The chill mold is a reusable mold for pouring metal. It can be either detachable (consist of two parts) or not (shake mold). Die casting has a number of advantages over shell casting, but there are also some disadvantages, for example, when casting cast iron, castings require additional heat treatment.
Benefits
During the formation of a casting, there is intense heat transfer from the molten metal to the mold. This results in higher density, better mechanical properties of the metal, higher precision, better structure and less roughness compared to sand castings.
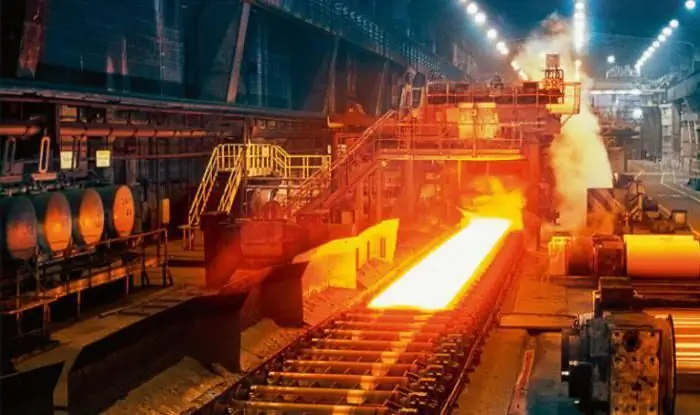
The mold casting process is also different in that the metal mold (chill mold) can be reused. It is made of high strength material, due to which the working surface of the mold is performed more accurately. This improves the surface quality of the castings, and due to the high thermal conductivity of the mold, the castings quickly solidify.
Another advantage of die casting over sand molds is that the resulting castings are less mechanically processed, and this reduces the consumption of molding materials.
He alth and ecology
Cold molding increases labor productivity by 2-3 times, because from the processtime-consuming operations such as preparation of the mixture, cleaning and molding of products are excluded. Since the production area is also decreasing, the cost of repairing and building new workshops is becoming significantly lower.
Many unhe althy work operations are eliminated from the process, such as mold knockout, casting cleaning and chipping. This contributes not only to improving working conditions, but also to reducing environmental pollution.
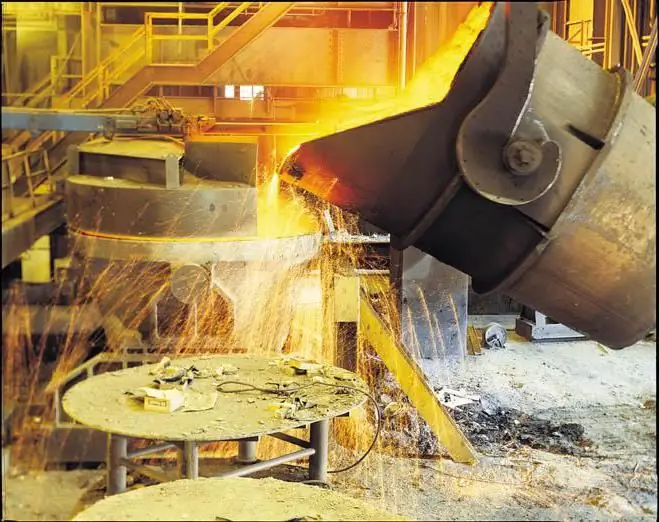
Flaws
The production of a chill mold is quite expensive due to the complexity of the process itself. If there are undercuts in the castings, the cost of the mold increases due to the need to complicate the design: inserts, disposable sand and split metal rods are used.
The life of a chill mold is determined by the number of good quality castings that can be obtained in it. The stability of the shape determines the economic feasibility of the process, especially in the process of casting steel and cast iron. Increasing the life of molds is one of the main technological challenges in this area of production.
Due to the rapid cooling and thickening of the melt, it is difficult to obtain long thin-walled products when casting into a mold. This also causes the cast iron to acquire a hard, bleached layer. The shape is malleable, which can lead to stresses and cracks in the castings. When using disposable sand cores, the accuracy of castings decreases, the surface roughness increases at the point of contact with the core.
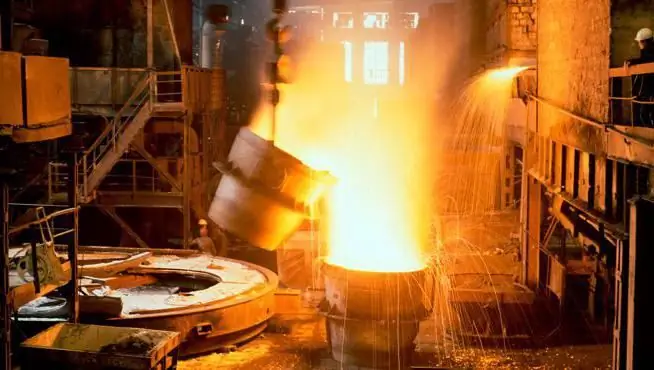
Quality castings
The casting and the mold interact with high efficiency. The casting hardens and cools in the sand mold much longer than in the mold, however, the fillability of the sand mold is usually better, which makes the production process by mold casting of non-fluid castings more laborious, and also imposes restrictions on such parameters as the size of the casting and the minimum thickness walls. Aluminum die casting (as well as copper and other non-ferrous metals) is the most popular in Russia.
However, as a result of rapid cooling, a non-porous, fine-grained structure can be obtained, which increases not only the strength, but also the ductility of the resulting casting. In the manufacture of cast iron products by chill casting, a number of problems arise: due to the peculiar crystallization in castings, the formation of carbides, ferrite-graphite eutectics is possible. This reduces the toughness and wear resistance of cast iron. The bleached surface layer in such castings is very hard, so that the products are suitable for cutting only after heat treatment (annealing), which eliminates the chill.
Shape structure
The chill mold is, as a rule, two half-molds that are fastened with clamps (pins), and immediately before the start of pouring the molten metal, the half-moulds are fixed with locks. Profits feed the casting through the so-called vents and vent plugs. Metal molds without a connector function are called shake molds.
Before pouring, the work surface of the moldtreated with a layer of a substance that protects the mold from thermal shock from a sharp increase in temperature. This measure also prevents the casting from seizing with the mold.
Steel and cast iron
Die casting of steel and cast iron occurs using powdered quartz, graphite, water glass and refractory clay as a refractory coating. Before pouring, the mold must be heated to a certain temperature, which depends on the wall thickness of the casting and the alloy used.
The main requirement that the mold material must meet is resistance to heat shocks, inevitable when pouring molten metal. For the manufacture of molds, gray cast iron, ductile iron, structural, carbon and alloy steel, as well as copper and aluminum alloys are used.
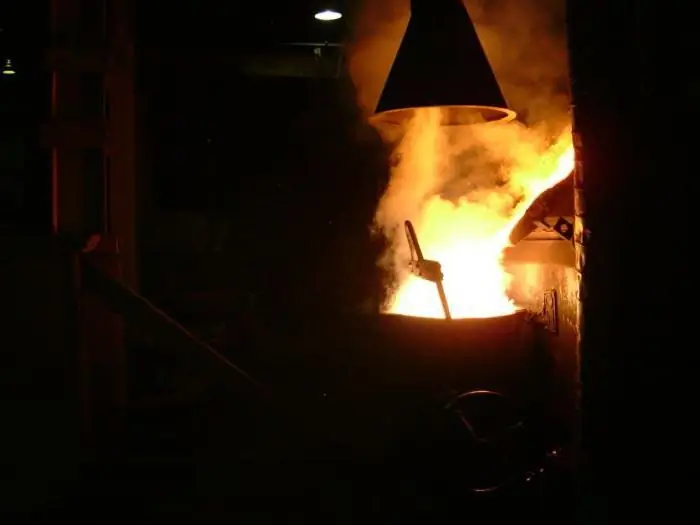
Lined chill mold
This is a type of technology that combines the advantages of shell and die casting, while the disadvantages of both methods are smoothed out. This technology is characterized not only by crack resistance, but also by ductility, which makes it possible to produce castings of high precision, and compared with shell casting, expensive molding material is consumed minimally.
Lined metal mold is made by filling the space between the metal model of the casting and the inner surface of the mold. The most commonly used sandblasting and jellied methods. For filling, a sand-resin mixture is taken, in which the binder is phenol-formaldehyde resin (2-2.6%) andurotropin (about 10% by weight), as well as self-hardening (binder - liquid glass) and ceramic compounds (binder - ethyl silicate). The chill mold and casting model, having a temperature of 200 degrees, transfer the heat of the mixture, which hardens and forms a lining layer 3-5 mm thick. Ordinary or shell rods are used to make cavities in castings.
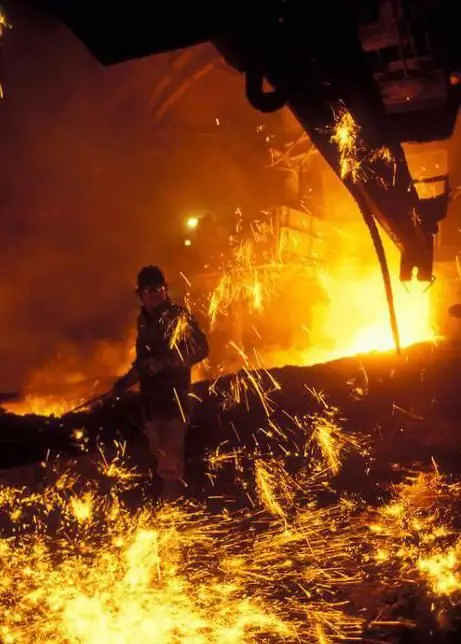
Casting process
The chill mold, covered with a layer of refractory material, heats up. The operating temperature must be at least two hundred degrees, but depends not only on the alloy used for pouring, but also on the dimensions of the casting, its wall thickness and on the properties that are required of it. After heating, rods, ceramic or sand, can be installed in the mold, if this, of course, is required according to the casting plan, and then the mold halves are connected and tightly locked with special clamps. If the casting takes place in a mold machine, then its own mold locking mechanism is used. After these preparatory measures, molten metal can be poured into the chill mold.
When the casting has already acquired some strength, metal rods can be partially removed from it. This subsequently facilitates the final removal of the cores from the castings due to the reduction of pressure on them from the solidifying metal.
After the casting has cooled to the desired temperature, the mold can be opened. At this stage, the metal rods are removed and the castings are taken out of the mold. Sand cores are knocked out, profits, risers and spruesare cut off, and the quality control of the product is carried out, after which the whole process can be repeated.
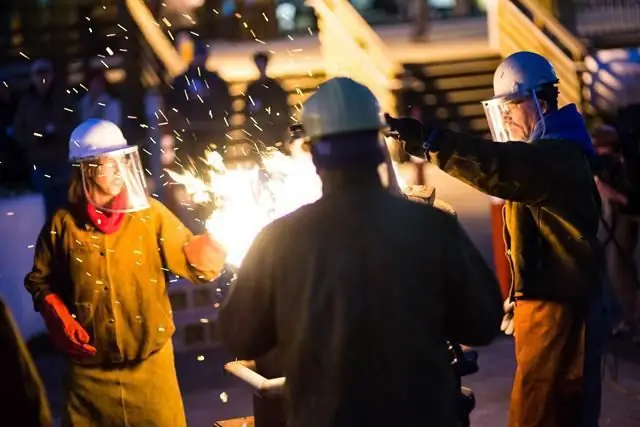
Before making a new casting, the parting plane and the mold surface are carefully examined. The refractory composition is applied once or twice per shift, however, in case of delamination from the working surface, it is necessary to restore the layer. If the product is thin-walled, the mold is strongly cooled; if the casting being made was massive enough, then the mold could heat up above the operating temperature, and then specially provided cooling systems are used, so that the mold will be cooled in any case before the next casting.
Cold casting does not involve any complex and time-consuming actions, except for the process of cooling the casting to the desired temperature. Most of the operations can be performed automatically by machines, which is one of the important advantages of the method, but the main thing is that the mold is not a one-time form.