Electromagnetic screens are widely used in industry. They serve to eliminate the harmful effects of some elements of an electrical device on others, to protect personnel and equipment from the effects of external fields that occur during the operation of other devices. The "quenching" of the external magnetic field is necessary in the creation of laboratories intended for adjustment and testing of highly sensitive equipment. It is also required in medicine and those areas of science where the measurement of fields with ultra-low induction is carried out; to protect information during its transmission over cables.
Methods
Magnetic field shielding is a set of ways to reduce the strength of a constant or alternating field in a certain area of space. A magnetic field, unlike an electric field, cannot be completely weakened.
In industry, stray fields from transformers, permanent magnets, high current installations and circuits have the greatest environmental impact. They can completely disrupt the normal operation of neighboring appliances.
Most used 2protection method:
- The use of screens made of superconducting or ferromagnetic materials. This is effective in the presence of a constant or low frequency magnetic field.
- Compensation method (eddy current damping). Eddy currents are bulk electric currents that occur in a conductor when the magnetic flux changes. This method shows the best results for high frequency fields.
Principles
The principles of shielding the magnetic field are based on the patterns of propagation of the magnetic field in space. Accordingly, for each of the methods listed above, they are as follows:
- If you place an inductor in a casing made of a ferromagnet, then the lines of induction of the external magnetic field will pass along the walls of the protective screen, since it has less magnetic resistance compared to the space inside it. Those lines of force that are induced by the coil itself will also almost all be closed to the walls of the casing. For the best protection in this case, it is necessary to choose ferromagnetic materials that have a high magnetic permeability. In practice, iron alloys are most often used. In order to increase the reliability of the screen, it is made thick-walled or prefabricated from several casings. The disadvantages of this design are its heavy weight, bulkiness and deterioration of shielding in the presence of seams and cuts in the walls of the casing.
- In the second method, the weakening of the external magnetic fieldoccurs as a result of the imposition of another field on it, induced by ring eddy currents. Its direction is opposite to the lines of induction of the first field. As the frequency increases, the attenuation will be more pronounced. In this case, plates in the form of a ring of conductors with low resistivity are used for shielding. Cylinder-shaped boxes made of copper or aluminum are most often used as screen-casings.
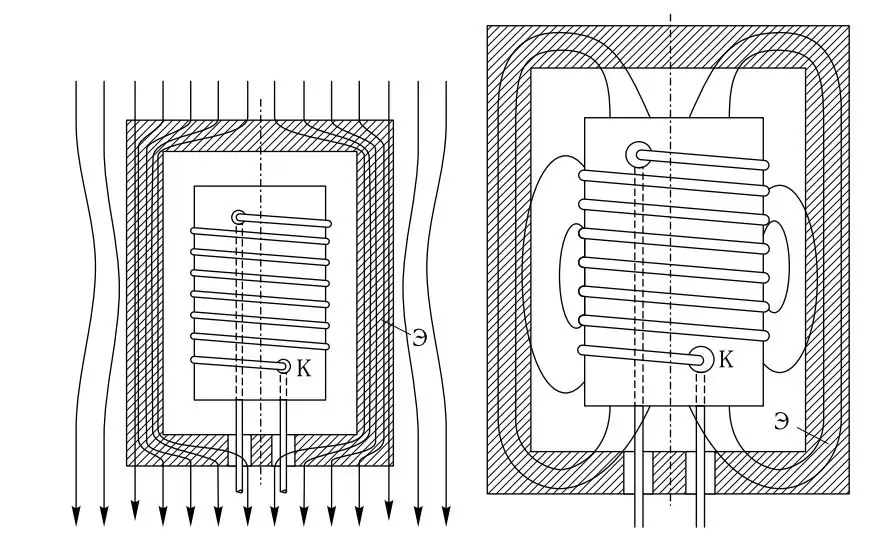
Key Features
There are 3 main characteristics to describe the shielding process:
- Equivalent magnetic field penetration depth. So let's continue. This figure is used for the screening effect of eddy currents. The smaller its value, the higher the current flowing in the surface layers of the protective casing. Accordingly, the greater the magnetic field induced by it, which displaces the external one. The equivalent depth is determined by the formula below. In this formula, ρ and Μr are the resistivity and relative magnetic permeability of the screen material, respectively (the units of measurement of the first value are Ohm∙m); f is the frequency of the field, measured in MHz.
- Shielding efficiency e - the ratio of the magnetic field strength in the shielded space in the absence and presence of the shield. This value is the higher, the greater the thickness of the screen and the magnetic permeability of its material. Magnetic permeability is an indicator characterizing how many times the induction in a substancedifferent from that in a vacuum.
- Reduction of magnetic field strength and eddy current density at a depth x from the surface of the protective casing. The indicator is calculated using the formula below. Here A0 is the value on the screen surface, x0 is the depth at which the intensity or current density decreases e times.
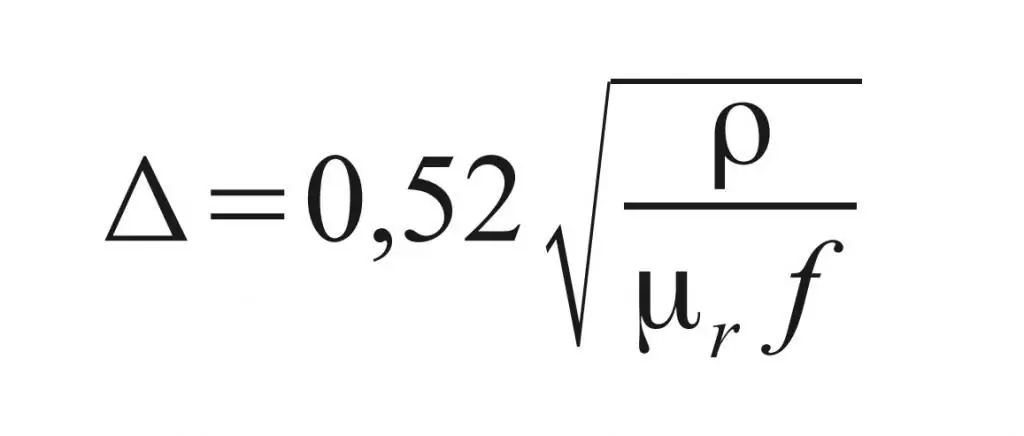
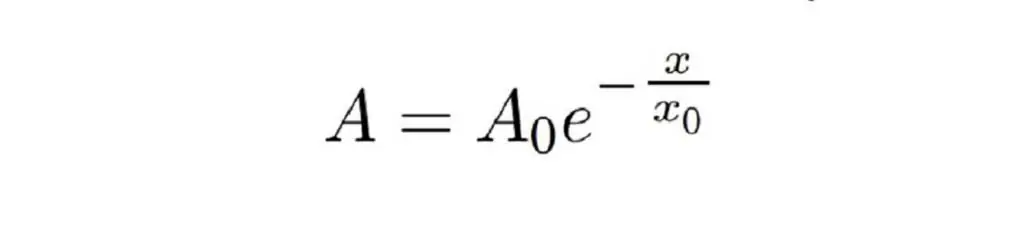
Screen designs
Protective covers for shielding the magnetic field can be made in various designs:
- sheet and massive;
- in the form of hollow tubes and casings with a cylindrical or rectangular section;
- single-layer and multi-layer, with an air gap.
Since the calculation of the number of layers is rather complicated, this value is most often chosen from reference books, according to shielding efficiency curves that were obtained experimentally. Cuts and seams in boxes are allowed to be made only along the lines of eddy currents. Otherwise, the shielding effect will be reduced.
In practice, it is difficult to obtain a high shielding factor, as it is always necessary to make holes for cable entry, ventilation and maintenance of installations. For coils, seamless casings are made using the sheet extrusion method, and the bottom of the cylindrical screen serves as a removable cover.
In addition, when the structural elements come into contact, cracks form due to surface irregularities. To eliminate them, usemechanical clamps or gaskets made of conductive materials. They are available in different sizes and with different properties.
Eddy currents are currents that are much less circulating, but they are able to prevent the penetration of the magnetic field through the screen. In the presence of a large number of holes in the casing, the decrease in the shielding coefficient occurs according to a logarithmic dependence. Its smallest value is observed with technological holes of large size. Therefore, it is recommended to design several small holes rather than one large one. If it is necessary to use standardized holes (for cable entry and other needs), then transcendental waveguides are used.
In a magnetostatic field created by direct electric currents, the screen's job is to shunt the field lines. The protective element is installed as close as possible to the source. Grounding is not required. The shielding effectiveness depends on the magnetic permeability and the thickness of the shield material. As the latter, steels, permalloy and magnetic alloys with high magnetic permeability are used.
Shielding of cable routes is mainly performed by two methods - using cables with shielded or protected twisted pair and laying conduits in aluminum boxes (or inserts).
Superconductive screens
The operation of superconducting magnetic screens is based on the Meissner effect. This phenomenon consists in the fact that a body in a magnetic field goes into a superconducting state. At the same time, the magneticthe permeability of the casing becomes equal to zero, that is, it does not pass the magnetic field. It is fully compensated in the volume of the given body.
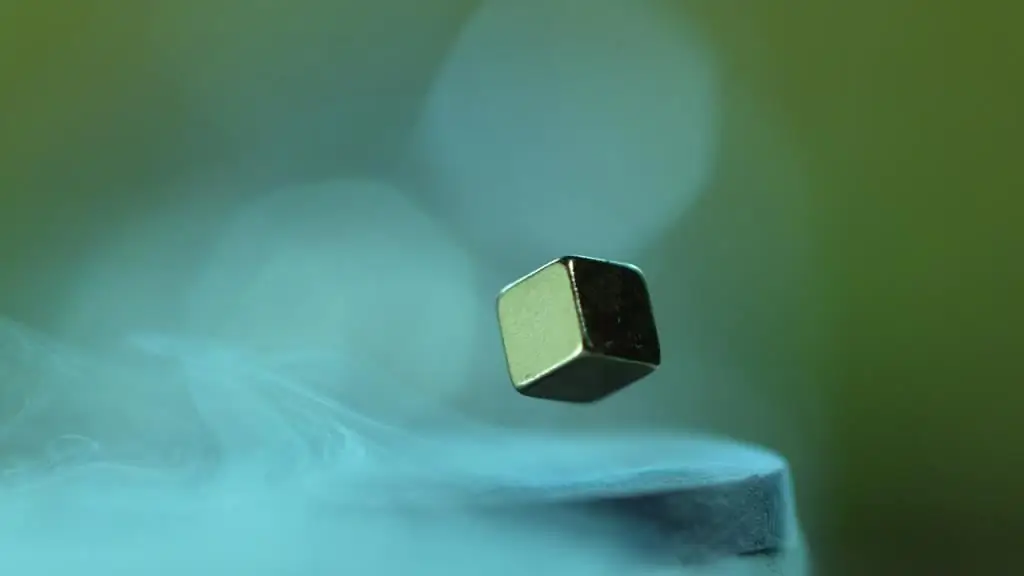
The advantage of such elements is that they are much more efficient, protection from an external magnetic field does not depend on frequency, and the compensation effect can last for an arbitrarily long time. However, in practice, the Meissner effect is not complete, since in real screens made of superconducting materials there are always structural inhomogeneities that lead to magnetic flux trapping. This effect is a serious problem for the creation of casings in order to shield the magnetic field. The magnetic field attenuation coefficient is the greater, the higher the chemical purity of the material. In experiments, the best performance was noted for lead.
Other disadvantages of superconducting magnetic field shielding materials are:
- high cost;
- presence of residual magnetic field;
- appearance of the state of superconductivity only at low temperatures;
- inability to function in high magnetic fields.
Materials
Most often, carbon steel screens are used to protect against a magnetic field, as they are highly adaptable for welding, soldering, inexpensive and characterized by good corrosion resistance. In addition to them, materials such as:
- technical aluminum foil;
- soft magnetic alloy of iron, aluminum and silicon (alsifer);
- copper;
- conductive coated glass;
- zinc;
- transformer steel;
- conductive enamels and varnishes;
- brass;
- metallized fabrics.
Structurally, they can be made in the form of sheets, nets and foil. Sheet materials provide better protection, and mesh materials are more convenient to assemble - they can be joined together by spot welding in 10-15 mm increments. To ensure corrosion resistance, the grids are varnished.
Recommendations for material selection
When choosing a material for protective screens, the following recommendations are guided:
- In weak fields, alloys with high magnetic permeability are used. The most technologically advanced is permalloy, which lends itself well to pressure and cutting. The magnetic field strength required for its complete demagnetization, as well as the electrical resistivity, depend mainly on the percentage of nickel. By the amount of this element, low-nickel (up to 50%) and high-nickel (up to 80%) permalloys are distinguished.
- To reduce energy losses in an alternating magnetic field, casings are placed either from a good conductor or from an insulator.
- For a field frequency of more than 10 MHz, silver or copper film coatings with a thickness of 0.1 mm or more (screens made of foil-coated getinaks and other insulating materials), as well as copper, aluminum, brass, give a good effect. To protect copper from oxidation, it is coated with silver.
- Thicknessmaterial depends on the frequency f. The lower f, the greater the thickness must be to achieve the same shielding effect. At high frequencies, for the manufacture of casings from any material, a thickness of 0.5-1.5 mm is sufficient.
- For fields with high f, ferromagnets are not used, since they have high resistance and lead to large energy losses. Highly conductive materials other than steel should also not be used to shield permanent magnetic fields.
- For protection over a wide f range, multi-layer materials (steel sheets with a highly conductive metal layer) are the optimal solution.
The general selection rules are as follows:
- High frequencies are highly conductive materials.
- Low frequencies are materials with high magnetic permeability. Shielding in this case is one of the most difficult tasks, as it makes the design of the protective screen heavier and more complicated.
Foil tapes
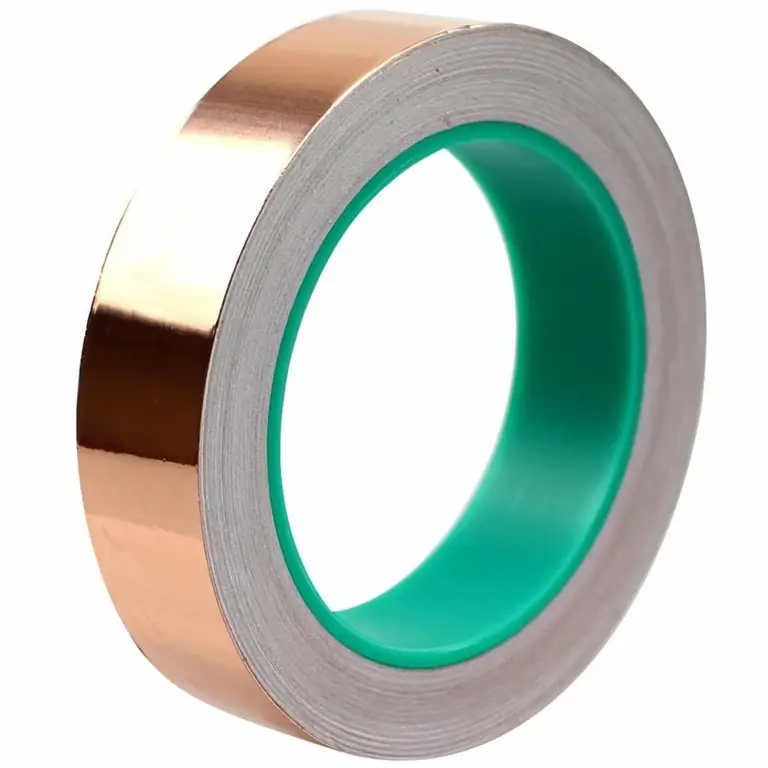
Foil shielding tapes are used for the following purposes:
- Shielding broadband electromagnetic interference. Most often they are used for doors and walls of electrical cabinets with devices, as well as for forming a screen around individual elements (solenoids, relays) and cables.
- Removal of static charge that accumulates on devices containing semiconductors and cathode ray tubes, as well as in devices used to input / output information fromcomputer.
- As a component of ground circuits.
- To reduce electrostatic interaction between transformer windings.
Structurally, they are based on a conductive adhesive material (acrylic resin) and foil (with a corrugated or smooth surface) made of the following types of metal:
- aluminum;
- copper;
- tinned copper (for soldering and better anti-corrosion protection).
Polymer materials
In those devices where, along with the shielding of the magnetic field, protection against mechanical damage and shock absorption are required, polymeric materials are used. They are made in the form of polyurethane foam pads covered with a polyester film, based on an acrylic adhesive.
In the production of liquid crystal monitors, acrylic seals made of conductive fabric are used. In the layer of acrylic adhesive is a three-dimensional conductive matrix made of conductive particles. Due to its elasticity, this material also effectively absorbs mechanical stress.
Compensation method
The principle of the compensation shielding method is to artificially create a magnetic field that is directed opposite to the external field. This is usually achieved with a Helmholtz coil system. It consists of 2 identical thin coils located coaxially at a distance of their radius. Electricity is passed through them. The magnetic field induced by the coils is highly uniform.
Shielding canalso produced by plasma. This phenomenon is taken into account in the distribution of the magnetic field in space.
Cable shielding
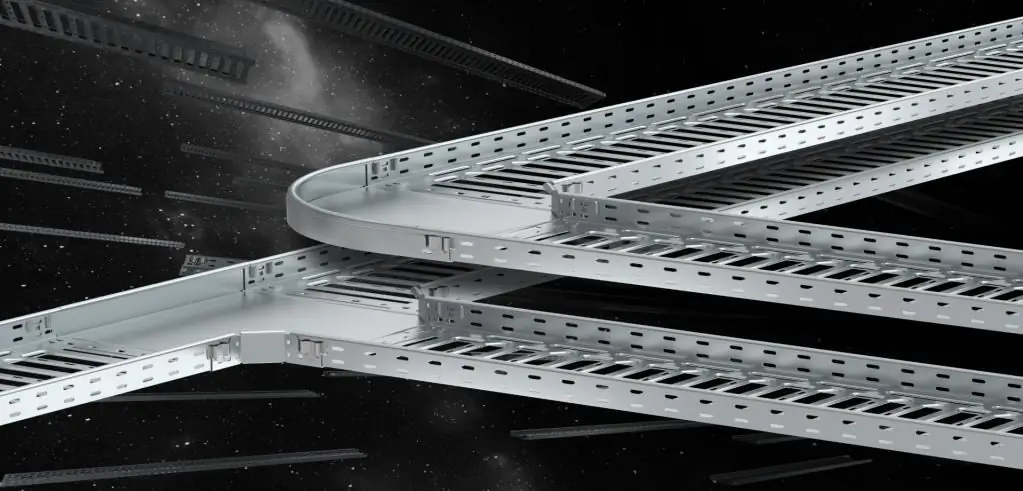
Magnetic field protection is essential when laying cables. Electric currents induced in them can be caused by the inclusion of household appliances in the room (air conditioners, fluorescent lamps, telephones), as well as elevators in mines. These factors have a particularly great influence on digital communication systems operating on protocols with a wide frequency band. This is due to the small difference between the power of the useful signal and the noise in the upper part of the spectrum. In addition, the electromagnetic energy emitted by cable systems adversely affects the he alth of personnel working in the premises.
Cross-talk occurs between pairs of wires due to the presence of capacitive and inductive coupling between them. The electromagnetic energy of the cables is also reflected due to the inhomogeneities of their wave impedance and is weakened in the form of heat losses. As a result of attenuation, the signal power at the end of long lines drops hundreds of times.
Currently, 3 methods of shielding cable routes are practiced in the electrical industry:
- The use of all-metal boxes (steel or aluminum) or the installation of metal inserts in plastic ones. As the field frequency increases, the screening ability of aluminum decreases. The disadvantage is also the high cost of boxes. For long cable runs there isthe problem of ensuring the electrical contact of individual elements and their grounding to ensure the zero potential of the box.
- Use shielded cables. This method provides maximum protection as the sheath surrounds the cable itself.
- Vacuum deposition of metal on the PVC channel. This method is ineffective at frequencies up to 200 MHz. The “quenching” of the magnetic field is ten times less compared to laying the cable in metal boxes due to the high resistivity.
Types of cables
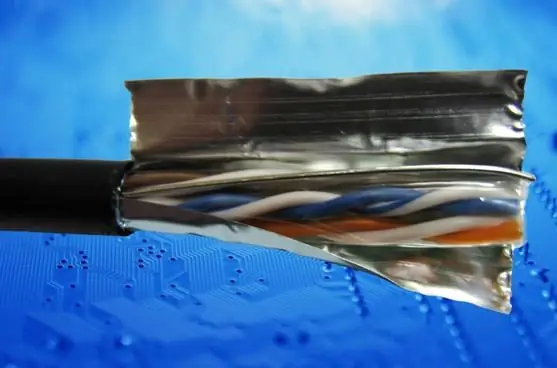
There are 2 types of shielded cables:
- With a common screen. It is located around unprotected stranded conductors. The disadvantage of such cables is that there is large crosstalk (5-10 times more than shielded pairs), especially between pairs with the same twist pitch.
- Cables with shielded twisted pairs. All pairs are individually shielded. Due to their higher cost, they are most often used in networks with stringent safety requirements and in rooms with a difficult electromagnetic environment. The use of such cables in parallel laying makes it possible to reduce the distance between them. This reduces costs compared to split routing.
Twisted-pair shielded cable is an insulated pair of conductors (their number is usually from 2 to 8). This design reduces crosstalk.between conductors. Unshielded pairs have no grounding requirements, they have more flexibility, smaller transverse dimensions, and ease of installation. The shielded pair provides protection against electromagnetic interference and high quality data transmission over networks.
Information systems also use two-layer shielding, which consists of protection of twisted pairs in the form of a metallized plastic tape or foil, and a common metal braid. For effective protection against the magnetic field, such cable systems must be properly grounded.