiency of using such heating technologies is low and amounts to only 10-12%, but given the absence of raw material costs, this approach justifies itself. Another thing is that the use of secondary energy resources in itself requires the initial organization of conditions for generating heat and the subsequent distribution of combustion products through heat exchange networks. It may also be necessary to additionally equip production lines with units for removing unwanted suspensions and basic cleaning systems.
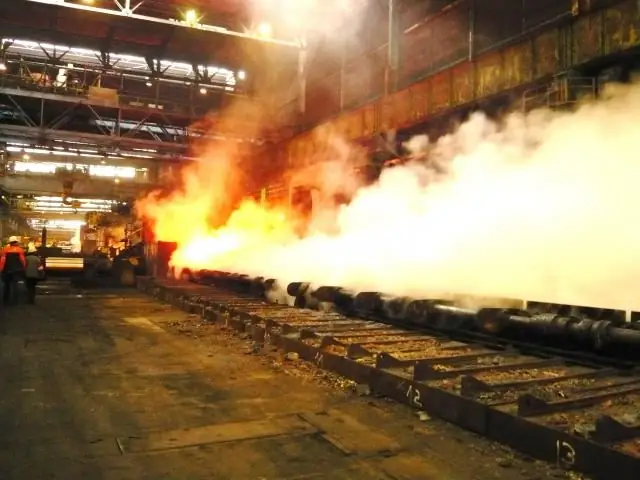
Heating outdoor areas with VER
Creating outdoor workspaces with technological equipment, according to various estimates, saves from 10 to 20% of the estimated costs of organizing production processes. Of course, there is no question of a complete exit from the workshops, but minimizing the volume of building structures when creating such sites significantly reduces the cost of projects. But at the same time, the operation of the equipment will be difficult due to the presence of snow and ice in the areas. Accordingly, there is a need to organize a heat supply system in an open area. The choice of a specific installation and the type of secondary energy resource will also depend on the direction of the enterprise and its technological waste. As a rule, inas a heat carrier, water is used, circulating in the annulus with a reverse return to the heating source. To maintain the optimal parameters of the liquid, antifreeze is additionally used, and the regulation of flows is carried out by automation with buffer expansion tanks.
Heat transfer will depend on the volume of the resource, the design of the pipeline and external microclimatic conditions. In order to maintain safety during the operation of the system in winter, it is recommended to arrange special coatings on a concrete basis. Also, in the interests of increasing thermal conductivity, technologists advise covering the structure with solutions based on heavy concrete, bas alt chips and granite inclusions. If we are talking about cold regions with severe frosts, then it is better to choose a water-based secondary energy resource with the addition of snow melting plants to the working infrastructure. The estimated amount of heat generated for the melting of snow masses and icing should be approximately 630 kJ / kg. If the design of the system does not allow the accumulation of snow in the working area, then the energy consumption for its melting at the time of precipitation will increase to 1250 kJ/kg.
Benefits of using VER
The use of alternative energy sources is usually driven by economic, technical and environmental factors. In this case, all these factors work, but the economic one is dominant. With a well-executed project for the implementation of the utilizer at the enterprise, you can count on reducing the cost of heat supply, for example, up to 25-30%. A specific savings indicator is determined by the conditions for the production and use of secondary energy resources, but there will be a benefit in any case. Especially if local and own processing materials are used at the target plant.
Another benefit comes from the high energy potential of the waste. Gases, technical fluids and solid-state production raw materials are initially selected according to the principles of maximizing the extraction of large volumes of heat. Moreover, unlike the operation of the main traditional energy carriers, secondary resources at the time of use are already in the optimal state of aggregation and temperature for processing.
Disadvantages of using VER
Wide dissemination of this concept of energy supply is hindered by several factors, the main of which is the complexity of the technological device of such systems. Even if we do not take into account the cost of equipment in the form of utilizers, the technical organization of the process will inevitably require the reorganization of the operation site, since the system will work in conjunction with different engineering units.
Another disadvantage of using secondary resources can be seen as low energy returns. Again, taking into account the free nature of this raw material, the economic feasibility will be positive, however, a modest percentage of heat transfer, in particular, will not allow, in principle, to rely on the arrangement of generating stations for the comprehensive maintenance of industries and other consumption facilities. As a rule, this is onlyauxiliary power source.
Conclusion
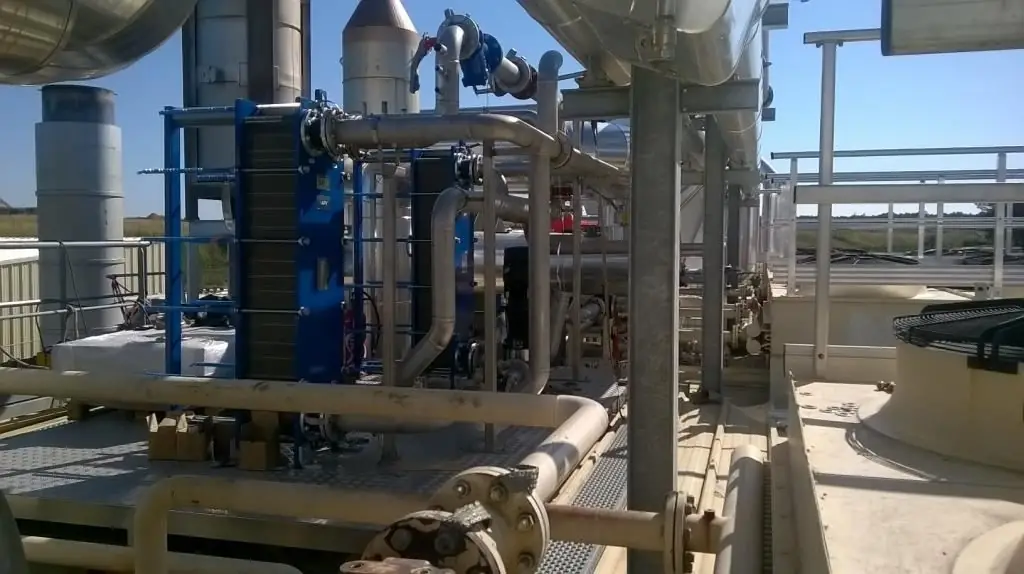
Resources for processing for the purpose of secondary energy recovery are fundamentally different from both traditional and natural sources of energy supply. They are partly due to the very origin of this raw material, but to a greater extent - the specifics of the technologies for their application. At the same time, the consumption of primary and secondary resources can occur within the same production process. For example, if fittings are manufactured at the plant, and combustion products from blast furnaces are sent to waste heat exchangers that serve other technological operations. A complete production cycle is implemented, which is more efficient, resource-saving and environmentally friendly, as waste is recycled.