When the question "Calculate the manufacturing cost of a product" comes up, it becomes very important to research the methods used for these calculations. The cost price is the estimated cost of natural resources used in production (works, services), raw materials, materials, fuel and energy resources, fixed assets, labor, marketing and advertising costs.
In accordance with the concept of cost, it includes all the total costs associated with the manufacture or purchase of a unit of output (work).
Cost structure
Products (services) obtained during production or acquisition have their own cost, consisting of the following cost elements:
- Material costs represent the cost of all materials spent on the production process of manufacturing products.
- Value of goods purchased for resale.
- Costenergy resources and other natural resources used for space heating, lighting and water use.
- The cost of raw materials that are needed in the production process.
- The cost of labor. This category includes resources that were spent on the formation of the wages of the employees involved, as well as on contributions to the budget and off-budget funds, taxes and insurance payments for these employees.
- Cost of fixed assets. These include expensive equipment, the use of which is necessary in the production or production. Depreciation of this equipment needs to be accounted for.
- Administrative expenses include the maintenance of managers and managers.
- Other expenses incurred during the production cycle.
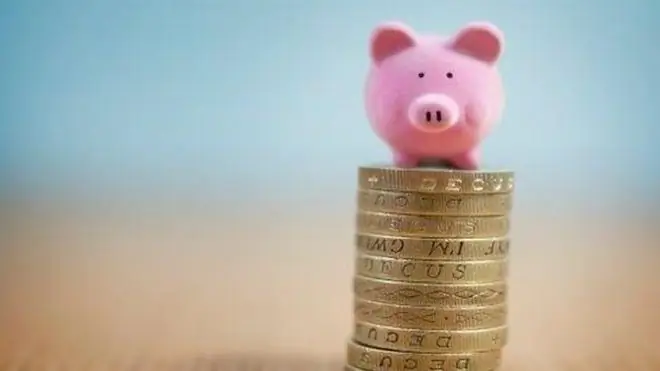
Cost types
Cost can be of two types:
- Full or average, which includes absolutely all expenses of the enterprise. It takes into account all expenses related to the purchase of equipment, tools, materials, transportation of goods, etc. The indicator is taken as an average value.
- Marginal cost depends on the quantity of production and reflects the cost of all additional units of production. Thanks to the obtained value, it is possible to calculate the efficiency of further expansion of production.
Cost types
By the nature of the costs incurred, there are several types of cost of goods, products or services:
- Shop cost consists of the amounts of expenses that are related to the production process of the company. They include the cost of raw materials, the wages of workers.
- Production cost consists of other expenses for the maintenance of the enterprise. This is the cost of natural resources, the maintenance of management personnel.
- Full cost - these are all costs that are associated not only with the process of purchasing or manufacturing products, but also with its sale of products. In addition to the above, this includes advertising, hospitality and other expenses.
The most demanded in the accounting of economic activity is the total cost (full). Its analysis allows us to identify ways to reduce costs, thereby increasing the overall profit of the company.
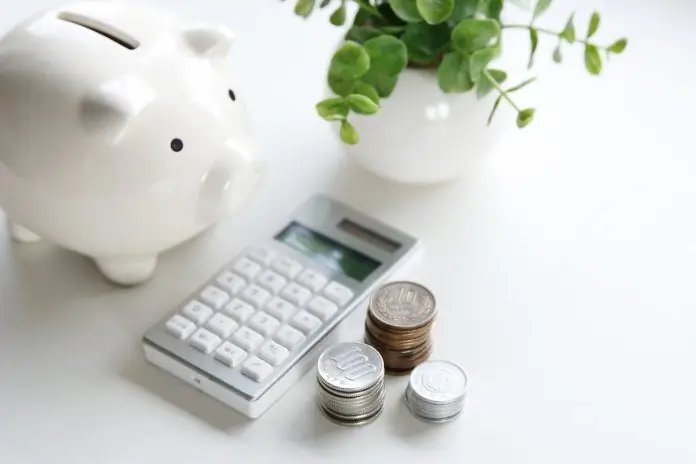
Cost calculation
To calculate the cost of production at the enterprise, it is necessary to sum up the costs that are required for the production and release of products. This indicator does not take into account the cost of sales.
The formation of the cost of the enterprise occurs before the sale of products, since the price of the product depends on the value of this indicator.
The most popular option to calculate the cost of manufactured products is the costing technique. Thanks to this method, you can calculate how much money is spent on the production of 1 unit of output.
Analysis of the amount of costs and costing isa necessary condition for calculating the efficiency of the firm's output. The lower the level of the resource base spent on the production of one unit of goods (services), the more profitable the production process becomes for the company. The cost, therefore, directly affects the final profit. An increase in the cost of production costs worsens the financial condition of the enterprise. Sometimes the proceeds from the sale of goods may not even cover all the expenses incurred.
One of the easiest ways to increase a company's profits is to cut costs. It is unacceptable that the cost reduction will negatively affect the product itself. After all, it will be very difficult to sell goods with insufficient quality in the future. As a result, the owner will suffer losses even at a low price.
The main source of information about the resources spent can be primary accounting data in the accounting department. In the process of producing goods or providing services, the main part consists of the costs of the main, auxiliary production processes, as well as other general business expenses.
If we are talking about trading processes, then the cost of a product consists of the cost of buying this product and the cost of selling it.
When providing services, the cost is formed at the expense of the necessary costs for the process of providing the service: rent payments, utilities, material costs, labor costs.
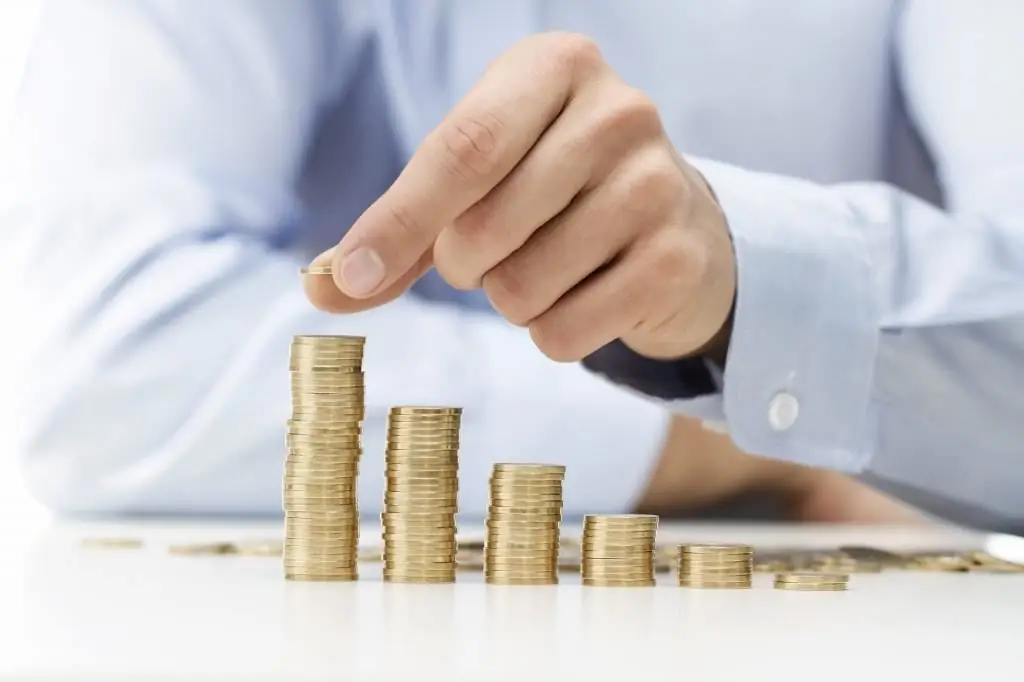
Calculation methods
Calculate the costThere are two ways to sell products. These are the costing method and the tiered allocation method. The first method is most often used, since it allows you to more accurately and quickly determine the cost of production. Let's consider it in more detail.
Cost calculation is the calculation of costs and expenses that are taken into account per unit of output. In this case, the costs are grouped by elements.
Depending on the type of production activity and its costs, the calculation can be performed in several ways:
- The method of "direct costing" arose and developed in a market economy. It has a limited cost. That is, the sum of direct costs is used in the calculation. Indirect costs are charged to the sales account.
- Custom method. It can be used to calculate the cost of each unit of production in enterprises that produce unique equipment and products. For complex and time-consuming orders, it is reasonable to calculate the cost of each product.
- Procedural method. This method is used by enterprises that carry out mass production, and the production process itself includes several stages. The cost price is calculated for each stage of production.
- Process method. It is used by mining companies or companies with a simple process (such as asph alt production).
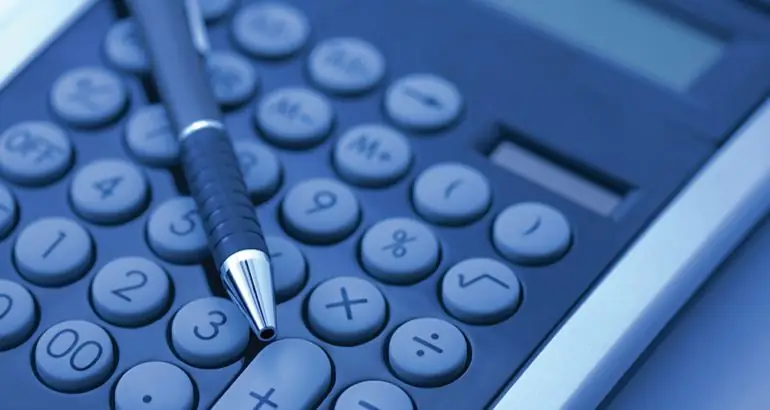
Calculation formula
The answer to the question of how to calculate the costproducts according to the formula, is as follows:
Total cost=Production cost + Selling and distribution costs
This is a simplified version.
A detailed and extended answer to the question of how to calculate the cost of production using the formula looks like this:
S=P + OM + VM + T + E + C + Am + B + NC + Above + Z + SS + CR,
where P is the cost of purchasing semi-finished products;
OM - basic materials;
BM - auxiliary materials;
T - transportation costs;
E - energy costs;
С - sales and sales expenses;
Am - depreciation expenses;
B - remuneration of key employees;
NZ - non-manufacturing costs;
Over - employee bonus payments;
З - factory costs;
SS - insurance payments;
PR - shop floor costs.

Production cost
The work of the company is always focused on the release and production of products. At the same time, the company incurs costs by investing in production, raw materials, labor and energy.
Thus, the cost of production is the total of all costs for the release of the product and does not include the costs associated with its sale.
Actual cost
To calculate the actual cost of production, real data is taken based on actual costs, then it is formedthe price of the product. It is very inconvenient to make such a calculation, since it is often necessary to know the cost of a product before it is sold. The profitability of the business depends on this.
Standard costs
The calculation of the standard cost is based on data obtained in accordance with existing standards. In this regard, it is easy to control the volume of consumption of materials, which minimizes the occurrence of unnecessary costs.

Unit cost
Calculation of unit costs for the production of one unit of output is carried out in three stages:
- it is necessary to determine the total cost for all manufactured products, then the total cost is divided by the number of products produced;
- administrative and commercial expenses in total divided by the number of products sold in the reporting month;
- need to add up all the figures calculated above.
However, in organizations that make one type of product and have a certain amount of inventory in stock that has not yet been sold to the buyer, a simple two-stage calculation method is used.
Question "How to calculate unit cost?" can be supplemented by using a simple two-step calculation method using the following formula:
C=(PZ / Kp) + (UK / Cr),
where C is the total cost of production, rubles;
PZ - total production costs for the reporting period, rub.;
MC - managerial and commercialexpenses, rub.;
Кп - the number of units of production produced during the reporting period, pieces;
Kr - the number of units of products sold during the reporting period, pcs.
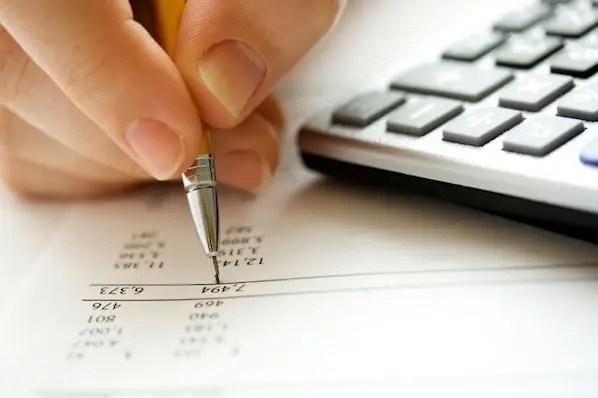
How to calculate the cost of production (and calculation example)
To understand how to perform the calculations, consider the costing example below.
Before proceeding with the calculations, you must do the following:
- summarize the total cost of all costs associated with the acquisition of raw materials and supplies needed for production;
- calculate how much money was spent on energy;
- identify all payroll costs;
- determine deductions for depreciation charges;
- calculate the costs associated with the sale of products;
- analyze and account for other production costs.
Our task is to calculate the cost of 1000 units. products at the reference plant. We have the following initial data, which are presented in the table below.
Costs | Amount, t.r. |
Raw materials | 5000 |
Fuel and energy | 400 |
Salary of key workers | 1800 |
Deductions from payroll | 40% |
General expenses | 20%from the salary of the main staff |
General production costs | 10% of key staff remuneration |
Shipping charges | 5% of overhead costs per 1000 units of production |
Calculate the cost of manufactured products in the table below.
Costs | Calculation | Amount, t.r. |
Deductions to funds | 1800 x 40% | 720 |
General production costs | 1800 x 15% | 270 |
General expenses | 1800 x 25% | 450 |
Production cost of 1000 units | 5000+400+1800+720+270+450 | 8640 |
Sales costs | 8640 x 5 % | 432 |
Full cost | 8640 + 432 | 9072 |
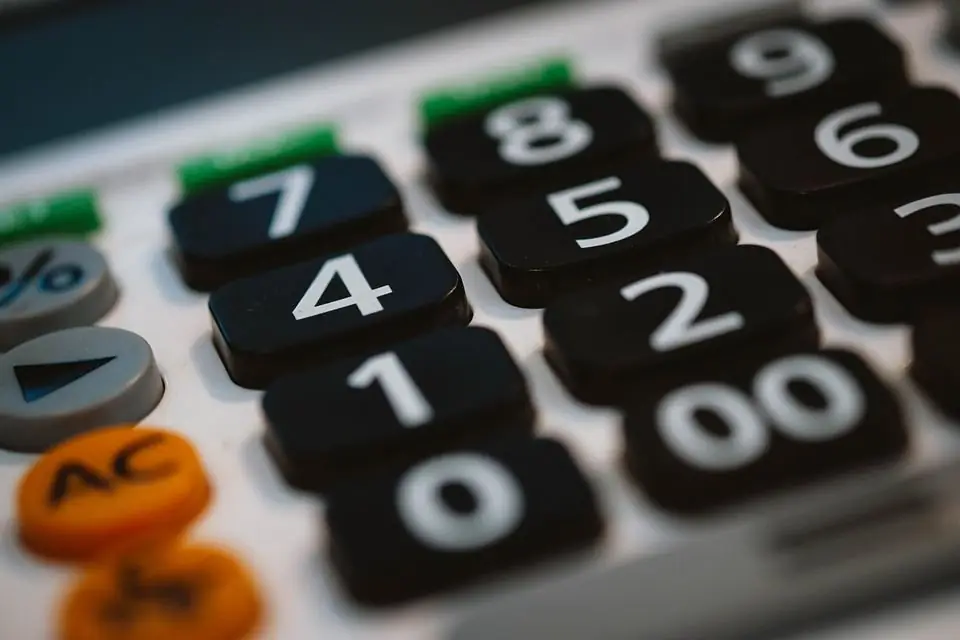
Ways to cut costs
The main tasks of economic entities in market conditions in the course of their activities can be called actions aimed at making a profit, including cost reduction within reasonable limits.
Reducing the cost of raw materials can significantly worsen the quality of products, which leads to a deterioration in the financial condition of the company. To resolve this issue, it is possible to purchase cheaper substitutes for raw materials or purchase goods in large quantities at wholesale prices. It is also necessary to comply with the modes of saving the use of inventory to eliminate damage and possible losses.
Utilities costs are constant, reasonable use of energy, water resources, fuel can save cost items.
A thorough study of each element of costs allows you to determine the need for certain costs, find ways to reduce them. The ultimate goal of these tasks is to obtain the maximum possible amount of profit and increase profitability.
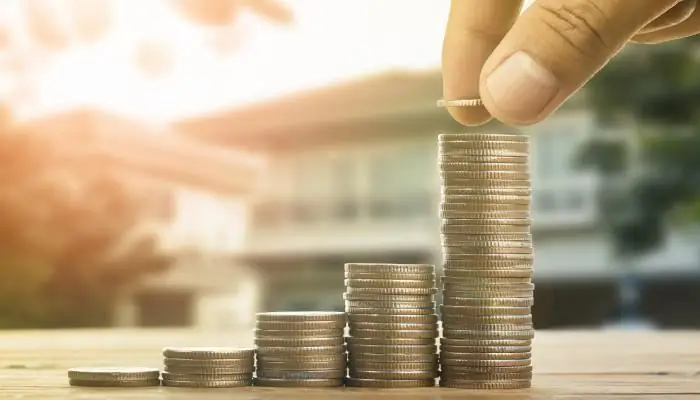
Conclusion
Cost is one of the most important indicators of the quality of any enterprise. It has no permanent value. The cost price tends to change and dynamics. Therefore, it is very important to periodically calculate it. Thanks to this, it is possible to regulate the market cost of goods, thereby avoiding bankruptcy and unnecessary costs for the enterprise.