Almost every power transformer heats up during operation due to natural physical processes. With severe overheating, the insulation wears out, which leads to premature failure of the device. To reduce the negative impact of such a phenomenon, the magnetic circuit, windings and other parts should be cooled. For this, various transformer cooling systems are used.
The main difference between the latter is associated with the environment in which the equipment is located and the introduction of additional devices for temperature control. Please note that modern transformers use oil, water, air cooling. Dry devices should be sent to a separate category.
Markings and types of transformer cooling systems
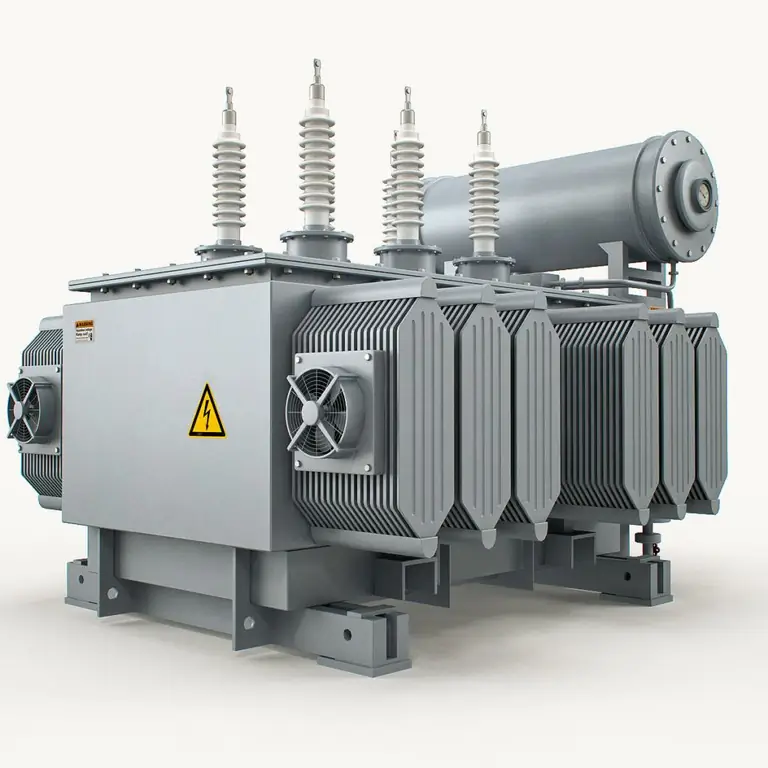
Determination of marking and type is carried out according to the state standard GOST 11677-75. It is registered herefull specification and gradation. Consider each group separately:
- C - dry-type transformers, which, due to their peculiarities, can use natural air cooling. Some variations are supplied with forced air circulation and are designated SD.
- M - power equipment with natural oil and air cooling. They are mainly used for distribution network with small transformer power. At large substations, there are variations with forced circulation of oil MTs, NMTs.
- D - equipment that has natural oil cooling and forced air. There are several variations of DC and NDC, depending on the additions in the form of circulation of technical fluid.
- Н - the presented type is less common, since non-combustible dielectrics are used for implementation. In most cases, these products are less prone to explosions, which ensures greater safety for people and the substation as a whole.
It should be noted that in modern practice there are foreign gradations in this direction. Almost all of the named transformer cooling systems are duplicated in the relevant standards.
Main advantages and disadvantages
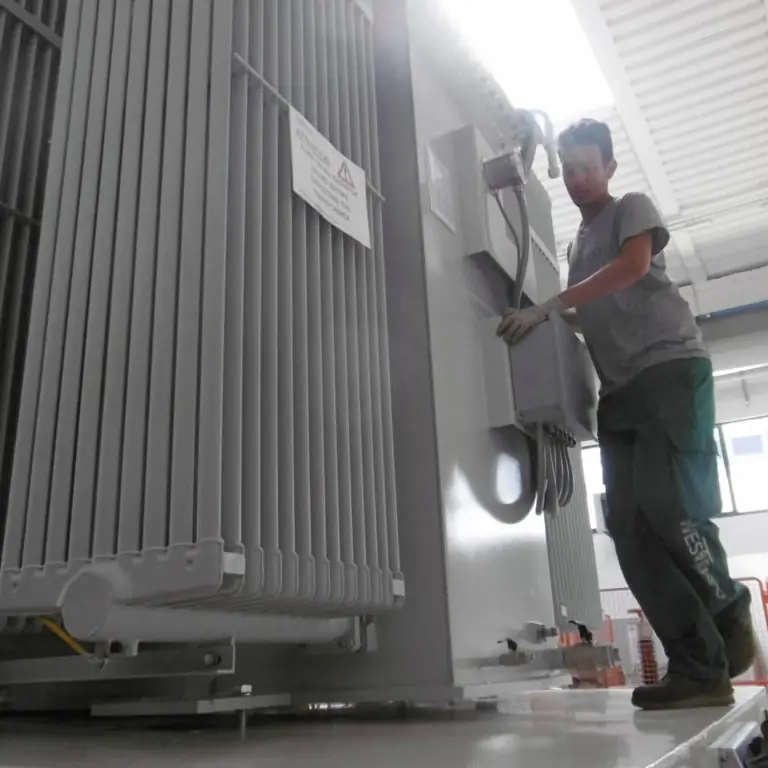
Practically each type is accompanied by a number of technical features, advantages and disadvantages. Next, we present the main criteria by which positive or negative positions are determined:
- Temperature level. The main purpose of cooling ismaintain a natural, favorable working environment for the equipment. The latter is largely determined by the installation environment, the load level of power plants.
- Cost of implementation. Almost every utility company wants to cut equipment costs, so they use old proven solutions in the form of oil cooling.
- Degree of security. This is an important criterion, which involves the use of a particular solution at different energy facilities. For nuclear power plants, it is preferable to use more modern and rational proposals that allow maintaining the desired temperature regime. When at a substation of a distribution network with small currents, an option of type C can be used.
Please note that power transformers with NMC, NDC cooling system are used in Russia, Belarus, Ukraine.
M type cooling

The presented type is considered the most common due to relative cheapness, extended service life and some other features. Oil-filled transformers with natural oil circulation and without additional airflow are used at distribution network substations. The cooling system of the M transformer has some operating nuances:
- The need to monitor the oil level and take gas to determine the condition of the equipment. Maintenance personnel must visit the distribution substation at least once every six months.
- The design must be airtight. Traces of smudges indicatethe need for technical or major repairs.
Theft of oil is considered a negative factor in operation. This is a common practice when there is a breakdown and drain of the technical fluid from the transformer tank. Due to barbaric actions, equipment overheats and shorts out, followed by burnout.
Cooling system for transformer D, DC
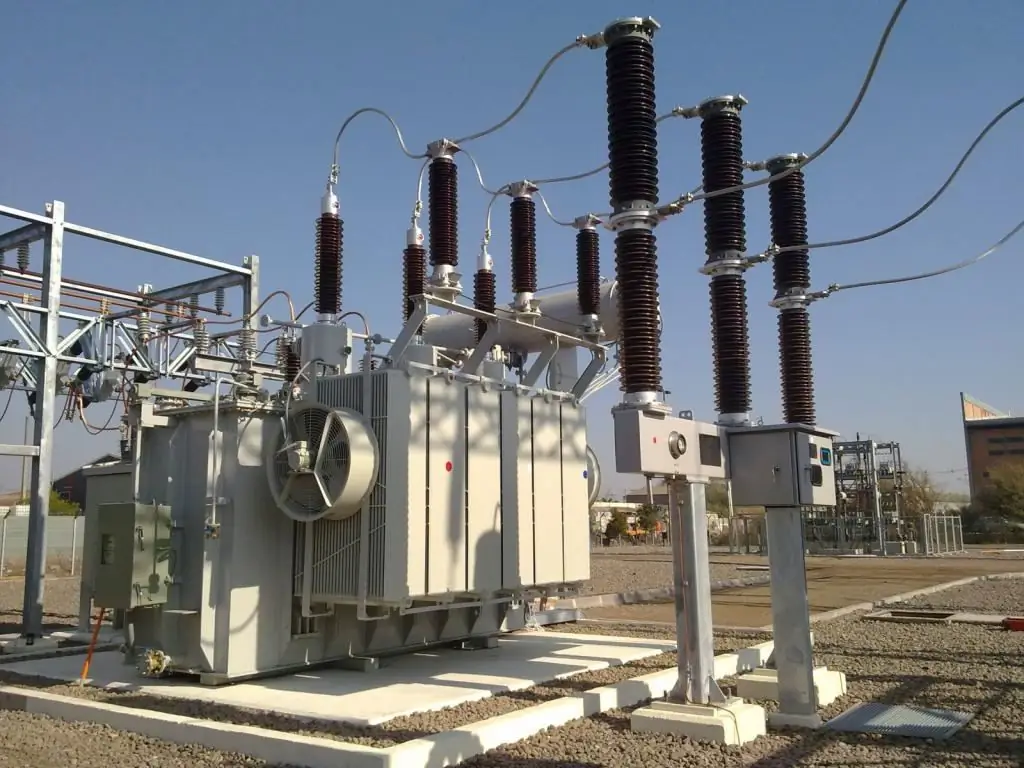
On large substations, natural oil circulation is supplemented by automatic blowing, which is triggered when the temperature rises. The DC transformer cooling system has a more perfect operation, as it avoids overheating even at high loads. It should be noted that this type is the most common and will be so for several decades. An important feature of operation is the need for proper regulation of airflow. The latter should turn on automatically when the temperature rises to 75 degrees, with a reverse shutdown when it drops.
H-type cooling
Type of transformer cooling system H is difficult to meet in modern operation. However, over time, their number will increase. As the main medium, distilled water with additives is used, which serves as a good dielectric and allows you to maintain the desired temperature. It should be noted that such a system is often combined with forced air type equipment.
As for the shortcomings - products are priced more expensive. This moment is also felt during operation, because to top up the liquid you will need to use a special solution that costs money. Otherwise, the presented option takes place in modern operation at various types of substations.
Cooling Options C, SG
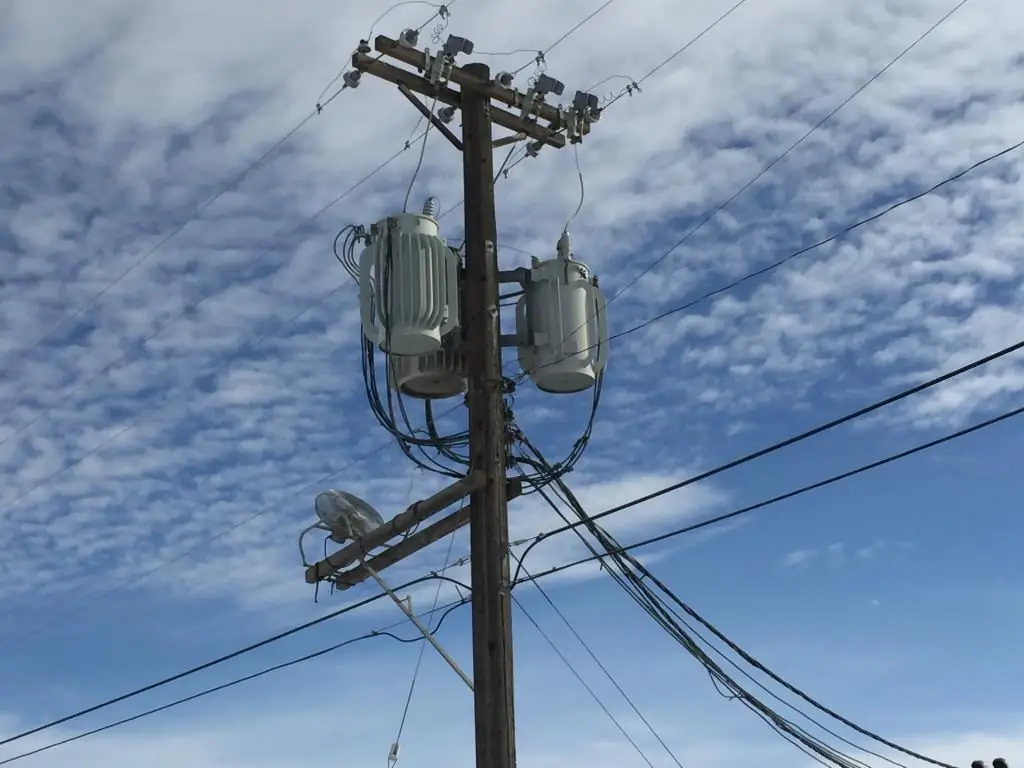
Unlike the oil-cooled transformers, the Type C variants do not use any liquid to correct the temperature. Temperature reduction is carried out by natural air circulation, which is acceptable in the following cases:
- Transformer up to 63kVA, which has a normal operating environment and light load.
- Power equipment used in low temperature environments.
- Temporary construction site where the duration of use of products is not important.
In other cases, it is recommended to focus on the solutions described above. This will extend the service life and save a lot of money.
Which option would you prefer?
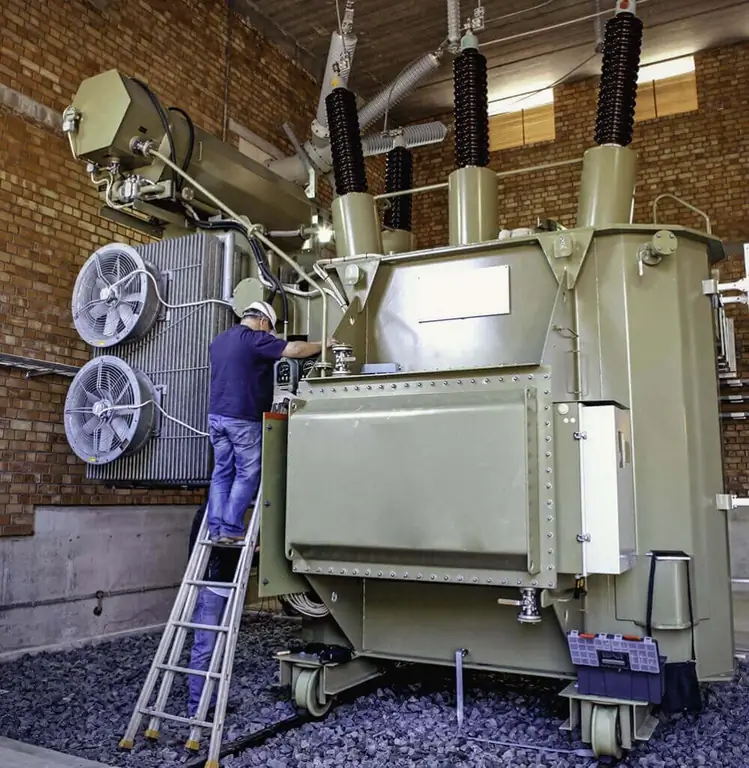
There is no single answer to this question, as there are many factors that determine the decision. As practice shows, in the modern market, transformers of the NDC and NMC types are used, which are accompanied by natural oil circulation and forced air supply. Such products are highly resistant to temperature changes, create a protective film that prolongs the life of the equipment.
At the same time, there are more advanced and safer technologies that help to avoid force majeure situations. For example, fires at substations, when all the equipment of the outdoor switchgear completely burns out. It is necessary to move forward towards technological progress, but also not to forget about the developments of the past years. After all, it will take a very long time to work with old equipment.
Conclusion
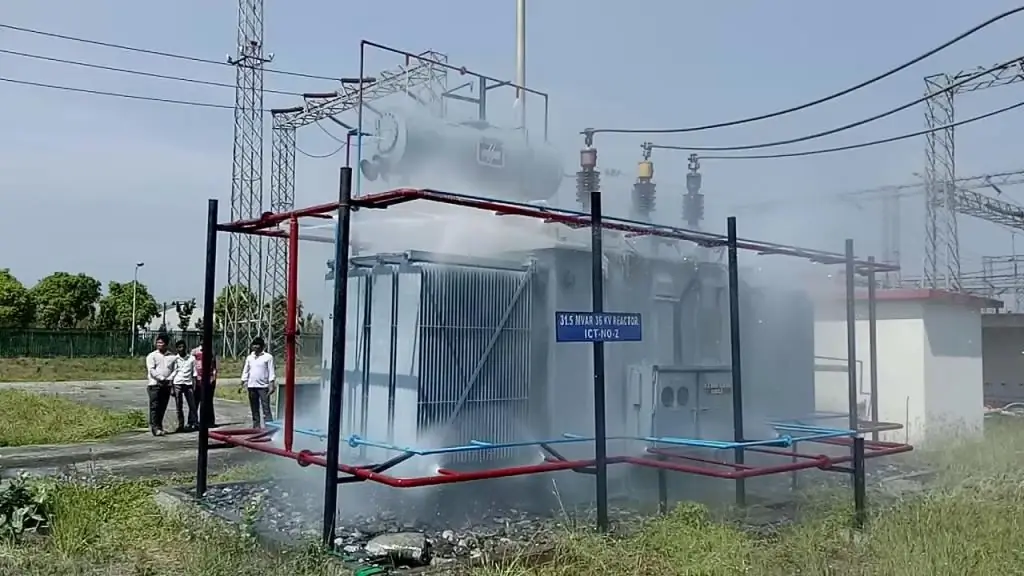
Power equipment of substations is in constant operation and heats up under the influence of physical phenomena. With an increase in workload, the temperature will increase and lead to burnout of the working elements. In order to extend the service life, various transformer cooling systems are used. In modern practice, options are used with air, oil and water methods for adjusting the medium.
The choice of cooling method is largely determined by a number of criteria, among which are the cost, the possibility of creating a support system, and environmental features. At substations 220/110/35/10, the NMC, NDC types are mainly used, which are considered combined.