To effectively use metals in various designs, it is important to know how strong they are. Hardness is the most commonly calculated quality characteristic of metals and alloys. There are several methods for its determination: Brinell, Rockell, Super-Rockwell, Vickers, Ludwik, Shor (Monotron), Martens. The article considers the method of the Rockwell brothers.
What is the method
Rockwell method is a method of testing materials for hardness. For the element under study, the penetration depth of the hard tip of the indicator is calculated. In this case, the load remains the same for each hardness scale. Usually it is 60, 100 or 150 kgf.
Indicator in the study are balls of durable material or diamond cones. They should have a rounded pointed end and a 120-degree apex angle.
This method has been found to be simple and quickly reproducible. Which gives it an advantage over other methods.
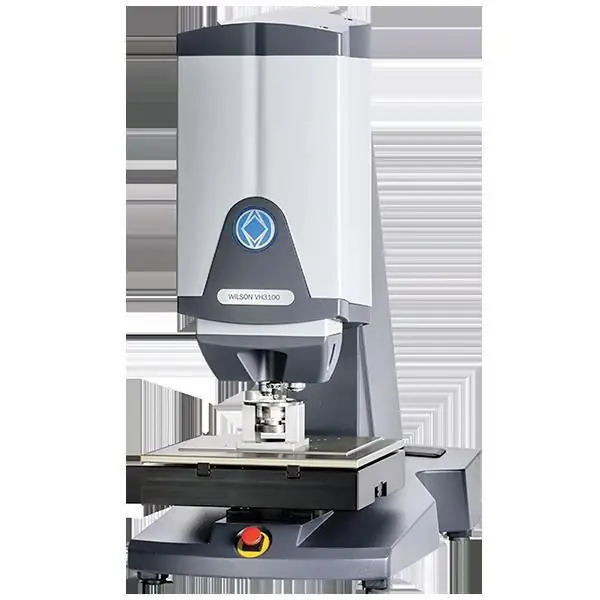
History
Vienna research professor Ludwig first proposed the use of an indenter for researchhardness by penetrating the material and calculating the relative depth. His method is described in the 1908 work Die Kegelprobe.
This method had drawbacks. The brothers Hugh and Stanley Rockwell proposed a new technology that eliminated the errors of the mechanical imperfection of the measurement system (backlashes and surface defects, contamination of materials and parts). Professors invented a hardness tester - a device that determines the relative depth of penetration. It was used to test steel ball bearings.
Determination of the hardness of metals by the methods of Brinell and Rockwell deserved attention in the scientific community. But the Brinell method was inferior - it was slow and was not used for hardened steels. Thus, it could not be considered a non-destructive testing method.
In February 1919, the hardness tester was patented under the number 1294171. At this time, the Rockwells worked for a ball bearing company.
In September 1919, Stanley Rockwell left the company and moved to New York State. There he submitted an application for improvement of the device, which was accepted. New device patented and improved by 1921.
In late 1922, Rockwell founded a heat treatment plant that still operates in Connecticut. Part of Instron Corporation since 1993.
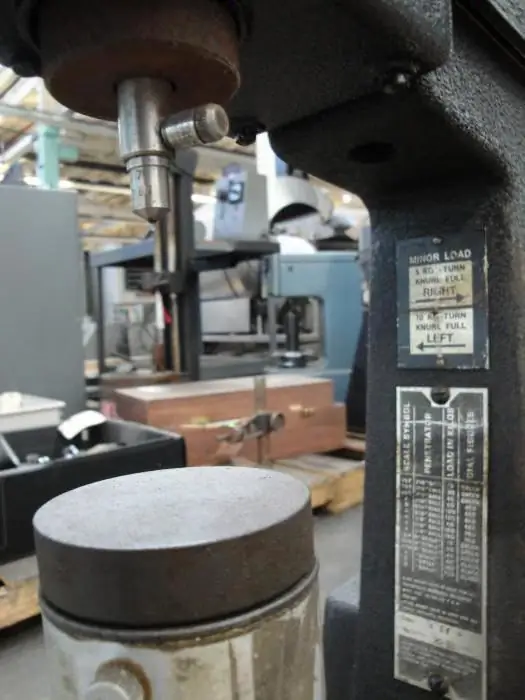
Advantages and disadvantages of the method
Each hardness calculation method is unique and applicable in some area. Brinell and Rockwell hardness methodsare basic.
There are a number of advantages of the method:
- possibility of high hardness experiments;
- minor surface damage during testing;
- simple method that does not require measurement of the indentation diameter;
- testing process is fast enough.
Flaws:
- compared to Brinell and Vickers hardness testers, the Rockwell method is not accurate enough;
- must carefully prepare the sample surface.
The structure of the Rockwell scale
To test the hardness of metals by the Rockwell method, only 11 scales have been derived. Their difference lies in the ratio of the tip and the load. The tip can be not only a diamond cone, but also a ball made of an alloy of carbide and tungsten or hardened steel in the form of a sphere. The tip fixed in the installation is called the identifier.
Scales are usually denoted by letters of the Latin alphabet: A, B, C, D, E, F, G, H, K, N, T.
Strength tests are carried out with the main scales - A, B, C:
- Scale A: testing with a diamond cone with a load of 60 kgf. Designation - HRA. Such tests are carried out for thin hard materials (0.3-0.5 mm);
- Scale B: 100 kgf steel ball test. Designation - HRB. Tests are carried out on annealed mild steel and non-ferrous alloys;
- Scale C: 150 kgf cone test. Designation - HRC. Tests are carried out for medium hard metals, hardened and tempered steel or layers with a thickness of not more than 0.5 mm.
Hardness by methodRockwell is usually denoted HR with the third letter of the scale (for example, HRA, HRC).
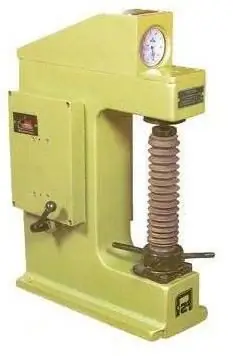
Formula for calculation
The hardness of the material affects the penetration depth of the tip. The harder the test object, the less penetration will be.
To numerically determine the hardness of a material, a formula is needed. Its coefficients depend on the scale. To reduce the measurement error, one should accept the relative difference in the penetration depth of the indenter at the moment of application of the main and preliminary (10 kgf) load.
The Rockwell hardness measurement method involves the use of the formula: HR=N-(H-h)/s, where the difference H-h denotes the relative penetration depth of the indenter under loads (preliminary and main), the value is calculated in mm. N, s are constants, they depend on the specific scale.
Rockwell hardness tester
Hardness tester is a device for determining the hardness of metals and alloys by the Rockwell method. It is a device with a diamond cone (or ball) and the material into which the cone must enter. A weight is also attached to adjust the impact force.
Time indicator displays. The process takes place in two stages: first, pressing is done with a force of 10 kgf, then stronger. For more pressing, a cone is used, for less, a ball.
The test material is placed horizontally. The diamond is lowered onto it with a lever. For a smooth descent, the device uses a handle with an oil shock absorber.
The main load time is usuallyis 3 to 6 seconds, depending on the material. Preload must be maintained until test results are available.
The large arrow of the indicator moves clockwise and reflects the result of the experiment.
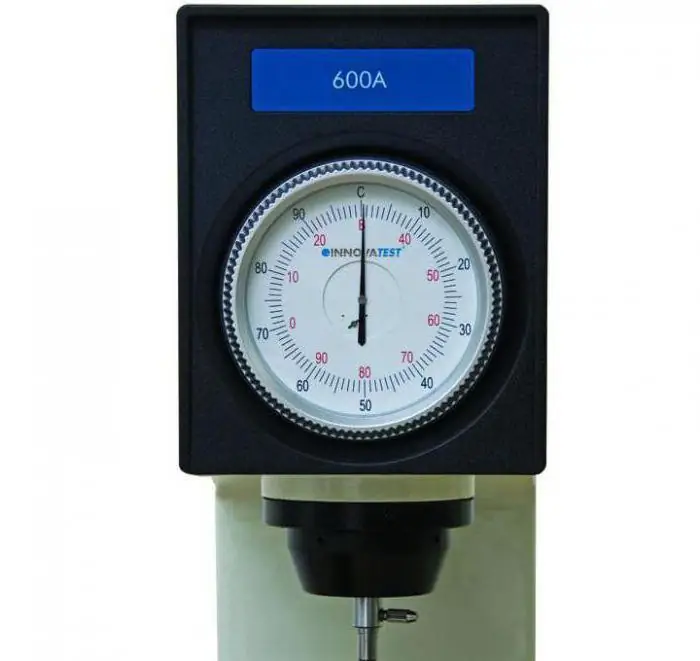
The most popular in practice are such rockwell hardness tester models:
- Stationary devices "Metrotest" model "ITR", for example, "ITR-60/150-M".
- Qness GmbH model Q150R.
- Stationary automated device TIME Group Inc model TH300.
Test Methodology
Research requires careful preparation. When determining the hardness of metals by the Rockwell method, the surface of the sample must be clean, free of cracks and scales. It is important to constantly check whether the load is applied perpendicularly to the surface of the material, and whether it is stable on the table.
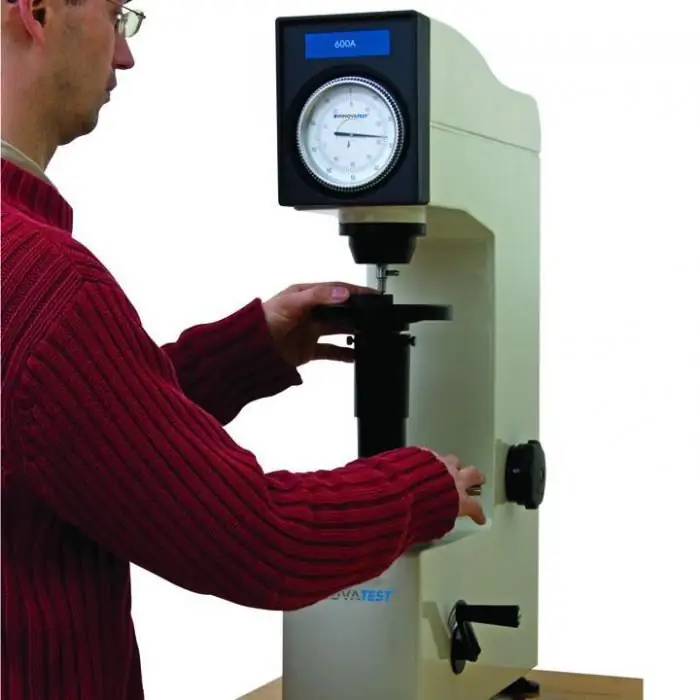
The imprint when pushing the cone should be at least 1.5 mm, and when pushing the ball - more than 4 mm. For effective calculations, the sample must be 10 times thicker than the penetration depth of the indenter after the removal of the main load. Also, at least 3 tests of one sample should be carried out, after which the results should be averaged.
Test steps
In order for the experiment to have a positive result and a small error, you should follow the order of its conduct.
Stages of the experiment on the method of determining hardness byRockwell:
- Determine the choice of scale.
- Install the required indenter and load.
- Perform two test (not included in the results) prints to correct the installation of the device and the sample.
- Place the reference block on the instrument table.
- Test the preload (10 kgf) and reset the scale.
- Apply the main load, wait for maximum results.
- Remove the load and read the received value on the dial.
Regulations allow testing of one sample when testing mass products.
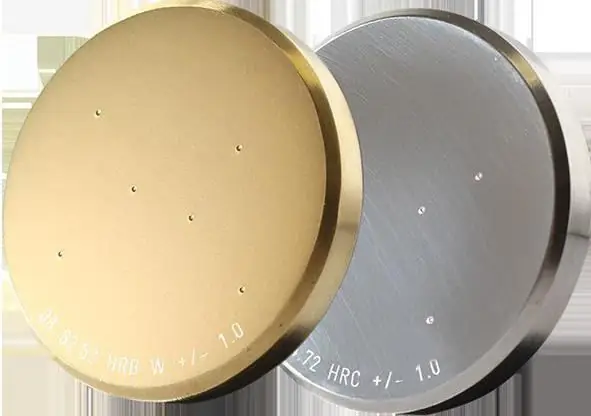
Which will affect accuracy
When conducting any test, it is important to consider many factors. Rockwell hardness detection also has its own characteristics.
Factors to pay attention to:
- The thickness of the test specimen. It is forbidden by the rules of the experiment to use a sample that is less than ten times the penetration depth of the tip. That is, if the penetration depth is 0.2 mm, then the material must be at least 2 cm thick.
- There must be a distance between the prints on the sample. It is three diameters between the centers of near prints.
- One should take into account the possible change in the results of the experiment on the dial, depending on the position of the researcher. That is, the reading of the result should be carried out from one viewpoint.
Mechanical properties in testsstrength
Relate and investigate the strength characteristics of materials and the results of hardness testing by the Rockwell hardness method were obtained by such material scientists as Davidenkov N. N., Markovets M. P. and others.
According to the results of the indentation hardness test, methods for calculating the yield strength are applied. This relationship is calculated for high chromium stainless steels that have undergone multiple heat treatments. The average deviation value, when using a diamond indenter, was only +0.9%.
Research is also underway to determine other mechanical properties of materials related to hardness. For example, tensile strength (or tensile strength), true fracture resistance and relative contraction.
Alternative methods for determining hardness
Measuring hardness is possible not only by the Rockwell method. Consider the main points of each method and their differences. Static load test:
- Study samples. The Rockell and Vickers methods make it possible to test relatively soft and high strength materials. The Brinell method is designed to study softer metals with hardness up to 650 HBW. The Super-Rockwell method allows hardness testing at low loads.
- GOSTs. Rockwell method complies with GOST 9013-59, Brinell method - 9012-59, Vickers method - 2999-75, Shor method - GOST 263-75, 24622-91, 24621-91, ASTM D2240, ISO 868-85.
- Durometers. Rockwell and Shore researchers' devices are simpleuse and small size. Vickers equipment allows testing on very thin and small specimens.
Experiments under dynamic pressure were carried out according to the method of Martel, Poldi, using the Nikolaev vertical impact tester, the Schopper and Bauman spring device and others.
Hardness can also be measured by scratching. Such tests were carried out using a Barb file, Monters, Hankins, Birbaum microcharacterizer and others.
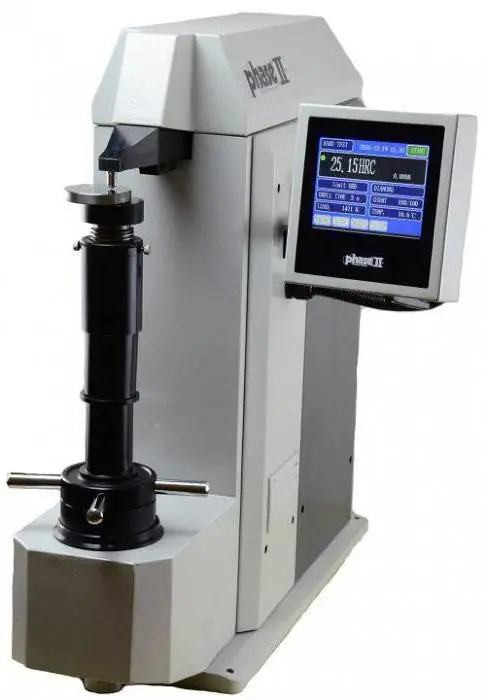
Despite its shortcomings, the Rockwell method is widely used for hardness testing in industry. It is easy to perform, mainly due to the fact that it is not necessary to measure the print under a microscope and polish the surface. But at the same time, the method is not as accurate as the proposed studies of Brinell and Vickers. Hardness, measured in different ways, has a dependence. That is, Rockwell effective units can be converted to Brinell units. At the legislative level, there are regulations such as ASTM E-140 that compare hardness values.