Electric motors appeared quite a long time ago, but great interest in them arose when they began to represent an alternative to internal combustion engines. Of particular interest is the question of the efficiency of the electric motor, which is one of its main characteristics.
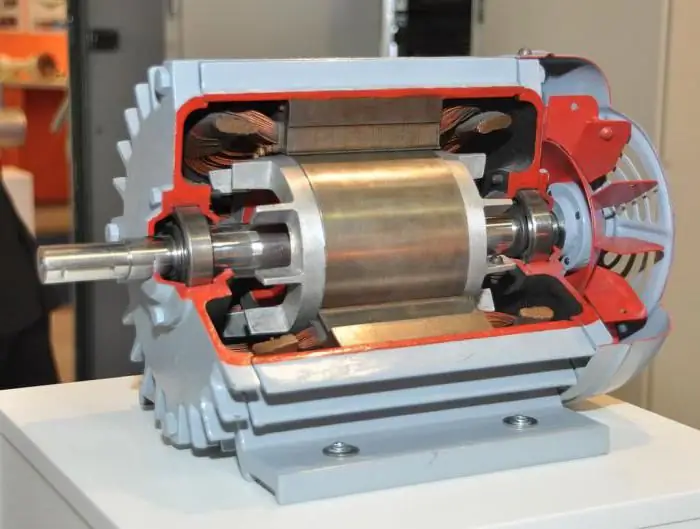
Each system has some kind of efficiency, which characterizes the efficiency of its work as a whole. That is, it determines how well a system or device delivers or converts energy. By value, the efficiency has no value, and most often it is presented as a percentage or a number from zero to one.
Efficiency parameters in electric motors
The main task of the electric motor is to convert electrical energy into mechanical energy. Efficiency determines the efficiency of this function. The motor efficiency formula is as follows:
n=p2/p1
In this formula, p1 is the supplied electrical power, p2 is the useful mechanical power that is generated directlyengine. Electrical power is determined by the formula: p1=UI (voltage multiplied by current), and the value of mechanical power according to the formula P=A/t (the ratio of work to unit time). This is how the calculation of the efficiency of the electric motor looks like. However, this is the simplest part of it. Depending on the purpose of the engine and its scope, the calculation will differ and take into account many other parameters. In fact, the motor efficiency formula includes many more variables. The simplest example was given above.
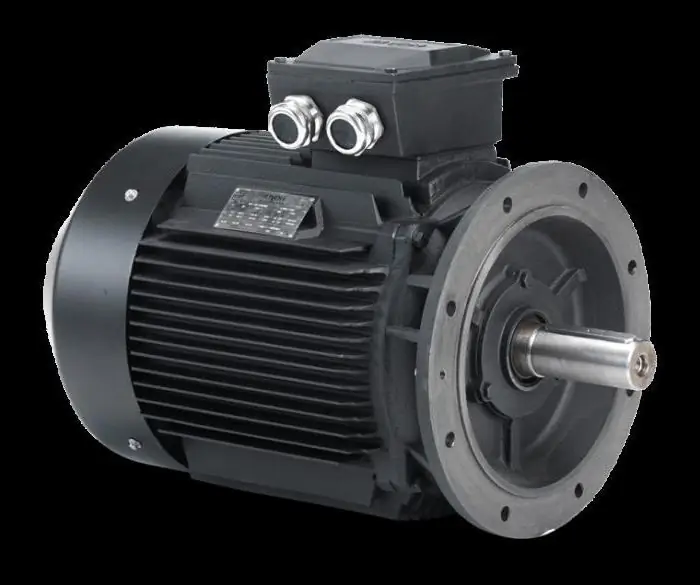
Reduced efficiency
The mechanical efficiency of an electric motor must be taken into account when choosing a motor. Losses associated with motor heating, power reduction, and reactive currents play a very important role. Most often, the drop in efficiency is associated with the release of heat, which naturally occurs during engine operation. The reasons for the release of heat can be different: the engine can heat up during friction, as well as for electrical and even magnetic reasons. As the simplest example, we can cite a situation where 1,000 rubles were spent on electrical energy, and work was done for 700 rubles. In this case, the efficiency will be equal to 70%.
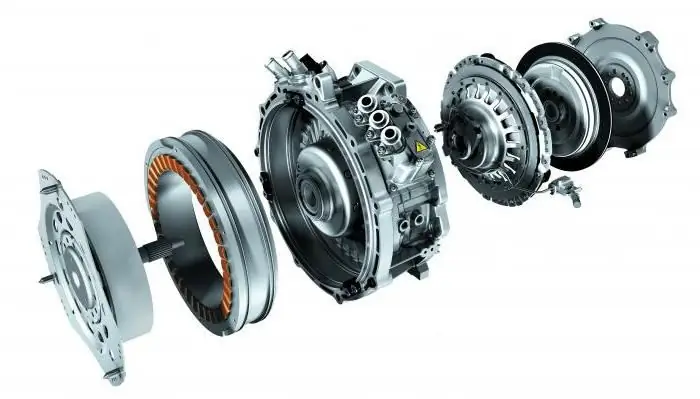
To cool electric motors, fans are used to force air through the created gaps. Depending on the class of engines, heating can be carried out up to a certain temperature. For example, class A motors can get hotup to 85-90 degrees, class B - up to 110 degrees. In the event that the temperature exceeds the permissible limit, this may indicate a stator short circuit.
Average efficiency of electric motors
It is worth noting that the efficiency of a DC (and AC) motor varies depending on the load:
- Efficiency is 0% at idle.
- At 25% load, efficiency is 83%.
- At 50% load, the efficiency is 87%.
- At 75% load, the efficiency is 88%.
- At 100% load, the efficiency is 87%.
One of the reasons for the drop in efficiency is the asymmetry of the currents, when a different voltage is applied to each of the three phases. If, for example, the first phase has a voltage of 410 V, the second - 403 V, and the third - 390 V, then the average value will be 401 V. The asymmetry in this case will be equal to the difference between the maximum and minimum voltages on the phases (410 -390), that is, 20 V. The motor efficiency formula for calculating losses will look like in our situation: 20/401100=4.98%. This means that we lose 5% efficiency during operation due to the voltage difference in the phases.
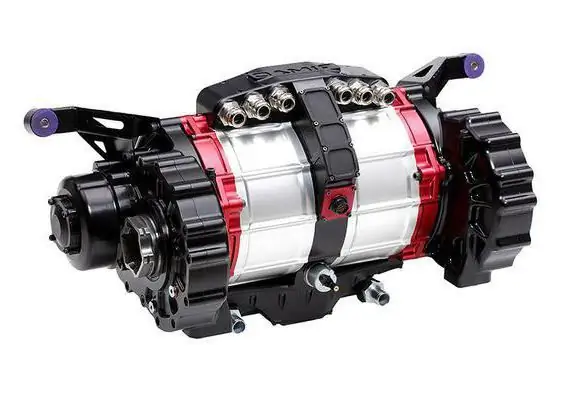
Total losses and drop in efficiency
There are a lot of negative factors that affect the drop in the efficiency of an electric motor. There are certain methods that allow you to determine them. For example, you can determine if there is a gap through which power is partially transferred from the network to the stator and then to the rotor.
Starter losses also occur, and they consist of severalvalues. First of all, these can be losses related to eddy currents and remagnetization of the stator cores.
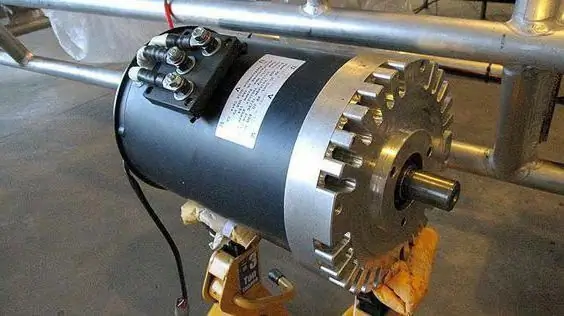
If the motor is asynchronous, then there are additional losses due to the teeth in the rotor and stator. Eddy currents can also occur in individual engine components. All this in total reduces the efficiency of the electric motor by 0.5%. In asynchronous motors, all losses that may occur during operation are taken into account. Therefore, the efficiency range can vary from 80 to 90%.
Automotive engines
The history of the development of electric motors begins with the discovery of the law of electromagnetic induction. According to him, the inductive current always moves in such a way as to counteract the cause that causes it. It was this theory that formed the basis for the creation of the first electric motor.
Modern models are based on the same principle, but radically different from the first copies. Electric motors have become much more powerful, more compact, but most importantly, their efficiency has increased significantly. We have already written above about the efficiency of an electric motor, and compared to an internal combustion engine, this is an amazing result. For example, the maximum efficiency of an internal combustion engine reaches 45%.
Electric motor advantages
High efficiency is the main advantage of such a motor. And if an internal combustion engine spends more than 50% of energy on heating, then in an electric motor a small part is spent on heatingenergy.
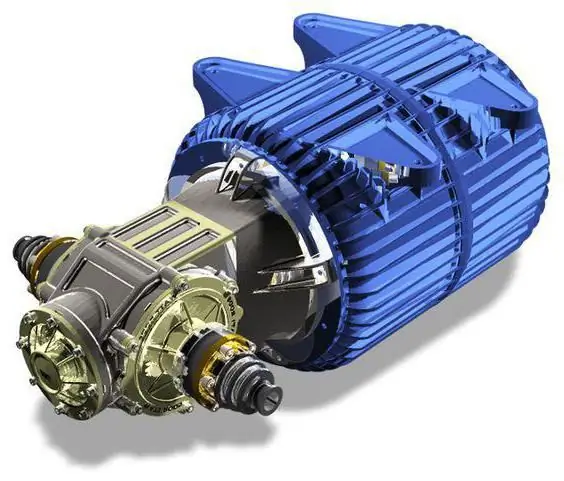
The second advantage is light weight and compact size. For example, Yasa Motors has created a motor with a weight of only 25 kg. It is capable of delivering 650 Nm, which is a very decent result. Also, such motors are durable, do not need a gearbox. Many electric car owners talk about the efficiency of electric motors, which is logical to some extent. After all, during operation, the electric motor does not emit any combustion products. However, many drivers forget that it is necessary to use coal, gas or enriched uranium to generate electricity. All these elements pollute the environment, so the environmental friendliness of electric motors is a very controversial issue. Yes, they do not pollute the air during operation. For them, power plants do this in the production of electricity.
Improve the efficiency of electric motors
Electric motors have some drawbacks that have a bad effect on work efficiency. These are weak starting torque, high starting current and inconsistency between the mechanical torque of the shaft and the mechanical load. This leads to the fact that the efficiency of the device decreases.
To improve efficiency, they try to load the engine to 75% or more and increase power factors. There are also special devices for regulating the frequency of the supplied current and voltage, which also leads to increased efficiency and increased efficiency.
One of the most popular devices for increasing the efficiency of an electric motor is a smoothstart, which limits the rate of growth of the inrush current. It is also appropriate to use frequency converters to change the speed of rotation of the motor by changing the frequency of the voltage. This leads to a reduction in power consumption and provides a smooth start of the engine, high adjustment accuracy. The starting torque also increases, and with a variable load, the rotation speed stabilizes. As a result, the efficiency of the electric motor is increased.
Maximum motor efficiency
Depending on the type of construction, the efficiency of electric motors can vary from 10 to 99%. It all depends on what kind of engine it will be. For example, the efficiency of a piston-type pump motor is 70-90%. The final result depends on the manufacturer, the design of the device, etc. The same can be said about the efficiency of the crane motor. If it is equal to 90%, then this means that 90% of the consumed electricity will be used to perform mechanical work, the remaining 10% will be used to heat parts. Still, there are the most successful models of electric motors, the efficiency of which is close to 100%, but not equal to this value.
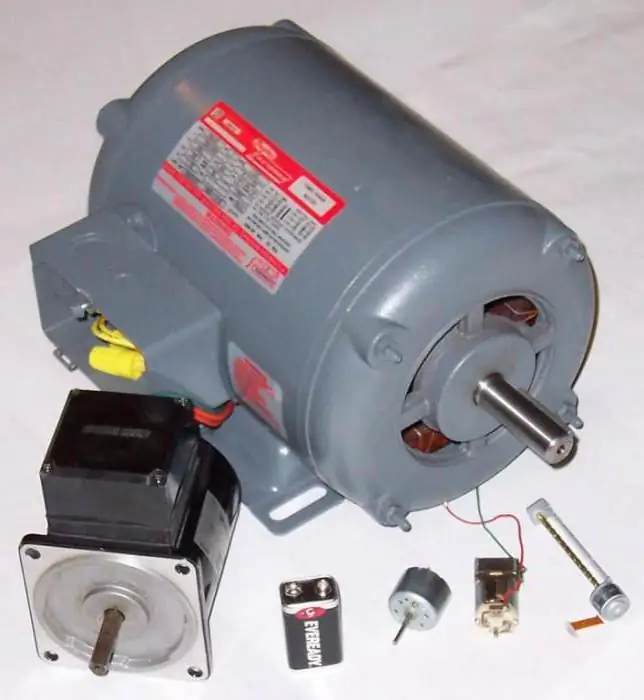
Is it possible to achieve over 100% efficiency?
It's no secret that electric motors whose efficiency exceeds 100% cannot exist in nature, as this contradicts the basic law of conservation of energy. The fact is that energy cannot come from nowhere and disappear in the same way. Every engine needsenergy source: gasoline, electricity. However, gasoline is not eternal, like electricity, because their stocks have to be replenished. But if there was an energy source that did not need to be replenished, then it would be quite possible to create a motor with an efficiency of over 100%. Russian inventor Vladimir Chernyshov showed a description of the engine, which is based on a permanent magnet, and its efficiency, as the inventor himself assures, is more than 100%.
Hydroelectric as an example of a perpetual motion machine
For example, let's take a hydroelectric power plant, where energy is generated by falling from a great height of water. The water turns the turbine, which produces electricity. The fall of water is carried out under the influence of the gravity of the Earth. And although the work of producing electricity is being done, the gravity of the Earth does not become weaker, that is, the force of attraction does not decrease. Then the water evaporates under the action of sunlight and again enters the reservoir. This completes the cycle. As a result, electricity has been generated, and the costs of its production have been restored.
Of course, we can say that the Sun is not eternal, it is true, but it will last a couple of billion years. As for gravity, it is constantly doing work, pulling moisture out of the atmosphere. Generally speaking, a hydroelectric power plant is an engine that converts mechanical energy into electrical energy, and its efficiency is more than 100%. This makes it clear that it is not worth stopping to look for ways to create an electric motor, the efficiency of which can be more than 100%. After all, not only gravity can be used as an inexhaustible sourceenergy.
Permanent magnets as energy sources for motors
The second interesting source is a permanent magnet, which does not receive energy from anywhere, and the magnetic field is not consumed even when doing work. For example, if a magnet attracts something to itself, then it will do the work, and its magnetic field will not become weaker. This property has already been tried more than once to create the so-called perpetual motion machine, but so far nothing more or less normal has come of it. Any mechanism will wear out sooner or later, but the source itself, which is a permanent magnet, is practically eternal.
However, there are experts who say that over time, permanent magnets lose their strength as a result of aging. This is not true, but even if it were true, then it would be possible to bring him back to life with just one electromagnetic pulse. An engine that would require recharging once every 10-20 years, although it cannot claim to be eternal, is very close to this.
There have already been many attempts to create a perpetual motion machine based on permanent magnets. So far there have been no successful solutions, unfortunately. But given the fact that there is a demand for such engines (there simply cannot be), it is quite possible that in the near future we will see something that will come very close to the perpetual motion machine model that will be powered by renewable energy.
Conclusion
The efficiency of an electric motor is the most important parameter that determines the efficiency of a particular motor. The higher the efficiency, the better the motor. In an engine with an efficiency of 95%, almost allthe energy expended is spent on doing work and only 5% is spent not on need (for example, on heating spare parts). Modern diesel engines can reach an efficiency of 45%, and this is considered a cool result. The efficiency of gasoline engines is even less.