Scientific organization of labor is a process of improving enterprises and organizations based on the implementation of the results of scientific and engineering research that relate to the activities of an employee as a subject of the labor process (abbreviated abbreviation - "NOT"). NOT is a term actively used on the territory of the USSR and the former Soviet republics. Abroad, in particular in the countries of Western Europe, the term SOP has become more common - the scientific organization of production. Given the identity of both terms, it would be correct to speak of the scientific organization of labor and production.
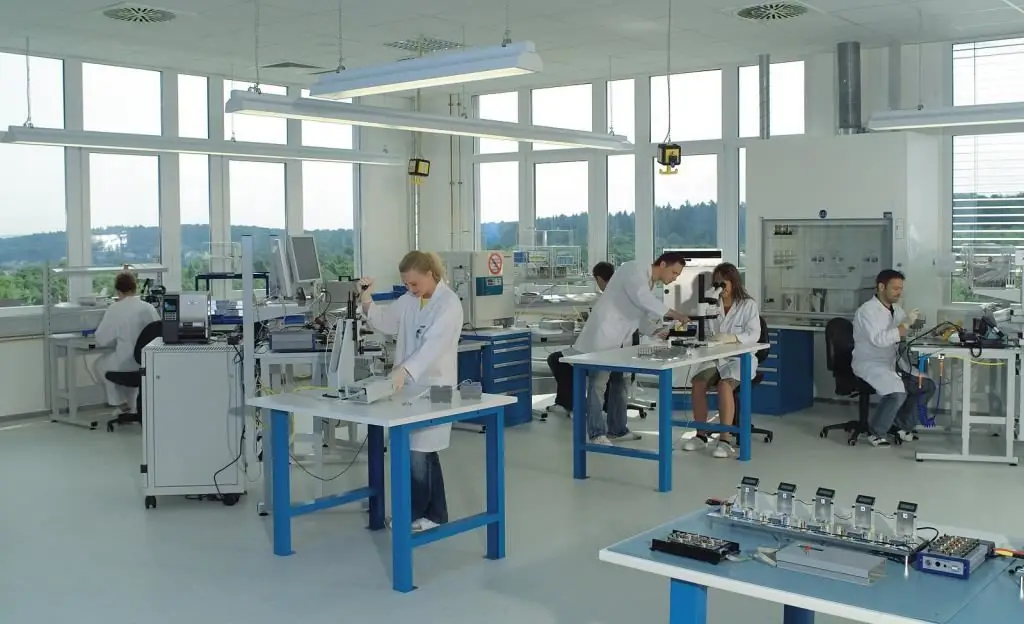
Overseas Development History
The system of scientific organization of labor originated more than 100 years ago, having gone through periods of rapid growth and cycles of stagnation. The starting point in the systematic development of the system is considered to be the end of the 19th beginning of the 20th century. The widespread use of progressive technologies required the creation of a high-performance technologicalequipment. This complicated the system of the enterprise and increased the cost of operation. Under such conditions, obtaining economically liquid enterprises was possible only when using the principles of the scientific organization of labor in production processes. Decisions were required that were based on a strict mathematical basis, and were not made on the basis of rough estimates, "by eye". The new field of science was the brainchild of the first professional industrial engineers.
Rationalist school
The period of development - 1885-1920. Notable activists are Frederick Taylor, Frank and Lillian Gilbreth. Notable innovators were Henry Gant, Harrington Emerson and Henry Ford. The base of the methodology is the measurements of the elements of the labor process, the logical analysis of the elements. Timing of operational movements was carried out. Manufacturing standards have been developed. The mode of operation has been optimized. New forms and payment systems were proposed.
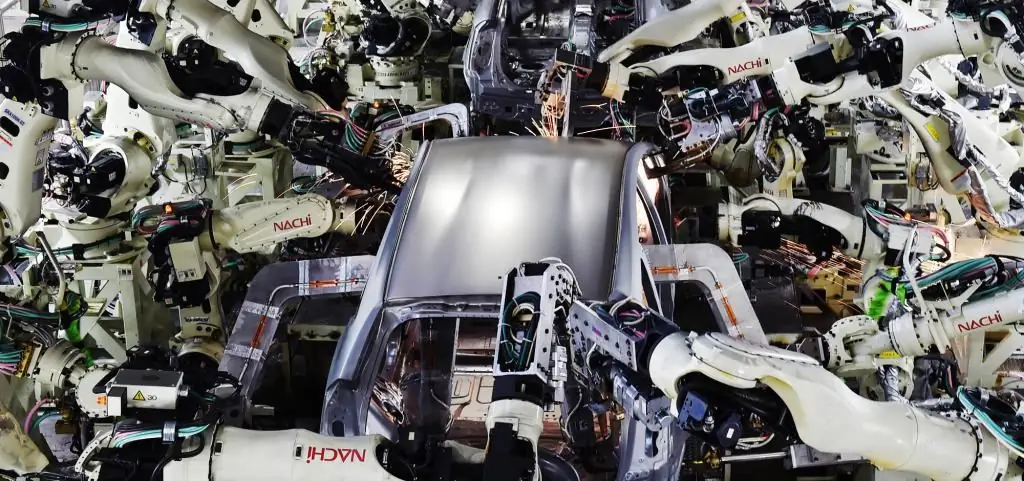
School of Administrative Development
Years of activity - 1920-1950. Representatives - Henri Fayol, James Mooney and Max Weber. The main focus of the activity concerned research in the field of determining the principles of management applicable to all systems. Having extensive experience in practical production management, we considered organizational structures and models of production control that were progressive for that time.
School of Human Relations
Actively developed in the 1930s-1950s, later transforming into well-known and now approaches to scientific organizationmanagerial work. Mary Parker, Elton Mayo and Abraham Maslow. The main emphasis was placed on studying the influence of the human factor, which was considered the main element of an effective organization. An analysis of the mechanisms of employee motivation was carried out. The behavioral strategies of employees in the organization were studied.
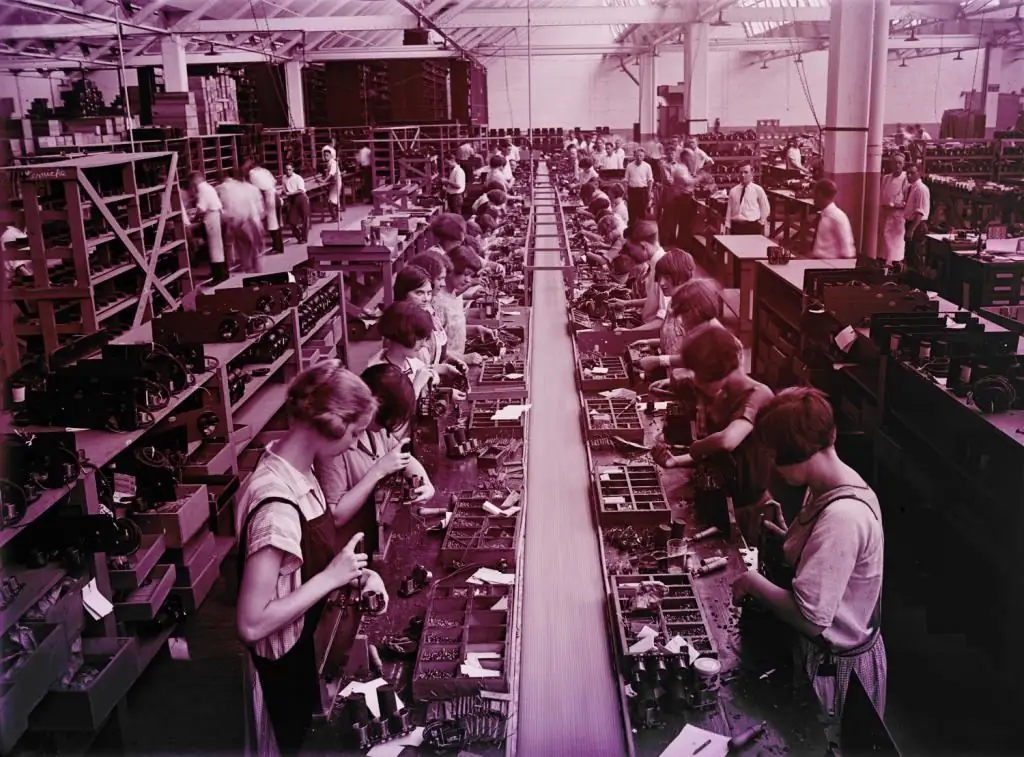
In the second half of the 20th century, more modern trends arise - the school of scientific management, the "7-S" theory, the "Z" theory, etc. From the height of the data of the doctrine, the scientific organization of labor is a constant process of improving all links of the production chain.
Development in domestic production
Chronologically, the scientific foundations of domestic enterprises were based on the following key stages:
- Development of the principles of interchangeability in the production of weapons, developed by Count G. I. Shuvalov in 1761 at the Tula arms factory.
- Creation of a system of teaching "mechanical skills" in 1868, called the "Russian system". At the same time, there was a separation of training workshops and factory workshops. Initially, theoretical training was carried out with practical elements. Then the acquired skills were consolidated in real production.
- From 1921-1927, functional and combined (linear-functional) management structures were introduced. New functional departments of enterprise management were created: statistics, rationing, rationalization, planning, technical control departments, etc.
- At the beginning30s Professor V. M. Ioffe developed the first classification of work movements, which made it possible to create a system of production standards.
- During the Second World War, flow methods of production, operational planning and dispatching, progressive methods of organization (daily and hourly schedules for departments) were actively developed.
- In the post-war period, the area of modernization of production infrastructure, the development of industry-specific automated control systems and automated workstations (AWS) rapidly developed.
- In the future, information technology and production are integrated, which creates a flexible production environment.
Process content
Scientific organization of labor is an important part of the procedures for modernizing and maintaining subsystems of enterprises (private or public, commercial or non-commercial). Its level has a direct impact on the economic component of production and the scale of capital expenditures to achieve the liquidity of the enterprise.
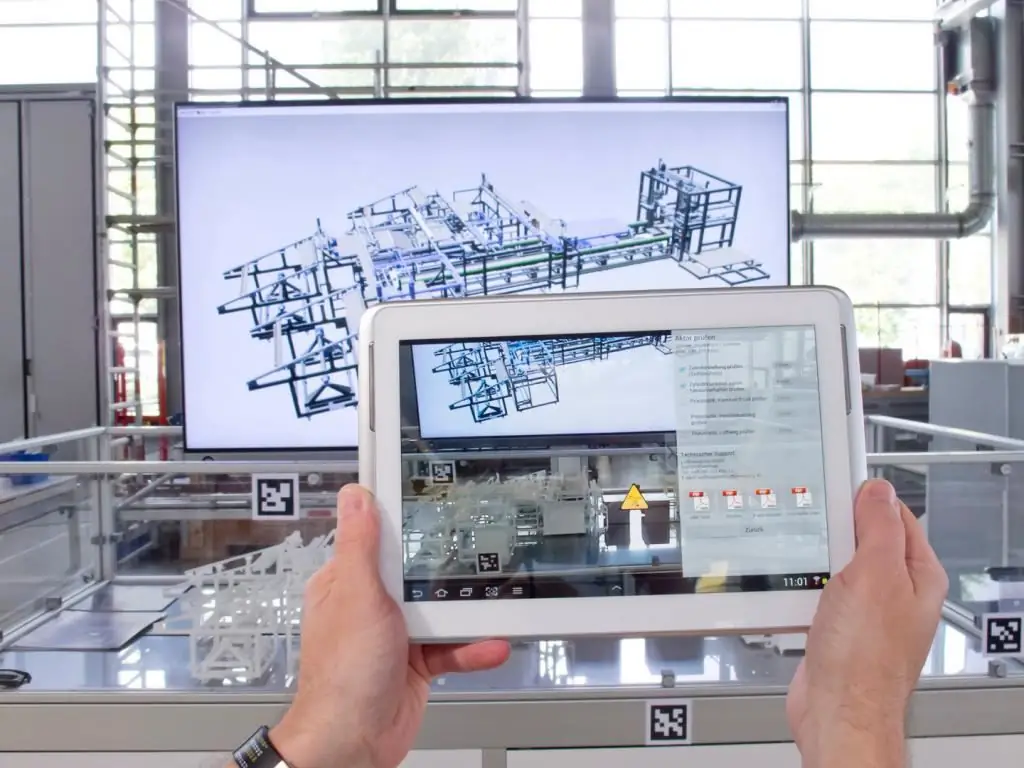
Under the scientific organization of labor is understood a set of different approaches, methodologies and techniques that ensure the most optimal distribution and use of various resources of the production system (including labor). Methods of scientific organization of labor are a necessary factor in the development of the production system. The main goal is to achieve maximum operator productivity and product quality based on the results of scientific analysis and synthesisproduction. This contributes to the leveling of biased and arbitrary estimates of factors of production. There is a transition to precise production control mechanisms (the use of advanced methods of process flow control).
Tasks of the scientific organization of labor
The main goal of NOT is the rational use of production (labor) resources in the process of professional activity. To solve it, a class of additional tasks is used, which can be grouped into the following blocks:
- Economic bloc. Improvement of the working area (the production environment as a whole), optimization of manufacturing and repair methods, reduction of time losses during labor operations, etc.
- Psychophysiological block. Creating a flexible and ergonomic environment for the worker, in terms of the impact on physical he alth and perception, ensuring the required performance in the production process.
- Social bloc. Development of mechanisms that make work attractive and meaningful (the level of salaries, additional payments and allowances, changing time funds).
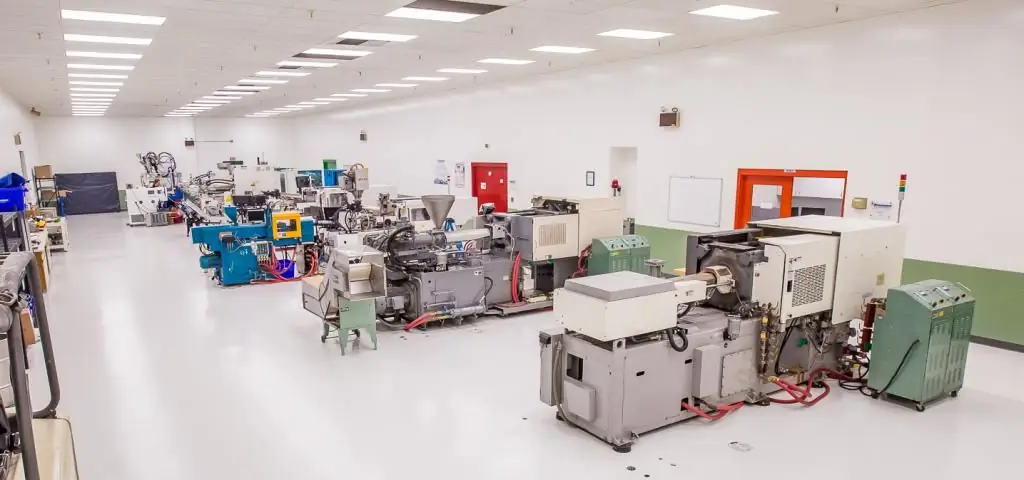
Influencing factors
In the practice of production activities, the NOT system is influenced by a large number of factors of production, the key of which are:
- degree of development of fixed assets;
- perfection of manufacturing technology (product repair);
- features of approaches to the organization of production (stationary, flow, flexible systems);
- dominant management models;
- in-plant planning level;
- development of the resource supply system;
- level of auxiliary production;
- availability of mechanisms for taking into account scientific approaches in the design of production facilities.
System Orientation
The directions of the scientific organization of labor are the points of application of the required resources in order to optimize the activities of enterprises. Consider the most famous and common:
- rational use of appropriate forms of labor (cooperation, specialization, etc.);
- using forward-looking approaches to work areas ("5S" and "TPM", lean manufacturing methods, etc.);
- optimization of losses when creating new products;
- improving production techniques;
- development of motivation mechanisms;
- adopting progressive procedures to ensure the necessary qualifications of staff;
- continuous improvement of working conditions;
- creation of labor discipline control mechanisms;
- use of optimal work patterns for employees of different levels;
- adjustment of rationing processes.

Principles of the scientific organization of labor
In order to systematically use the results of scientific and technical activities, it is necessary to adhere to certain provisions (principles), which include:
- Science - a systematic analysis of operating activities over time, the use of progressive tools(equipment) for conducting surveys, carrying out the necessary calculations using mathematical models for analyzing labor activity data. Allows to minimize excessive administration, unreasonable and incompetent decisions in scientific management and scientific organization of labor.
- Plannedness - determination of the speed and scale of the development of NOT based on existing research experience.
- Complexity - involves a systematic improvement of labor in relation to all subsystems of the enterprise, all categories of employees and activities. There is a similarity with the principle of proportionality in the organization of production activities.
- Continuity - implies the constant use of the foundations of the scientific organization of labor. Any changes in production (introduction of new equipment, use of new technologies) must be accompanied by the implementation of GOT procedures. At the same time, they must correspond to the actual development of labor processes at different stages of development.
- Normativity - involves the linkage of all decisions of the NOT with the current regulatory and technical documentation. Which, in turn, stimulates the development of the regulatory framework and mechanisms for its creation.
- Economy is the implementation of the most optimal, in terms of material, labor and other costs, scientific and technical solutions. Reduction and subsequent leveling of various losses and irrational costs.
Compliance with these principles ensures the formation of the foundations of the scientific organization of labor in the production system.
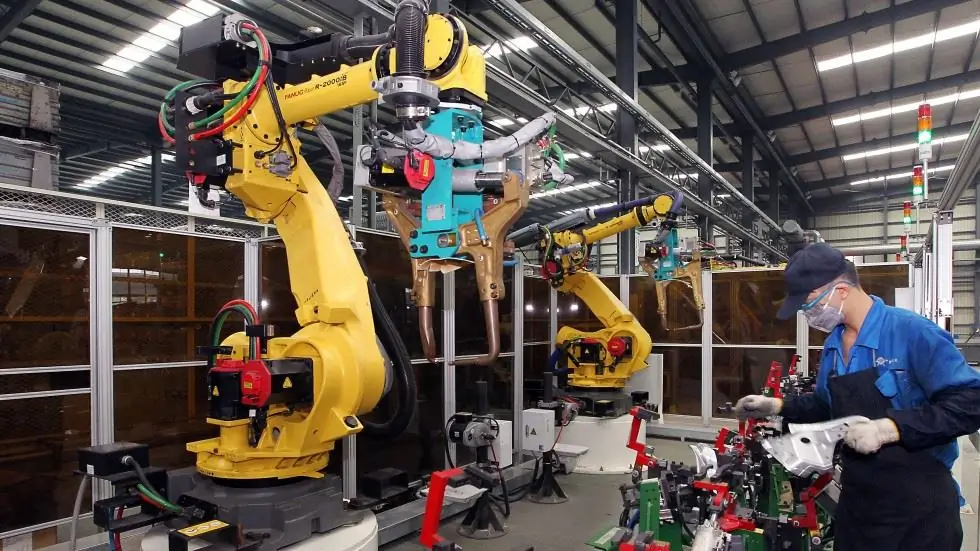
Common functions
Scientific organization of labor is the implementation of innovative processes in time. The key elements in the theory of NOT are functions that are implemented in processes and affect production elements, including humans. The following key types of functions can be distinguished:
- Resource saving. Intensification of production (labor) on the basis of saving elements of the production environment (time, semi-finished products, materials, spare parts, energy resources).
- Optimization. Ensuring the proportional development of the components of production and labor (qualification corresponds to the level of equipment used). In addition, it involves coordinating the level of payment with the characteristics of production and products.
- Employee efficiency. Professional selection for a specific activity, staffing through accurate methods of quantitative and qualitative assessments and continuous improvement of qualifications.
- Safety. It involves the creation of normal conditions for employees.
- Harmonization. Everything for the maximum disclosure of professional and creative reserves, consistency of different loads (physical and intellectual).
- Culture of processes. Use of democratic management styles, elements of aesthetics in the production environment.
- Activation. Development of the employee's creative initiatives by creating appropriate working environment conditions.
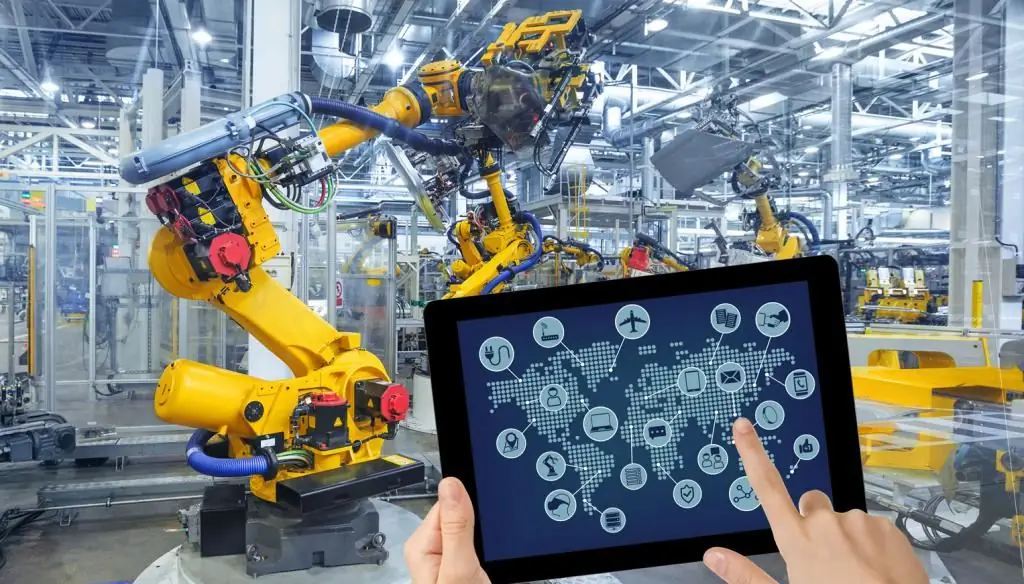
Conclusion
Modernbusinesses and organizations are facing new and serious challenges: customers demand individual, high-quality, and at the same time inexpensive and reliable products in the shortest possible time. To solve this problem, it is necessary to intensify scientific and engineering research. After all, the scientific organization of labor is the most effective mechanism that allows solving problems of this magnitude.
Informatization and digitalization of production, the development of embedded systems for monitoring the technical condition and communication with control centers, the introduction of new generation industries "Industry 4.0" - all this is the basis of HOT research.