Company management must understand that quality management is a complex and purposeful process that affects the entire structure of the enterprise - from appointment to the production and sale of finished products.
Despite this, the effective functioning of the quality management system is impossible in the absence of objective and reliable information of a quantitative and qualitative nature. The main purpose of using quality management tools in an enterprise is to develop practical skills for analysis, ensuring control over the level of production of services and products.
What issues need to be considered?
For a long time, experts in the field of quality definition were able to identify the basic concepts, which include:
- qualification (Philip Crosby);
- correspondence of the quality of the goods to the money given for it;
- consumer acceptability;
- satisfaction with the requirements and requests of the buyer;
- roadworthiness (Juran);
- the principle by which the consumer returns to the producer,not the product or service produced.
The last definition is considered one of the most important, as it is mainly focused on the consumer and includes the creation of products or services that can fully meet expectations. The buyer, having made a monetary transaction and received the product, must be completely satisfied and after some time, return to make new orders and purchases.
Dependence of the quality of a thing on production
What is the quality of a thing and the quality of its production? To understand this, you should use the following relationship:
- doing the wrong thing right is good;
- doing the right thing right is good;
- doing the wrong thing wrong is bad;
- doing the right thing wrong is bad.
Quality Tools
Modern quality management tools are as follows:
- brainstorming technique;
- affinity diagram;
- link diagram;
- tree diagram;
- matrix chart;
- arrow chart;
- network chart;
- Gantt chart;
- process flowchart;
- priority matrix.
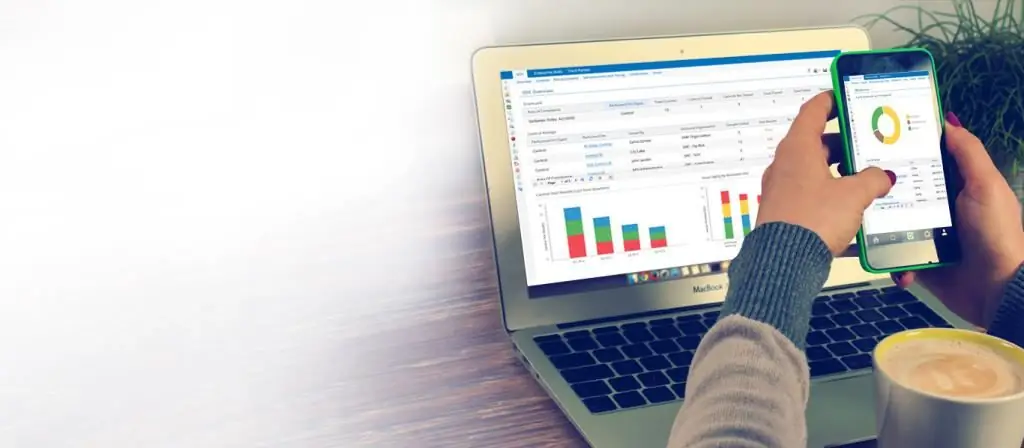
All the described tools for monitoring the production process have the following goals:
- mastering the basic quality assurance tools in product design and customer service;
- developmentpractical skills in applying benchmarking and QFD methodology;
- a detailed study of how to analyze the quality level as the basis for making management decisions in the field of TQM;
- gaining the skills to create a quality control system with static methods at the core.
Seven Popular Instruments
There are also seven quality management tools that no production can do without:
- histogram;
- Pareto chart;
- control cards;
- scatterplot;
- stratification;
- control sheet;
- Ishikawa diagram.
What is the goal matrix?
Experts recommend adhering to the following rule during production: "You can bargain for the price, but not for the quality." It is for this reason that the quality of the products produced should remain the fundamental goal of any entrepreneur.
It should be set at the initial stage of product production, as it will not be possible to embed it later. Quality must be planned from the very first stage of product development. Quality issues are better addressed through the establishment of an effective, cost-effective preventive action system that will consistently improve the quality of services and products.
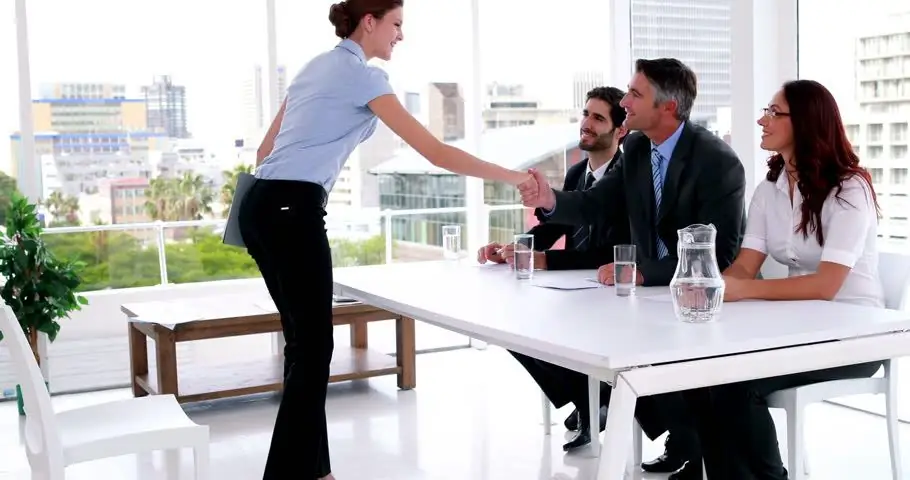
Another important rule to keep in mind throughout production is the ten times cost rule. Empirically, it was proved that the elimination of a lack of a product at the stagedesign creation on average costs the enterprise ten times cheaper than if such a defect was identified in the production process itself. If a significant defect has already been identified in the hands of the consumer, then the price of its elimination increases ten times more, which is twenty in total.
New tools in production
Most of the quality control tools discussed earlier in production are used to analyze numerical indicators, which meets the requirement of TQM: decision-making is based on facts.
But it is important to remember that facts are not always numerical, so in order to be ready to make decisions of any nature, it is important to have at least a minimal understanding of behavioral sciences, operational analysis, optimization theory and statistics. To do this, the Union of Japanese Scientists and Engineers, on the basis of the considered sciences, has created a powerful and effective set of tools for the quality work of an enterprise, which helps to greatly facilitate the process of quality management in an enterprise.
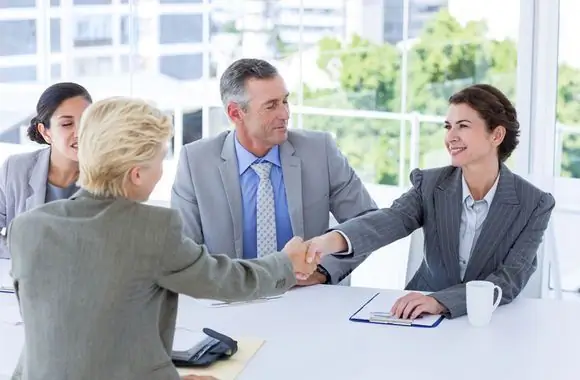
Although quality control tools are often considered new, different companies have already used them at different time intervals. They are effective in dealing with issues that arise during the design of products, unlike other tools that are useful only at the time of production.
These assistants are best suited for improving the quality of production by creatingproduct or service. New quality management tools include:
- affinity diagram;
- link diagram;
- tree diagram;
- matrix chart;
- arrow chart;
- diagram of the program implementation process;
- priority matrix.
It is important to remember that each of the described tools is closely interconnected and inseparable during production.
How is it done?
The collection of information for quality tools is most often carried out at the time of brainstorming. Brainstorming is used to develop in a group the maximum number of new and different ideas on a certain issue in a short time.
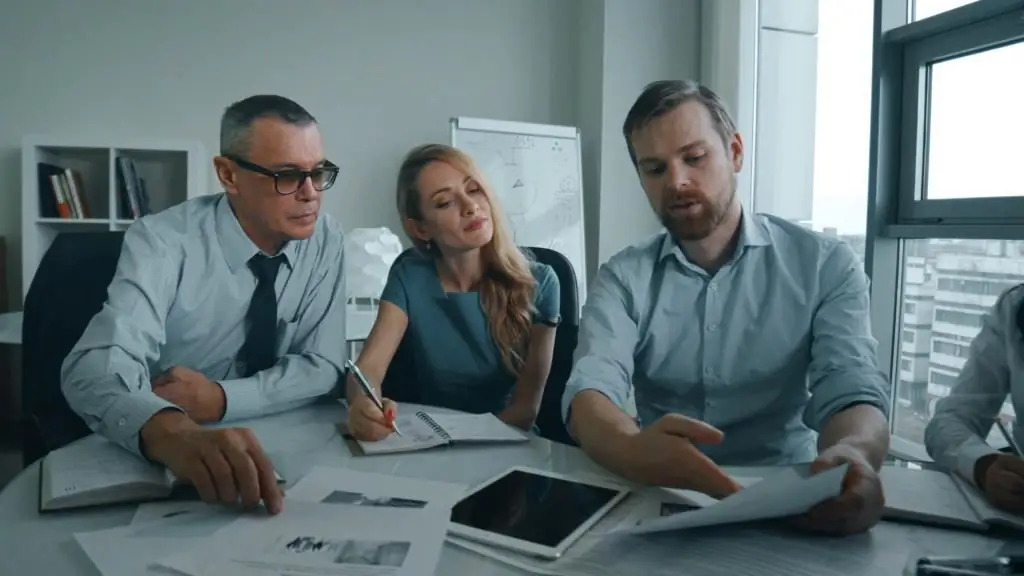
It is carried out in several ways:
- Ordered - each employee of the enterprise, in the next order, submits an interesting idea, which he considers the most successful in a particular situation for the project. This is how you can encourage even the most silent people to communicate, but in this case it is important to remember about the elements of pressure, which can sometimes interfere greatly.
- Disordered - members of the organization do not share their ideas at a specific time, but as something comes to mind. But in this way, a high-risk atmosphere is created and there is a danger that attention will be given only to the ideas of those people who, by their nature, talk a lot.
How should a leader behave?
In both ways, the rulesBrainstorming is almost the same. The organizer of the organization is best to behave by following the following pattern.
- Never criticize ideas coming from employees - it is recommended to take each of them into account, write it down on a board or a separate sheet. If the participant's thought is conveyed clearly and written on the board, then everyone can understand it and, based on it, even create new ideas.
- Everyone must agree on the issue that will be raised at the time of the brainstorm.
- It is recommended to write down proposed ideas on a piece of paper or a board word for word without modifying them.
- Brainstorming should be carried out quickly, it is best to spend 15-45 minutes for this, but no more.
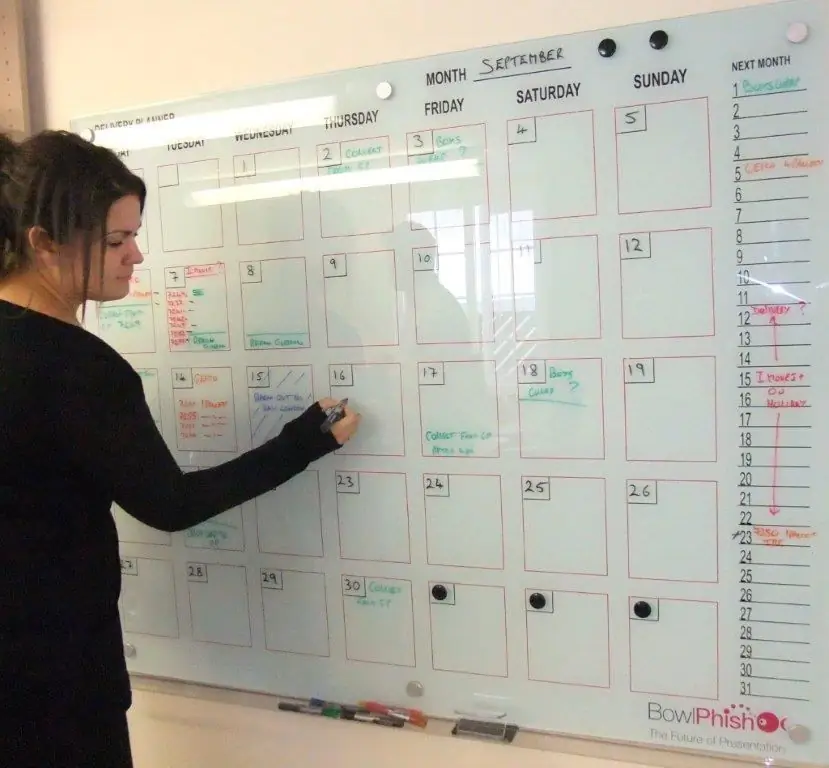
Affinity diagram
The affinity diagram is one of the 7 statistical type quality management tools. It helps to identify the main violations using verbal data. Sometimes such a diagram is called the KJ method (in honor of its founder, Japanese scientist Jiro Kawakita).
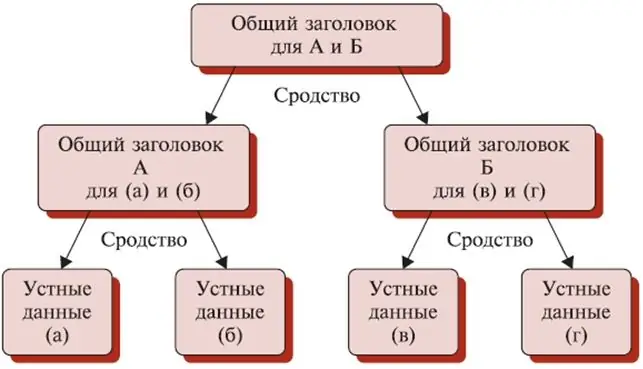
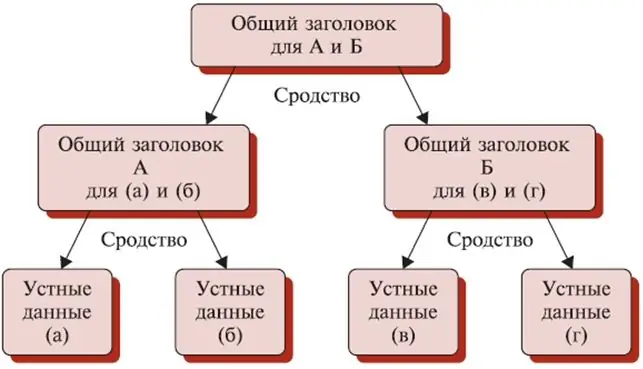
An affinity diagram is built when, after brainstorming, the organizer has received too many new and interesting ideas, information and points of view that need to be grouped into one in order to determine their relationship. This method of analysis is most often used in order to correlate in a creative way all the ideas expressed by the members of the organization. Building an affinity diagram,usually goes the following way.
- The subject or topic is identified, which will become the basis for collecting useful information.
- Collection of information that employees of the enterprise will express during the brainstorming. It is very important to collect ideas in a random order. Each message must be entered on the card by a separate participant.
- Afterwards, you need to make sure that all related data is grouped in the direction of different levels.
To do this, find cards that seem even minimally related to each other, put them together. Then fold again. The work ends at the moment when all the information is laid out on the shelves, clear and understandable. This makes it possible to obtain groups of related data in which a specific focus is located. Such a focus should unify the affinity of each group of data. This can be done in another way, by selecting one card and making it the main one, or by creating a new direction.
The described manipulations can be repeated, but with a summary of the main directions, thereby creating a real hierarchy. The analysis is considered complete when all the received data are grouped according to the number of leading directions.
Building a link diagram
A mind map is a quality management tool and method that helps to determine the logical relationships between the main and secondary ideas, solves problems with different data. The basis for constructing a diagram is the same principle as with an affinity diagram. To the centerthe main idea, problem or question is posed, and then additional links are put aside that connect individual factors that are directly or indirectly related to the question posed.
A link diagram can be easily recreated based on the ideas that were taken into account during the construction of the affinity diagram. At the same time, it is important to look for those links that can provide a critical result. The mind map is the most powerful logical tool as opposed to the more creative affinity diagram.
When is a mind map useful?
- when the issue at hand is so complex that the links between the ideas put forward cannot be determined through simple discussion;
- when the time sequence on which steps are taken is critical;
- when there is a suspicion that the problem raised in the question is a symptom of a more complex and untouched problem.
As in the case of the affinity diagram, the procedure for constructing the table must be carried out in a specific group. In this case, the most important thing to pay attention to is that the subject under investigation must be determined in advance.
Tree diagram and its construction principle
Tree diagram (systematic) is a tool and method of quality management that helps to determine the method of resolving the issue raised, the central idea, and also to satisfy needs that differ in different levels of complexity. Tree Diagramcan be seen as an extension of the link diagram. It is created on the basis of a multi-stage tree structure, the elements of which are different means and methods for solving the issue that has arisen.
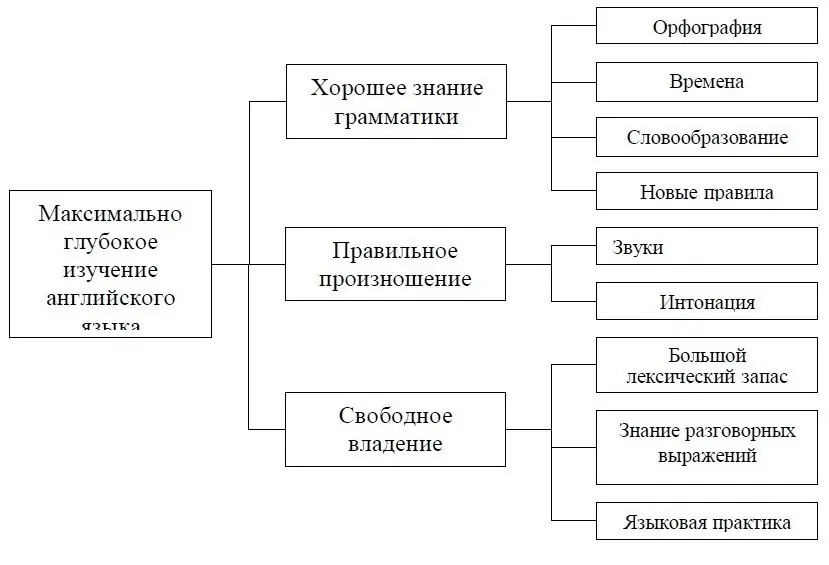
The tree diagram as a management and quality control tool is considered the most effective and useful for the production process. The process of reproducing a diagram is similar to the process of constructing an affinity diagram, but in this case it is important to remember that the subject that is being examined must be pre-determined and recognized.
The tree diagram is the main quality management tool used in the following cases:
- when the organizing team is not completely clear about the wishes of the consumer regarding a particular product;
- when you need to research all the parts that somehow affect the problem;
- when short-term goals need to be achieved before the results of the work, even at the time of product design or project preparation.
As an example, we can mention the purpose of creating English courses. Most often, the main goal is to provide in-depth knowledge of the subject. However, every person who is about to start learning a language means something different by deep knowledge. Some need speaking practice, some need grammar rules, some want to improve their pronunciation.
It is for this reason that a tree diagram was created when creating courses, which helps to put into practicelevel all the requirements put forward in random order. Based on such a diagram, the most effective program for teaching schoolchildren and students is being developed.
Matrix chart
Matrix chart is a management and quality control tool that helps to recreate the relationship between the main idea and the problem, different data obtained during the discussion. The use of quality management tools is important for organizing a large flow of incoming information and illustrating the relationships between different elements through graphs.
The main purpose of the diagram is to depict the contour of relationships and the correlation between functions, tasks and characteristics, followed by highlighting their degree of importance.