The work activity of a person is carried out in working conditions, which include certain factors. In the process of work, various environmental conditions can affect the body, which can change the state of he alth, lead to damage to the he alth of offspring. In order to avoid exposure to such hazardous factors in the working environment, there is a hygienic standard. It contains detailed provisions characterizing various hazard classes and working conditions.
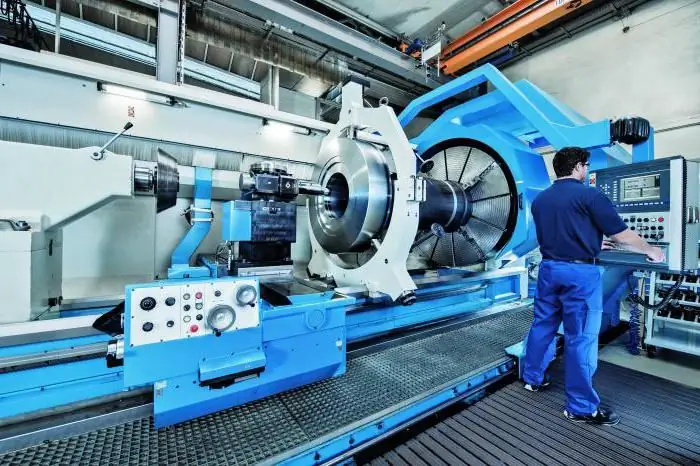
Hygienic standards of working conditions. What is this?
The maximum allowable level (MPL) and the maximum allowable coefficient (MPC) determine the level of harmful factors in the working environment for a period of 8 hour working days with a forty-hour working week. They are included in the hygienic standards of working conditions. Normal indicators should not contribute to the occurrence of any diseases, as well as cause deviations in the state of he alth, both in the worker and in subsequent periods of life in his offspring. ATin some cases, even if hygiene standards are observed, some hypersensitive people may experience he alth problems.
Hygienic and sanitary-hygienic standards are established, taking into account an 8-hour working day. If the shift is longer, the possibility of work is agreed upon taking into account the indications of the he alth of the workers. The data of periodic medical examinations and other examinations are checked, complaints of employees are taken into account.
Sanitary and hygienic standards indicate the maximum allowable concentrations, doses of biological and chemical harmful substances, their effects on the body. Sanitary protection zones are determined, as well as the maximum tolerance for radiation exposure. Such indicators are designed to ensure the epidemiological well-being of the entire population, and are developed using evidence-based methods.
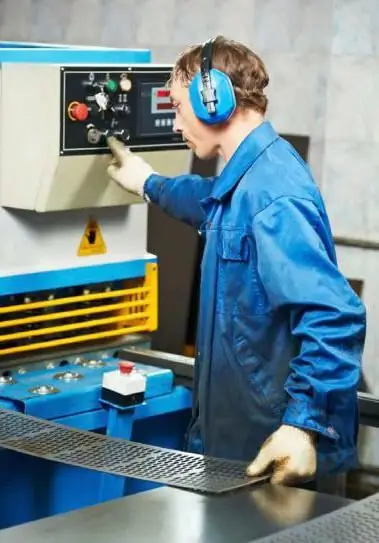
Work activity
The labor activity of people depends on the tools and objects of labor, the proper organization of jobs, efficiency, as well as on the factors of production, developed by the hygienic standard.
Efficiency is a value indicating the functionality of an employee, characterized by the quantity and quality of work performed for a certain period of time.
An important element of improving performance is improving skills and knowledge as a result of training.
In the efficiency of the labor process, an important role is played by the correct layout, location of the workerspace, freedom of movement, comfortable posture. The equipment must meet the requirements of engineering psychology and ergonomics. At the same time, fatigue is reduced, the risk of occupational diseases is reduced.
The vital activity and performance of the body is possible with the correct alternation of working periods, sleep and rest of a person.
It is recommended to resort to the services of psychological relief rooms, relaxation rooms to relieve psychological and nervous tension.
Optimal working conditions
Based on the hygienic standard, working conditions can be divided into four main classes:
- optimal conditions (grade 1);
- permissible conditions (grade 2);
- harmful conditions (Grade 3);
- dangerous (and extreme) conditions (Grade 4).
If, in fact, the values of harmful factors fit within the limits of permissible and optimal values, and the working conditions are in accordance with hygienic requirements, then they are classified as first or second class.
Under optimal conditions, labor productivity is maximum, while the stress of the human body is minimal. Optimal standards are set for the factors of the process of labor activity and for microclimate parameters. Under other factors, such working conditions should be applied under which the level of safety should not be exceeded.
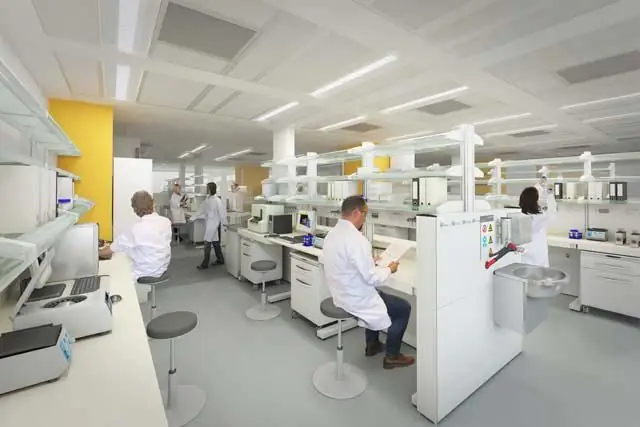
Acceptable conditions
Permissible conditions of the labor process have such levels of environmental factors that should not exceedestablished in the hygienic standard.
The working functions of the body must be fully restored after rest by the beginning of a new shift. Environmental factors should not have an adverse effect on human he alth even in the long term, as well as on the he alth of his offspring. The acceptable class of conditions must fully comply with the regulations and safety of working conditions.
Harmful and extreme conditions
Sanitary rules and hygiene standards emphasize harmful working conditions. They are characterized by harmful factors of production. They exceed the requirements of the standards, have an adverse effect on the body, as well as on distant offspring.
Extreme conditions include those under which during the entire work shift (or any part of it) harmful production factors pose a threat to the life of the worker. There are high risks of acute, severe forms of occupational injury.
Degrees of harmfulness
Hygienic labor quality standards divide the class (3) of harmful working conditions into several degrees:
- 1 degree (3.1). These conditions characterize deviations of the level of harmful factors from the hygienic standard, causing functional changes. They tend to recover over a longer period than by the start of a new shift. There is a risk of damage to he alth in contact with harmful factors.
- 2 degree (3.2). Harmful factors of this level cause such functional changes that often lead to conditioned professionalmorbidity. It may manifest its level with disability (temporarily). After prolonged exposure to harmful factors, often after 15 years, occupational diseases appear, their mild forms, the initial stages.
- 3 degree (3.3). Harmful working conditions leading to the development of mild and moderate occupational diseases with loss of professional performance. There is a development of chronic work-related pathologies.
- 4 degree (3.4). Harmful conditions leading to the occurrence of severe forms of occupational diseases, which are characterized by the loss of general ability to work. The number of chronic diseases is increasing, their level is accompanied by a temporary loss of working capacity.
Specialized research laboratories are engaged in assigning certain working conditions to any class, as well as the degree of harmfulness, which have the appropriate accreditation for certification of working conditions of workplaces.
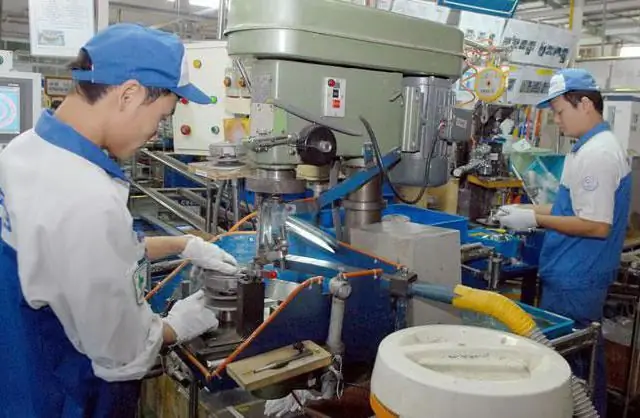
Harmful factors
Sanitary norms, rules and hygienic standards necessarily contain a list of harmful factors. These include factors of the labor process, as well as environments that can cause occupational pathologies, temporary, persistent declines in performance. Under their influence, the frequency of infectious and somatic diseases increases, and a violation of the he alth of offspring is possible. Harmful factors include:
- chemical factors, aerosols, most oftenfibrinogenic effects;
- noise in the workplace (ultrasound, vibration, infrasound);
- biological factors (protein preparations, microspores, pathogenic microorganisms);
- microclimate in the production area (hygienic air standards are too high or too low, humidity and air movement, thermal exposure);
- radiation and non-ionizing electromagnetic field (electrostatic field, power frequency electric field, alternating magnetic field, radio frequency fields);
- radiation ionizing radiation;
- light environment (artificial and natural lighting);
- tension and severity of labor (dynamic physical load, lifting weights, working posture, static load, movement, body tilts).
Depending on how long a performance has been affected, it can become hazardous.
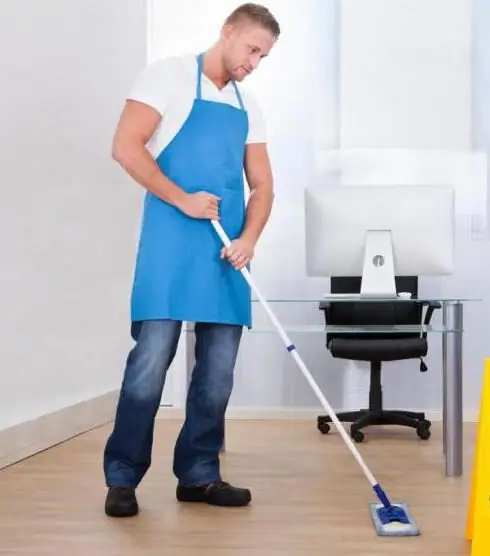
Relation to classes
Sanitary norms and hygienic standards imply normal working conditions that belong to the 1st or 2nd class. If the prescribed norms are exceeded, then, depending on the magnitude, in accordance with the prescribed provisions for individual factors or their combination, working conditions can be classified as one of the degrees of the 3rd class (harmful conditions) or to the 4th class (dangerous conditions).
If one substance contains several harmful specific effects at once (allergen, carcinogen and others), the working conditions are assigned morehigh degree of hazard class.
To establish the class of conditions, exceeding the MPC and MPC is recorded during one shift, if the picture is typical for the production process. If hygiene standards (GN) are exceeded in an episodic manner (week, month) or have a picture that is not typical for the production process, then the assessment is given in agreement with the federal services.
In dangerous (extreme) working conditions of the 4th class, work is prohibited. Exceptions are catastrophes, elimination of the consequences of accidents, as well as activities to prevent accidents. At the same time, work is carried out in special protective suits, subject to strict security regimes and work regulations.
Risk groups
The high levels of occupational risk include those categories of workers who are exposed to factors that exceed the hygienic standards of class 3.3. Working in such conditions increases the risk of occupational diseases, the occurrence of severe forms. Lists 1 and 2 of this group include most professions in non-ferrous and ferrous metallurgy, mining enterprises and others. These lists were approved by Committee Resolution No. 10 of 1991-26-01.
Ultra-high risk categories include workers in industries where extreme conditions can cause a sharp, sudden deterioration in he alth. This includes coke-chemical, metallurgical production, as well as areas of activity in an unusual environment for humans (in the air, under water, underground, in space).
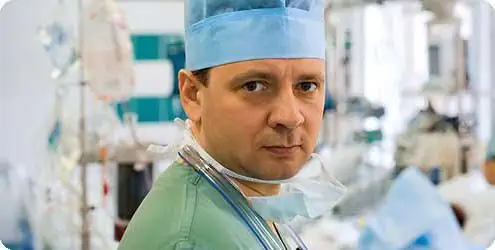
Hazardous production facilities
The Government established the Register, which registers hazardous (according to working conditions) production facilities. That activity is recognized as a source of danger if it includes two signs: the likelihood of causing harm to others, the lack of full control on the part of a person.
Dangerous objects themselves serve as a source of possible danger, both for others and for workers. Most often, this includes industrial organizations that use high-voltage electricity, nuclear energy. This includes construction, vehicle operation and some other areas of activity.
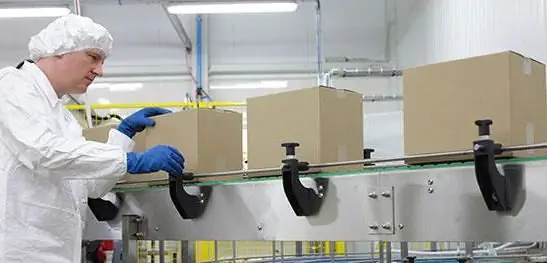
Labor hygienic assessment
Labor hygienic assessment is carried out in accordance with the Guidelines, the main objectives are:
- monitoring the state of working conditions, compliance with hygiene standards;
- revealing priority in carrying out professional activities, evaluating their effectiveness;
- at the organization level, the creation of a data bank according to working conditions;
- analysis of the connection between the state of he alth of an employee and his working conditions; special examinations; diagnosis;
- investigation of occupational diseases;
- assessment of occupational he alth risks for workers.
If any violations of hygiene standards are revealed, the employer is obliged to develop a set of measures to improve working conditions. Hazards should be eliminated or reduced to a safe limit whenever possible.