Since all gases have several states of aggregation and can be liquefied, air, consisting of a mixture of gases, can also become a liquid. Basically, liquid air is produced to extract pure oxygen, nitrogen and argon from it.
A bit of history
Until the 19th century, scientists believed that gas has only one state of aggregation, but they learned how to bring air to a liquid state already at the beginning of the last century. This was done using a Linde machine, the main parts of which were a compressor (an electric motor equipped with a pump) and a heat exchanger, presented in the form of two tubes rolled into a spiral, one of which passed inside the other. The third component of the design was a thermos, and liquefied gas was collected inside it. Machine parts were covered with heat-insulating materials to prevent access to the heat gas from the outside. The inner tube located near the neck ended with a throttle.
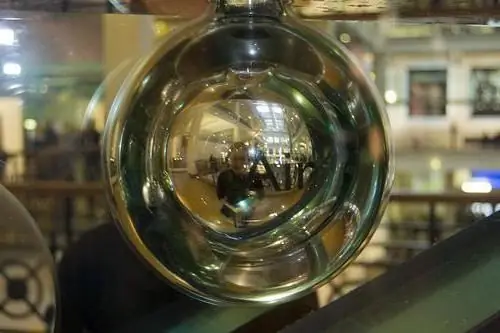
Gas work
The technology for obtaining liquefied air is quite simple. First, the mixture of gases is cleaned from dust, water particles, and also from carbon dioxide. There is another important component, without which it will not be possible to produce liquid air - pressure. With the help of a compressor, air is compressed up to 200-250 atmospheres,while cooling it with water. Next, the air goes through the first heat exchanger, after which it is divided into two streams, the larger of which goes to the expander. This term refers to a piston machine that works by expanding gas. It converts potential energy into mechanical energy and the gas cools because it does work.
Further, the air, having washed the two heat exchangers and thereby cooling the second flow going towards it, goes outside and collects in a thermos.
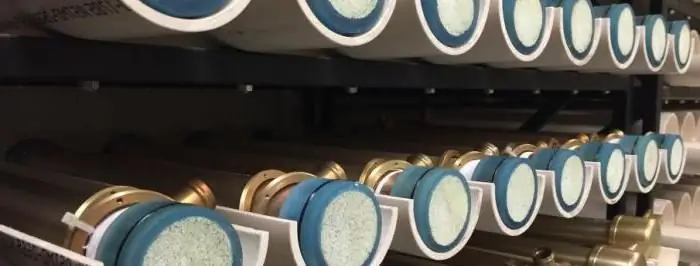
Turbo expander
Despite its apparent simplicity, the use of an expander is impossible on an industrial scale. The gas obtained by throttling through a thin tube turns out to be too expensive, its production is not efficient enough and energy-consuming, and therefore unacceptable for industry. At the beginning of the last century, there was a question of simplifying the smelting of iron, and for this a proposal was put forward to blow air from air with a high oxygen content. Thus, the question arose about the industrial production of the latter.
The piston expander quickly becomes clogged with water ice, so the air must be dried first, making the process more difficult and expensive. The development of a turboexpander using a turbine instead of a piston helped to solve the problem. Later, turboexpanders were used in the production of other gases.
Application
Liquid air itself is not used anywhere, it is an intermediate product in obtaining pure gases.
The principle of separation of constituents is based on the difference in boilingparts of the mixture: oxygen boils at -183 °, and nitrogen at -196 °. The temperature of liquid air is below two hundred degrees, and by heating it, separation can be carried out.
When liquid air begins to slowly evaporate, nitrogen is the first to evaporate, and after its main part has already evaporated, oxygen boils at a temperature of -183 °. The fact is that while nitrogen remains in the mixture, it cannot continue to heat up, even if additional heating is used, but as soon as most of the nitrogen has evaporated, the mixture will quickly reach the boiling temperature of the next part of the mixture, i.e. oxygen.
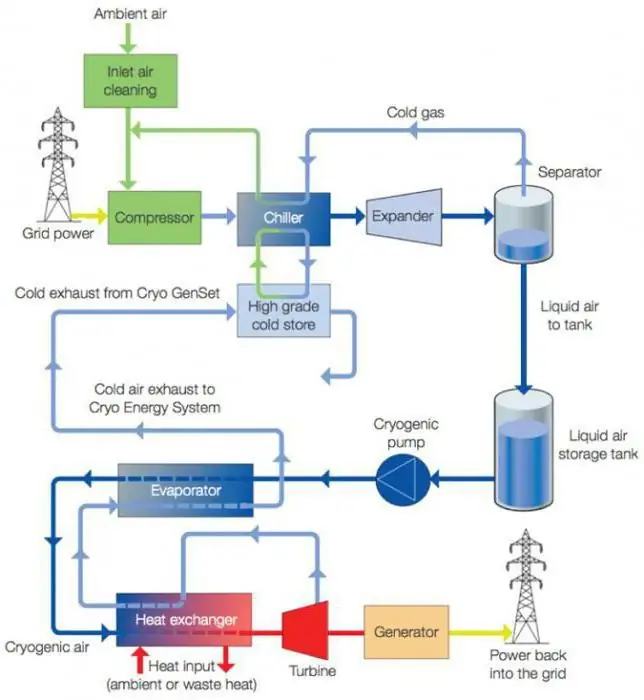
Purification
However, in this way it is impossible to obtain pure oxygen and nitrogen in one operation. Air in the liquid state at the first stage of distillation contains about 78% nitrogen and 21% oxygen, but the further the process goes and the less nitrogen remains in the liquid, the more oxygen will evaporate with it. When the nitrogen concentration in the liquid drops to 50%, the oxygen content in the vapor increases to 20%. Therefore, the evaporated gases are again condensed and distilled a second time. The more distillations were, the cleaner the resulting products will be.
In industry
Evaporation and condensation are two opposite processes. In the first case, the liquid must consume heat, and in the second case, heat will be released. If there is no heat loss, then the heat released and consumed during these processes is equal. Thus, the volume of condensed oxygen will be almost equal to the volumeevaporated nitrogen. This process is called rectification. The mixture of two gases, formed as a result of the evaporation of liquid air, is again passed through it, and some of the oxygen passes into the condensate, while giving off heat, due to which some of the nitrogen evaporates. The process is repeated many times.
Industrial production of nitrogen and oxygen takes place in the so-called distillation columns.
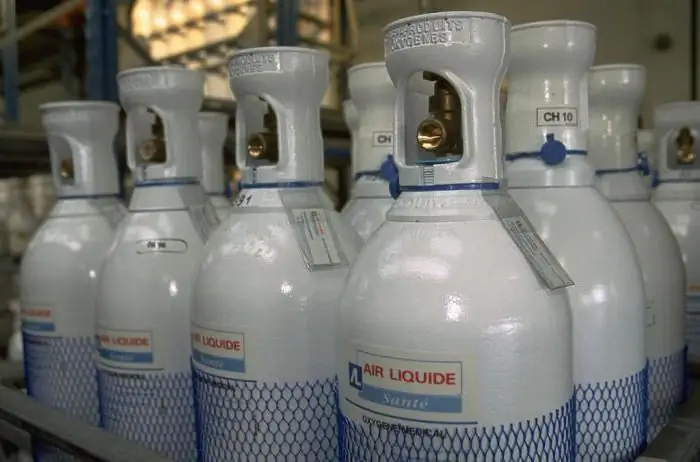
Interesting facts
When in contact with liquid oxygen, many materials become brittle. In addition, liquid oxygen is a very powerful oxidizing agent, therefore, once in it, organic substances burn out, releasing a lot of heat. When impregnated with liquid oxygen, some of these substances acquire uncontrolled explosive properties. This behavior is typical of petroleum products, which include conventional asph alt.