This process was named after the outstanding Polish scientist and citizen of the Russian Empire, Jan Czochralski, who invented it back in 1915. The discovery happened by accident, although Czochralski's interest in crystals, of course, was not accidental, because he studied geology very closely.
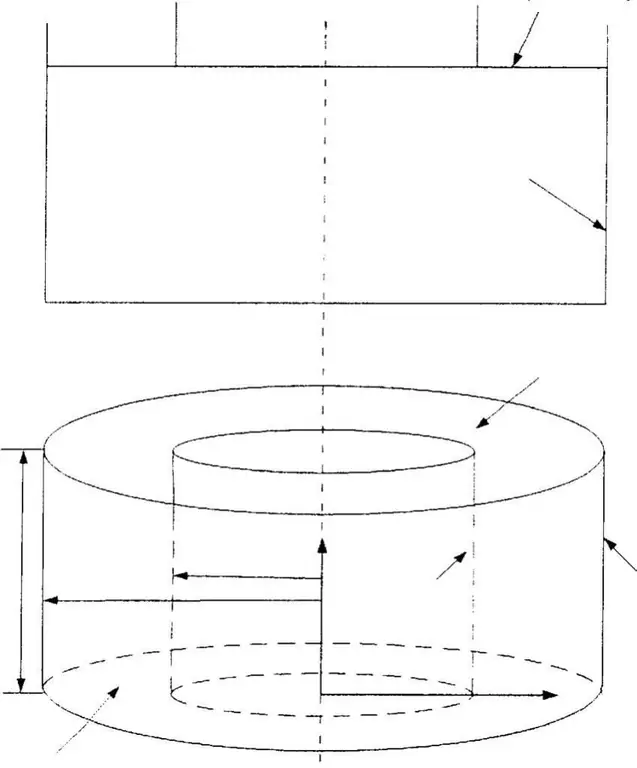
Application
Perhaps the most important area of application of this method is industry, especially heavy industry. In industry, it is still used to artificially crystallize metals and other substances, which cannot be achieved in any other way. In this regard, the method has proved its almost absolute non- alternativeness and versatility.
Silicon
Monocrystalline silicon - mono-Si. It also has another name. Silicon grown by the Czochralski method - Cz-Si. That is Czochralski silicon. It is the main material in the production of integrated circuits used in computers, televisions, mobile phones and all types of electronic equipment and semiconductor devices. silicon crystalsare also used in large quantities by the photovoltaic industry for the production of conventional mono-Si solar cells. The near-perfect crystal structure gives silicon the highest light-to-electricity conversion efficiency.
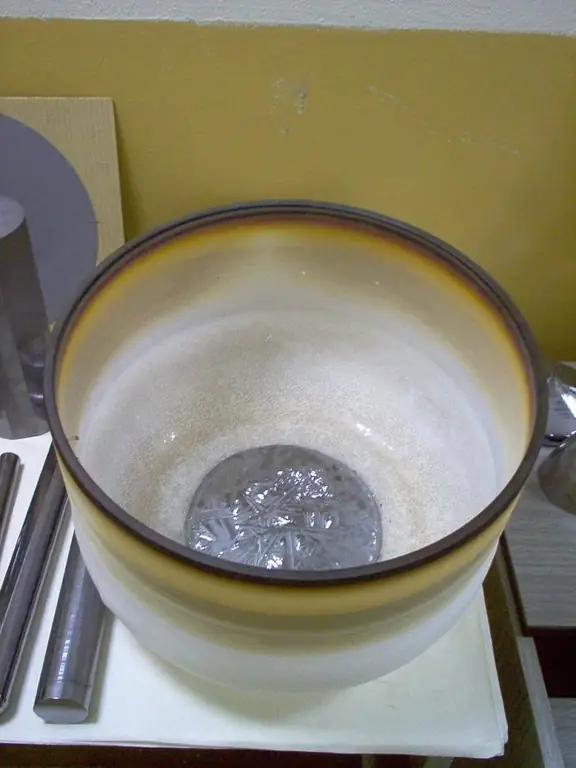
Melting
High-purity semiconductor silicon (only a few parts per million of impurities) is melted in a crucible at 1425 °C (2.597 °F, 1.698 K), usually made of quartz. Dopant impurity atoms such as boron or phosphorus can be added to molten silicon in precise amounts for doping, thereby changing it to p- or n-type silicon with different electronic properties. A precisely oriented rod-seed crystal is immersed in molten silicon. The stem of the seed crystal slowly rises up and rotates at the same time. Through precise control of temperature gradients, draw speed and rotation speed, a large single crystal billet can be removed from the melt. The occurrence of undesirable instabilities in the melt can be avoided by examining and visualizing the temperature and velocity fields. This process is usually carried out in an inert atmosphere such as argon, in an inert chamber such as quartz.
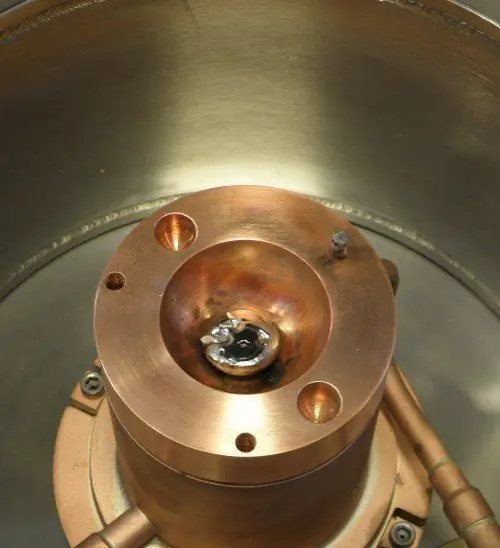
Industrial subtleties
Because of the effectiveness of the general characteristics of crystals, the semiconductor industry uses crystals with standardized sizes. In the early days, their boules were smaller, only a few incheswidth. With advanced technology, high quality device manufacturers use 200mm and 300mm diameter plates. Width is controlled by precise temperature control, rotation speed and seed holder removal speed. The crystalline ingots from which these plates are cut can be up to 2 meters long and weigh several hundred kilograms. Larger wafers allow for better manufacturing efficiency because more chips can be made on each wafer, so the stable drive has increased the size of the silicon wafers. The next step up, 450 mm, is currently scheduled to be introduced in 2018. Silicon wafers are typically about 0.2-0.75mm thick and can be polished to a large flatness to create integrated circuits or texturing to create solar cells.
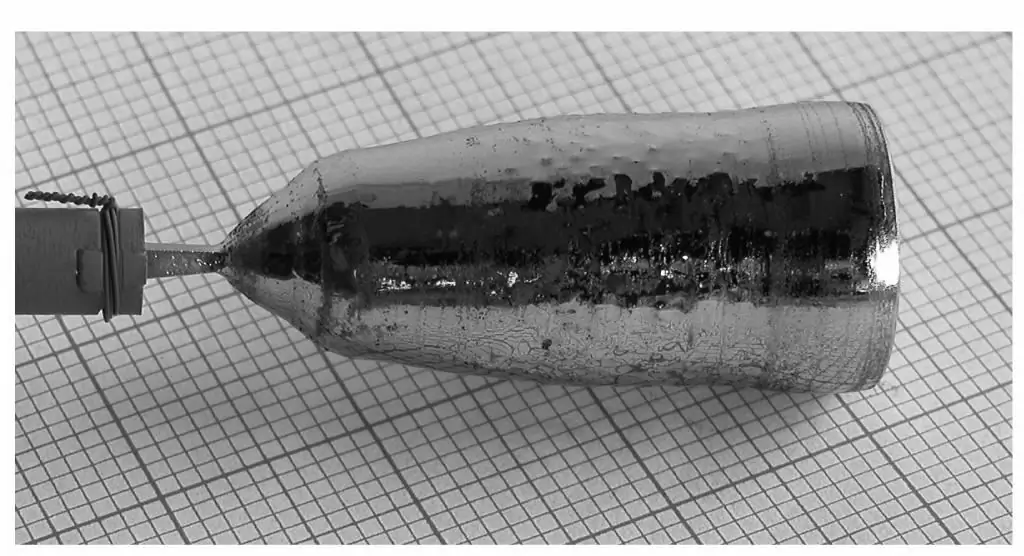
Heating
The process begins when the chamber is heated to about 1500 degrees Celsius, melting the silicon. When the silicon is completely melted, a small seed crystal mounted on the end of the rotating shaft slowly descends until it is below the surface of the molten silicon. The shaft rotates counterclockwise and the crucible rotates clockwise. The rotating rod is then pulled upward very slowly-about 25 mm per hour in the manufacture of a ruby crystal-to form a roughly cylindrical boule. The boule can be from one to two meters, depending on the amount of silicon in the crucible.
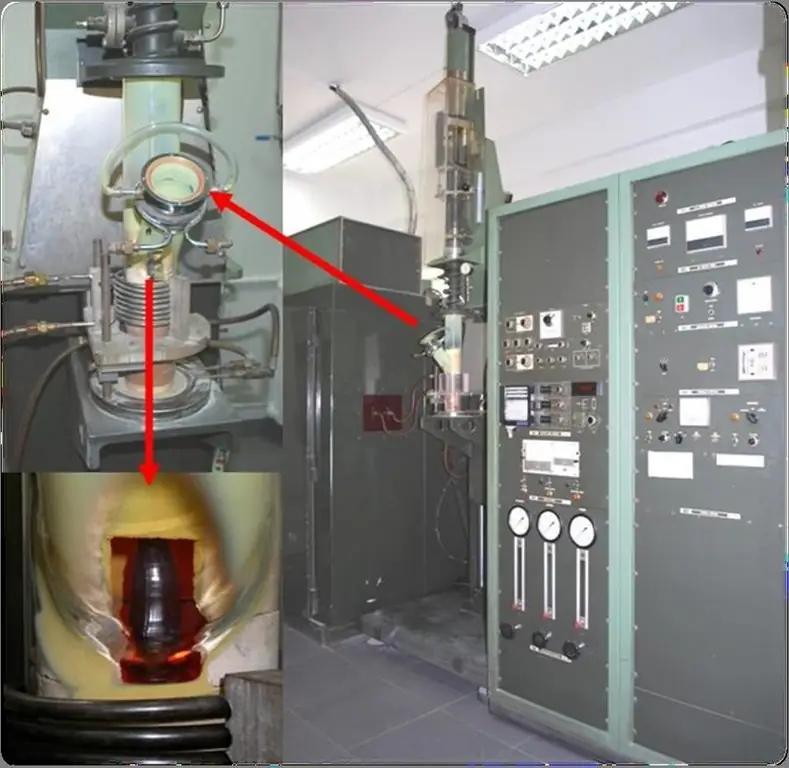
Electrical Conductivity
The electrical characteristics of silicon are adjusted by adding a material such as phosphorus or boron to it before melting it. The added material is called dopant and the process is called doping. This method is also used with semiconductor materials other than silicon, such as gallium arsenide.
Features & Benefits
When silicon is grown by the Czochralski method, the melt is contained in a silica crucible. During growth, the walls of the crucible dissolve in the melt, and the resulting substance contains oxygen at a typical concentration of 1018 cm-3. Oxygen impurities can have beneficial or harmful effects. Carefully chosen annealing conditions can lead to the formation of oxygen deposits. They affect the capture of unwanted transition metal impurities in a process known as gettering, improving the purity of the surrounding silicon. However, the formation of oxygen deposits in unintended places can also destroy electrical structures. In addition, oxygen impurities can improve the mechanical strength of silicon wafers by immobilizing any dislocations that may be introduced during device processing. In the 1990s, it was experimentally shown that high oxygen concentration is also beneficial for the radiation hardness of silicon particle detectors used in harsh radiation environments (such as CERN's LHC/HL-LHC projects). Therefore, Czochralski-grown silicon radiation detectors are considered promising candidates for many future applications.experiments in high energy physics. It has also been shown that the presence of oxygen in silicon increases impurity uptake in the post-implantation annealing process.
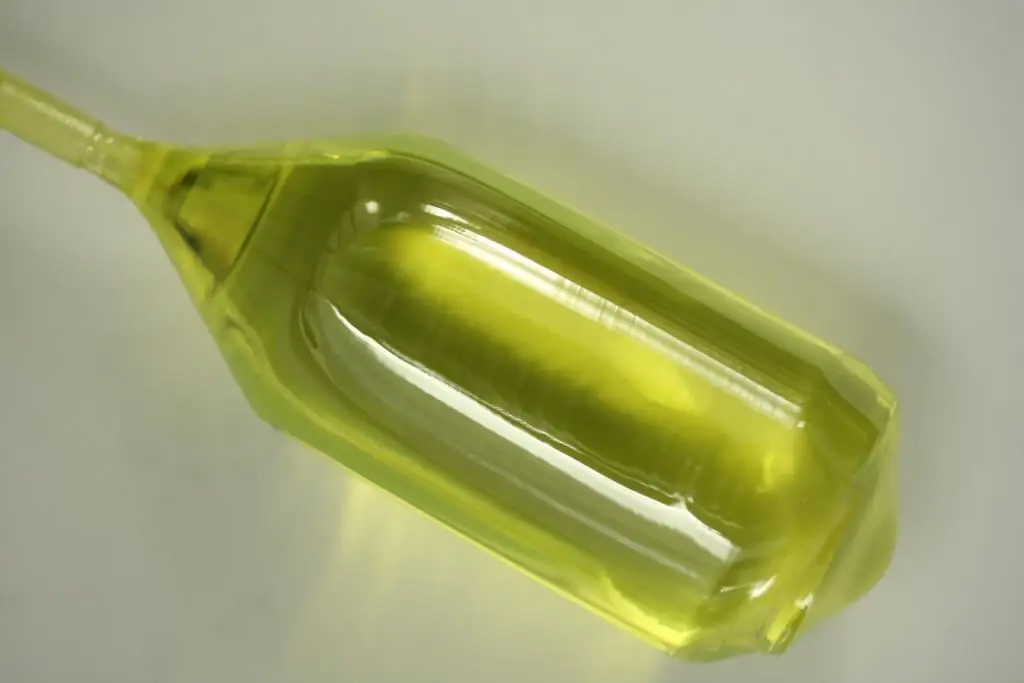
Reaction problems
However, oxygen impurities can react with boron in an illuminated environment. This leads to the formation of an electrically active boron-oxygen complex, which reduces the efficiency of the cells. Module output drops by approximately 3% during the first few hours of illumination.
The solid crystal impurity concentration resulting from volume freezing can be obtained from consideration of the segregation coefficient.
Growing crystals
Crystal growth is a process in which a pre-existing crystal becomes larger as the number of molecules or ions in their positions in the crystal lattice increases, or a solution turns into a crystal and further growth is processed. The Czochralski method is one form of this process. A crystal is defined as atoms, molecules, or ions arranged in an ordered, repeating pattern, a crystal lattice that extends through all three spatial dimensions. Thus, the growth of crystals differs from the growth of a liquid drop in that during growth, molecules or ions must fall into the correct positions of the lattice in order for an ordered crystal to grow. This is a very interesting process that has given science many interesting discoveries, such as the electronic formula of germanium.
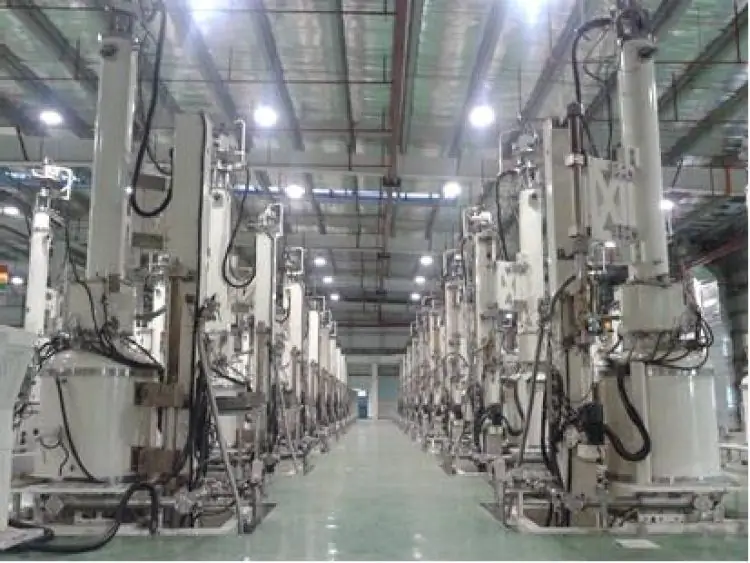
The process of growing crystals is carried out thanks to special devices - flasks and gratings, in which the main part of the process of crystallization of a substance takes place. These devices exist in large numbers in almost every enterprise that works with metals, minerals and other similar substances. During the process of working with crystals in production, many important discoveries were made (for example, the electronic formula of germanium mentioned above).
Conclusion
The method to which this article is devoted has played a large role in the history of modern industrial production. Thanks to him, people have finally learned how to create full-fledged crystals of silicon and many other substances. First in laboratory conditions, and then on an industrial scale. The method of growing single crystals, discovered by the great Polish scientist, is still widely used.