To evaluate the performance properties of products and determine the physical and mechanical characteristics of materials, various instructions, GOSTs and other regulatory and advisory documents are used. Methods for testing the destruction of a whole series of products or samples of the same type of material are also recommended. This is not a very economical method, but it is effective.
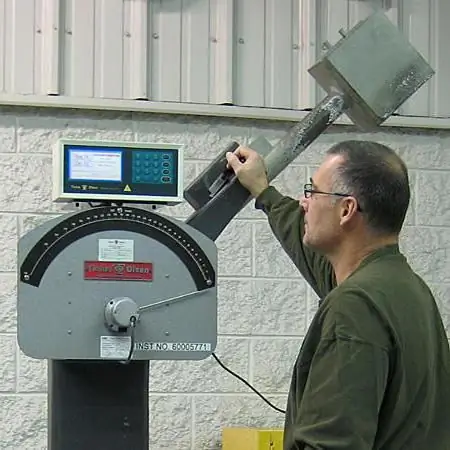
Definition of characteristics
The main characteristics of the mechanical properties of materials are as follows.
1. Tensile strength or tensile strength - that stress force that is fixed at the highest load before the destruction of the sample. The mechanical characteristics of the strength and plasticity of materials describe the properties of solids to resist irreversible changes in shape and destruction under the influence of external loads.
2. The conditional yield strength is the stress when the residual strain reaches 0.2% of the sample length. This isthe least stress while the specimen continues to deform without a noticeable increase in stress.
3. The limit of long-term strength is called the greatest stress, at a given temperature, causing the destruction of the sample for a certain time. The determination of the mechanical characteristics of materials focuses on the ultimate units of long-term strength - destruction occurs at 7,000 degrees Celsius in 100 hours.
4. The conditional creep limit is the stress that causes at a given temperature for a certain time in the sample a given elongation, as well as the creep rate. The limit is the deformation of the metal for 100 hours at 7,000 degrees Celsius by 0.2%. Creep is a certain rate of deformation of metals under constant loading and high temperature for a long time. Heat resistance is the resistance of a material to fracture and creep.
5. The fatigue limit is the highest value of the cycle stress when fatigue failure does not occur. The number of loading cycles can be given or arbitrary, depending on how the mechanical testing of materials is planned. Mechanical characteristics include fatigue and endurance of the material. Under the action of loads in the cycle, damage accumulates, cracks are formed, leading to destruction. This is fatigue. And the fatigue resistance property is endurance.
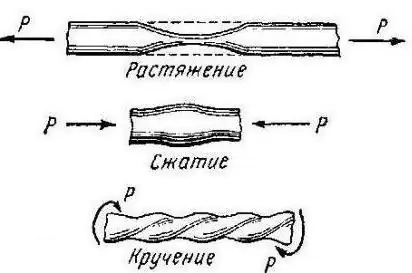
Stretch and shrink
Materials used in engineeringpractice are divided into two groups. The first is plastic, for the destruction of which significant residual deformations must appear, the second is brittle, collapsing at very small deformations. Naturally, such a division is very arbitrary, because each material, depending on the conditions created, can behave both as fragile and as plastic. It depends on the nature of the stress state, temperature, strain rate and other factors.
The mechanical characteristics of materials in tension and compression are eloquent for both ductile and brittle. For example, mild steel is tested in tension, while cast iron is tested in compression. Cast iron is brittle, steel is ductile. Brittle materials have greater compressive strength, while tensile deformation is worse. Plastic have approximately the same mechanical characteristics of materials in compression and tension. However, their threshold is still determined by stretching. It is these methods that can more accurately determine the mechanical characteristics of materials. The tension and compression diagram is shown in the illustrations for this article.
Fragility and plasticity
What is plasticity and fragility? The first is the ability not to collapse, receiving residual deformations in large quantities. This property is decisive for the most important technological operations. Bending, drawing, drawing, stamping and many other operations depend on the characteristics of plasticity. Ductile materials include annealed copper, brass, aluminum, mild steel, gold, and the like. Much less ductile bronzeand dural. Almost all alloyed steels are very weakly ductile.
The strength characteristics of plastic materials are compared with the yield strength, which will be discussed below. The properties of brittleness and plasticity are greatly influenced by temperature and loading rate. Fast tension makes the material brittle, while slow tension makes it ductile. For example, glass is a brittle material, but it can withstand a long-term load if the temperature is normal, that is, it shows the properties of plasticity. And mild steel is ductile, but under shock load it appears as a brittle material.
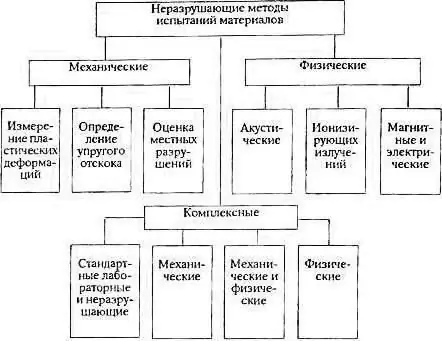
Variation method
Physico-mechanical characteristics of materials are determined by the excitation of longitudinal, bending, torsional and other, even more complex types of vibrations, and depending on the size of the samples, shapes, types of receiver and exciter, methods of attachment and schemes for applying dynamic loads. Large-sized products are also subject to testing using this method, if the method of application in the methods of applying the load, excitation of vibrations and registering them is significantly changed. The same method is used to determine the mechanical characteristics of materials when it is necessary to assess the rigidity of large-sized structures. However, this method is not used for local determination of material characteristics in a product. The practical application of the technique is possible only when the geometric dimensions and density are known, when it is possible to fix the product on supports, and on theproduct - converters, certain temperature conditions are needed, etc.
For example, when changing temperature regimes, one or another change occurs, the mechanical characteristics of materials become different when heated. Almost all bodies expand under these conditions, which affects their structure. Any body has certain mechanical characteristics of the materials of which it is composed. If these characteristics do not change in all directions and remain the same, such a body is called isotropic. If the physical and mechanical characteristics of materials change - anisotropic. The latter is a characteristic feature of almost all materials, just to a different extent. But there are, for example, steels, where the anisotropy is very insignificant. It is most pronounced in such natural materials as wood. In production conditions, the mechanical characteristics of materials are determined through quality control, where various GOSTs are used. An estimate of heterogeneity is obtained from statistical processing when the test results are summarized. Samples should be numerous and cut from a specific design. This method of obtaining technological characteristics is considered quite laborious.
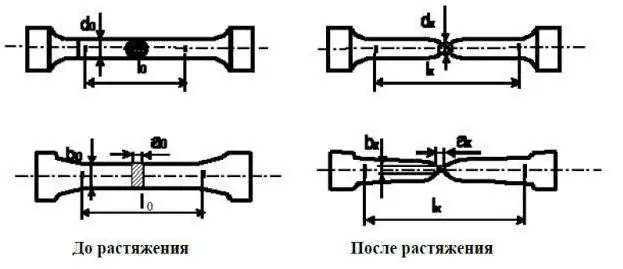
Acoustic method
There are a lot of acoustic methods for determining the mechanical properties of materials and their characteristics, and they all differ in the ways of input, reception and registration of oscillations in sinusoidal and pulsed modes. Acoustic methods are used in the study, for example, of building materials, their thickness and tension state, during flaw detection. The mechanical characteristics of structural materials are also determined using acoustic methods. Numerous various electronic acoustic devices are already being developed and mass-produced, which allow recording elastic waves, their propagation parameters both in sinusoidal and pulsed modes. On their basis, the mechanical characteristics of the strength of materials are determined. If elastic oscillations of low intensity are used, this method becomes absolutely safe.
The disadvantage of the acoustic method is the need for acoustic contact, which is not always possible. Therefore, these works are not very productive if it is necessary to urgently obtain the mechanical characteristics of the strength of materials. The result is greatly influenced by the state of the surface, the geometric shapes and dimensions of the product under study, as well as the environment where the tests are carried out. To overcome these difficulties, a specific problem must be solved by a strictly defined acoustic method or, on the contrary, several of them should be used at once, it depends on the specific situation. For example, glass-reinforced plastics lend themselves well to such a study, since the propagation velocity of elastic waves is good, and therefore end-to-end sounding is widely used, when the receiver and emitter are located on opposite surfaces of the sample.
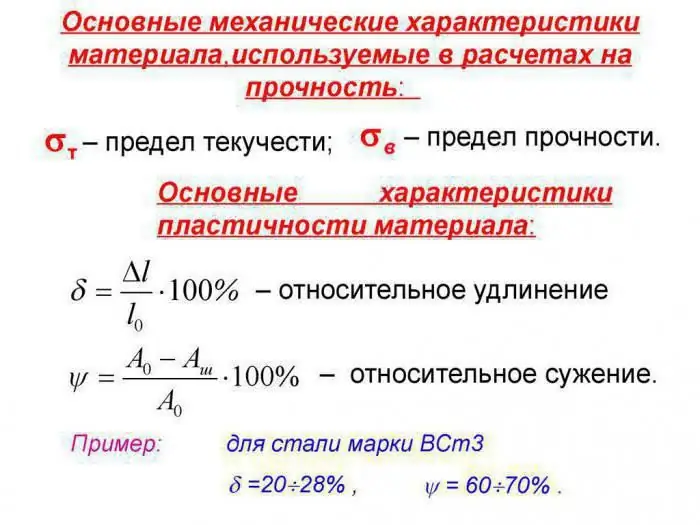
Defectoscopy
Defectoscopy methods are used to control the quality of materials in various industries. There are non-destructive and destructive methods. Non-destructive include the following.
1. Magnetic flaw detection is used to determine surface cracks and lack of penetration. Areas that have such defects are characterized by stray fields. You can detect them with special devices or simply apply a layer of magnetic powder over the entire surface. In places of defects, the location of the powder will change already when applied.
2. Defectoscopy is also carried out with the help of ultrasound. The directional beam will be reflected (scattered) differently even if there are any discontinuities even deep inside the sample.
3. Defects in the material are well shown by the radiation method of research, based on the difference in the absorption of radiation by a medium of different density. Gamma flaw detection and X-ray are used.
4. Chemical flaw detection. If the surface is etched with a weak solution of nitric acid, hydrochloric acid or a mixture of them (aqua regia), then in places where there are defects, a network appears in the form of black stripes. You can apply a method in which sulfur prints are removed. In places where the material is inhomogeneous, sulfur should change color.
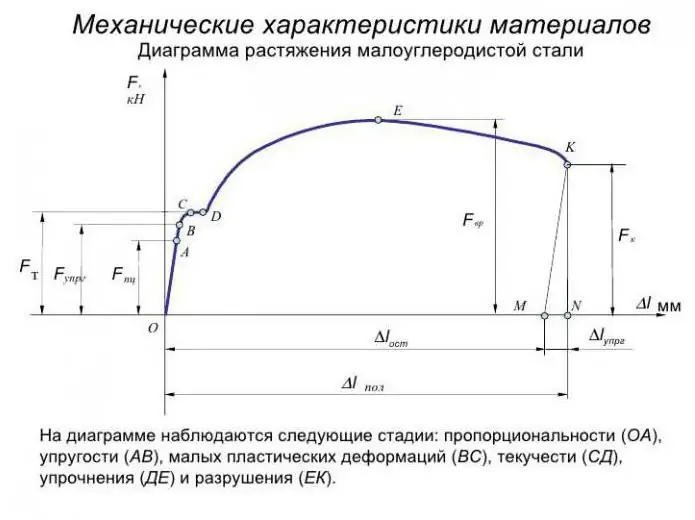
Destructive methods
Destructive methods are already partially dismantled here. Samples are tested for bending, compression, tension, that is, static destructive methods are used. If the productare tested with variable cyclic loads on impact bending - dynamic properties are determined. Macroscopic methods draw a general picture of the structure of the material and in large volumes. For such a study, specially polished samples are needed, which are subjected to etching. So, it is possible to identify the shape and arrangement of grains, for example, in steel, the presence of crystals with deformation, fibers, shells, bubbles, cracks and other inhomogeneities of the alloy.
Microscopic methods study the microstructure and reveal the smallest defects. Samples are preliminarily ground, polished and then etched in the same way. Further testing involves the use of electrical and optical microscopes and X-ray diffraction analysis. The basis of this method is the interference of rays that are scattered by the atoms of a substance. The characteristics of the material are controlled by analyzing the X-ray diffraction pattern. The mechanical characteristics of materials determine their strength, which is the main thing for building structures that are reliable and safe in operation. Therefore, the material is tested carefully and by different methods in all conditions that it is able to accept without losing a high level of mechanical characteristics.
Control methods
For non-destructive testing of the characteristics of materials, the right choice of effective methods is of great importance. The most accurate and interesting in this regard are the methods of flaw detection - defect control. Here it is necessary to know and understand the differences between methods for implementing flaw detection methods and methods for determining the physicalmechanical characteristics, since they are fundamentally different from each other. If the latter are based on the control of physical parameters and their subsequent correlation with the mechanical characteristics of the material, then flaw detection is based on the direct conversion of radiation that is reflected from a defect or passes through a controlled environment.
The best thing, of course, is complex control. The complexity lies in the determination of the optimal physical parameters, which can be used to identify the strength and other physical and mechanical characteristics of the sample. And also, at the same time, an optimal set of means for controlling structural defects is developed and then implemented. And, finally, an integral assessment of this material appears: its performance is determined by a whole range of parameters that helped determine non-destructive methods.
Mechanical testing
Mechanical properties of materials are tested and evaluated with the help of these tests. This type of control appeared a long time ago, but still has not lost its relevance. Even modern high-tech materials are often and severely criticized by consumers. And this suggests that the examinations should be carried out more carefully. As already mentioned, mechanical tests can be divided into two types: static and dynamic. The former check the product or sample for torsion, tension, compression, bending, and the latter for hardness and impact strength. Modern equipment helps to perform these not too simple procedures with high quality and to identify all operational problems.properties of this material.
Tensile testing can reveal the resistance of a material to the effects of applied constant or increasing tensile stress. The method is old, tested and understandable, used for a very long time and is still widely used. The sample is stretched along the longitudinal axis by means of a fixture in the testing machine. The tensile rate of the sample is constant, the load is measured by a special sensor. At the same time, the elongation is monitored, as well as its compliance with the applied load. The results of such tests are extremely useful if new designs are to be made, since no one yet knows how they will behave under load. Only the identification of all parameters of the elasticity of the material can suggest. Maximum stress - the yield strength makes the definition of the maximum load that a given material can withstand. This will help calculate the margin of safety.

Hardness test
The stiffness of the material is calculated from the modulus of elasticity. The combination of fluidity and hardness helps to determine the elasticity of the material. If the technological process contains such operations as broaching, rolling, pressing, then it is simply necessary to know the magnitude of possible plastic deformation. With high plasticity, the material will be able to take any shape under the appropriate load. A compression test can also serve as a method for determining the margin of safety. Especially if the material is fragile.
Hardness is tested usingIdentator, which is made of a much harder material. Most often, this test is carried out according to the Brinell method (a ball is pressed in), Vickers (a pyramid-shaped identer) or Rockwell (a cone is used). An identifier is pressed into the surface of the material with a certain force for a certain period of time, and then the imprint remaining on the sample is studied. There are other fairly widely used tests: for impact strength, for example, when the resistance of a material is evaluated at the moment of application of a load.