Let's talk about the role of coke in the blast furnace process. Let's take a closer look at the essence of this metallurgical production.
Today, iron and steel are made using the blast furnace process, in which the furnace is an important component.
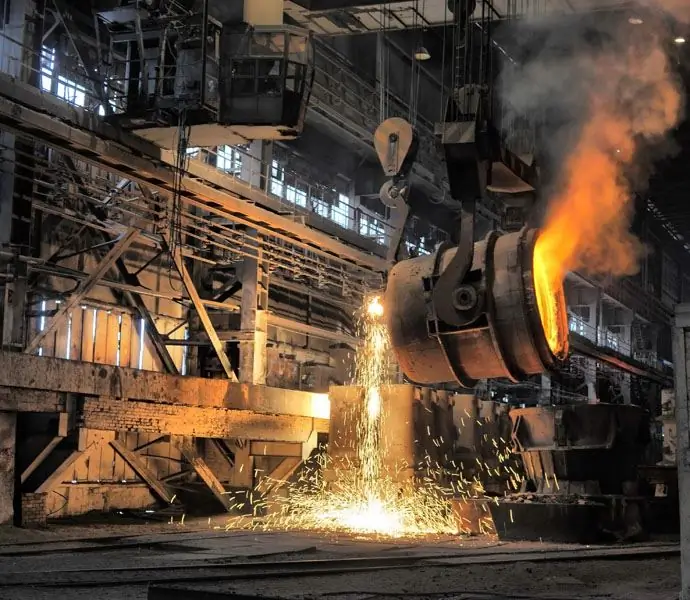
Unit specifics
Consider the features of the device, its purpose. The main processes of the blast furnace are associated with the smelting of coke. It is a porous material that is sintered from a mass of carbon obtained by calcining coal without the presence of atmospheric oxygen.
A blast furnace is a powerful and high-performance unit, where a significant amount of blast and charge is consumed.
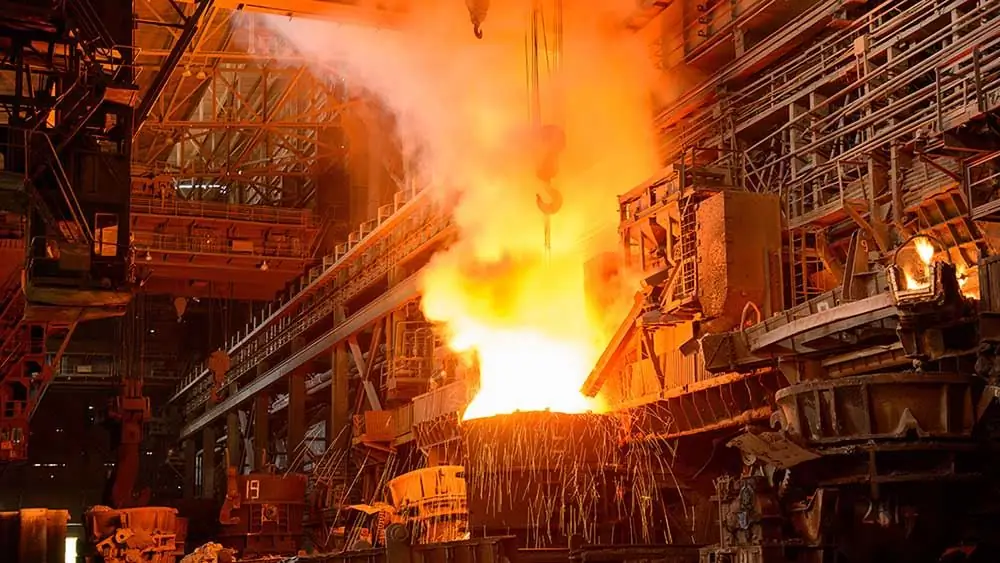
Loading raw materials
Modern blast furnace requires materials to stay in it for 4-6 hours, gaseous substances - 3-12 seconds. If the gases are completely distributed over the cross sectionfurnaces, you can count on high melting rates, iron production is underway. The blast-furnace process involves taking into account the movement of gases through zones that have a lower charge resistance. Therefore, when it is loaded into the furnace, adjustment is carried out, redistribution of coke and sinter over the cross section of the furnace so that they differ in gas permeability. Otherwise, a larger percentage of gases will leave the furnace with a significant temperature, which will negatively affect the use of thermal energy, the blast furnace process will not be fully efficient.
In those areas that have high resistance, the gas mixture will pass slightly heated, additional heat consumption will be required in the lower part of the furnace, as a result, the consumption of raw materials will increase significantly.
What other features are important to consider when downloading? The blast-furnace process for producing pig iron is an energy-intensive production. That is why a layer of less gas-permeable agglomerate is used near the walls of the furnace, and a layer of coke is increased in the center, due to which the gas flow is redistributed to the center. Materials are evenly spaced around the circumference.
The charge is loaded in separate portions - feeds. One portion consists of several skips, ore part (agglomerate), coke. The ratio of the original ingredients is determined by experts.
The blast-furnace process allows co-feeding of raw materials, in which coke and sinter skips are collected on a large cone and then loaded into a furnace.
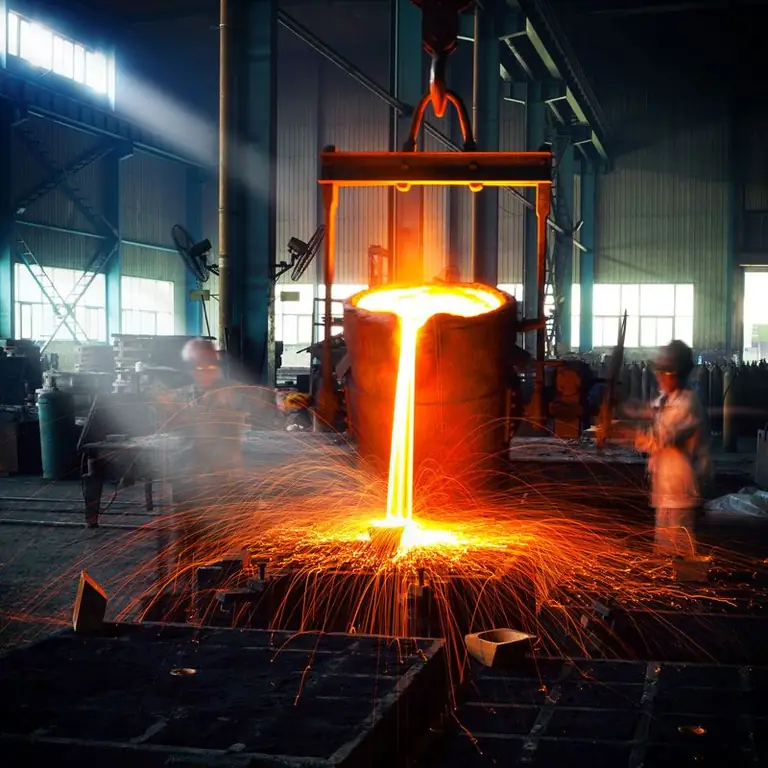
Batch distribution adjustment
The distribution of coke and agglomerate over the cross section of the tops is controlled by the following methods:
- changing the order of raw materials on the big cone;
- split and split serves apply;
- movable plates are installed near the walls of the top.
The blast-furnace process involves taking into account certain regularities of introducing bulk materials:
- laying raw materials falling from a large cone on a top with an elevation - a comb;
- At the crest (at the point of fall) of the charge, fines accumulate, large pieces roll down to the foot of the crest, therefore, in this zone, the gas permeability of the charge is greater;
- the crest is affected by the level of backfill on the top, as well as the distance with a large cone;
- the big cone does not go down completely, so small pieces of coke get to the periphery.
Majorly the center of the kiln receives material from the feed skips, which were the last to be loaded into the large cone. If you change the loading order, you can achieve a redistribution of materials across the cross section of the top.
To control the process of distribution of the used charge over the volume of the furnace, two cone apparatuses are used. Recently, some blast furnaces are equipped with movable plates near the walls of the top, allowing you to change the angle of inclination, move them along a horizontal plane.
Pieces of the charge that fall on the plates are reflected from them, which allows you to direct the raw materials to certain zones of the top.
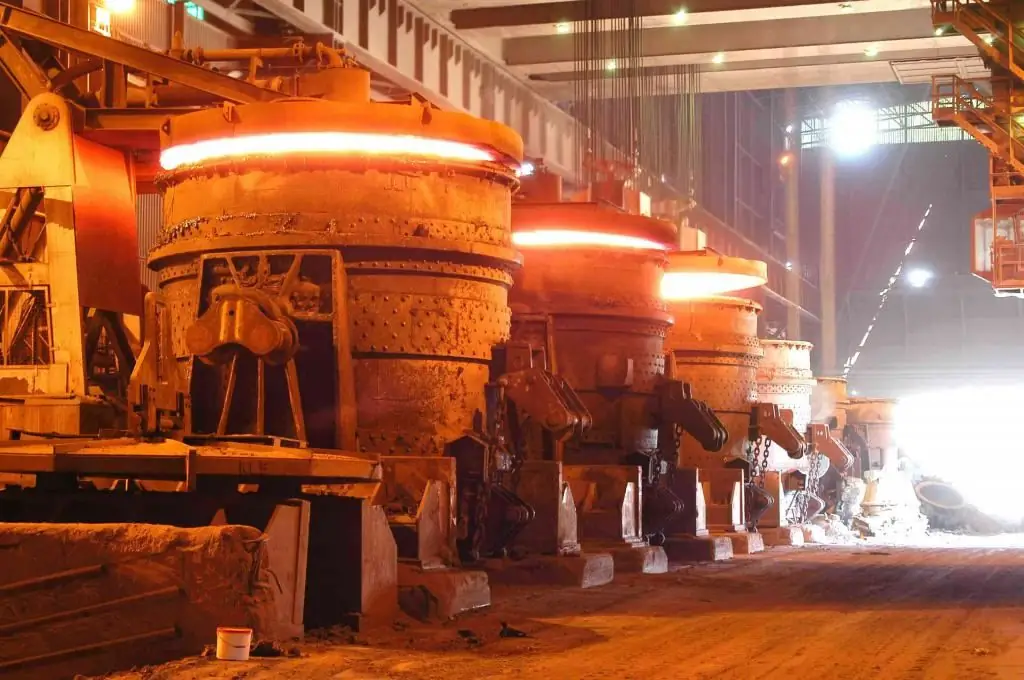
Stove optionsno taper
In furnaces that do not have a cone loading device, the loading of raw materials is carried out through two sluice hoppers that open alternately. Raw materials are delivered to them by inclined belt conveyors, on which coke and sinter are located at clear intervals. One portion comes from the belt into one bunker, then it is unloaded onto the top of the furnace along a rotating inclined tray. During the unloading period, they make about ten full revolutions around the fixed central axis.
Load cycle
It is customary to call it a repeating number of batches of charge materials. The maximum portion is determined by the volume of the lock hopper of the charging mechanism. The number of servings in one cycle can be from 5 to 14. How to get the products of the blast-furnace process in full? In order to answer this question, let's take a closer look at the essence of the process. With an increased content of carbon dioxide in the mixture, low temperature contributes to the completeness of the heat exchange and chemical processes in the blast furnace. In order for the apparatus to work economically and intensively, the quantitative content of carbon dioxide along the axis and on the periphery of the furnace should be reduced, and at a height of one or two meters from the walls - increased.
Temperature control in new ovens is carried out by introducing probes through holes in the casing. Mandatory for all processes is the control of the filling level at the top.
Among the innovations is the use of non-contact level measurement methods based on the readings of microwave and infrared sensors.
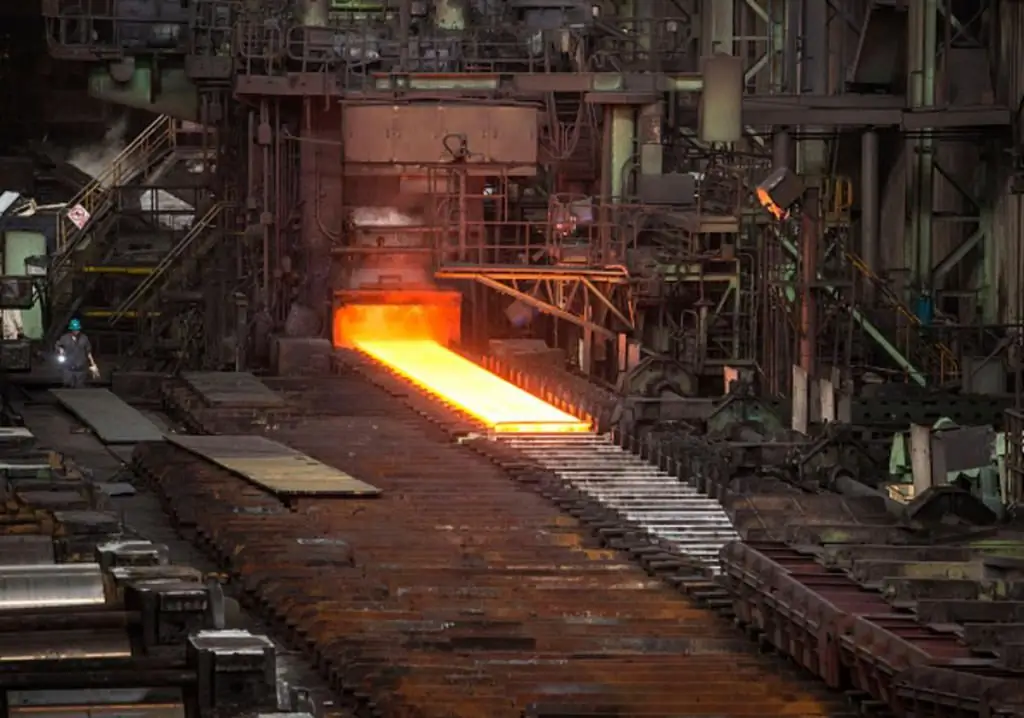
Temperature distribution features
In addition to the heat that is introduced by heated blast, as the main source of heat for heating gases and charge, carrying out recovery and compensating for heat losses, it is possible to compensate for losses with heat that is released during the combustion of fuel in the upper part of the hearth. As the gaseous products move upwards from the hearth, the heat descends to the cold charge materials, and heat exchange occurs. A similar process explains the temperature drop from 1400 to 200 degrees at the outlet of the furnace top.
Remove excess moisture
Let's consider the main physical and chemical processes in a blast furnace. In the mixture, which is loaded into the blast furnace, there is hygroscopic moisture. For example, in the composition of coke, its content can be up to five percent. Moisture evaporates quickly on the top, so additional heat is required to remove it.
Hydrate moisture appears when brown iron ore and kaolin are loaded into the blast furnace. To solve the problem in modern iron production, these ores are practically not used as raw materials.
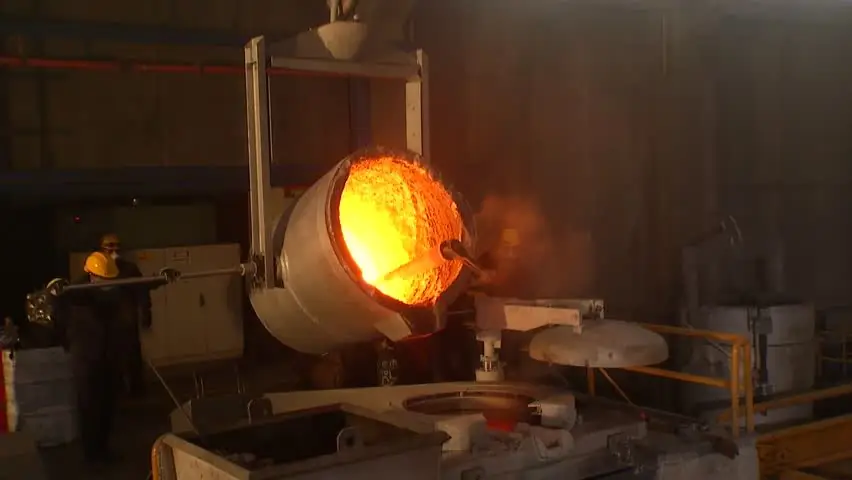
Processes of decomposition of carbonates
S alts of carbonic acid can enter the blast furnace. As they heat up, they decompose into oxides of calcium and carbon, and the process is accompanied by the release of a sufficient amount of energy.
Recently, almost no ore has been loaded into blast furnaces. What is the role of fluxes in the blast furnace process? They increase its effectivenessallow to reduce production costs. Thanks to the use of fluxed sinter, the complete removal of limestone from the blast-furnace charge can achieve significant coke savings. The process of decomposition of limestone during agglomeration is provided by the combustion of low-grade fuel.
Iron recovery
Iron is introduced into the blast furnace in the form of oxides. The main objective of the process is to maximize the extraction of iron from oxides by reduction. The essence of the process is to remove oxygen, carbon, carbon monoxide, hydrogen are used for this. Reduction with carbon is called a direct process, and the reaction with gaseous substances is called an indirect interaction. What are their distinguishing features? In the direct reaction, carbon is consumed, as a result of which its amount is significantly reduced. The second type of reduction of iron from oxides requires an excess amount of hydrogen.
The process produces solid iron. The degree of recovery in cast iron is 99.8%. Thus, only 0.2 -1% turn into slag.
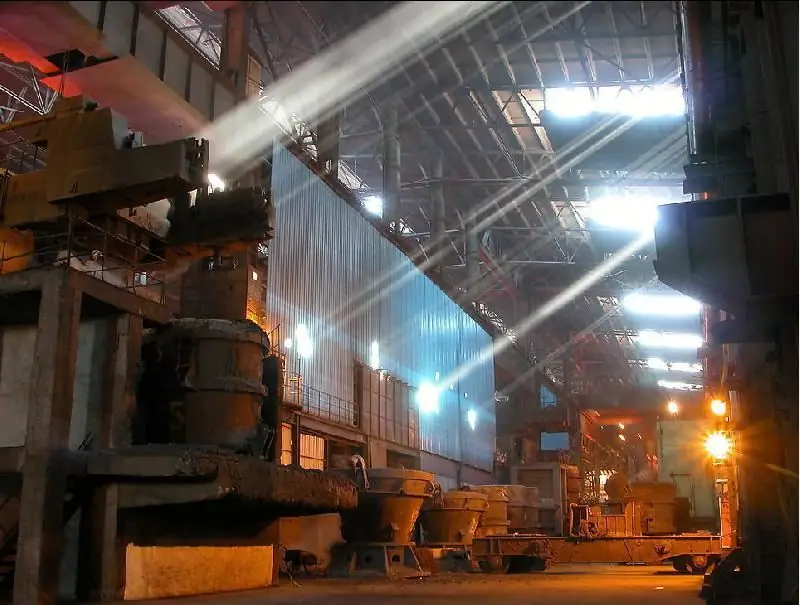
Smelting manganese cast iron
In the process of smelting remanufactured cast iron, manganese enters the blast furnace in the form of an agglomerate. In some quantities, manganese ores in the form of manganese silicates contribute to the production of manganese cast iron.
Recovery from manganese oxides occurs in steps. In order to complete the process, high temperatures must be set in the furnace. The process of smelting pig iron is accompanied byreduction of manganese only in the ratio of 55-65%. At present, due to the scarcity of manganese ores and manganese, a small amount of manganese cast iron has been used in the technological chain. When switching to low-manganese cast irons, it is possible to save not only manganese itself, but also coke, since its consumption for direct reduction of the metal will decrease.
Conclusion
The blast furnace process is one of the main methods of iron and steel smelting. Depending on what components are introduced into the initial mixture, various types of the finished product are currently obtained. Among the areas of application of the resulting cast iron and steel, we single out: mechanical engineering, chemical industry, medicine, instrument making.