One of the most common metals on Earth is aluminum. It is also called "flying metal". Although it is not found in nature in its pure form, it can be found in many minerals. And the most common alloy, which is used to produce many parts and structures, is duralumin (duralumin).
It was invented by the German scientist Alfred Wilm, who worked at the Dürener Metallwerke AG plant (Düren). He determined that an alloy of aluminum and copper has much better characteristics than the metal itself in its pure form.
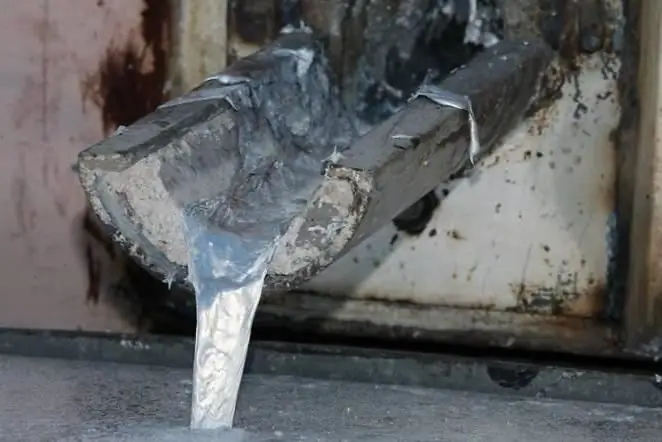
High strength alloy group
In fact, duralumin is a whole group of alloys in which the main component is aluminum, and its alloying elements are copper, zinc, manganese, magnesium. But in general, their characteristics are determined not only by the composition, but also by the method of heat treatment. In 1903, it was first discovered that during the aging process, an aluminum alloy withcopper becomes even more durable and hard.
As it turned out later, this is due to the fact that when, after hardening, the metal is at room temperature for several days, its supersaturated solid solution decomposes, and this, in turn, is accompanied by hardening of the material.
The aging process and return to the previous state
As mentioned earlier, metal aging is an important process, which is caused by structural transformations that cause changes in physical and mechanical properties. It can be natural and artificial. In the first case, the alloy is kept for several days at room temperature.
With artificial aging, the processing time is reduced, but the temperature is increased. In order to return the alloy to its previous state, it must be heated to 270 degrees for a few seconds and then quickly cooled.
Aluminum production
In order to make an alloy of aluminum with copper, you need high-tech equipment and, of course, the metal itself. It is mined from bauxite. This is a rock that needs to be crushed, water added to it and steamed under high pressure. Thus, silicon is separated from alumina. Then the thick mass is placed in a special bath with straightened cryolite. The contents are heated to 950 ° C and an electric current of 400 kA is passed through it.
This allows you to break the bond between the oxygen and aluminum atoms. As a result, the latter settles to the bottom as a liquid metal. This is how castings are made from liquid aluminum. Now metalcompletely ready for machining. However, in order to increase its strength, it is necessary to add alloying elements to it and thus obtain a high-quality aluminum-copper alloy.
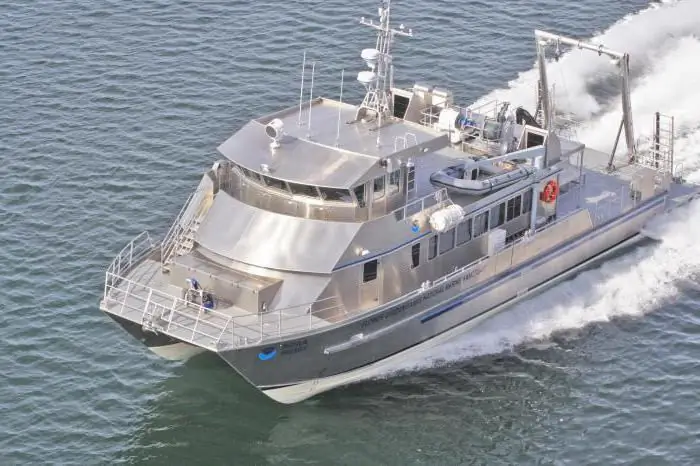
Duralumin production
In total, all aluminum alloys are divided into two groups: cast and deformed. The process of their production depends precisely on what kind should be obtained in the end. In addition, the manufacturing method also depends on the required characteristics.
For the production of duralumin, aluminum ingots are melted in an electric furnace. Interestingly, this is one of the few metals that can be converted from solid to liquid and vice versa many times. This will not affect its performance. Copper and other alloying elements such as manganese, iron, and magnesium are added in turn to molten aluminum. It is very important to observe the percentage ratio: 93% aluminum, 5% copper, the remaining 2% are other alloying elements.
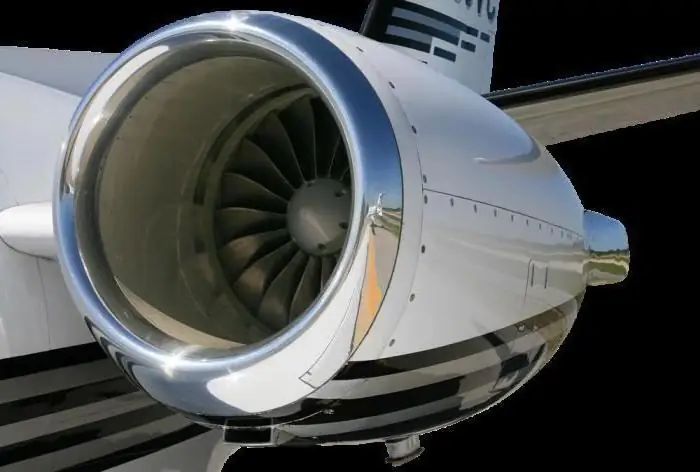
Hardening and annealing of duralumin
Mandatory for such an alloy is the hardening process. The holding time for small parts is only a few minutes, and the temperature is about 500 °C. Immediately after the procedure, duralumin is soft and viscous. It is easy to deform and process. After some time, the alloy hardens and its mechanical properties increase. If the temperature threshold is exceeded, oxidation occurs and the material loses its characteristics. After hardening, it must be slowly cooled in cool water.
So, you already know the name of aluminum-copper alloy. It often lends itself to deformation: cold rolling, drawing, forging. In this case, the so-called hardening occurs. This is a process during which the movement and multiplication of dislocations occurs in the metal structure. As a result, the alloy itself changes its structure, becomes harder and stronger. This reduces its ductility and impact strength. In order for the deformations to pass more easily and the work hardening does not destroy the metal, annealing is used. To do this, the alloy is heated to 350 ° C and then cooled in air.
Chart of the state of the alloy (aluminum and copper)
In order to most clearly describe the interaction of the components of duralumin in the solid and liquid state, as well as to explain the nature of the change in the properties of the alloy, use the state diagram.
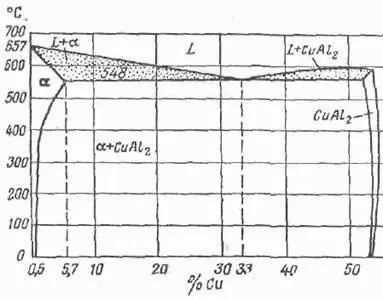
It can be seen from it that the highest solubility of Cu in an alloy with aluminum is observed at a temperature of 548 ° C and at the same time it is 5.7%. When the temperature rises, it will increase, and when it falls, it will decrease. Minimal solubility (0.5%) will be observed at room temperature. If the duralumin is hardened above 400 ° C, it will become a solid homogeneous solution - α.
During this process, the solid solution will decompose. An alloy of aluminum and copper behaves very unusually, the formula of which is CuAl2. The process is accompanied by the release of excess phase A1. This breakdown takes place duringlong time. This is the natural aging we mentioned earlier.
Alloy properties
Alloying a metal with certain elements makes it possible to increase its characteristics. Do you remember the name of aluminum-copper alloy? What properties does it have?
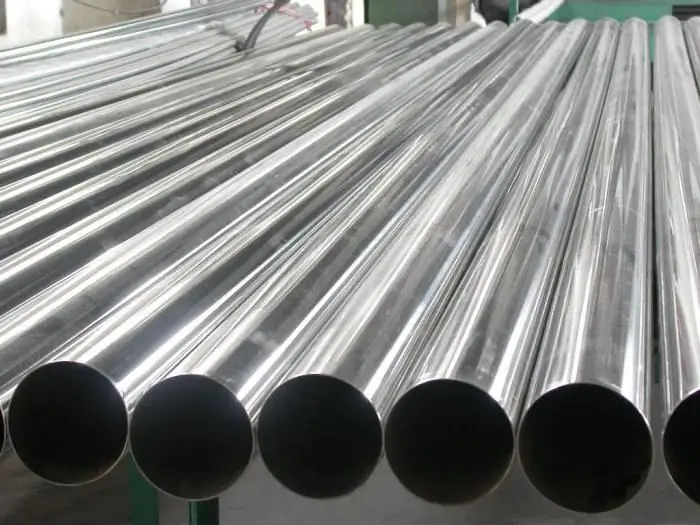
Aluminum itself is very light, soft and completely fragile. It is soluble in weakly concentrated alkalis and acids. By adding copper and magnesium to aluminum, you can already get a fairly strong alloy. Its performance is quite easy to improve - you just need to leave it to lie down at room temperature. So, the effect of aging increases the strength of duralumin, as we talked about above.
Aluminum itself is quite light. A small percentage of copper does not make the alloy heavier. Another positive characteristic is the ability to repeatedly remelt the alloy. At the same time, it will not lose its properties. The only thing that is needed is to give it a “rest” for a couple of days after casting.
The disadvantage of duralumin is its low corrosion resistance. Therefore, most often such material is covered with a clean layer of aluminum or painted with varnishes and paints.
Aluminum alloys and their applications
For the first time, duralumin was used to make airships. The lightness and strength of this material made it possible to create an excellent aircraft. For this, the D16t brand was used. At present, alloys with aluminum, zinc, copper and other alloying elements are widely used inastronautics, aviation and other areas of mechanical engineering.
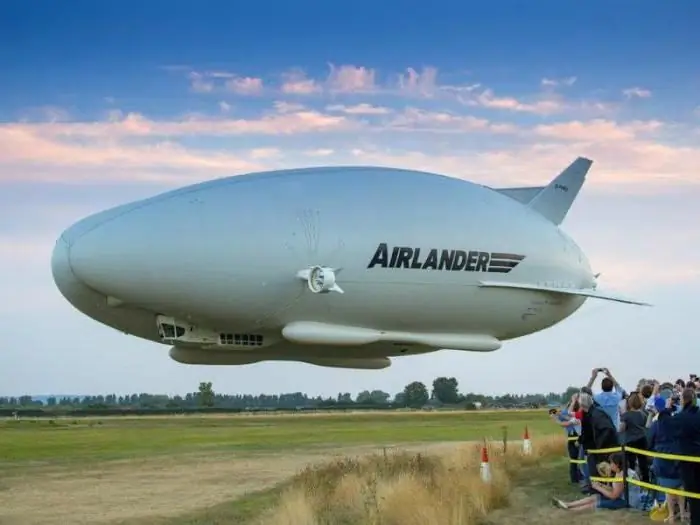
So, for example, the use of duralumin in the manufacture of a car can significantly reduce its weight and cost, but at the same time it will be strong enough.
In general, it can be noted that the range of this alloy is quite wide: pipes, wires, sheets, tapes, rods and cast parts of various shapes. D16t is still considered one of the most popular and widespread brands. The small letter "t" at the end of the marking means that the alloy is hardened and naturally aged. It is used:
- In the designs of spacecraft, ships and aircraft.
- For the manufacture of various parts for machine tools and machines.
- For the manufacture of street signs, road signs.
Everyone should know the name of the alloy of aluminum and copper. Dural is also used in the oil industry. So, special pipes made from it can ensure the operation of the well for 6-7 years.
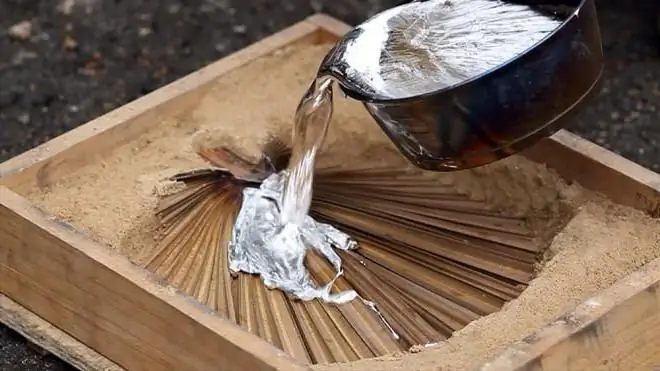
What is the name of the alloy of aluminum and copper, easy to remember. So, we told what properties it has and where it is used. It can easily replace rolled steel, especially if it is necessary to make the structure lightweight.