Currently, the lathe is widely known. The history of its creation begins in the 700s AD. The first models were used for woodworking, 3 centuries later a machine for working with metals was created.
First mentions
In the 700s A. D. a unit was created that partially resembles a modern lathe. The history of its first successful launch begins with the processing of wood by the method of rotation of the workpiece. Not a single part of the installation was made of metal. Therefore, the reliability of such devices is rather low.
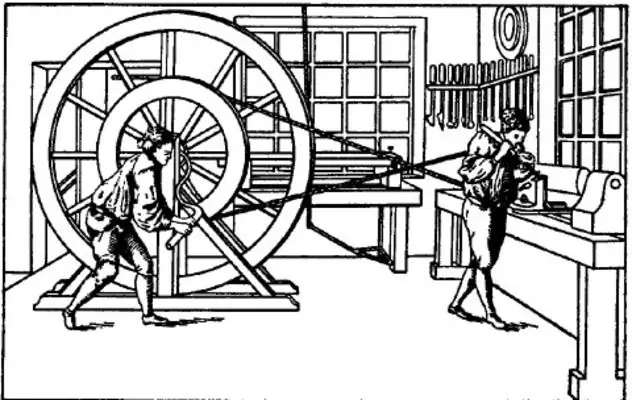
At that time, the lathe had a low efficiency. The history of production has been restored according to the preserved drawings and drawings. To unwind the workpiece, 2 strong apprentices were required. The accuracy of the resulting products is not high.
Information about installations, vaguely reminiscent of a lathe, history dates back to 650 BC. e. However, these machines had only the principle of processing in common - the rotation method. The rest of the nodes were primitive. The workpiece was set in motion in the truest sense of the word. Slave labor was used.
The created models in the 12th century already had a semblance of a drive and they could get a full-fledged product. However, there were no tool holders yet. Therefore, it was too early to talk about the high accuracy of the product.
The device of the first models
An old lathe clamped a workpiece between centers. The rotation was carried out by hands for only a few revolutions. The cut was carried out with a stationary tool. A similar processing principle is present in modern models.
As a drive for the rotation of the workpiece, the craftsmen used: animals, a bow with arrows tied with a rope to the product. Some craftsmen built a kind of water mill for these purposes. But there was no significant performance improvement.
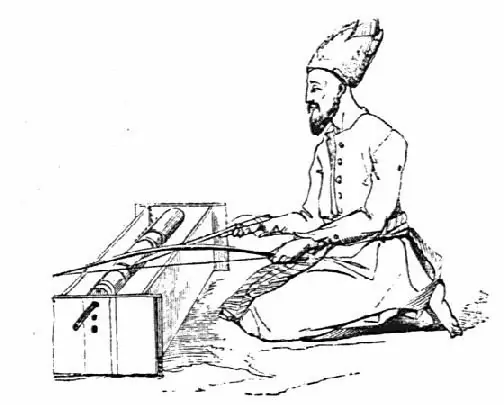
The first lathe had wooden parts, and as the number of nodes increased, the reliability of the device was lost. Water devices quickly lost their relevance due to the complexity of the repair. Only by the 14th century did the simplest drive appear, which greatly simplified the processing process.
Early actuators
Several centuries have passed from the invention of the lathe to the implementation of the simplest drive mechanism on it. You can imagine it in the form of a pole fixed in the middle on the frame on top of the workpiece. One end of the ochepa is tied with a rope that is wrapped around the workpiece. The second is fixed with a foot pedal.
This mechanism worked successfully, but could not provide the necessaryperformance. The principle of operation was built on the laws of elastic deformation. When the pedal was pressed, the rope was tensioned, the pole was bent and experienced significant stress. The latter was transferred to the workpiece, setting it in motion.
Having turned the product 1 or 2 turns, the pole was released and bent again. With a pedal, the master regulated the constant operation of the oche, forcing the workpiece to rotate continuously. At the same time, the hands were busy with the tool, making the processing of wood.
This simplest mechanism was inherited by the following versions of machines that already had a crank mechanism. Mechanical sewing machines of the 20th century subsequently had a similar drive design. On lathes, with the help of a crank, they achieved uniform movement in one direction.
Due to the uniform movement of the master began to receive products of the correct cylindrical shape. The only thing missing was the rigidity of the nodes: centers, tool holders, drive mechanism. The holders of the cutters were made of wood, which led to their wringing out during processing.
But, despite the listed shortcomings, it became possible to produce even spherical parts. Metalworking was still a difficult process. Even soft alloys by rotation did not give in to real turning.
A positive development in the design of machine tools was the introduction of versatility in processing: workpieces of various diameters and lengths were already processed on one machine. This was achieved by adjustable holders and centers. However, large details required significantthe physical cost of the wizard to implement the rotation.
Many craftsmen have adapted a flywheel made of cast iron and other heavy materials. Using the force of inertia and gravity facilitated the work of the handler. However, it was still difficult to achieve industrial scale.
Metal Parts
The main task of the inventors of machine tools was to increase the rigidity of the nodes. The beginning of technical re-equipment was the use of metal centers clamping the workpiece. Later, gears made of steel parts were already introduced.
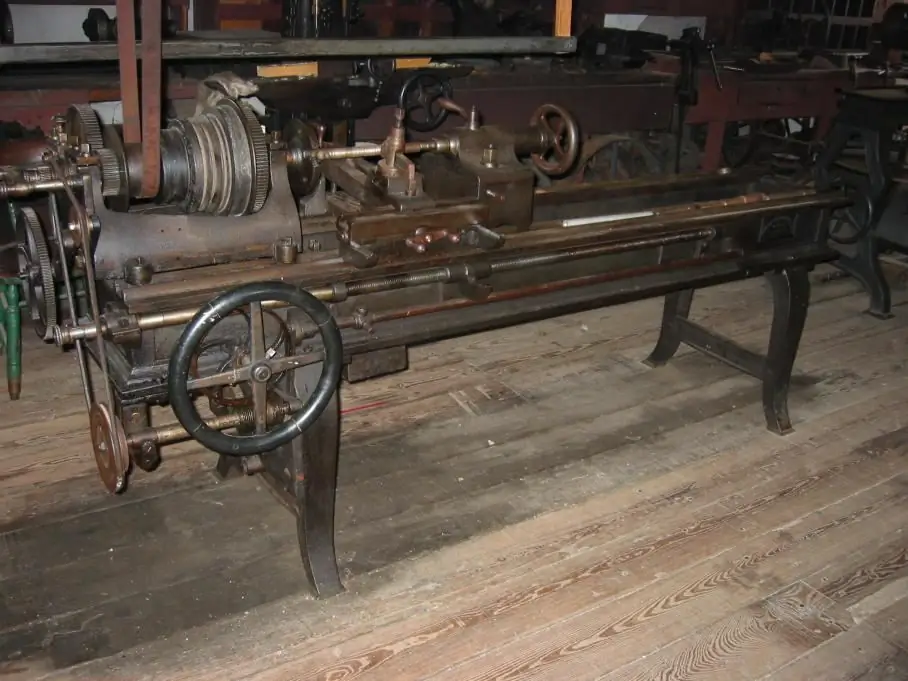
Metal parts made it possible to create screw-cutting machines. Rigidity was already enough for processing soft metals. Individual units were gradually improved:
- blank holder, later called the main unit - spindle;
- conical stops were equipped with adjustable mechanisms to change the position along the length;
- lathe work made easier with the invention of the metal tool holder, but constant chip evacuation was required to increase productivity;
- The cast iron bed increased the rigidity of the structure, which made it possible to process parts of considerable length.
With the introduction of metal knots, it becomes more difficult to unwind the workpiece. The inventors thought about creating a full-fledged drive, wanting to eliminate human manual labor. The transmission system helped to carry out the plan. The steam engine was first adapted to rotate workpieces. It was preceded by a water engine.
Uniformity of movement of the cuttingthe tool was carried out by a worm gear using a handle. This resulted in a cleaner surface of the part. Interchangeable blocks made it possible to realize universal work on a lathe. Mechanized structures have improved over the centuries. But to this day, the principle of operation of nodes is based on the first inventions.
Scientific inventors
Currently, when buying a lathe, technical specifications are analyzed first. They provide the main possibilities in processing, dimensions, rigidity, production speed. Earlier, with the modernization of nodes, parameters were gradually introduced, according to which the models were compared with each other.
Classification of machines helped to assess the degree of perfection of a particular machine. After analyzing the collected data, Andrey Nartov, a domestic inventor from the time of Peter the Great, upgraded previous models. His brainchild was a real mechanized machine that allows you to perform various types of processing of bodies of rotation, cut threads.
A plus in Nartov's design was the ability to change the speed of rotation of the movable center. They also provided interchangeable gear blocks. The appearance of the machine and the device resemble a modern simple lathe TV3, 4, 6. Modern machining centers have similar units.
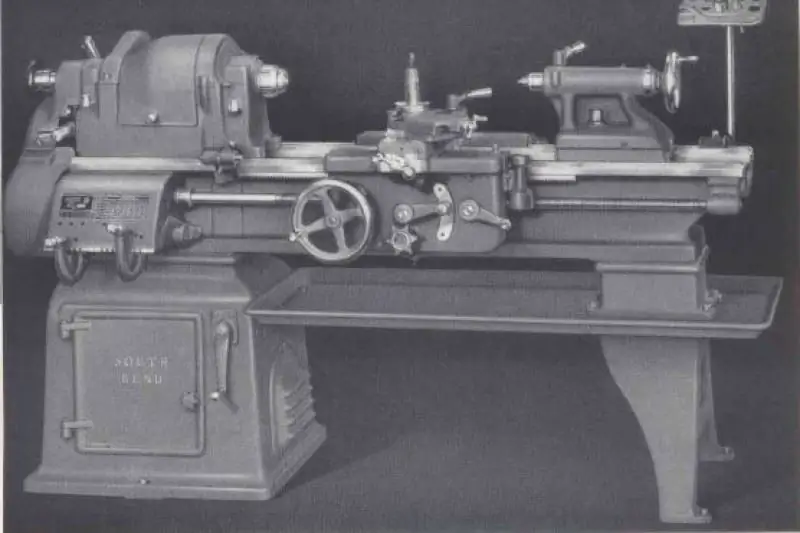
In the 18th century Andrey Nartov introduced the self-propelled caliper to the world. The lead screw transmitted the uniform movement of the tool. Henry Maudsley, English inventor, presented hisversion of an important node by the end of the century. In its design, the change in the speed of movement of the axes was carried out due to the different thread pitch of the lead screw.
Main Knots
Lathes are ideal for turning 3D parts. An overview of a modern machine contains the parameters and characteristics of the main components:
- Bed - the main loaded element, the frame of the machine. Made from durable and hard alloys, pearlite is mainly used.
- Support - an island for attaching rotating tool heads or a static tool.
- Spindle - acts as a workpiece holder. The main powerful rotation knot.
- Additional units: ball screws, sliding axes, lubrication mechanisms, coolant supply, air bleeders from the working area, coolers.
A modern lathe contains drive systems consisting of sophisticated control electronics and a motor, often a synchronous one. Additional options allow you to remove chips from the working area, measure the tool, supply coolant under pressure directly to the cut area. The mechanics of the machine is selected individually for the tasks of production, and the cost of the equipment also depends on this.
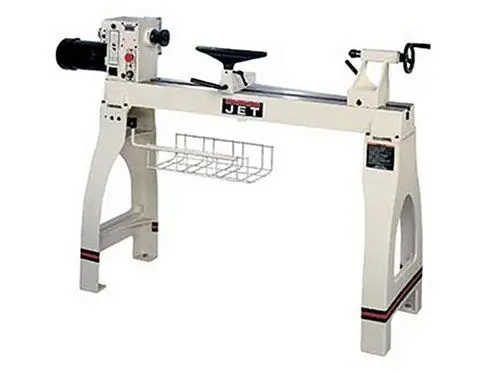
The caliper contains nodes for placing bearings that are mounted on the ball screw (ball screw pair). Also, elements for contact with the sliding guides are mounted on it. Lubrication in modern machines is supplied automatically, its level in the tank is controlled.
In the first lathes, movementthe tool was carried out by a person, he chose the direction of its movement. In modern models, all manipulations are carried out by the controller. It took several centuries for the invention of such a knot. Electronics has greatly expanded processing capabilities.
Management
Recently, CNC metal lathes have become widespread - with numerical control. The controller controls the cutting process, monitors the position of the axes, calculates the movement according to the set parameters. The memory stores several stages of cutting, up to the exit of the finished part.
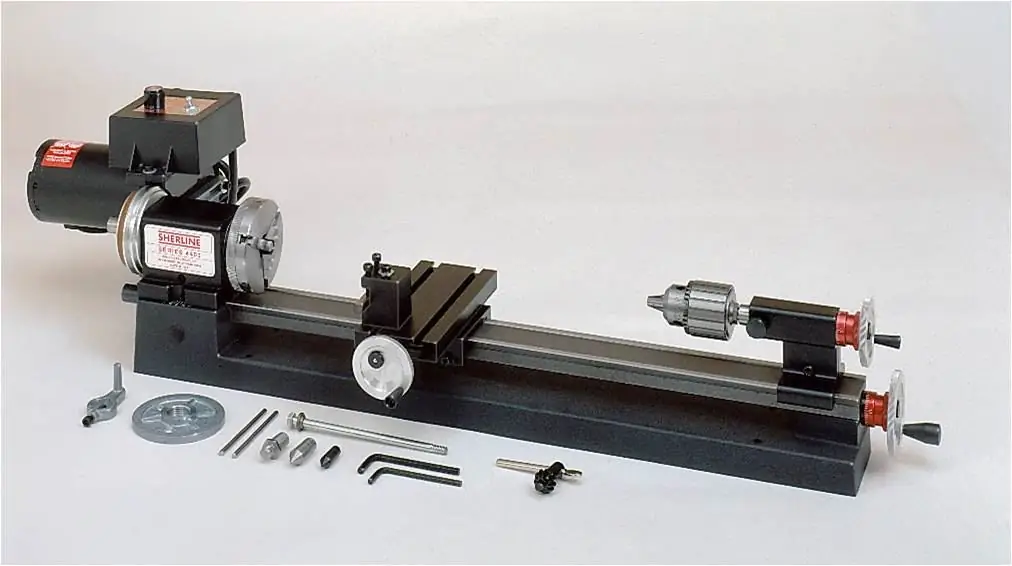
CNC metal lathes can have process visualization, which helps to check the written program before the tool moves. The entire cut can be seen virtually and code errors can be corrected in time. Modern electronics controls axle load. The latest versions of the software allow you to identify a broken tool.
Methodology for monitoring broken inserts on the toolholder is based on comparing the load curve of the axis during normal operation and when the alarm threshold is exceeded. Tracking happens in the program. Information for analysis is provided to the controller by a drive system or a power sensor with the ability to digitize values.
Position sensors
The first machines with electronics had limit switches with microswitches to control the extreme positions. Later, encoders were installed on the propeller. Currently, high-precision rulers are used that can measure a few microns of play.
Equipped with circular sensors and rotation axes. The spindle assembly could be controlled. This is required to implement the milling functions that were performed by the driven tool. The latter was often built into the turret.
Tool integrity is measured using electronic probes. They also make it easier to find anchor points to start the cutting cycle. The probes can measure the geometry of the obtained contours of the part after processing and automatically make corrections that are included in the re-finishing.
The simplest modern model
The TV 4 lathe is a training model with the simplest drive mechanism. All control is manual.
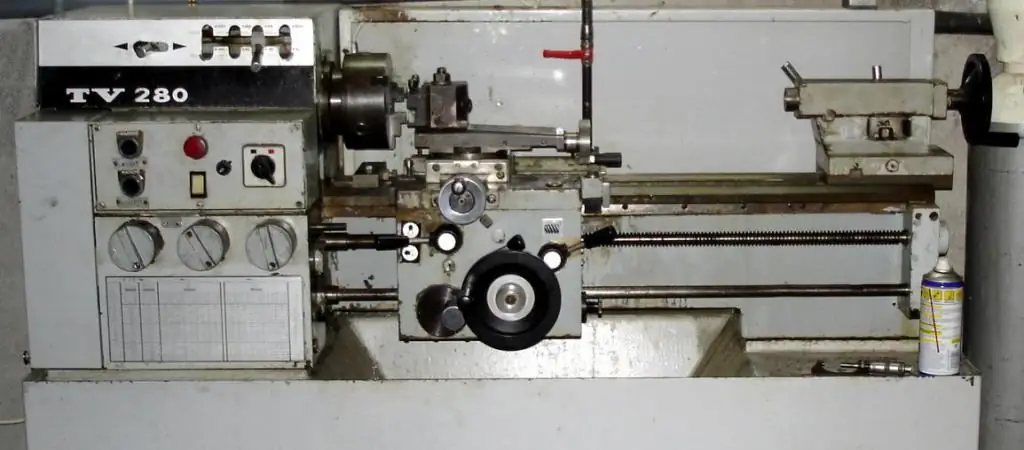
Handles:
- adjust the position of the tool relative to the axis of rotation;
- set the direction of threading right or left;
- are used to change the speed of the main drive;
- determine the thread pitch;
- include longitudinal movement of the tool;
- are responsible for fastening the nodes: the tailstock and its quills, heads with incisors.
Flywheels move nodes:
- tailstock quill;
- longitudinal carriage.
The design provides a lighting circuit for the working area. A safety screen in the form of a protective screen protects workers from chips. The design of the machine is compact, which allows it to be used in classrooms, service rooms.
The TV4 screw-cutting lathe is a simplestructures, where all the necessary components of a full-fledged metal processing structure are provided. The spindle is driven through a gearbox. The tool is mounted on a support with a mechanical feed, driven by a screw pair.
Sizes
The spindle is driven by an asynchronous motor. The maximum workpiece size can be in diameter:
- no more than 125 mm if machining over the caliper;
- no more than 200 mm if machining is carried out over the bed.
The length of the workpiece clamped in the centers is not more than 350 mm. The assembled machine weighs 280 kg, the maximum spindle speed is 710 rpm. This rotational speed is decisive for finishing. Power is supplied from a 220V network with a frequency of 50 Hz.
Features of the model
The gearbox of the TV4 machine is connected to the spindle motor by a V-belt transmission. On the spindle, the rotation is transmitted from the box through a series of gears. The direction of rotation of the workpiece is easily changed by phasing the main motor.
The guitar is used to transfer rotation from the spindle to the calipers. It is possible to switch 3 feed rates. Accordingly, three different types of metric threads are cut. The lead screw ensures smooth and uniform travel.
The handles set the direction of rotation of the propeller pair of the headstock. The handles also set the feed rates. The caliper only moves in the longitudinal direction. Assemblies should be lubricated according to machine regulations manually. Gears, on the other hand, take grease from the bath in which they work.
On the machinethe ability to work manually. Flywheels are used for this. The rack and pinion meshes with the rack and pinion. The latter is bolted to the frame. This design allows, if necessary, to include manual control of the machine. A similar handwheel is used to move the tailstock quill.