Bronze is an alloy based on copper. Auxiliary metals can be nickel, zinc, tin, aluminum and others. In this article, we will consider types, technological features, chemical. the composition of bronze, as well as methods for its manufacture.
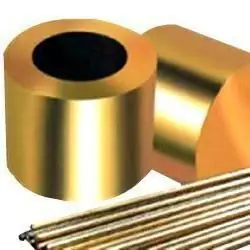
Classification
1. According to the chemical composition, this metal is usually divided into two groups. The first is tin bronzes. In them, tin is the main alloying element. The second is tinless. We will talk about this in more detail below.
2. According to the technological features of bronze, it is customary to divide it into deformable and foundry. The former are well processed under pressure. The latter are used for shaped castings.
This metal, compared to brass, has much better anti-friction, mechanical properties, as well as corrosion resistance. In fact, bronze is an alloy of copper and tin (as the main auxiliary element). Nickel and zinc are not the main alloying elements here; for this, components such as aluminum, tin, manganese, silicon, lead, iron, beryllium, chromium, phosphorus, magnesium, zirconium and others are used.
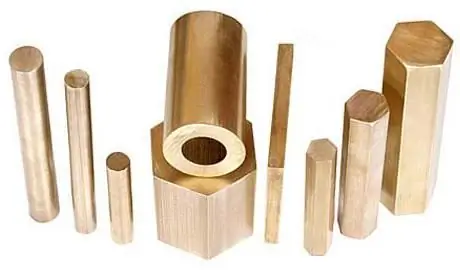
Tin Bronzes: Foundry
Let's figure out what such a metal is. Tin bronze (photo below shows castings) is an alloy that has lower fluidity than other types. However, it has an insignificant volumetric shrinkage, which makes it possible to obtain shaped bronze castings. These properties determine the active use of bronze in the casting of antifriction parts. Also, the considered alloy is used in the manufacture of fittings intended for operation in an aqueous medium (including sea water) or in water vapor, in oils and under high pressure. There are also so-called non-standard casting bronzes for responsible purposes. They are used in the production of bearings, gears, bushings, pump parts, low sealing rings. These parts are designed to operate under high pressure, high speeds and low loads.
Lead bronzes
This subspecies of foundry tin alloys is used in the manufacture of bearings, seals and shaped castings. Such bronzes are characterized by low mechanical properties, as a result of which, in the process of manufacturing bearings and bushings, they are simply applied to a steel base in the form of a very thin layer. Alloys with a high content of tin have higher mechanical properties. Therefore, they can be used without a steel backing.

Tin Bronzes: Deformable
Alloys processed by pressure are usually divided into the following groups:tin-phosphorous, tin-zinc and tin-zinc-lead. They have found their application in the pulp and paper industry (nets are made from them) and mechanical engineering (the production of springs, bearings and machine parts). In addition, these materials are used in the manufacture of bimetallic products, rods, tapes, strips, gears, gears, bushings and gaskets for highly loaded machines, tubes for instrumentation, pressure springs. In electrical engineering, the widespread use of bronze (wrought) is due to its excellent mechanical properties (along with high electrical characteristics). It is used in the manufacture of current-carrying springs, plug connectors, contacts. In the chemical industry, tin bronzes are used to produce spring wire, in precision mechanics - fittings, in the paper industry - scrapers, in the automotive and tractor industries - bushings and bearings.
These alloys can be supplied in extra hard, hard, semi-hard and soft (annealed) states. Tin bronzes are usually cold worked (rolled or drawn). Hot metal is only pressed. Under pressure, bronze is perfectly worked both cold and hot.
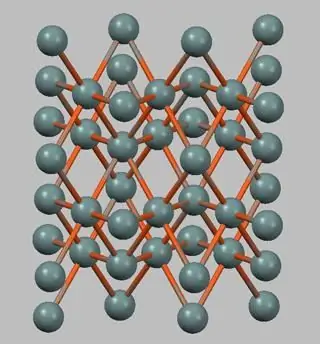
Beryllium bronze
This is an alloy belonging to the group of precipitation hardening metals. It has high mechanical, physical and elastic properties. Beryllium bronze has a high level of heat resistance, corrosion resistance and cyclic strength. It is resistant to lowtemperature, does not magnetize and does not give sparks when struck. Hardening of beryllium bronzes is carried out at temperatures of 750-790 degrees Celsius. The addition of cob alt, iron and nickel contributes to slowing down the rate of phase transformations during heat treatment, which greatly facilitates the technology of aging and hardening. In addition, the addition of nickel contributes to an increase in the recrystallization temperature, and manganese can replace, albeit not completely, expensive beryllium. The above characteristics of bronze make it possible to use this alloy in the manufacture of springs, spring parts, and membranes in the watch industry.
An alloy of copper and manganese
This bronze has special high mechanical properties. It is processed by pressure, both cold and hot. This metal is characterized by high heat resistance, as well as corrosion resistance. An alloy of copper with the addition of manganese has found wide application in furnace fittings.
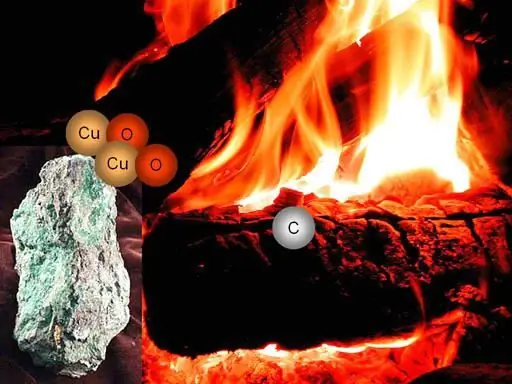
Silicon bronze
This is an alloy containing nickel, less often manganese. Such a metal is characterized by ultra-high mechanical, anti-friction and elastic properties. At the same time, silicon bronze does not lose its plasticity at low temperatures. The alloy is well soldered, processed by pressure at both high and low temperatures. The metal in question is not magnetized, does not spark when struck. This explains the widespread use of bronze (silicon) in marine shipbuilding in the manufacture of anti-friction parts, bearings, springs,grates, evaporators, meshes and guide bushings.
Casting Tinless Alloys
This type of bronze is characterized by good corrosion, anti-friction properties, as well as high strength. They are used for the manufacture of parts that are operated in particularly difficult conditions. These include gears, valves, bushings, gears for powerful turbines and cranes, worms that work in tandem with hardened steel parts, bearings that work under high pressure and shock loads.
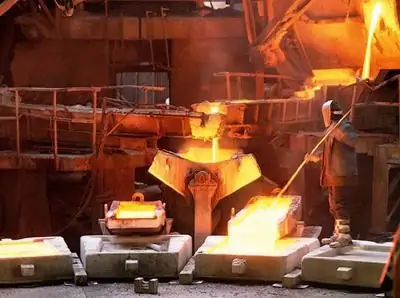
How to make bronze?
The production of this metal must be carried out in special furnaces used for smelting copper alloys. Bronze charge can be made from fresh metals or with the addition of secondary waste. The melting process is usually carried out under a layer of flux or charcoal.
The process using a mixture of fresh metals occurs in a certain sequence. First, the required amount of flux or charcoal is loaded into a highly heated furnace. Then copper is placed there. After waiting for it to melt, increase the heating temperature to 1170 degrees. After that, the melt must be deoxidized, for which phosphorous copper is added. This process can be carried out in two stages: directly in the furnace, and then in the ladle. In this case, the additive is introduced in equal proportions. Next, the necessary alloying elements heated to 120 degrees are added to the melt. Refractory components should be introduced in the form of ligatures. Further molten bronze (photo,below, demonstrates the smelting process) is stirred until all added substances are completely dissolved and heated to the desired temperature. When issuing the resulting alloy from the furnace, before pouring, it must be finally deoxidized with the remainder (50%) of phosphorous copper. This is done to release bronze from oxides and increase the fluidity of the melt.
Smelting from recycled materials
In order to make bronze using recycled metals and waste, melting should be done in the following order. First, copper is melted and deoxidized with phosphorus additives. Then circulating materials are added to the melt. After that, the metals are completely melted and alloying elements are introduced in the appropriate sequence. In the event that the charge consists of a small amount of pure copper, it is necessary to first melt the circulating metals, and then add copper and alloying elements. Melting is carried out under a layer of flux or charcoal.
After melting the mixture and heating it to the required temperature, the final deoxidation of the mixture with phosphorous copper is carried out. Next, the melt is covered on top with calcined coal or dried flux. The consumption of the latter is 2-3 percent by weight of the metal. The heated melt is kept for 20-30 minutes, periodically stirred, and then the separated slag is removed from its surface. Everything, bronze is ready for casting. For better slag removal, quartz sand can be added to the ladle, which thickens it. To determine if the bronze is ready for casting into molds, a speci altechnological test. The fracture of such a sample must be uniform and clean.
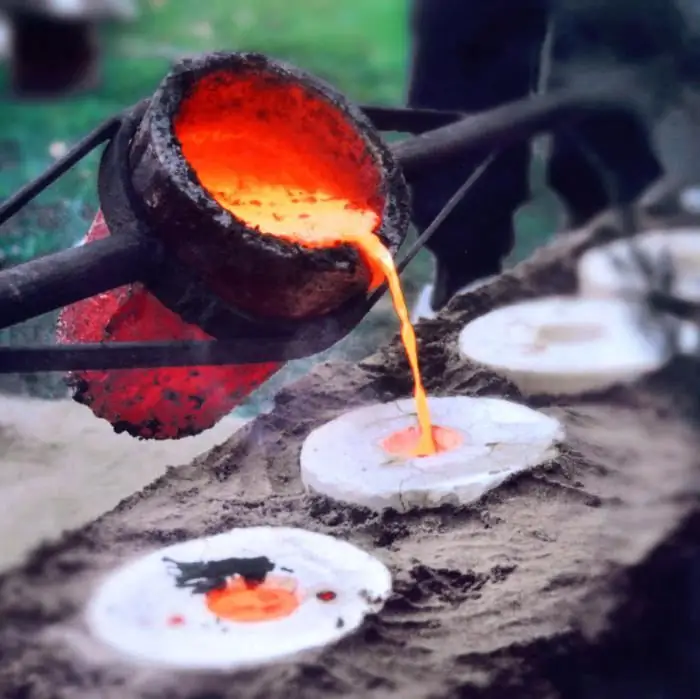
Aluminum Bronze
It is an alloy of copper and aluminum as an alloying element. The melting process of this metal differs significantly from the above, which is explained by the chemical characteristics of the auxiliary component. Consider how to make bronze using aluminum alloying components. In the manufacture of this type of alloy using recycled materials in the charge, the operation for deoxidation with phosphorus components is not used. This is due to the fact that phosphorus is characterized by a lower affinity for oxygen molecules than aluminum. You should also be aware that this type of bronze is very sensitive to overheating, so the temperature should not exceed 1200 degrees. In a superheated state, aluminum is oxidized, and the bronze alloy is saturated with gases. In addition, the oxide formed during the melting of this kind of bronze is not reduced by the addition of deoxidizers, and it is very difficult to remove it from the melt. The oxide film has a very high melting point, which significantly reduces the fluidity of bronze and causes rejection. Melting is carried out very intensively, at the upper limits of heating temperatures. In addition, the finished melt should not be retained in the furnace. When melting aluminum bronze, it is recommended to use a flux that is 50% soda ash and 50% cryolite as a cover layer.
The finished melt is refined before pouring into molds by introducing manganese chloride into it, orzinc chloride (0.2-0.4% of the total mass of the charge). After this procedure, the alloy should be held for five minutes until the complete cessation of gas evolution. After that, the mixture is brought to the required temperature and poured into molds.
In order to prevent segregation in the bronze melt with a high content of lead impurities (50-60%), it is recommended to add 2-2.3% nickel in the form of copper-nickel ligatures. Or, as fluxes, it is necessary to use the sulfate s alt of alkali metals. Nickel, silver, manganese, if they are part of bronze, should be introduced into the melt before the tin addition procedure. In addition, to improve the quality of the resulting alloy, it is sometimes modified with minor additives based on refractory metals.