Alkyd resins occupy one of the leading positions as a raw material for the production of modern paints and varnishes. Film-forming compositions based on them have a wide range of applications. Coating properties depend on the type of resins and semi-finished varnishes. The most widespread are modified compositions, as they have high decorative and protective qualities.
Description
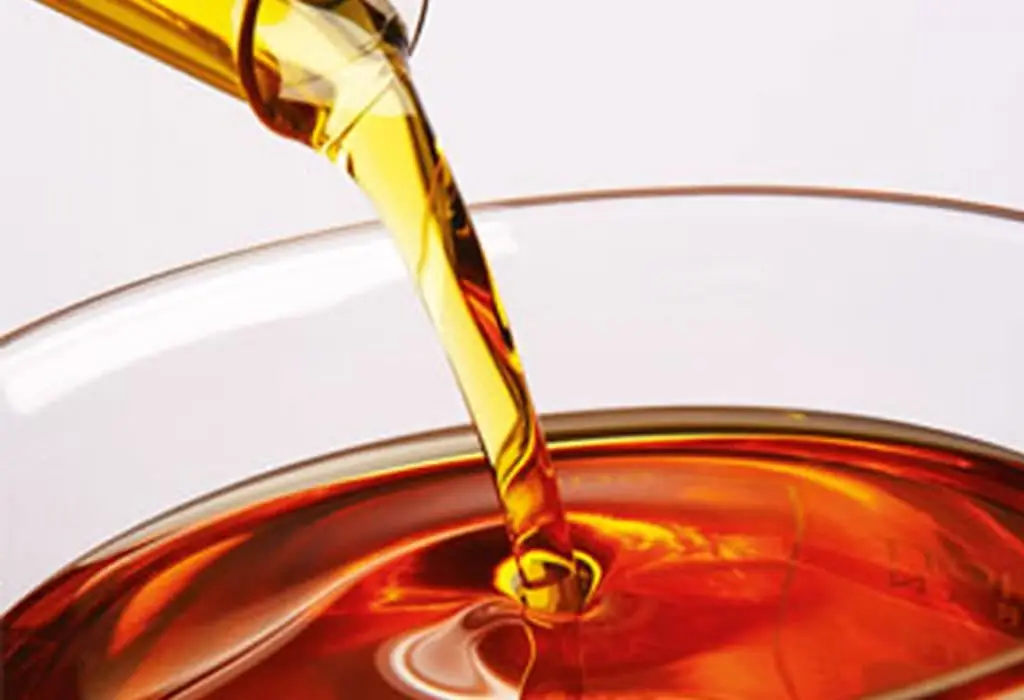
Alkyd resins (or alkyds) are esters resulting from the reaction of polyhydric alcohols with polybasic acids or their anhydrides. In appearance, they are a highly viscous sticky mass, the color of which is from dark yellow to brown.
Alkyds are also combined with other resins and cellulose (alkyd-urea-formaldehyde, phenol-alkyd, alkyd-acrylic copolymers and other compounds). To reduce surface tension, butyl alcohol is added to their composition, which makes it easier to pour the finished product.
Chemical composition and classification
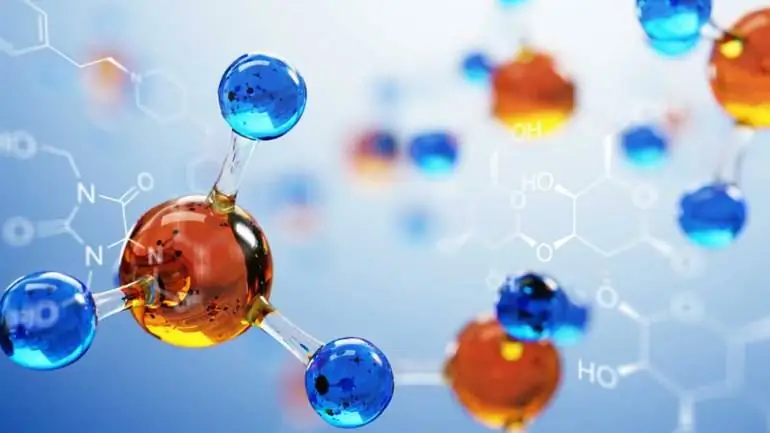
Alkyd resins are systematized according to several criteria:
-
By the presence of fatty acids in the composition: unmodified (phthalate) and modified.
- By oil content: fatty (>60%), medium fat (40-60%), lean (35-60%), extra-lean (<34%). Fatty alkyds are mainly prepared with drying oils.
- According to the type of alcohol on the basis of which the composition is obtained: glyphthalic, xyphthalic, pentaphthalic, etrifthalic.
- By drying ability: drying and non-drying.
- According to the method of dissolution: diluted with organic solvents or water.
The chemical composition of alkyd resin is a 40-60% solution of non-volatile substances in organic solvents.
Features
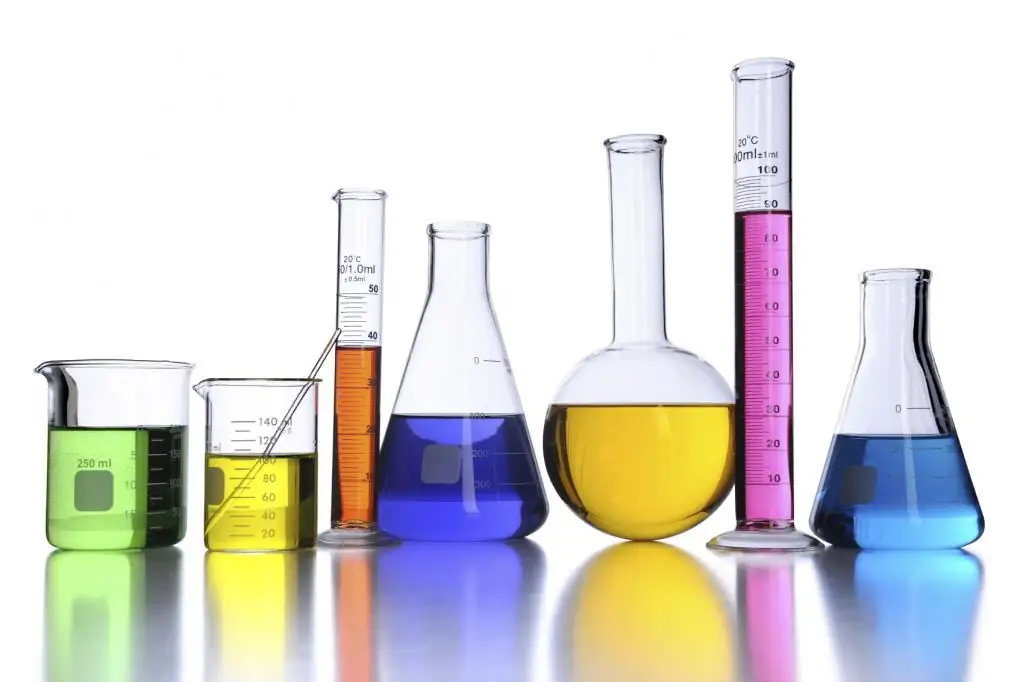
The properties of alkyds depend on the type of polyhydric alcohol, its concentration and the presence of other components. Aromatic components give coatings based on these compounds hardness and wear resistance, aliphatic polyols - elasticity, cycloaliphatic structural units - a balance of characteristics.
Alkyd resin solutions are characterized by the following parameters:
- viscosity - 35-100 s (according to VZ-4 viscometer);
- molecular weight - 1500-5000 kDa;
- density - 0.9-1.05 g/cm3;
- the amount of potassium hydroxide, which is the main indicator of the quality of oils, is not more than 20.
As the temperature increases, the viscosity of alkyds decreases and vice versa. The lower the fat content of a substance, the worse it dissolves in aliphatic and naphthenic hydrocarbons.
Improve properties
Unmodified alkyds form hard and brittle films, dissolve poorly. To improve their qualities, additional components are introduced into the composition of the reaction mixture, which give the coatings gloss, elasticity, resistance to water, solvents, oils and weathering, accelerate drying at room temperature, and increase adhesion with the base material. Modified alkyd resins are obtained using linseed, tall oil, tung oil, sunflower oil, castor oil, cottonseed oil, rosin, synthetic fatty acids.
There are 3 main modification methods:
- introduction of monomers in resin production;
- by reacting finished alkyds with modifying agents;
- mixing resins with other film formers.
Receive
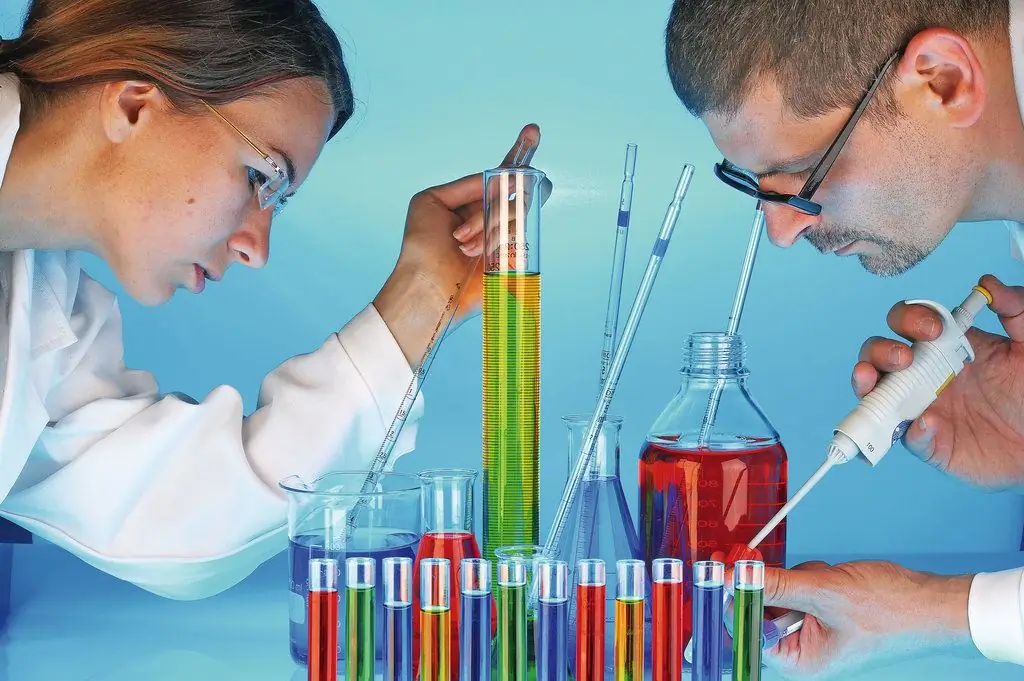
Alkyds are synthesized in two ways: alcoholysis and fatty acid method.
In the first case, the process takes place in 3 stages:
- Transesterification of vegetable oil or triglycerides of its fatty acids with polyhydric alcohols. The chemical reaction takes place at a temperature of 240-260 °C and in the presence of a catalyst. For the production of glyphthalic resins from alcohols, glycerin is used, for etrifthalic resins - etriol, for pentaphthalic resins - pentaerythritol.
- Esterification of partial esters with phthalic anhydride, resulting in an acidic ester.
-
Polyesterification with water release and alkyd formation.
The second method for producing resins is esterification and polyesterification of fatty acid esters and polyhydric alcohols.
Alkyd thinners
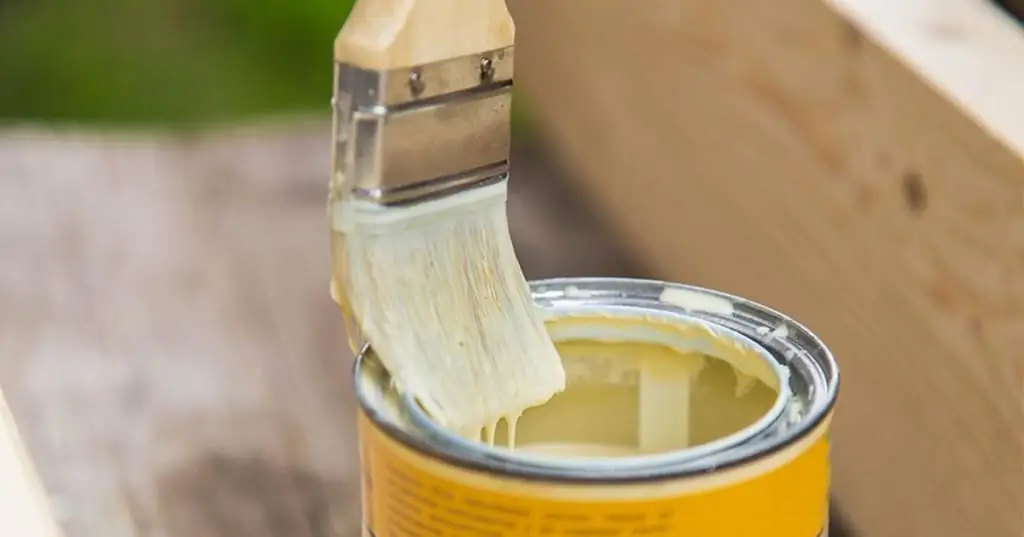
The following carbon compounds serve as solvents for alkyd resins:
- aliphatic (hexane, heptane, C6-C12 paraffins);
- aromatic (benzene, solvent, toluene, xylene and others);
- terpene (turpentine);
- halogenated (trichlorethylene, tetrachlorethylene, perchlorethylene);
- oil (nefras, gasoline).
Low boiling ethers (ethyl alcohol, ethyl acetate), glycol ethers, ketones (acetone) can also be used as diluents. Butanol is unsuitable for these purposes, since its molecules attract to themselves a large amount of the solvent contained in alkyd resins. Lean alkyds dissolve only in aromatic hydrocarbons, while fatty alkyds dissolve in aliphatic ones.
There are also water-soluble resins, on the basis of which water-borne coatings are produced (hot-drying enamels and primers).
Application
The main purpose of alkyd resins is the production of paints and varnishes (LKM). Unmodified compounds are used for the manufacture of electrical insulating varnishes and adhesives.
Fromresin solutions make semi-finished and finished varnishes used in industry and everyday life.
Paint materials

Alkyd coatings are the most widely used of all materials based on polycondensation resins. Since pentaerythritol alcohol has 4 hydroxyl groups, alkyds containing pentaerythritol cure faster and produce glossier coatings. In this regard, the industry mainly produces paintwork materials based on alkyd resins of the pentaphthalic type. The use of a large number of aromatic components ensures the hardness and resistance of coatings to mechanical stress.
Pigmented coatings based on alkyds are divided into the following groups:
- glyphthalic (GF), pentaphthalic (EF), etrifthalic (ET) enamels;
- soils;
- putty.
Drying alkyd resins are used as independent film formers for paints and varnishes, and non-drying ones are used in formulations with carbamide resins, cellulose nitrates (to improve elasticity and adhesion of coatings to the base material).
Properties of coatings depend on their chemical composition. Thus, fatter alkyd resins in organic solvents are easier to apply with a brush, have increased elasticity and weather resistance, but dry more slowly and are less resistant to mineral oils. The maximum drying rate is typical for resins modified with tung or linseed.oil. The average dry-to-tack time for alkyd enamels is 24 hours.
Specific paintwork
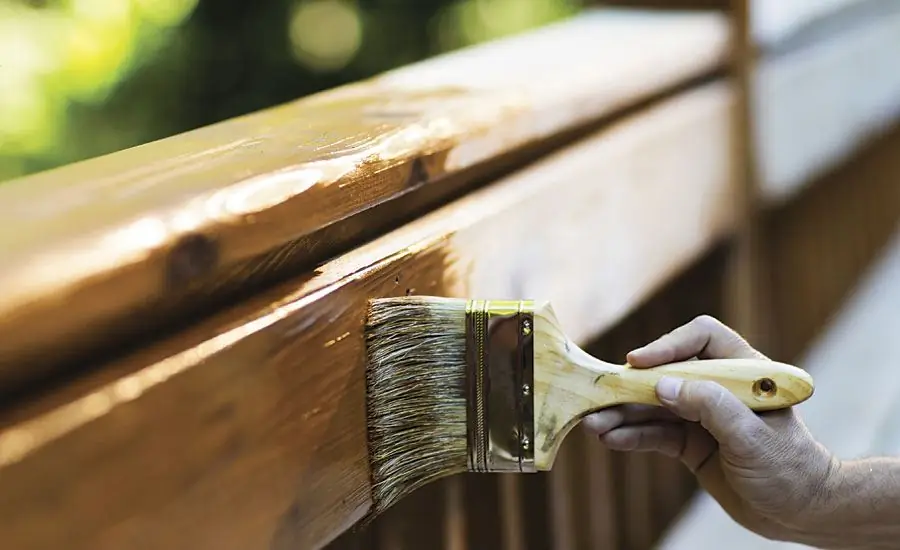
Alkyd resins, depending on the component composition, are used for the following purposes:
- Based on benzoic acid (oil content 38-50% by weight) - enamels for painting agricultural machines, radiators, car repairs. Highly fade and weather resistant.
- Containing 9,12-linoleic and 9,11-linoleic acids - equipment repair.
- Skinny - quick dry single coats, primers, radiator paint.
- Based on linseed oil and glycerin - anti-corrosion coatings, printing inks. Can fade quickly when exposed to sunlight, so they are most often used in primers and leveling compounds.
- Soybean or tall oil based top coats with good weather resistance.
- Modified with natural resins (rosin acids) - production of primers and putties. Compounds are prone to fading.
- Modified with styrene, acrylate - primers, putties, leveling compounds, coatings for painting ships, equipment, sheet metal, wood subjected to strong mechanical stress (parquet varnishes, floor enamels, furniture); packaging of enamels in tubes. They have increased resistance to abrasion and elasticity.
Environmental aspects
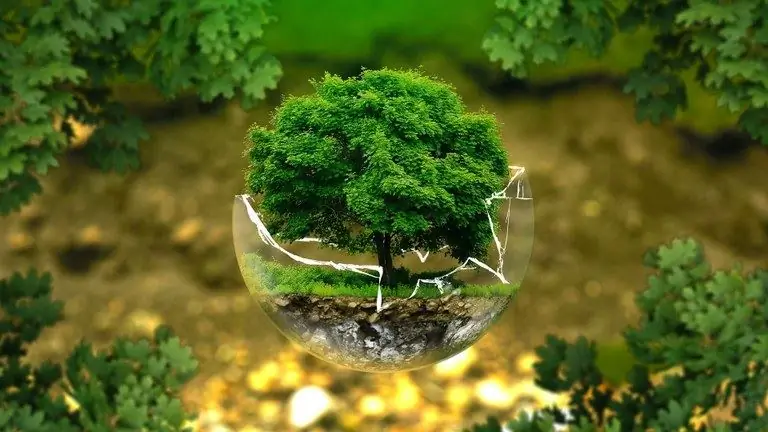
Since alkyd resins contain organic solvents, they pose a certain danger to human he alth and the environment. When carrying out paint and varnish work using paintwork materials based on them, it is necessary to use personal protective equipment (gas masks, overalls). Painting should be done in rooms with supply and exhaust ventilation.
According to the level of toxicity of solvents, alkyds can be divided into 3 groups:
- the least toxic (MPC=300-1000 mg/m3) - ethyl ether, alcohol, gasoline;
- medium toxicity (MPC=100-200 mg/m3) - acetone, butyl ether;
- highly toxic (MPC=20-50 mg/m3) - ethylene glycol, benzene.
Abroad, there are high requirements for the environmental friendliness of the production of coatings, therefore, work is currently underway to create materials with a high content of dry matter and water-borne compositions. However, alkyd resins with organic solvents still outperform water-soluble resins in processing properties.