How often we hear the word "steel". And it is pronounced not only by professionals in the field of metallurgical production, but also by the townsfolk. No strong structure is complete without steel. In fact, when we talk about something metal, we mean a product made of steel. Let's find out what it consists of and how it is classified.
Definition
Steel is perhaps the most popular alloy, which is based on iron and carbon. Moreover, the share of the latter ranges from 0.1 to 2.14%, while the former cannot be lower than 45%. The ease of production and the availability of raw materials are of decisive importance in the distribution of this metal to all areas of human activity.
The main characteristics of the material vary depending on its chemical composition. The definition of steel as an alloy consisting of two components, iron and carbon, cannot be called complete. It may include, for example, chromium for heat resistance, and nickel for corrosion resistance.
Required componentsmaterials provide additional benefits. So, iron makes the alloy malleable and easily deformable under certain conditions, and carbon makes strength and hardness simultaneously with brittleness. That is why its share is so small in the total mass of steel. Determination of the method of production of the alloy led to the content of manganese in it in the amount of 1% and silicon - 0.4%. There are a number of impurities that appear during the melting of the metal and which they try to get rid of. Along with phosphorus and sulfur, oxygen and nitrogen also degrade the properties of the material, making it less durable and changing ductility.
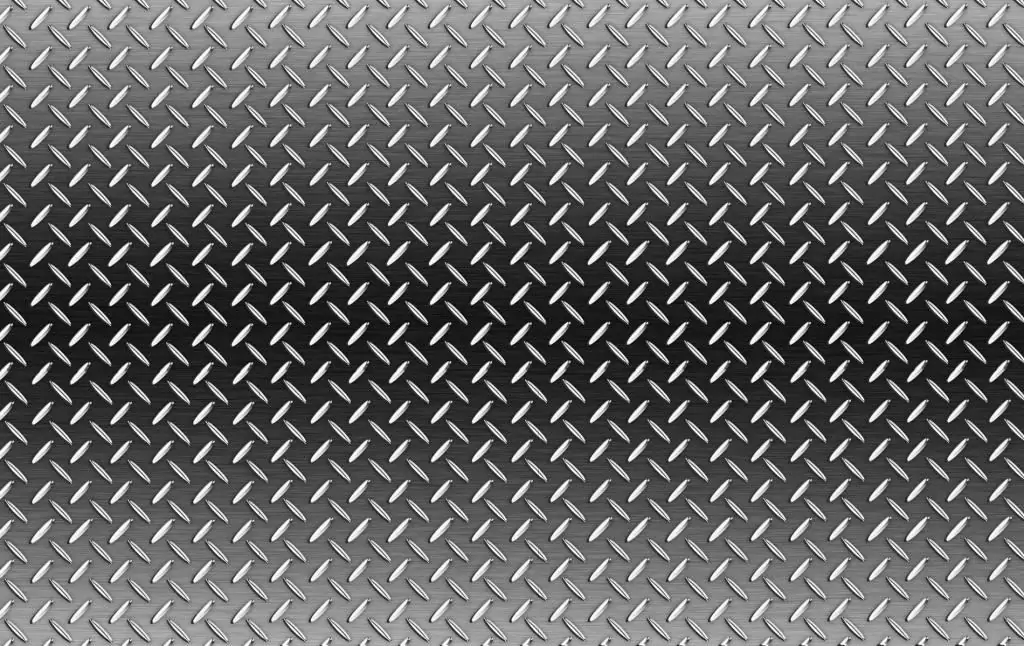
Classification
The definition of steel as a metal with a certain set of characteristics, of course, is beyond doubt. However, it is precisely its composition that makes it possible to classify the material in several directions. So, for example, metals are distinguished by the following features:
- on chemical;
- structural;
- by quality;
- as intended;
- according to the degree of deoxidation;
- by hardness;
- on steel weldability.
Steel definition, marking and all its characteristics will be described below.
Marking
Unfortunately, there is no global steel designation, which greatly complicates trade between countries. In Russia, an alphanumeric system is defined. The letters indicate the name of the elements and the method of deoxidation, and the numbers indicate their number.
Chemical composition
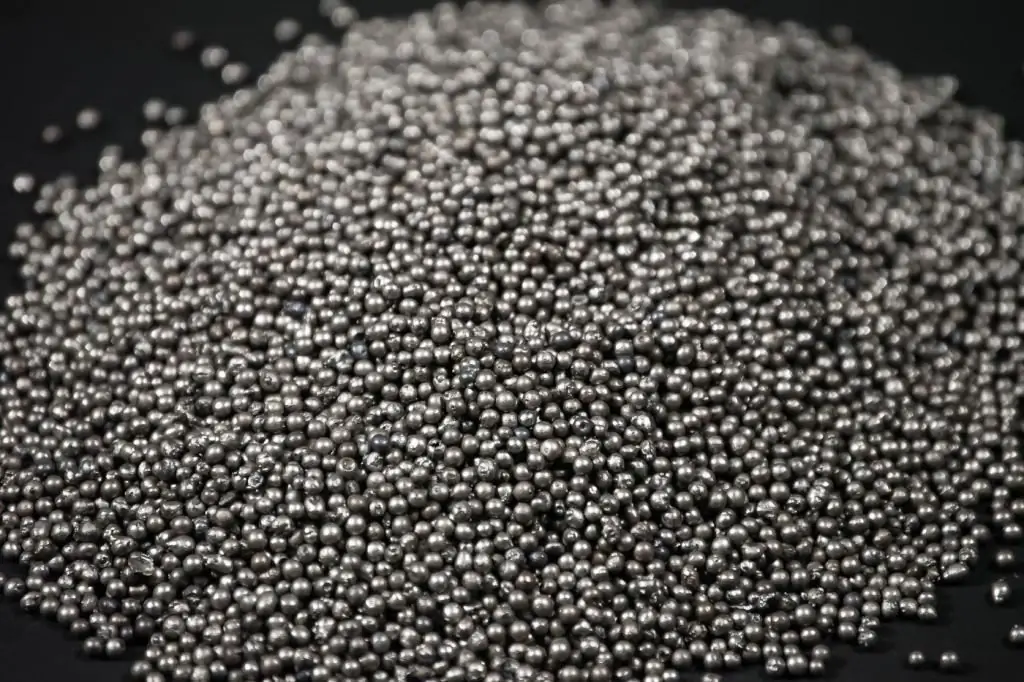
There are two waysdivision of steel by chemical composition. The definition given by modern textbooks makes it possible to distinguish between carbon and alloyed material.
The first attribute defines steel as low-carbon, medium-carbon and high-carbon, and the second - low-alloy, medium-alloy and high-alloy. Low-carbon metal is called, which, according to GOST 3080-2005, may include, in addition to iron, the following components:
- Carbon - up to 0.2%. It promotes thermal strengthening, due to which the tensile strength and hardness are doubled.
- Manganese in an amount of up to 0.8% actively enters into a chemical bond with oxygen and prevents the formation of iron oxide. The metal is better able to withstand dynamic loads and is more amenable to thermal hardening.
- Silicon - up to 0.35%. It improves mechanical properties such as toughness, strength, weldability.
According to GOST, the definition of steel as low-carbon steel is given to a metal that contains, in addition to useful, a number of harmful impurities in the following quantity. This is:
- Phosphorus - up to 0.08% is responsible for the appearance of cold brittleness, impairs endurance and strength. Reduces the toughness of the metal.
- Sulfur - up to 0.06%. It complicates the processing of metal by pressure, increases temper brittleness.
- Nitrogen. Reduces the technological and strength properties of the alloy.
- Oxygen. Reduces strength and interferes with cutting tools.
It should be noted that low orlow-carbon steels are particularly soft and ductile. They deform well both hot and cold.
The definition of medium carbon steel as well as its composition is of course different from the material described above. And the biggest difference is the amount of carbon, which ranges from 0.2 to 0.45%. Such a metal has low toughness and ductility along with excellent strength properties. Medium carbon steel is commonly used for parts that are used under normal power loads.
If the carbon content is over 0.5%, then such steel is called high-carbon steel. It has increased hardness, reduced viscosity, ductility, and is used for stamping tools and parts by hot and cold deformation.
In addition to identifying the carbon present in the steel, the determination of the characteristics of the material is possible through the presence of additional impurities in it. If, in addition to ordinary elements, chromium, nickel, copper, vanadium, titanium, nitrogen in a chemically bound state are purposefully introduced into the metal, then it is called doped. Such additives reduce the risk of brittle fracture, increase corrosion resistance and strength. Their number indicates the degree of alloying of steel:
- low-alloyed - has up to 2.5% alloying additives;
- medium alloyed - from 2.5 to 10%;
- highly alloyed - up to 50%.
What does this mean? For example, the increase of any properties began to be provided as follows:
- Adding chromium. positiveaffects the mechanical characteristics already in the amount of 2% of the total.
- The introduction of nickel from 1 to 5% increases the temperature margin of viscosity. And reduces cold brittleness.
- Manganese works in the same way as nickel, although much cheaper. However, it helps to increase the sensitivity of the metal to overheating.
- Tungsten is a carbide-forming additive that provides high hardness. Because it prevents grain growth when heated.
- Molybdenum is an expensive additive. Which increases the heat resistance of high speed steels.
- Silicon. Increases acid resistance, elasticity, scale resistance.
- Titanium. May promote fine grain structure when combined with chromium and manganese.
- Copper. Increases anti-corrosion properties.
- Aluminum. Increases heat resistance, scaling, toughness.
Structure
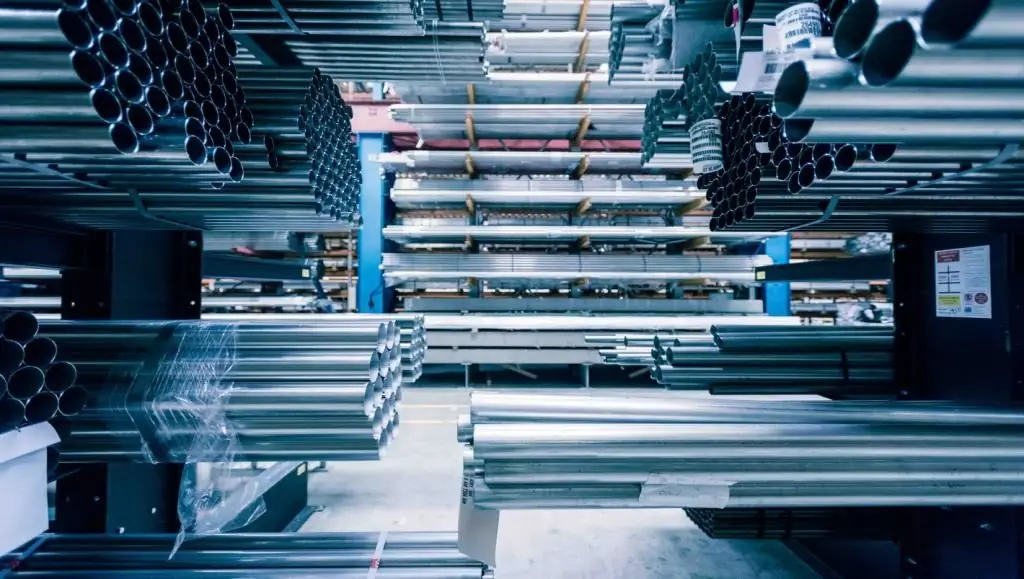
Determining the composition of steel would be incomplete without studying its structure. However, this sign is not constant, and may depend on a number of factors, such as: heat treatment mode, cooling rate, degree of alloying. According to the rules, the steel structure should be determined after annealing or normalization. After annealing, the metal is divided into:
- pro-eutectoid structure - with excess ferrite;
- eutectoid, which consists of perlite;
- hypereutectoid - with secondary carbides;
- ledeburite - with primary carbides;
- austenitic - with a face-centered crystal lattice;
- ferritic - with a cubic body-centered lattice.
Determining the steel class is possible after normalization. It is understood as a type of heat treatment, which includes heating, holding and subsequent cooling. Here, pearlite, austenitic and ferritic grades are distinguished.
Quality
Determining types has become possible in terms of quality in four ways. This is:
- Ordinary quality - these are steels with a carbon content of up to 0.6%, which are smelted in open-hearth furnaces or in converters using oxygen. They are considered the cheapest and are inferior in characteristics to metals of other groups. An example of such steels are St0, St3sp, St5kp.
- Quality. Prominent representatives of this type are steels St08kp, St10ps, St20. They are smelted using the same furnaces, but with higher requirements for the charge and production processes.
- High-quality steels are melted in electric furnaces, which guarantees an increase in the purity of the material for non-metallic inclusions, that is, an improvement in mechanical properties. These materials include St20A, St15X2MA.
- Especially high-quality - are made according to the method of special metallurgy. They are subjected to electroslag remelting, which provides purification from sulfides and oxides. Steels of this type include St18KhG-Sh, St20KhGNTR-Sh.
Structural steels
This is perhaps the most simple and understandable sign for the layman. There are structural, tool and special-purpose steels. Structural is usually divided into:
- Construction steels are carbon steels of ordinary quality and representatives of the low-alloy series. They are subject to several requirements, the main of which is weldability at a sufficiently high level. An example is StS255, StS345T, StS390K, StS440D.
- Cemented materials are used to make products that operate under surface wear conditions and simultaneously experience dynamic loads. These include low-carbon steels St15, St20, St25 and some alloyed ones: St15Kh, St20Kh, St15KhF, St20KhN, St12KhNZA, St18Kh2N4VA, St18Kh2N4MA, St18KhGT, St20KhGR, St30KhGT.
- For cold stamping, rolled leaves from high-quality low-carbon samples are used. Such as St08Yu, St08ps, St08kp.
- Treatable steels that are improved through the quenching and high tempering process. These are medium-carbon (St35, St40, St45, St50), chromium (St40X, St45X, St50X, St30XRA, St40XR) steels, as well as chromium-silicon-manganese, chromium-nickel-molybdenum and chromium-nickel.
- Spring springs have elastic properties and retain them for a long time, as they have a high degree of resistance to fatigue and destruction. These are carbon representatives of St65, St70 and alloyed steels (St60S2, St50KhGS, St60S2KhFA, St55KhGR).
- High-strength samples are those that have twice the strength of other structural steels, achieved by heat treatment and chemical composition. In the bulk, these are alloyed medium-carbon steels, for example, St30KhGSN2A, St40KhN2MA, St30KhGSA, St38KhN3MA, StOZN18K9M5T, St04KHIN9M2D2TYu.
- Ball bearingsteels are characterized by special endurance, a high degree of wear resistance and strength. They are required to meet the requirements for the absence of various kinds of inclusions. These samples include high-carbon steels with a chromium content in the composition (StSHKh9, StSHKh15).
- Automatic steel definitions are as follows. These are samples for use in the manufacture of non-critical products such as bolts, nuts, screws. Such spare parts are usually machined. Therefore, the main task is to increase the machinability of parts, which is achieved by introducing tellurium, selenium, sulfur and lead into the material. Such additives contribute to the formation of brittle and short chips during machining and reduce friction. The main representatives of automatic steels are designated as follows: StA12, StA20, StA30, StAS11, StAS40.
- Corrosion-resistant steels are alloy steels with a chromium content of about 12%, since it forms an oxide film on the surface that prevents corrosion. Representatives of these alloys are St12X13, St20X17N2, St20X13, St30X13, St95X18, St15X28, St12X18NYUT,
- Wear-resistant samples are used in products that operate under abrasive friction, shock and strong pressure. An example is the parts of railway tracks, crushers and caterpillar machines, such as St110G13L.
- Heat-resistant steels can work at high heat. They are used in the manufacture of pipes, gas and steam turbine spare parts. These are mainly high-alloyed low-carbon samples, which necessarily contain nickel, which may contain additives in the formmolybdenum, nobium, titanium, tungsten, boron. An example would be St15XM, St25X2M1F, St20XZMVF, St40HUS2M, St12X18N9T, StXN62MVKYU.
- Heat-resistant are particularly resistant to chemical damage in air, gas and furnace, oxidizing and carburizing environments, but show creep under severe loads. Representatives of this type are St15X5, St15X6SM, St40X9S2, St20X20H14S2.
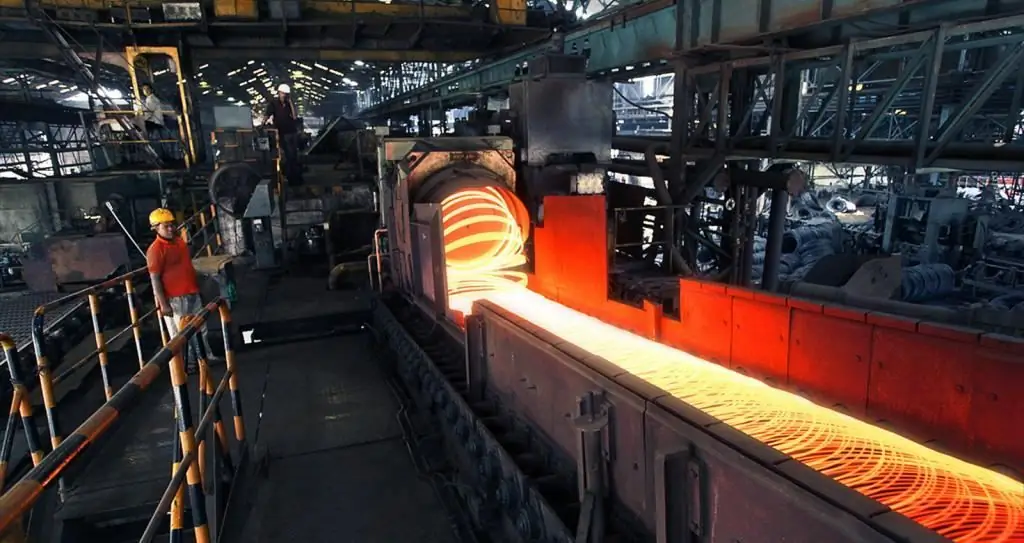
Tool steels
In this group, alloys are divided into die, for cutting and measuring tools. There are two types of die steels.
- The material for cold forming should have a high degree of hardness, strength, wear resistance, heat resistance. But have sufficient viscosity (StX12F1, StX12M, StX6VF, St6X5VMFS).
- The hot forming material has good strength and toughness. Along with wear resistance and scale resistance (St5KhNM, St5KhNV, St4KhZVMF, St4Kh5V2FS).
Measuring tool steels, in addition to wear resistance and hardness, must be dimensionally stable and easy to grind. Calibers, staples, templates, rulers, scales, tiles are made from these alloys. An example would be alloys StU8, St12Kh1, StKhVG, StKh12F1.
Determining steel groups for cutting tools is fairly easy. Such alloys must have cutting ability and high hardness for a long time, even when subjected to heat. These include carbon and alloy tool, as well ashigh speed steels. Here you can name the following prominent representatives: StU7, StU13A, St9XS, StKhVG, StR6M5, Stryuk5F5.
Deoxidation of the alloy
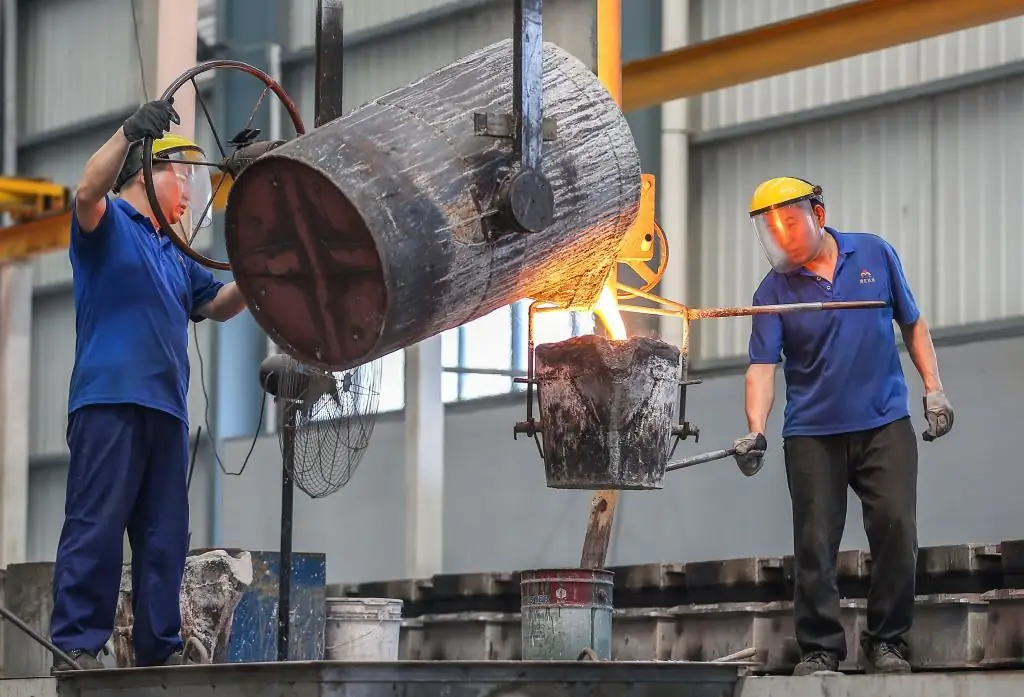
Determination of steel by the degree of deoxidation implies its three types: calm, semi-calm and boiling. The very concept refers to the removal of oxygen from the liquid alloy.
Quiet steel almost does not emit gases during solidification. This is due to the complete removal of oxygen and the formation of a shrinkage cavity on top of the ingot, which is then cut off.
In semi-calm steel, gases are partially released, that is, more than in calm steel, but less than in boiling ones. There is no shell here, as in the previous case, but bubbles form at the top.
Boiling alloys release a large amount of gas when solidified, and in cross-section it is enough to simply notice the difference in chemical composition between the upper and lower layers.
Hardness
This concept refers to the ability of a material to resist harder penetrating into it. Hardness determination became possible using three methods: L. Brinell, M. Rockwell, O. Vickers.
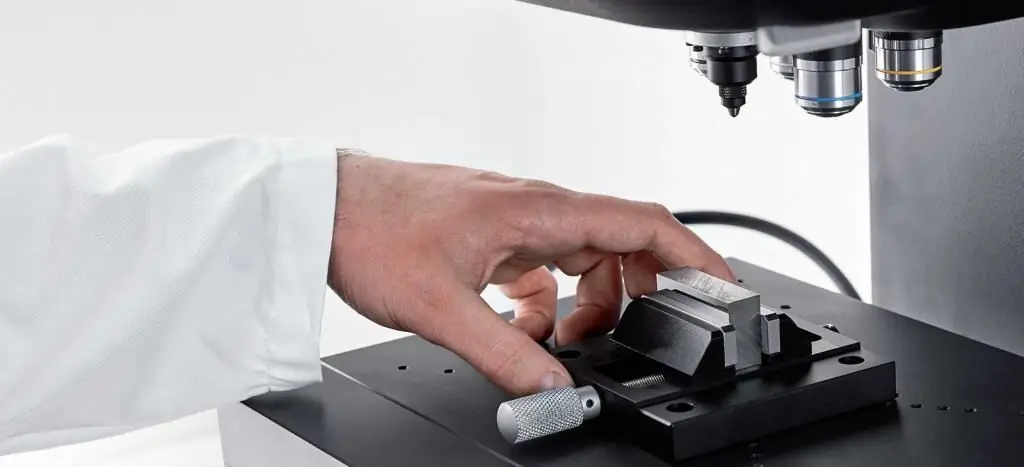
According to the Brinell method, a hardened steel ball is pressed into the ground surface of the sample. By studying the diameter of the print, determine the hardness.
Method for determining the hardness of steel according to Rockwell. It is based on calculating the penetration depth of a 120 degree diamond cone tip.
According to Vickers in the test samplea diamond tetrahedral pyramid is pressed in. With an angle of 136 degrees on opposite faces.
Is it possible to determine the grade of steel without chemical analysis? Specialists in the field of metallurgy are able to recognize the grade of steel by a spark. The determination of the constituents of the metal is possible during its processing. So for example:
- CVG steel has dark crimson sparks with yellow-red dots and tufts. At the ends of the branched threads, bright red stars appear with yellow grains in the middle.
- P18 steel is also identified by dark crimson sparks with yellow and red tufts at the beginning, however, the threads are straight and do not have forks. At the ends of the bundles there are sparks with one or two light yellow grains.
- Steel grades ХГ, Х, ШХ15, ШХ9 have yellow sparks with light stars. And red grains on the branches.
- U12F steel is distinguished by light yellow sparks with dense and large stars. With several red and yellow tufts.
- Steels 15 and 20 have light yellow sparks, many forks and stars. But few tufts.
Determination of steel by a spark is a fairly accurate method for specialists. However, ordinary people cannot characterize the metal by examining only the color of the spark.
Weldability
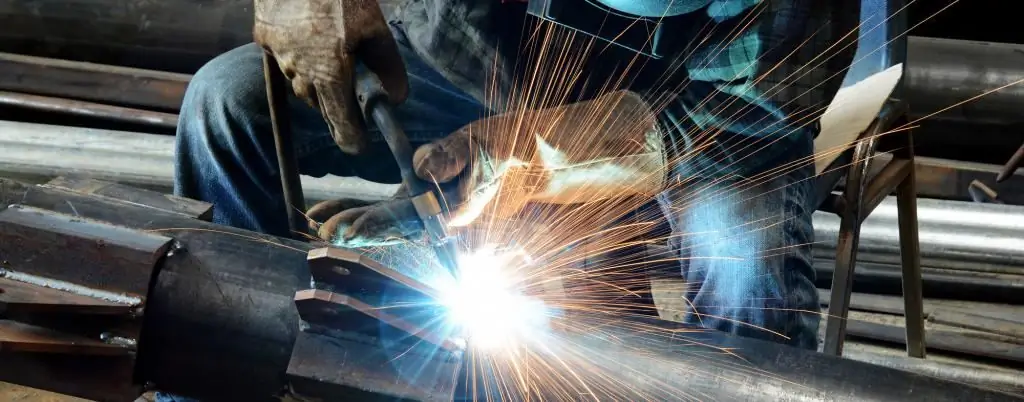
The property of metals to form a joint under a certain impact is called the weldability of steels. The determination of this indicator is possible after the content of iron and carbon is detected.
It is believed that they are well connected by weldinglow carbon steels. When the carbon content exceeds 0.45%, the weldability deteriorates and becomes worse when the carbon content is high. This also happens because the inhomogeneity of the material increases, and sulfide inclusions stand out at the grain boundaries, which lead to the formation of cracks and an increase in internal stress.
Alloying components also act, worsening the connection. The most unfavorable for welding are such chemical elements as chromium, molybdenum, manganese, silicon, vanadium, phosphorus.
However, compliance with the technology when working with low-alloy steels provides a good percentage of weldability without the use of special measures. Determination of weldability is possible after evaluating a number of important material qualities, including:
- Cooling speed.
- Chemical composition.
- View of primary crystallization and structural changes during welding.
- The ability of metal to form cracks.
- Tendency of material to form hardening.