Surface roughness is a special material parameter. This name is often shortened to just roughness and is a component of surface texture. It is quantitatively determined by the deviations of the direction of the real surface vector from its ideal shape. If these deviations are large, the surface is rough; if they are small, the surface is smooth. In surface metrology, roughness is usually considered to be the high frequency, short wavelength component of the surface being measured. However, in practice it is often necessary to know both amplitude and frequency to ensure that a surface is suitable for a particular purpose. Surface roughness is a very important design parameter.
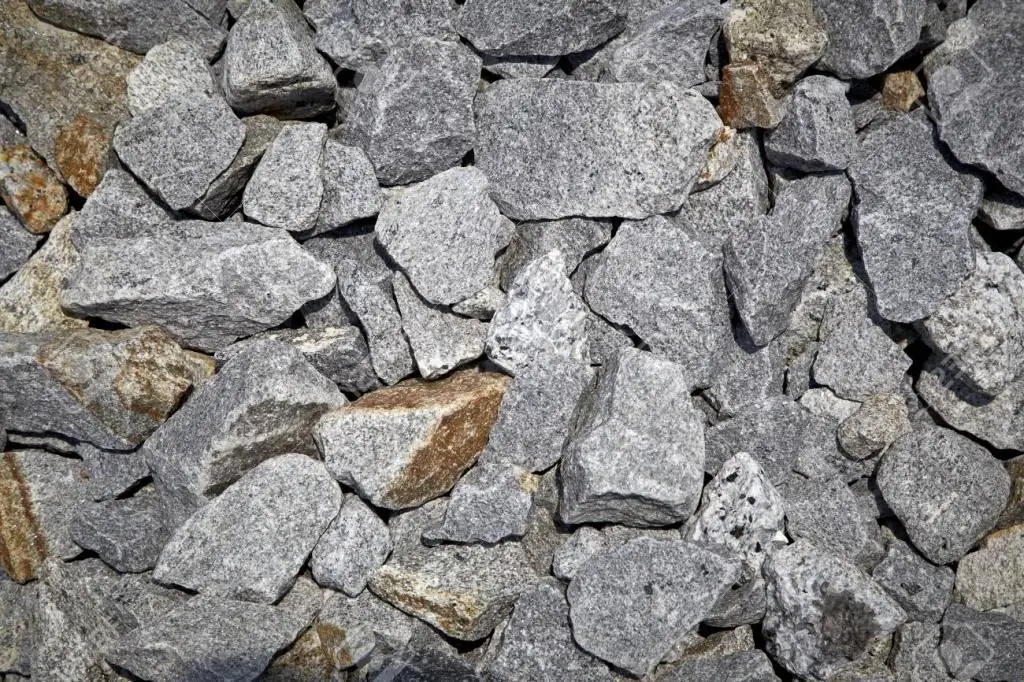
Role and Meaning
Roughness plays an important role in determining how a real object will interact with its environment. In tribologyRough surfaces generally wear faster and have higher coefficients of friction than smooth surfaces. Roughness is often a good predictor of the performance of a mechanical component, as surface irregularities can form nucleation sites for cracks or corrosion. On the other hand, roughness can promote adhesion. Generally speaking, instead of scale descriptors, cross-scale descriptors such as surface fractality provide more meaningful predictions of mechanical interactions on surfaces, including contact stiffness and static friction. Surface roughness is a rather complex parameter, details of which can be found below.
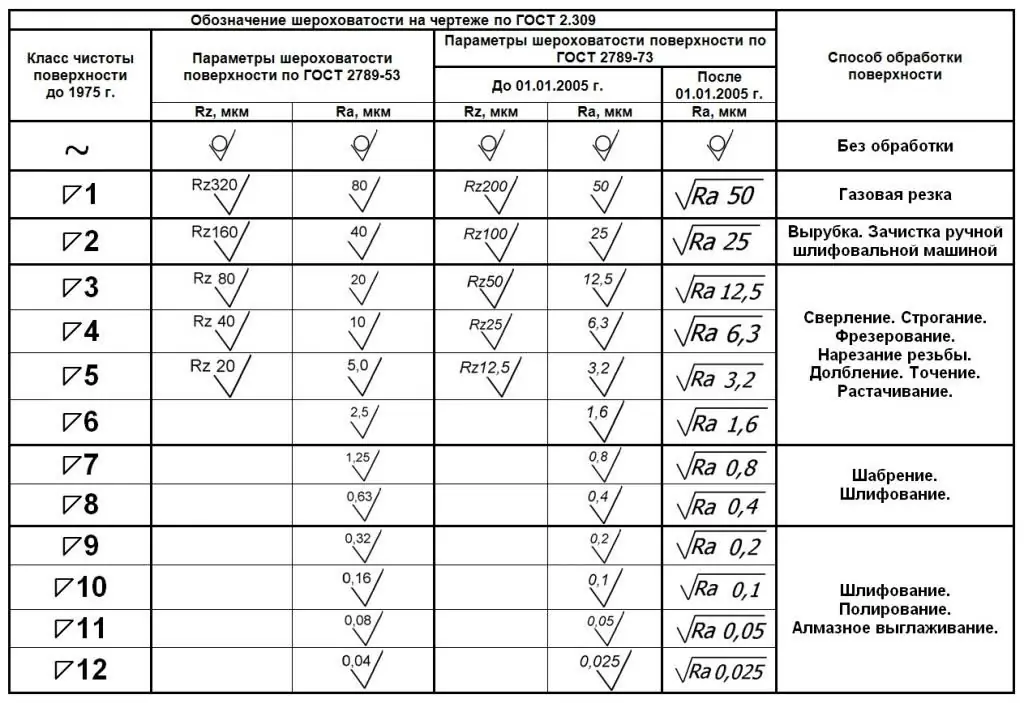
High and low values
Although a high roughness value is often undesirable, it can be difficult and costly to control during manufacture. For example, it is difficult and expensive to control the surface roughness of FDM parts. Reducing these rates usually increases the cost of manufacture. This often results in a trade-off between the cost of producing a component and its efficiency in application.
Measurement methods
The index can be measured by manual comparison with a "roughness comparator" (a sample of known surface roughness), but more generally the measurement of a surface profile is done with profilometers. They can be of the contact type (usually a diamond stylus) or optical (for example,white light interferometer or laser scanning confocal microscope).
However, controlled roughness can often be desirable. For example, a glossy surface can be too shiny for the eyes and too slippery for the finger (a good example is the touchpad), so controlled performance is required. Surface roughness is where amplitude and frequency are very important.
Its value can be calculated either from the profile (line) or from the surface (area). The profile roughness parameter (Ra, Rq, …) is more common. Area roughness parameters (Sa, Sq, …) give more meaningful definitions.
Parameters
Each of the roughness parameters is calculated by the surface description formula. The standard references that describe each of them in detail are the surfaces and their measurements. Surface roughness is a characteristic.
Profile roughness parameters are included in the British (and worldwide) standard BS EN ISO 4287: 2000, which is identical to ISO 4287: 1997. The standard is based on the ″M″ (Midline) system.
There are many different roughness parameters, but the above are the most common, although standardization often occurs for historical reasons rather than merit. Surface roughness is a collection of irregularities.
Some parameters are only used in certain industries or in certain countries. For example, MOTIF parameters are mainly used in the French automotive industry. MOTIF Methodprovides a graphical assessment of the surface profile without filtering out waviness from roughness. MOTIF consists of the portion of the profile between two peaks, and the final combinations eliminate the "minor" peaks and retain the "significant" ones. Surface roughness in a drawing is the presence of bumps imprinted and carefully measured on it.
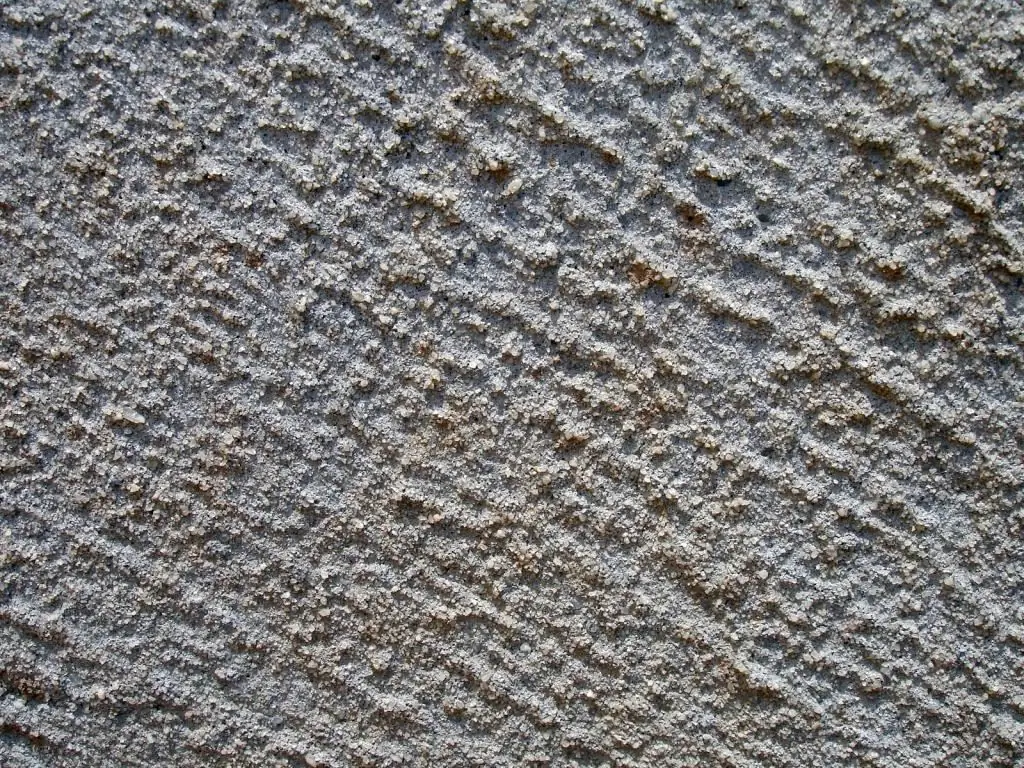
Because these parameters reduce all profile information to a single number, care must be taken when applying and interpreting them. Small changes in how the raw profile data is filtered, how the midline is calculated, and the physics of the measurement can have a big impact on the calculated parameter. On modern digital equipment, scans can be evaluated to ensure there are no obvious glitches that skew values.
Features of parameters and measurements
Because it may not be obvious to many users what each measurement actually means, the modeling tool allows the user to adjust key parameters, rendering surfaces that are distinctly different from the human eye, differ in measurements. For example, some parameters cannot distinguish between two surfaces where one consists of peaks and the other consists of troughs with the same amplitude.
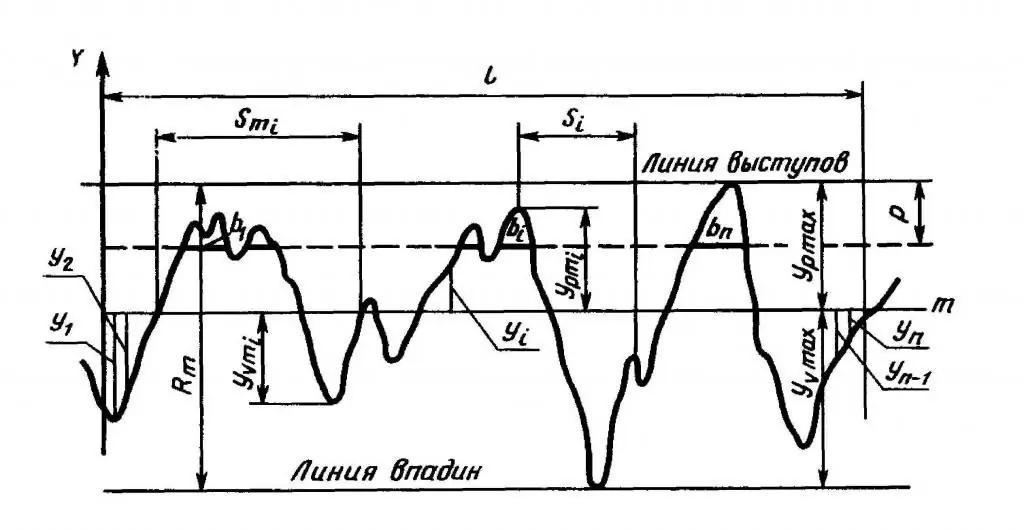
By convention, each 2D roughness parameter is an uppercase R followed by additional characters in a subscript. The subscript specifies the formula that was used, andR means the formula has been applied to a 2D roughness profile.
Different capitalization means the formula has been applied to a different profile. For example, Ra is the arithmetic mean of the roughness profile, Pa is the arithmetic mean of the unfiltered raw profile, and Sa is the arithmetic mean of the 3D roughness.
Amplitude settings
The amplitude parameters characterize the surface based on vertical deviations of the roughness profile from the midline. For example, the arithmetic mean of the filtered roughness profile, determined from the deviations from the centerline within the evaluation length, can be related to the range of points collected for that roughness. This value is often used as a reference to surface roughness.
Arithmetic mean roughness is the most widely used one-dimensional parameter.
Research and observation
Mathematician Benoit Mandelbrot pointed out the relationship between surface roughness and fractal dimension. The description represented by a fractal at the level of microroughness can make it possible to control the properties of the material and the type of chip formation. But fractals cannot provide a full scale representation of a typical machined surface affected by tool feed marks, they ignore cutting edge geometry.
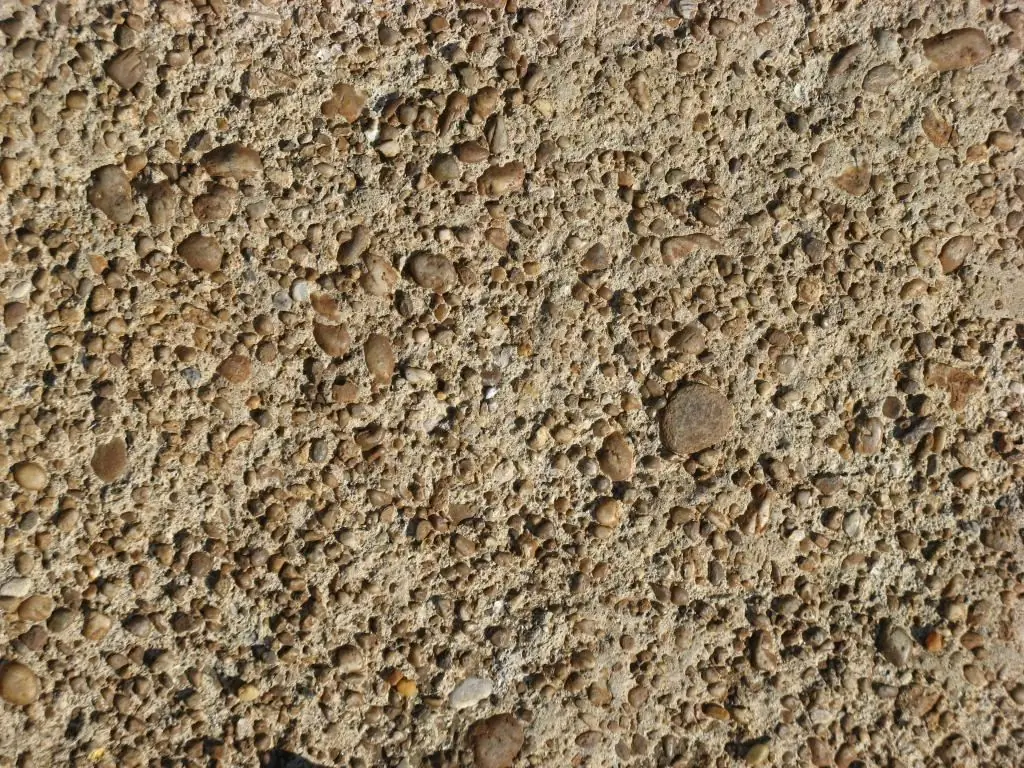
A little more about measurement
The surface roughness parameters are defined in the ISO 25178 series.values: Sa, Sq, Sz… Many optical measuring instruments are capable of measuring surface roughness by area. Area measurements are also possible with contact systems. Multiple, closely spaced 2D scans are taken from the target area. They are then digitally stitched together using the appropriate software, resulting in a 3D image and corresponding roughness parameters.
Soil surface
Soil surface roughness (SSR) refers to the vertical changes present in the micro- and macrotopography of the ground surface, as well as their stochastic distribution. There are four different SSR classes, each representing a characteristic vertical length scale:
- first class includes changes in microrelief from individual soil grains to aggregates of the order of 0.053-2.0 mm;
- second class consists of variations of soil clods from 2 to 100 mm;
- the third class of soil surface roughness is systematic elevation changes due to tillage, called oriented roughness (OS), ranging from 100 to 300 mm;
- fourth class includes planar curvature or macroscale topographic features.
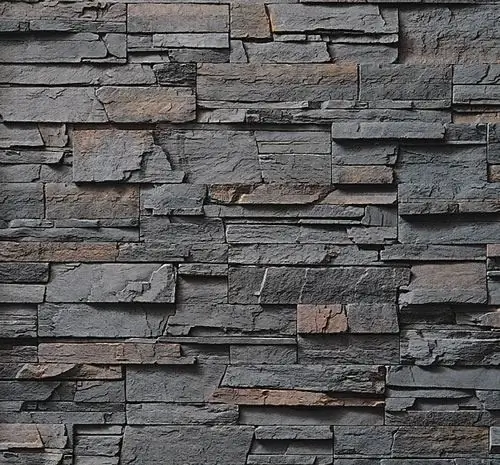
The first two classes explain the so-called micro-roughness, which has been shown to greatly influence the event and the seasonal scale depending on rainfall and tillage, respectively. Microroughness is most often determinedquantified by random roughness, which is essentially the standard deviation of layer surface elevation data around mean height after slope correction, using a plane of best fit and removing tillage effects in individual height readings. Precipitation exposure can lead to deterioration or increase in micro-roughness, depending on the initial conditions and soil properties.
On rough ground surfaces, the breakaway action of rain spray tends to smooth out the edges of the roughness of the soil surface, resulting in an overall reduction in RR. However, a recent study that examined the response of smooth soil surfaces to rainfall showed that RR can increase significantly at small initial microroughness scales of the order of 0-5 mm. It has also been shown that the increase or decrease is consistent across different SSR scores.
Mechanics
Surface structure plays a key role in controlling contact mechanics, that is, the mechanical behavior that occurs at the interface between two solid objects as they approach each other and go from non-contact to full contact. In particular, normal contact stiffness is determined predominantly by roughness structures (surface slope and fractality) and material properties.
From an engineering surface perspective, roughness is considered detrimental to part performance. As a consequence, most production prints set an upper limitroughness, but not bottom. The exception is cylinder bores where oil is retained in the surface profile and minimum surface roughness (Rz) is required.
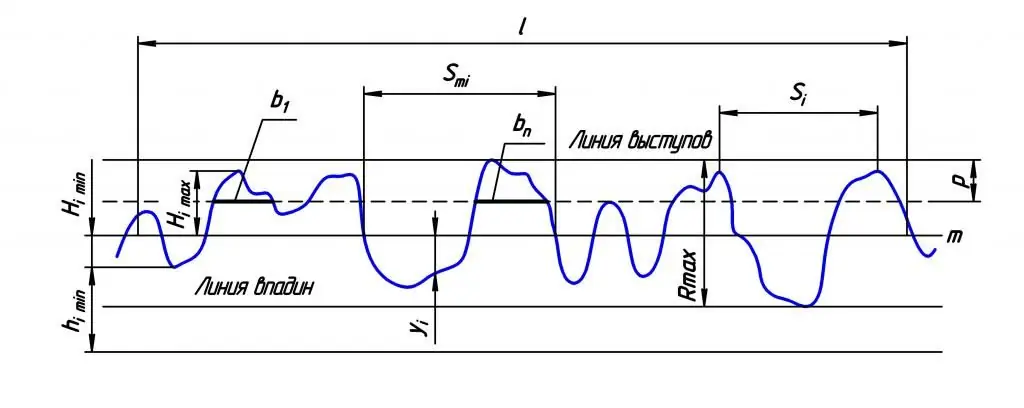
Structure and fractality
The structure of a surface is often closely related to its frictional and wear-resistant properties. A surface with a higher fractal dimension, a large value, or a positive value will usually have slightly higher friction and will wear out quickly. The peaks in the roughness profile are not always points of contact. Shape and waviness (that is, both amplitude and frequency) must also be considered, especially when processing surface roughness.