Corrosion rate is a multifactorial parameter that depends both on external environmental conditions and on the internal properties of the material. In the normative and technical documentation, there are certain restrictions on the permissible values of metal destruction during the operation of equipment and building structures to ensure their trouble-free operation. In engineering, there is no universal method for determining the corrosion rate. This is due to the complexity of taking into account all factors. The most reliable method is to study the operation history of the facility.
Criteria
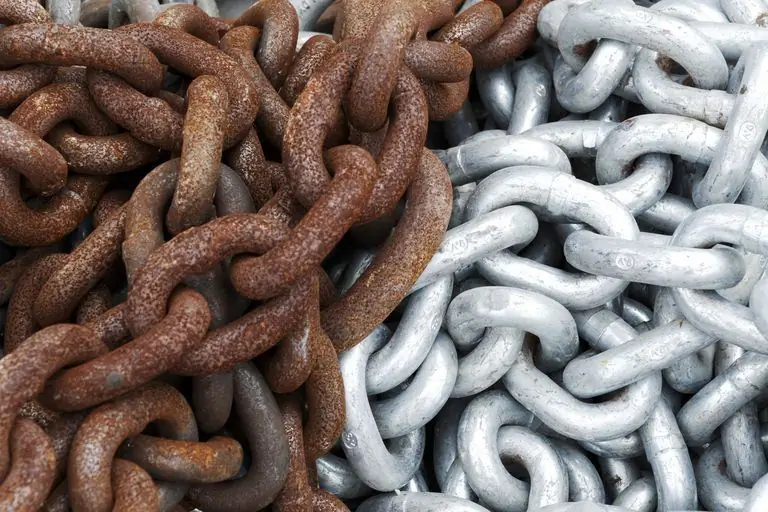
Currently, several corrosion rates are used in engineering design:
- According to the direct method of assessment: reduction in the mass of a metal part per unit surface - weight indicator (measured in grams per 1 m2 for 1 hour); damage depth (or corrosion process permeability), mm/year; the amount of the released gas phase of corrosion products; the length of time during which the first corrosion damage appears; number of corrosion centers per unit areasurfaces that appeared over a certain period of time.
- Indirectly estimated: electrochemical corrosion current strength; electrical resistance; change in physical and mechanical characteristics.
The first direct valuation indicator is the most common.
Calculation formulas
In the general case, the weight loss that determines the corrosion rate of the metal is found by the following formula:
Vkp=q/(St), where q is the decrease in the mass of the metal, g;
S - surface area from which the material was transferred, m2;
t - time period, hours
For sheet metal and shells made from it, determine the depth index (mm/year):
H=m/t, m is the depth of penetration into the metal.
There is the following relationship between the first and second indicators described above:
H=8, 76Vkp/ρ, where ρ is the density of the material.
Main factors affecting corrosion rate
The following groups of factors influence the rate of metal destruction:
- internal, related to the physical and chemical nature of the material (phase structure, chemical composition, surface roughness of the part, residual and operating stresses in the material, and others);
- external (environmental conditions, speed of movement of a corrosive medium, temperature, composition of the atmosphere, the presence of inhibitors or stimulants, and others);
- mechanical (development of corrosion cracks, destruction of metal under the action of cyclic loads,cavitation and fretting corrosion);
- design features (selection of metal grade, gaps between parts, roughness requirements).
Physical and chemical properties
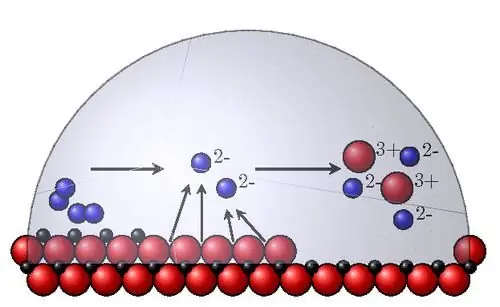
The most important internal corrosion factors are:
- Thermodynamic stability. To determine it in aqueous solutions, reference Pourbaix diagrams are used, along the abscissa axis of which the pH of the medium is plotted, and along the ordinate axis, the redox potential. A potential shift in the positive direction means greater stability of the material. Tentatively, it is defined as the normal equilibrium potential of the metal. In reality, materials corrode at different rates.
- The position of an atom in the periodic table of chemical elements. The metals most susceptible to corrosion are alkali and alkaline earth metals. The rate of corrosion decreases as the atomic number increases.
- Crystal structure. It has an ambiguous effect on destruction. The coarse-grained structure itself does not lead to an increase in corrosion, but is favorable for the development of intergranular selective destruction of grain boundaries. Metals and alloys with a homogeneous distribution of phases corrode evenly, while those with a non-uniform distribution corrode according to a focal mechanism. The mutual arrangement of the phases performs the function of the anode and cathode in an aggressive environment.
- Energy inhomogeneity of atoms in the crystal lattice. Atoms with the highest energy are located at the corners of the facesmicroroughnesses and are active centers of dissolution during chemical corrosion. Therefore, careful machining of metal parts (grinding, polishing, finishing) increases corrosion resistance. This effect is also explained by the formation of denser and more continuous oxide films on smooth surfaces.
Influence of medium acidity
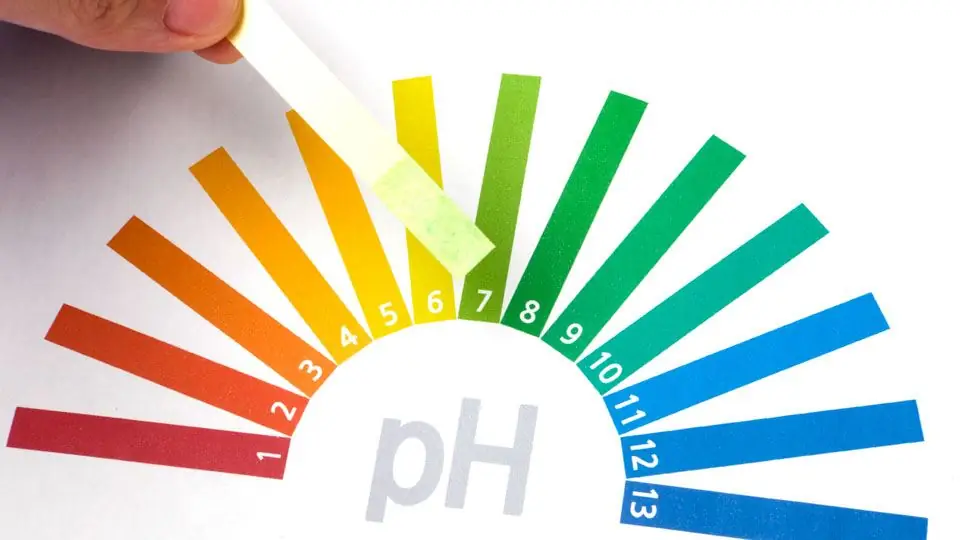
In the process of chemical corrosion, the concentration of hydrogen ions affects the following points:
- solubility of corrosion products;
- formation of protective oxide films;
- metal destruction rate.
When pH is in the range of 4-10 units (acidic solution), the corrosion of iron depends on the intensity of oxygen penetration to the surface of the object. In alkaline solutions, the corrosion rate first decreases due to surface passivation, and then, at pH >13, increases as a result of the dissolution of the protective oxide film.
For each type of metal there is its own dependence of the intensity of destruction on the acidity of the solution. Noble metals (Pt, Ag, Au) are resistant to corrosion in an acidic environment. Zn, Al are rapidly destroyed in both acids and alkalis. Ni and Cd are resistant to alkalis but corrode easily in acids.
Composition and concentration of neutral solutions
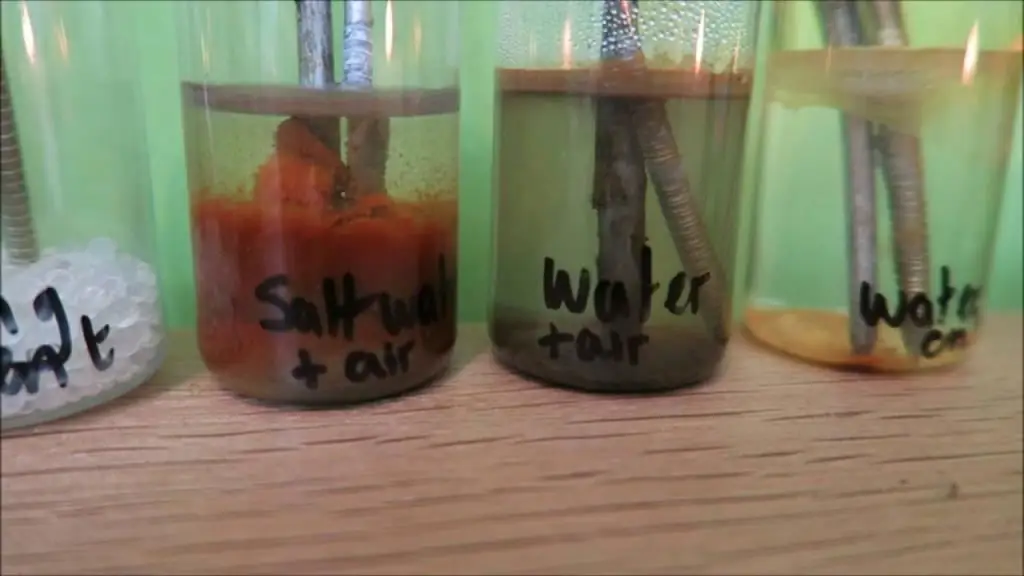
The rate of corrosion in neutral solutions depends more on the properties of the s alt and its concentration:
- During the hydrolysis of s alts inin a corrosive environment, ions are formed that act as activators or retarders (inhibitors) of metal destruction.
- Those compounds that increase pH also increase the rate of the destructive process (for example, soda ash), and those that reduce acidity decrease it (ammonium chloride).
- In the presence of chlorides and sulfates in the solution, the destruction is activated until a certain concentration of s alts is reached (which is explained by the intensification of the anode process under the influence of chlorine and sulfur ions), and then gradually decreases due to a decrease in the solubility of oxygen.
Some types of s alts are capable of forming an insoluble film (for example, iron phosphate). This helps protect the metal from further destruction. This property is used when applying rust neutralizers.
Corrosion inhibitors
Corrosion inhibitors (or inhibitors) differ in their mechanism of action on the redox process:
- Anode. Thanks to them, a passive film is formed. This group includes compounds based on chromates and bichromates, nitrates and nitrites. The last type of inhibitors is used for interoperational protection of parts. When using anodic corrosion inhibitors, it is necessary to first determine their minimum protective concentration, since adding in small quantities can lead to an increase in the rate of destruction.
- Cathode. The mechanism of their action is based on a decrease in the concentration of oxygen and, accordingly, a slowdown in the cathodic process.
- Shielding. These inhibitors isolate the metal surface by forming insoluble compounds that are deposited as a protective layer.
The last group includes rust neutralizers, which are also used for cleaning oxides. They usually contain phosphoric acid. Under its influence, metal phosphating occurs - the formation of a strong protective layer of insoluble phosphates. Neutralizers are applied with a spray gun or roller. After 25-30 minutes, the surface acquires a white-gray color. After the composition dries, paints and varnishes are applied.
Mechanical action
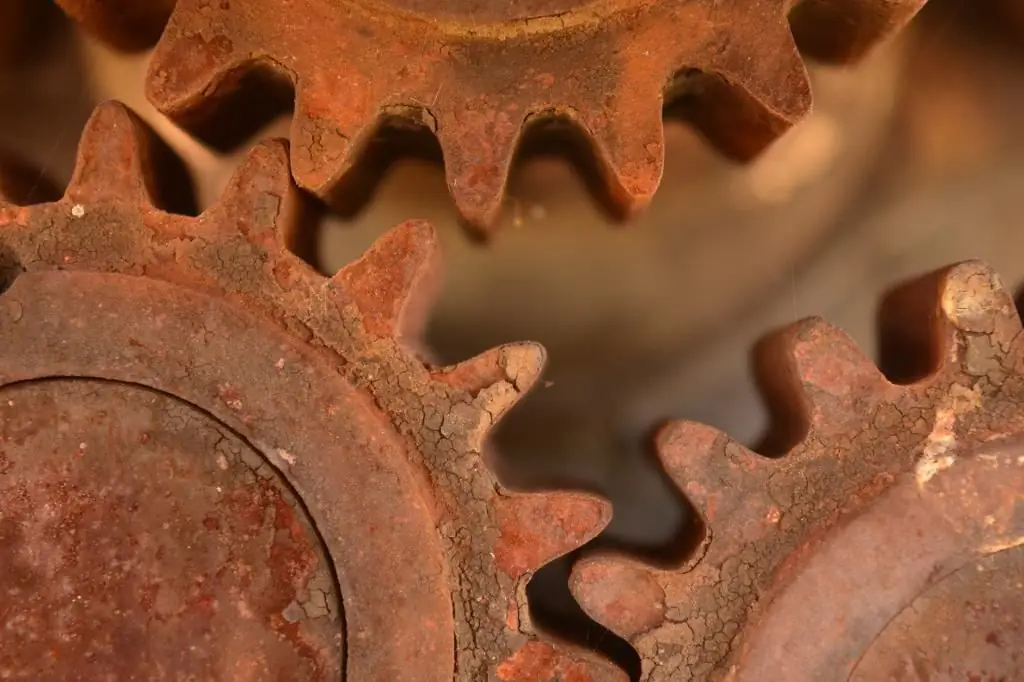
An increase in corrosion in an aggressive environment is facilitated by such types of mechanical action as:
- Internal (during molding or heat treatment) and external (under the influence of an externally applied load) stresses. As a result, electrochemical inhomogeneity occurs, the thermodynamic stability of the material decreases, and corrosion cracking is formed. Especially fast is the destruction under tensile loads (cracks are formed in perpendicular planes) in the presence of oxidizing anions, for example, NaCl. A typical example of devices subject to this type of destruction are parts of steam boilers.
- Alternating dynamic action, vibration (corrosion fatigue). There is an intensive decrease in the fatigue limit, multiple microcracks are formed, which then merge into one large one. Numbercycles to failure to a greater extent depends on the chemical and phase composition of metals and alloys. Pump shafts, springs, turbine blades and other equipment are subject to such corrosion.
- Friction of parts. Rapid corrosion is due to mechanical wear of the protective films on the surface of the part and chemical interaction with the environment. In liquid, the rate of destruction is lower than in air.
- Cavitation impact. Cavitation occurs when the continuity of the liquid flow is violated as a result of the formation of vacuum bubbles that collapse and create a pulsating effect. As a result, deep damage of a local nature occurs. This type of corrosion is often seen in chemical apparatus.
Design Factors
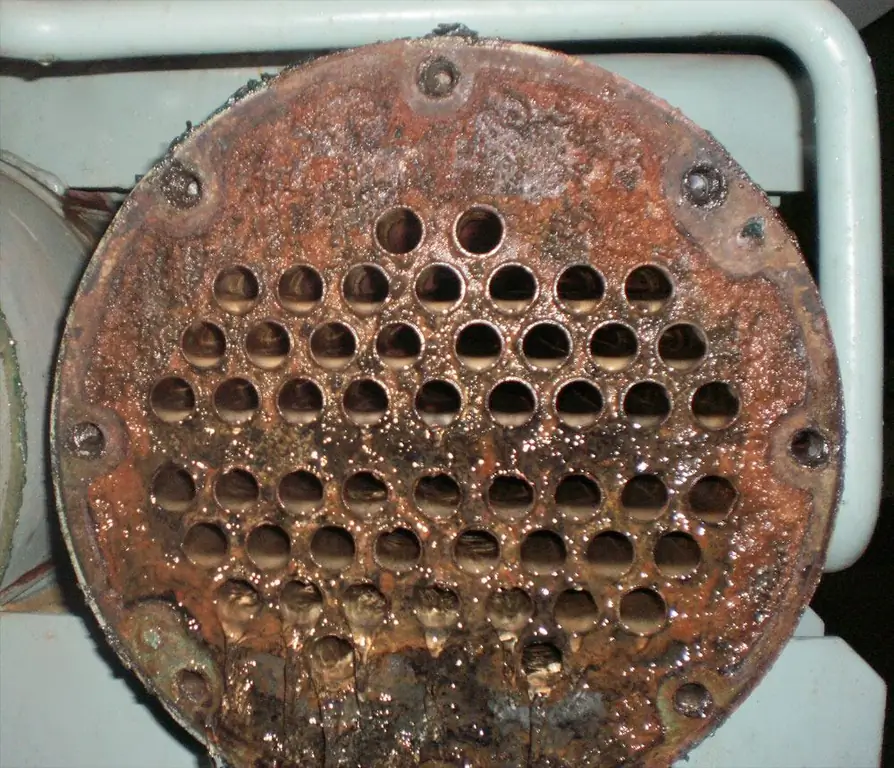
When designing elements operating in aggressive conditions, it must be taken into account that the corrosion rate increases in the following cases:
- when dissimilar metals come into contact (the greater the difference in the electrode potential between them, the higher the current strength of the electrochemical process of destruction);
- in the presence of mechanical stress concentrators (grooves, slots, holes, and others);
- with low cleanliness of the machined surface, as this results in local short-circuited galvanic pairs;
- with a significant difference in temperature of individual parts of the apparatus (thermal galvanic cells are formed);
- in the presence of stagnant zones (slots, gaps);
- when formingresidual stresses, especially in welded joints (to eliminate them, it is necessary to provide for heat treatment - annealing).
Evaluation methods
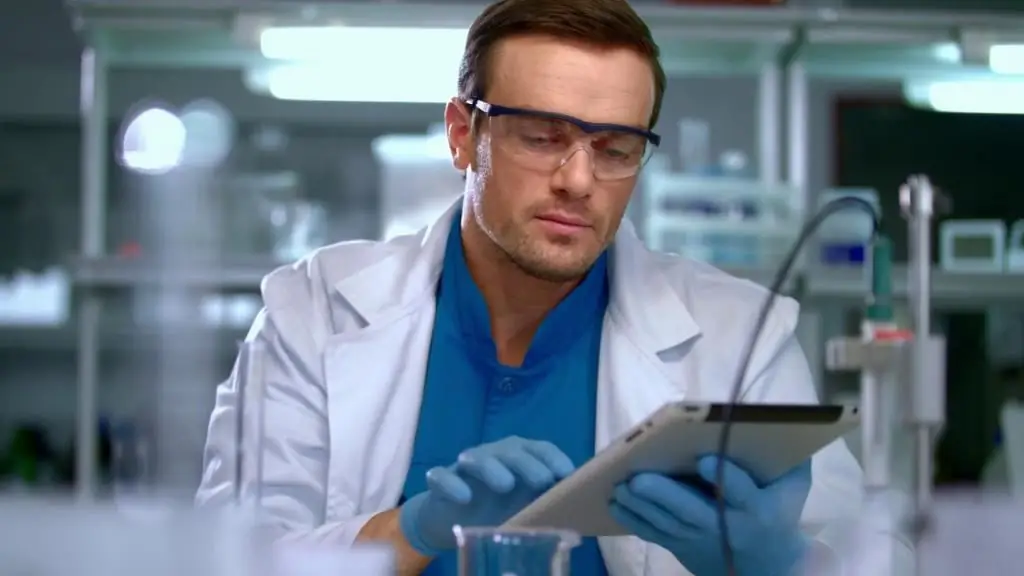
There are several ways to assess the rate of destruction of metals in aggressive environments:
- Laboratory - testing samples in artificially simulated conditions close to real. Their advantage is that they allow you to reduce the time of the study.
- Field - held in natural conditions. They take a long time. The advantage of this method is obtaining information about the properties of the metal in the conditions of further operation.
- In-situ testing of finished metal objects in the natural environment.